
ریخته گری فولاد چیست؟ تولید کننده قطعات ریخته گری فولادی
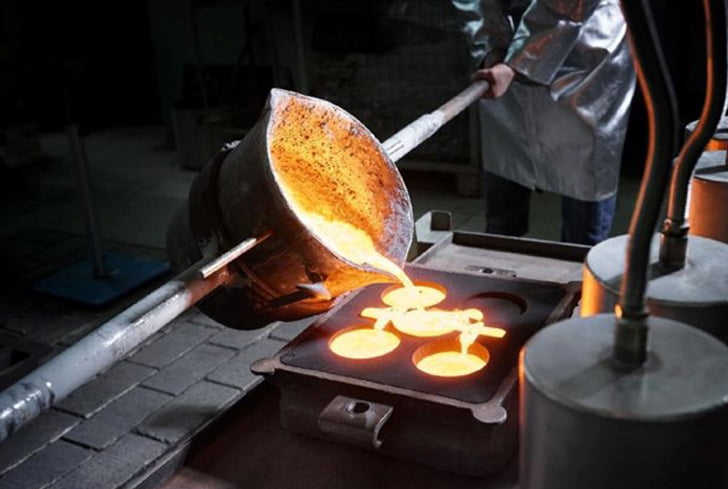
سهند آذرین: تولید کننده قطعات ریخته گری فولاد
جهت دریافت مشاوره تماس بگیرید.
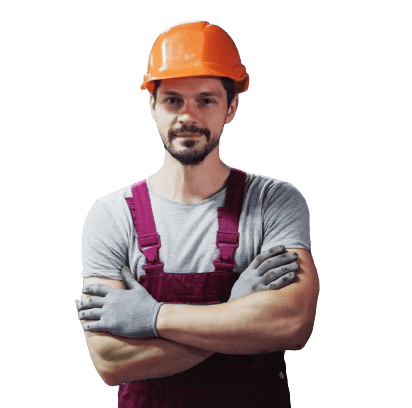
ریختهگری فولاد فرآیندی است که در آن فولاد مذاب در قالب ریخته شده و پس از ریخته گری ویژگیهای ظاهری و مکانیکی و الزامات , مطابق با نیازهای مشتری حاصل میشود. ریخته گری فولاد نقش بسیار مهمی در صنایع مختلف از جمله خودروسازی، ساختمانسازی و صنایع دریایی دارد.
ریخته گری فولاد چیست؟
فولادها جزو خانواده بزرگ آلیاژهای آهنی بوده و کاربردهای بسیاری در صنعت دارند.این آلیاژها به روش های مختلفی تولید می شوند که یکی از این روش ها؛ تولید به روش ریخته گری میباشد. فولادها کلا به 4 دسته تقسیم بندی میشوند:
1)فولادهای ساده کربنی (عنصر اصلی دراین فولادها کربن می باشد)
2)فولادهای کم آلیاژ (منگنز و سیلیسیم بالاتری دارندو سایر عناصر نیزهمچونNi-Cr-Cu-Moو…درآن ها وجود دارد)
3)فولادهای با آلیاژ متوسط (منگنز و سیلیسیم بالاتری دارند و سایر عناصر نیزهمچونNi-Cr-Cu-Moو…درآن ها وجوددارد)
4)فولادهای پرآلیاژ (حاوی بیش از10% عناصر آلیاژی)
عمده عیوب ریختگی قطعات فولادی مک و تخلخل – شلاکه – ترک و کشیدگی می باشد. عیوب ریختگی تاثیر زیادی برکیفیت قطعات تولیدی داشته و ریخته گرفولاد بایستی در گام اول بتواند نوع عیب را درست تشخیص داده و سپس منشا آنرا شناسایی و اقدام به رفع عیب نماید.
فرایند ریخته گری فولاد چیست؟
ریختهگری فولاد به فرآیندی گفته میشود که در آن، ابتدا فولاد در کوره القائی ذوب میشود. سپس آن را داخل قالب میریزند تا سرد شود. سپس قالبها را تخلیه و قطعات را جدا می کنند و به قسمت سنگ زنی جهت تمیزکاری ارسال می شوند.
قطعات فولادی که بهروش ریختهگری تولید میشوند کاربردهای متعددی دارند و وزن آنها میتواند از چند گرم تا چند تن متغیر باشد.
انواع روش های ریخته گری فولاد
انواع روشهای مختلف ریخته گری فولاد:
ریخته گری فولاد به روش شمش ریزی
ریختهگری شمشریزی به دو صورت تکبار و مداوم انجام میشود؛ که هر یک با ویژگیها و کاربردهای خاص خود را دارد.
ریخته گری شمش و کاربرد صنعتی آن یکی از فعالیتهای مهم در صنعت فولادسازی و ذوب آهن، عملیات ریخته گری شمش است. در حقیقت هدف اصلی ریخته گری شمش تبدیل انواع مختلف این محصول به فرآوردهی مصرفی است.
ریخته گری شمش های تکبار(Batch)
به این روش ریخته گری غیرپیوسته یا تکباری گفته میشود(batch)در روش تکبار، فولاد مذاب درون یک قالب ریخته می شوند.در این روش از قالب افقی روباز و قالب شمش عمودی استفاده میشود. در نهایت شمش تولید شده به این روش تحت فرآیند نورد قرار گرفته و محصولات مختلف دیگر از طریق آن تولید میشود.
ریخته گری مداوم(CCM)
ریختهگری پیوسته یا مداوم(CCM) یکی از روشهای پرکاربرد در تولید مقاطع میانی فولاد محسوب شده و در طی آن فلز مذاب به صورت مستقیم و پیوسته به مقاطع میانی تبدیل میشود.
ریخته گری فولاد به روش شکل ریزی(Part)
در ریخته گری فولاد، فلز با حرارت بالا ذوب شده و سپس در قالبهای از پیش آمادهشده ریخته میشود. پس از خنک شدن و انجماد، قطعهای با شکل دلخواه به دست میآید. اقتصادی بودن، قابلیت تولید انبوه، انعطافپذیری، امکان بازیافت و سرعت تولید بیشتر ازجمله مهمترین مزایا استفاده از روش ریخته گری فولاد است
ریخته گری فولاد نسوز
ریخته گری فولاد نسوز، فرآیندی تخصصی برای تولید قطعات فلزی با مقاومت بالا در برابر حرارت است. در این روش، آلیاژهای فولادی خاص با دمای ذوب بالا، ذوب میشوند و در قالبهای ریختهگری قرار میگیرند. پس از انجماد، قطعاتی با ویژگیهای منحصربهفرد مانند مقاومت در برابر خوردگی، سایش و اکسیداسیون در دماهای بالا تولید میشوند.
ریخته گری فولاد ضد سایش
ریخته گری فولاد ضد سایش، فرآیندی تخصصی برای تولید قطعات فلزی با مقاومت فوق العاده بالا در برابر سایش است. در این روش، آلیاژهای فولادی با ترکیبات خاص ذوب میشوند و در قالبهای ریختهگری قرار خواهند گرفت. پس از انجماد، قطعاتی با سختی و استحکام مثال زدنی به وجود می آیند که در برابر اصطکاک و سایش شدید، عمر طولانی و عملکردی بیعیب و نقص دارند.
ریخته گری قالب ماسه ای فولاد
ریختهگری فولاد در قالب ماسهای یکی از روش های مهم در صنعت فولادسازی است که برای کاهش خطر پارگی، ترکخوردگی و سایر عیوب فلزات بهکار میرود. این روش از انعطافپذیری و انقباض متوسطی در طول مرحله خنکشدن بهره میبرد تا عیوب بیشتری در محصول نهایی ایجاد نشود.
بهترین روش ریخته گری فولاد
انتخاب بهترین روش ریختهگری فولاد به عوامل متعددی بستگی دارد، از جمله:
• نوع و خواص فولاد: آلیاژهای مختلف فولاد، نیازهای متفاوتی در فرآیند ریختهگری دارند.
• شکل و ابعاد قطعه: هندسه و اندازه قطعه نهایی، انتخاب روشهای مناسب برای ریختهگری را محدود میکند.
• تیراژ تولید: تعداد قطعات موردنیاز، بر انتخاب روش ریختهگری تاثیرگذار است.
• دقت و کیفیت مورد نظر: سطح کیفیت و دقت ابعادی مورد انتظار، در انتخاب روش ریختهگری نقش دارد.
• هزینهها: بودجه و هزینههای تولید، فاکتور مهمی در انتخاب روش مناسب است.
در نهایت، انتخاب بهترین روش ریختهگری فولاد به یک تجزیهوتحلیل دقیق از نیازها و شرایط پروژه شما نیاز دارد. برای انتخاب بهترین روش ریختهگری، میتوانید از مشاوره متخصصان این حوزه استفاده کنید.
مراحل ریخته گری فولاد
ریختهگری فولاد فرآیندی چند مرحلهای است که طی آن فولاد ذوب شده و در قالبهای مخصوص ریخته میشود تا پس از انجماد، قطعه نهایی با شکل و خواص مورد نظر بهدست آید. مراحل اصلی این فرآیند عبارتند از:
1. آمادهسازی مواد اولیه
• فولاد و سایر مواد اولیه مانند آلیاژها و مواد افزودنی به دقت بررسی و آماده میشوند.
• مواد اولیه به نسبتهای مناسب مخلوط میشوند تا ترکیب شیمیایی مورد نظر برای فولاد نهایی حاصل شود.
2. ذوب کردن
• مواداولیه در کورههای مخصوص مانند کوره قوس الکتریکی یا کوره القایی ذوب خواهند شد.
• دمای ذوب به نوع فولاد و روش ریخته گری مورد استفاده بستگی دارد.
3. آمادهسازی قالب
• قالب ریخته گری مرد نیاز بر اساس شکل و ابعاد قطعه نهایی ساخته میشود.
• جنس قالبها میتواند از ماسه، فلز یا مواد نسوز باشد.
• برای جلوگیری از چسبیدن مذاب به قالب، از مواد جداکننده بهره میبرند.
4. ریختن مواد مذاب
• مذاب فولاد بهطور کنترلشده و با دقت در قالب ریخته میشود.
• سرعت و نحوه ریختن مذاب بر کیفیت و خواص قطعه نهایی تاثیرگذار است.
5. انجماد
• مذاب فولاد در قالب خنک میشود و به یک ماده جامد تبدیل خواهد شد.
• سرعت انجماد به نوع فولاد، ابعاد قالب و روش ریختهگری مورد استفاده بستگی دارد.
نکات مهم در ریخته گری فولاد
ریختهگری فولاد یک فرآیند پیچیده و حساس است که نیاز به رعایت نکات اساسی دارد. این نکات عبارتند از:
• انتخاب مواد اولیه: انتخاب موادی با کیفیت و استاندارد بالا از اهمیت ویژهای برخوردار است.
• طراحی قالب: طراحی صحیح و دقیق قالب با توجهبه شکل و ابعاد قطعه نهایی، اساس موفقیت در ریختهگری خواهد بود.
• کنترل دما و زمان: رعایت دقیق دما و زمان مورد نیاز برای ذوب فولاد و پرکردن قالب از جمله نکات حیاتی است.
• ریختهگری بدون هوا: جلوگیری از ورود هوا به داخل قالب که میتواند منجر به تولید بخار و عیوب در سطح قطعه شود، بسیار اهمیت دارد.
• خنکشدن مناسب: فرآیند خنکشدن با توجه به نوع قطعه و نیازهای آن، باید با دقت و صحیح انجام شود تا عیوب ناشی از تغییرات حرارتی کاهش یابد.
• بازرسی و کنترل کیفیت: پس از ریختهگری، بازرسی دقیق قطعات و کنترل کیفیت بهعنوان یک مرحله بسیار حیاتی در جلوگیری از تولید محصولات نامناسب بسیار اهمیت دارد.
رعایت این نکات مهم، میتواند به بهبود عملکرد و کیفیت در فرآیند ریختهگری فولاد کمک کند.
دمای ریخته گری فولاد
دمای ریختهگری فولاد به عوامل مختلفی بستگی دارد، از جمله:
• نوع فولاد: آلیاژهای مختلف فولاد، نقطه ذوب و دمای ریختهگری متفاوتی دارند.
• روش ریختهگری: روشهای مختلف ریختهگری، دمای ریختهگری خاص خود را خواهند داشت.
• شکل و ابعاد قطعه: قطعات با ضخامت بیشتر، به دمای ریختهگری بالاتری نیاز دارند.
• کیفیت و دقت مورد نظر: برای دستیابی به کیفیت و دقت بالا، باید از دمای ریختهگری مناسب استفاده کرد.
بهطور کلی، دمای ریختهگری فولاد بین 1500 تا 1700 درجه سانتیگراد است. در اینجا به چند نمونه از دمای ریختهگری برای فولادهای مختلف اشاره میشود:
• فولاد ساده کربنی: 1530-1650 درجه سانتیگراد
• فولاد ضد زنگ: 1550-1700 درجه سانتیگراد
• فولاد آلیاژی: 1500-1650 درجه سانتیگراد
• فولاد نسوز: 1600-1750 درجه سانتیگراد
مدلسازی قطعه در ریخته گری فولاد
مدلسازی قطعه در ریختهگری فولاد یک مرحله حیاتی است که با استفاده از نرمافزارهای مهندسی معکوس و سیستمهای CAD/CAM صورت میگیرد. در این مرحله، قالب و جزئیات آن به دقت مدلسازی میشود تا شرایط ریختهگری بهینه شود.
دربحث مدلسازی پیشبینی جریان فلز در قالب، انتخاب مواد و نوع فرایند ریختهگری اهمیت دارد. مدلسازی دقیق، از هدر رفت فلز، تغییر شکل ناخواسته و عیوب در قطعه جلوگیری میکند و باعث بهبود کیفیت و دقت نهایی قطعه میشود.
طراحی درست سیستم ریخته گری فولاد
طراحی درست سیستم ریختهگری فولاد، نقشی کلیدی در کیفیت، دقت، راندمان و بهینگی فرآیند تولید ایفا میکند. این سیستم شامل اجزای مختلفی مانند کوره ذوب، سیستم ریختن، قالب، سیستم خنک سازی و تجهیزات جانبی است که باید به طور هماهنگ با یکدیگر کار کنند تا به نتایج مطلوب دست یافت.
مزایای ریخته گری فولاد
ریختهگری فولاد فرآیندی پرکاربرد برای تولید قطعات فلزی با اشکال و ابعاد پیچیده است. این روش مزایای متعددی دارد که آن را به انتخابی ایده آل برای طیف وسیعی از کاربردها تبدیل کرده است. مزایای کلیدی ریختهگری عبارتند از:
• انعطافپذیری
• راندمان عالی
• اقتصادی بودن
• قابلیت تولید انبوه
• تنوع در قطعات ارائه شده
• قابلیت بازیافت
معایب ریخته گری فولاد
معایب کلیدی ریختهگری فولاد عبارتند از:
• دقت: دقت ابعادی و هندسی قطعات ریخته گری به اندازه روشهای دیگر مانند ماشینکاری، بالا نیست.
• عیوب: احتمال بروز عیوبی مانند تخلخل، انقباض و ترک خوردگی در قطعات ریختهگری وجود دارد.
• نیاز به عملیات تکمیلی: قطعات ریختهگری غالباً به عملیات تکمیلی مانند فرزکاری، صافکاری و … نیاز دارند.
• محدودیت در ضخامت: ریختهگری فولاد برای تولید قطعات با ضخامت کم مناسب نیست.
• هزینه اولیه بالا: هزینه اولیه ساخت قالب و تجهیزات ریختهگری میتواند بالا باشد.
• آلودگی: فرآیند ریختهگری فولاد میتواند آلودگیهای زیست محیطی ایجاد کند.
سخن پایانی
ریختهگری فولاد یک فرآیند صنعتی حیاتی است دراین روش با استفاده از ذوب فلز و ریختن آن در قالب، قطعات فولادی تولید میشود. این فرآیند نیازمند دقت و دانش فنی است و اهمیت بسیاری برای صنایع مختلف دارد.
مقالات و اخبار
یک نظر در “ریخته گری فولاد چیست؟ تولید کننده قطعات ریخته گری فولادی”
کیفیت ریخته گری فولاد به چه عواملی بستگی داره؟