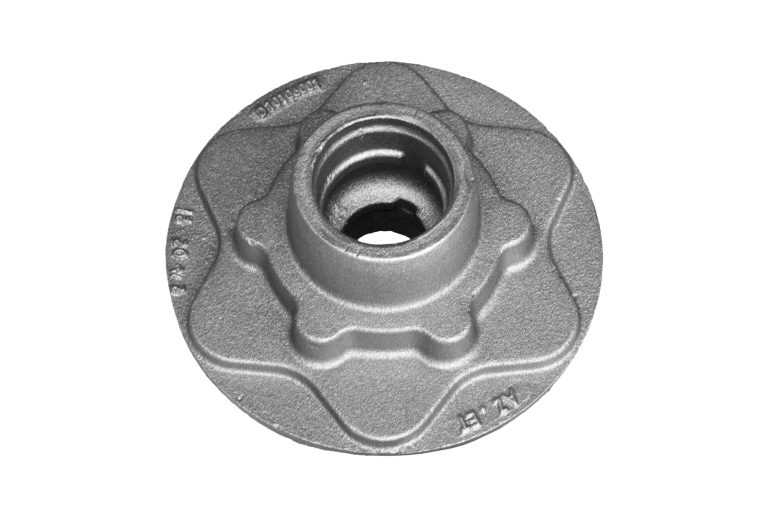
خانه » مقالات » مقایسه فولاد خط لوله X80 ذوب شده در کوره القایی تحت اتمسفر گاز آرگون در هوا و کوره القایی تحت خلاء
مقایسه فولاد خط لوله X80 ذوب شده در کوره القایی تحت اتمسفر گاز آرگون در هوا و کوره القایی تحت خلاء
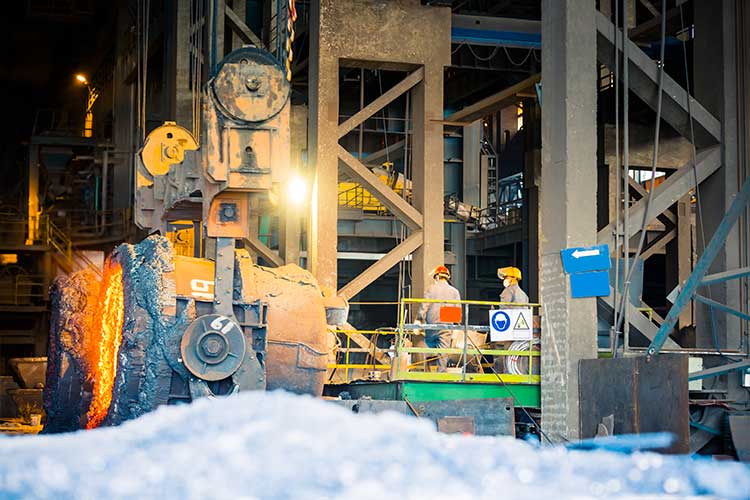
چکيده
در مقاله حاضر تميزي، ريزساختار و خصوصيات مکانيکي فولاد خط لوله X80 توليد شده به وسيله کوره القايي تحت خلاء (VIM)1 در مقابل کوره القايي تحت اتمسفر آرگون (AIM)2 مقايسه گرديده است. در اين تحقيق هر دو آزمايشات AIM ،VIM تحت اتمسفر گاز آرگون انجام شد اما در روش AIM از گاز آرگون و آرگون مايع هم زمان بدون اعمال خلاء استفاده گرديد.
شمش هاي فولادي با ضخامت 130 ميليمتر ريخته گري شدند سپس تا ضخامت 12/5 ميليمتر تحت نورد گرم قرار گرفتند . داده ها نشان دهنده ترکيب شيميايي فولاد، ريزساختارها و خصوصيات مکانيکي به صورت قابل مقايسه بين دو روش ذوب است. البته ذوب تحت خلاء در مقايسه با روش ديگر يک ارتقاي قابل توجه در تميزي فولاد و چقرمگي ضربه در آزمايش چارپي با نمونه شکاف دار نشان داد.
1- مقدمه
روش ذوب در خلاء برای تولید برخی آلیاژها به دلیل واکنش پذیری با اتمسفر اکسیژن و نیتروژن بسیار ضروری است (2 و 1). از سویی دیگر ذوب استاندارد القایی در هوا (AIM) به طور گسترده برای آلیاژهای چدن، فولاد و کبالت و نیکل استفاده می شود. اما برخی فولادهای کم آلیاژ مانند فولاد خط لوله جهت ارتقای در کیفیت و خصوصیات مکانیکی با استفاده از رو ش های خلاء تولید می شوند که موجب افزایش اساسی در هزینه ها خواهد گردید (3).
در دهه 60 میادی W. H Golding مقایسه ای را بین دو روش ذوب در اتمسفر هوا و تحت خلاء برای فولاد AISI (4340)(Ni- Cr- Mo Steel) انجام داد (4). به طور کلی ذوب تحت خلاء یک ارتقای قابل توجه در خصوصیات مکانیکی فولاد4340 نسبت به کوره القایی در اتمسفر معمولی ایجاد می کند البته مشروح نکات در مورد ذوب و ریخته گری در تحقیق (4) ارائه نشده است.
برخی اوقات روش AIM بجای اعمال خلاء جهت پیشگیری از تبخیر عناصر آلیاژی تحت پوشش یک گاز خنثی انجام می شود.
در این مورد ابتدا یک خلاء ایجاد می شود سپس محفظه کوره قبل از ذوب با گاز خنثی مانند گاز آرگون پر می شود (2 و 1).
در تحقیق حاضر از روش VIM – Ar استفاده شده است. از سویی دیگر روش های مختلف پوشش آرگون در ذوب AIM توسعه یافته تا از فلز مذاب و جداره کوره با هزینه کم محافظت نماید که در مقاله حاضر روش AIM – Ar به کار رفته است. از بین شیو ه های پوشش با گاز آرگون SPAL3 (5) 4LBI (6) بیشترین کاربرد را دارند. در فرآیند SPAL آرگون مایع به کوره اضافه می شود و در تبدیل مایع به گاز، حجم آرگون بیش 800 برابر افزایش می یابد تا فلز مذاب به خوبی پوشش داده شود (5).
در فرآیند LBI گاز آرگون به محفظه افزوده می شود و از یک صفحه متخلخل جریان پیدا کرده و یک لایه محافظ در بالای کوره به وجود می آورد (6). بنابر گزارشات هر دو فرایند SPAL و LBI می تواند کیفیت مذاب را از نظر تمیزی، مقدار گاز و بازیابی عناصر آلیاژی نسبت به روش ذوب هوایی ارتقاء دهد.
(6 و 5) مقایسه هایی بین انواع مختلف رو ش های ذوب شامل AIM استاندارد در برابر 4 (VIM) و روش AIM استاندارد در برابر استفاده از SPAL (5) و LBI (6) انجام شده ولی یک مطالعه مقایسه ای AIM و VIM تحت اتمسفر گاز آرگون تاکنون انجام نگردیده است. همچنین جالب توجه خواهد بود که در این تحقیق دو روش SPAL و LBI در فرآیند ذوب هوایی تلفیق شد ه اند.
در مرکز تحقیقات متالوژی MATERIALS Canmet (کانادا) امکانات ذوب و ریخته گری گوناگون مانند SPAL ،AIM ،VIM و LBI وجود دارد. در تحقیق حاضر رو ش هایی VIM – Ar و AIM – Ar برای ریخته گری شمش های فولاد 80 X خط لوله استفاده شد. شمش های فولادی برای بررسی آلیاژ ، تحت نورد گرم قرار گرفتند. موارد مورد بررسی عبارت بودند از ترکیب شیمیایی، تمیزی، ریزساختار، استحکام کشش، چقرمگی ضربه از طریق آزمون چارپی با نمونه دارای شکاف V شکل.
2- روش آزمایش
آزمایشات شامل انتخاب مواد، ریخت هگری شمش های فولاد با روش VIM – Ar و AIM – Ar ، نورد گرم شمش ها و ارزیابی و آزمایشات بوده است.
-2-1 انتخاب مواد
فولاد 80 X خط لوله براساس استاندارد API5 برای مطالعه اثر رو ش های ذوب انتخاب گردید 80 X یک فولاد کم آلیاژ استحکام بالا 6 ( HSLA) بوده که به صورت تجاری و در معرض تحقیقات و توسعه در دسترس است این فولاد برای تولید لوله های به کار رفته جهت انتقال هر نوع سیال تحت فشار مانند نفت و مشتقات آن مناسب است (8 و 7)
-2 -2 روش VIM – Ar
یک کوره در محفظه ای القایی خاء در مرکز متالوژی Materials موجود است و محفظه 1 آن یک ظرفیت 25 کیلوگرمی Canmet ذوب فولاد با یک میکروبار خلاء دارد. محفظه 2 ظرفیت بیشتری برای ذوب فولاد در حد 200 کیلوگرم داراست که در تحقیق حاضر استفاده گردید. در جریان آزمایشات محفظه بزر گتر در حد 40 میلی بار تحت خلاء قرار گرفت و سپس گاز آرگون با فشار 800 میلی بار در آن دمیده و شارژ فولاد گرم شده و ذوب گردید.
درجه حرارت فولاد با استفاده یک پیرومتر مادون قرمز و ترموکوپل های غوطه ور شده تعیین می شود. برداشت نمونه های تعیین ترکیب شیمیایی، افزودنی های آلیاژی و اکسیدزداها می تواند از طریق حامل ترموکوپل غوطه شده انجام گردد. مذاب فولاد مستقیما از کوره به درون قالب نصب شده بر روی صفحه حاوی سیستم توزین ، بارریزی شد .درجه حرارت بارریزی °C 1640 و کمتر بوده و در هر ذوب 4 شمش به ابعاد mm 130 × 120 × 300 بارریزی گردیده که در شکل 1 کوره VIM پس از بارریزی مشاهده می شود. محفظه VIM معمولاً حداقل 2 ساعت بعد از بارریزی مگر در مواردی که گفته خواهد شد، بسته مانده است.
3-2- روش AIM – Ar
علاوه بر VIM یک سری کوره های AIM با ظرفیت های 5، 12 ، 25 ،100 و 250 کیلوواتی نیز در مرکز Materials Canmet موجود است که از کوره AIM با توان 100 کیلو وات و قطر بوته mm 180 با ظرفیت 50 کیلوگرم فولاد برای تحقیق حاضر استفاده شد. از همان قالب های شمش که برای روش VIM به کار گرفت برای آزمایشات AIM نیز استفاده شد لیکن از هر ذوب کوره 100 کیلوواتی AIM فقط یک شمش ریخته گری گردید.
به منظور پوشش کامل گاز آرگون هر دو سیستم SPAL و LBI بر روی کوره 100 کیلوواتی نصب شد (شکل 2). در فرآیند LBI جریان گاز آرگون با میزان 15 لیتر در دقیقه در هنگام ذوب دمیده شد. جریان آرگون مایع نیز از دستگاه SPAL قبل ذوب اولیه اضافه شده و در جریان فرآیند ذوب ادامه یافت. مذاب فولاد در درجه حرارت 1640درجه سانتی گراد پس از اکسیدزدایی با0/05 درصد آلومینیم درون کوره برای تمامی نمونه های ریختگی داخل قالب شمش بارریزی شده گاز آرگون استفاده شده در این تحقیق با خلوص یکسانN5 از یک شرکت تأمین گردید.
4-2 نورد گرم
از نورد گرم / سرد آزمایشی در مرکز متالورژی Materials Canmet تک باند با قدرت 600 اسب بخار و ظرفیت شاسی 500 تن حداکثر ضخامت قابل نورد 330 و حداکثر عرض 360 میل یمتر برای نورد گرم صفحات به صورت رفت و برگشت استفاده شد. شمش های فولادی به مدت 4 ساعت تا 1250درجه سانتی گراد تحت پوشش گاز، پیشگرم گردید. ضخامت شمش از 130 تا 25 میلیمتر پس از چند رفت و برگشت سریع کاهش یافت و به دنبال آن سه بار بصورت دقیق ابعاد نهایی به ضخامت 5/ 12 و پهنای حدود 250 میلیمتر رسانده شد. برای تمامی شمش ها پروفیل نورد به طور یکسان رعایت گردید.
5-2 آزمایش مواد
ترکیب شیمیایی به وسیله یک اسپکترومتر نشر نوری7 (OES) و مقادیر کربن، گوگرد، اکسیژن، نیتروژن و هیدروژن با استفاده روش احتراق با دستگاه شرکت LECO انداز ه گیری گردید، به علاوه ترکیب فولاد مجدداً با روش ICP 8 به وسیله آزمایشگاه Canada Exova مورد آزمایش قرار گرفت. نمونه صفحات نورد گرم شده با برش جت آب (شکل 3) بریده شده و قطعات برداشته شده برای آزمایش مکانیکی ماشین کاری گردیدند.
آزمایش کشش براساس استاندارد ASTM E8/E8M بر روی نمونه های چهار پهلو با ضخامت 5/ 12 میلیمتر و آزمایش مقاومت به ضربه چارپی بر روی نمونه های mm 10 × 10 با شکاف V شکل که مطابق استاندارد ASTM E23 ماشین کاری شدند، انجام شد. نمونه های چارپی از جهت عرضی ( TD ) برداشته شد و شکاف V شکل به نحوی از ضخامتماشین کاری گردید که ترک به وجود آمده به موازات جهت نورد باشد. آزمایش مقاومت به ضربه چارپی در سه درجه حرارت 25 ، 0 و 40-درجه سانتی گراد انجام گردید.
3- نتایج و سگالش
3-1 ترکیب شیمیایی
نتایج آنالیز شیمیایی در جدول 1 به همراه مقادیر اکسیژن و نیتروژن آورده شده است. ذوب 1V مربوط به کوره VIM – Ar و ذو ب های2 A تا 5A از کوره AIM – Ar بدست آمده است. نتایج ترکیب شیمیایی آلیاژ بدست آمده از ذوب در کوره AIM – Ar و VIM – Ar یکسان و سازگار هستند و تمامی آزمایشات مطابق الزامات برای فولاد خط لوله 80 X می باشد. ( 8). بنابر جدول 1 مقادیر گوگرد و فسفر در ذوب VIM – Ar اندکی از AIM – Ar پایین تر است. البته این امر مربوط به فرآیند VIM نبوده و به دلیل استفاده از آهن الکترولیتی و میل گرد آهن با خلوص بالاست که برای شارژ VIM به کار رفته در حال که در شارژ AIM – Ar حدود 50 درصد از قراضه فولاد AISI 1010 استفاده گردیده است.
براساس نتایج جدول 1 ذوب1 V نسبت به نمونه های AIM – Ar میزان اکسیژن پایین تری دارد هر چند از نظر مقدار نیتروژن قابل مقایسه هستند. جهت مقایسه یک ذوب استاندارد AIM فولاد X80 بدون استفاده از آرگون تهیه شد که مقدار اکسیژن آن از ppm 500تجاوز نمود که بسیار بالاتر از نمونه های Ar – AIM بوده است. این امر تائید می کند که پوشش Ar می تواند به طور مؤثری از مذاب فولاد محافظت کند. در این تحقیق غلظت هیدروژن برای تمامی نمونه های VIM – Ar و AIM – Ar بین ۲ تا 3 ppm بوده است.
2-3 خصوصیات مکانیکی
سختی برینل مانند ترکیب شیمیایی و عملیات حرارتی یک شاخص سریع بوده و میانگین سختی برینل نمونه های فولاد در شکل 4 ارائه شده است. بنابر نتایج نمونه های نورد شده به دلیل ریزساختار بینایتی نسبت به نمونه های ریختگی سختی بیشتری دارند ولی سختی نمونه های VIM – Ar و AIM – Ar تقریباً یکسان هستند.
در جدول 2 نتایج آزمایش کشش صفحات نورد شده از ذوب Ar –AIM نشان داده شده که در آن RD نمونه ها در جهت نورد، TD نمونه ها در جهت عرضی، Eu ازدیاد طول یکنواخت و Eg ازدیاد طول گلوگاهی هستند. ازدیاد طول یکنواخت ازدیاد طول در بیشینه بار اعمالی بوده و ازدیاد طول گلوگاهی کل ازدیاد طول یا ازدیاد طول تا مرحله شکست است. خصوصیات کشش نمونه های RD دارای ازدیاد طول نسبی بیشتر ولی استحکا م های تسلیم و نهایی پایین تری نسبت به نمونه های TD هستند.
در جدول 2 همچنین خصوصیات کششی فولاد تجاری 80 X (7)و خصوصیات طبق استاندارد 8( API) نیز ارائه شده است. با توجه به خصوصیات کششی و نتایج بدست آمده ، نمونه های AIM – Ar در محدوده مشخصات فولاد 80 X قرار دارد. متاسفانه هیچ آزمایش کششی بر روی سه ذوب 1V در جدول 1 ارائه نشده ولی خصوصیات کششی برای نمونه مشابه که با روش VIM – Ar تهیه گردیده (9) در دسترس است.
ازدیاد طول نسبی یکنواخت و گلوگاهی (ازدیاد طول کلی) به ترتیب 7 و 20 درصد بود ه اند (9). در تحقیق حاضر و مراجع ( 9 و 7) ضخامت کامل12.5 میلیمتری استوانه های کشش مورد استفاده قرار گرفتند. به نظر می رسد مشخصات کششی فولادهای تولید شده با رو ش های VIM – Ar و AIM – Ar یکسان و قابل مقایسه باشند.
تمامی نمونه های آزمایش ضربه چارپی با شکاف V شکل در تحقیق حاضر از جهت عرضی شمش های نورد شده برداشته و ماشین کاری شدند و نتایج 41 آزمون در مجموع در شکل 5 ارائه گردیده است. میانگین بالایی انرژی شکست برای نمونه های VIM در این آزمایش حدود 200 ژول (10) بوده و نتایج شکل 5 همچنین نشان می دهد که نمونه های VIM – Ar از نظر چقرمگی نسبت به نمونه های AIM – Ar در تمامی درجه حرارت ها برتر هستند.
3- 3 تمیزی و ریزساختارها
جهت درک اختلاف زیاد در نتایج چقرمگی ضربه برای نمونه های شکافدار، سه سری نمونه های متالوگرافی براساس شکل 5 آماده گردید.
– سری اول صفحات نورد شده از نمونه های VIM – Ar
– سری دوم نمونه های ریختگی گرفته شده از کوره تحت شرایط AIM – Ar
– سری سوم ریزساختارهای نمونه های صفحات نورد شده و اچ شده از نظر ترکیب شیمیایی، سختی برینل و خصوصیات کششی تفاوتی بین نمونه های تهیه شده به رو ش های VIM – Ar و AIM – Ar قابل تشخیص نیست هر چند تفاوت قابل تفکیکی در ریز ساختارها با میکروسکوپ نوری (شکل 6) بین صفحات تولید شده با این دو فرآیند ملاحظه می شود.
به علاوه در نمونه های AIM – Ar آخال های بیشتری از نوع طویل و دراز (شکل a 6) وجود دارد. تصویر SEM (شکل 7) به وضوح این آخال های کشیده را در نمونه های AIM – Ar نشان می دهد و در آنالیز EDS / SEM مشخص گردیده ترکیب این آخال ها آلومینا (AL2O3) حضور آخال های بیشتر بدون شک مرتبط با عملکرد نامنظم و غیرعادی نمونه های AIM – Ar در آزمایشات مقاومت به ضربه است.
در مقابل نمونه های VIM – Ar فقط دارای آخال های کروی بوده و بسیار تمیزتر(شکل b 6) می باشند. باید توجه داشت که ارتقای تمیزی و خصوصیات فولاد به دست آمده تحت تأثیر استفاده از مواد اولیه با خلوص بالاتر در تلفیق با روش خلاء است. برای یافتن علل تشکیل آخال در نمونه های AIM – Ar یک سری دوم نمونه های متالوگرافی (شکل 8) از کوره و شمش در شرایط ریختگی آماده شد.
درست بلافاصله بعد از تخلیه کوره و پس از اکسیژن زدایی حدود 250 گرم مذاب فولاد به عنوان نمونه کوره، به وسیله ملاقه برداشته شد و بعد از آن 45 کیلوگرم مذاب کوره در مدت 16 ثانیه درون قالب شمش بارریزی گردید. شمش در قسمت 12 میلیمتر بالای سطح به صورت افقی بریده شد و یک نمونه متالوگرافی برداشته و به عنوان نمونه شمش آماده شد. در نمونه برداشته شده از کوره فقط یک مقدار اندکی از آخال های ظریف و پخش شده (شکل a8) مشاهده گردید که مشابه نمونه VIM بود.
البته در نمونه برداشته شده از شمش (شکل b 8) در مقایسه با نمونه کوره آخال های بیشتر و درشت تر مشاهده می شود. آخال های بزرگ با یک دنباله احتمالا فیلم اکسید در شمش ریختگی در جریان نورد به صورت طویل و دراز، تغییر شکل می دهند که این امر می تواند علت چقرمگی ضربه ضعیف نمونه های AIM – Ar باشد.
در جریان آزمایشات در روش AIM – Ar مذاب فولاد در کوره دارای یک سطح تمیز با سرباره اندک بود و در تصاویر از نمونه کوره شکل(a 8) آخال های کروی ظریفی مانند نمونه های VIM – Ar مشاهده گردید. در تصاویر شکل 8 آخال های خشن با دنباله اکسیدی قابل رویت است که می تواند از تخلیه کوره، بارریزی و برخورد مذاب با کف قالب بوجود آمده باشند.
آزمایشات آینده AIM شامل پوشش آرگون برای جریان تخلیه و فرآیند بارریزی قالب بوده تا به جز پوشش های آرگون در کوره بتوان به شمش های ریختگی تمیزتری دست یافت. به جز آخال های غیرفلزی ریزساختار نمونه های فولاد صفحات نورد شده (برای فرآیندهای AIM – Ar و VIM – Ar یکسان بوده و شامل بینایت و فریت است (شکل 9). مجدداً در نمونه های AIM – Ar آخال های بیشتری به صورت نقاط تیره (شکل a 9) نسبت به ریزساختار بسیار تمیزتر (VIM – Ar شکل b 9) مشاهده می شود.
-4 نتیجه گیری
فولاد 80 X خط لوله تحت پوشش آرگون در کوره های VIM و AIM ذوب شد و شمش هایی به ضخامت 130 میلیمتر ریخته گری و تا ضخامت 5/ 12 میلیمتری نورد گرم گردید. ترکیب شیمیایی نمونه های AIM – Ar و VIM – Ar یکسان بوده فقط در نمونه های VIM – Ar اندکی مقدار اکسیژن پایین تر بوده است. تفاوت قابل ملاحظه ای در سختی برینل و خصوصیات کششی نمونه های ذوب شده با دو فرآیند مشاهده نشد لیکن نمونه های VIM – Ar ارتقای قابل توجهی در تمیزی فولاد و در نتیجه نتایج چقرمگی ضربه با نمونه شکا ف دار نسبت به نمونه های AIM – Ar داشته است. نکته حائز توجه این که نمونه کوره AIM – Ar نسبت به نمونه شمش بسیار تمیزتر بوده که نشان از احتمال اکسید شدن مجدد و تشکیل آخال در جریان تخلیه و بارریزی دارد.
1 . Vacuum Induction Melting 2 . Air Induction Melting 3 . Surface Protection Air Liquid 4 . Laminar Barrier Inerting
5 . American Petroleum Institute 6 . High Strength Low Alloy 7 . Optical Emission Spectrometry 8 . Inductively Coupled Plasma
منبع خارجی: A.F.S Trans. 2020
منبع فارسی: ماهنامه آذر 1402 – صنعت ریخته گری
ترجمه: عبدالحمید قدیمی
منابع:
- ASM Handbook, “Casting,” Vol. 15, ASM International, USA, ISBN
0-87170-007-7 (1998).
- ASM, “Superalloys Source Book,” ASM, Metals Park, OH, ISBN:
0-87170-170-7 (1984).
- TMS, “Conference Proc. of Energy Materials,” Xi’an, China, ISBN
978-1-119-02794-2, 2014.
- Golding, W.H., “Evaluation of Air Melted and Vacuum Melted AISI
4340 Steel,” U. S. Naval Air Engineering Center, Report No. NAECAML-
1947, 1964, pp. 1–64.
- Anderson, S.H., et al., “SPAL for the Investment Casters,” AFS
Trans., 89–123, p. 709 (1989).
- Sharma, S.K., Nowotarski, M.S., “Laminar Barrier Inerting for Induction
Melting,” Modern Casting, p. 54 (Nov. 1990).
مقالات و اخبار
یک نظر در “مقایسه فولاد خط لوله X80 ذوب شده در کوره القایی تحت اتمسفر گاز آرگون در هوا و کوره القایی تحت خلاء”
با تغییر روش ذوب میشه خواص مکانیکی فولاد رو به این شکل تغییر داد؟