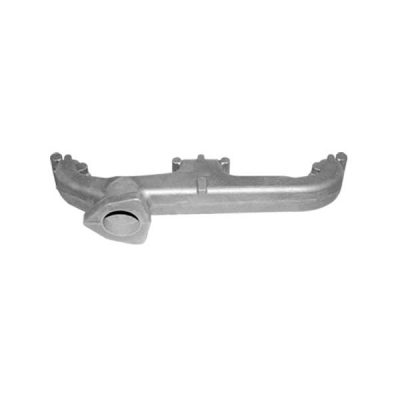
خانه » مقالات » اثر عملیات حرارتی بر ریز ساختار و خصوصیات مکانیکی فولاد مارتنزیتی کم آلیاژ مقاوم به سایش حاوی تیتانیم
اثر عملیات حرارتی بر ریز ساختار و خصوصیات مکانیکی فولاد مارتنزیتی کم آلیاژ مقاوم به سایش حاوی تیتانیم
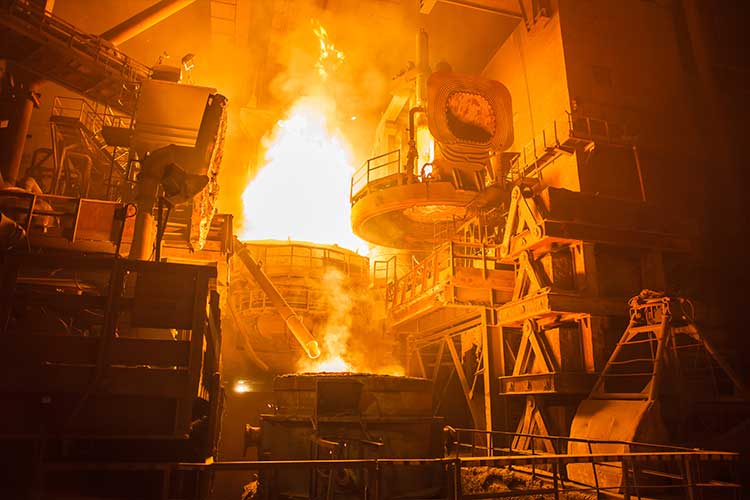
چکیده:
اثرات درجه حرارت کوئنچ و شرایط سرد شدن (خنک شدن در آب و آب حاوی ۱۰ درصد NaCl) بر ریزساختار و خصوصیات مکانیکی بر فولاد مارتنزیتی مقاوم به سایش حاوی ۲/ ۰ درصد تیتانیم استفاده شده برای صفحه پران قالب های دایکست مورد مطالعه قرار گرفت. نتایج نشان داد که مارتنزیت توفالی شکل می تواند پس از آستنیته کردن در C ۹۸۰° – ۸۶۰ و سپس خنک کردن در آب، به وجود آید. اما با افزایش درجه حرارت آستنیته کردن به تدریج مقدار رسوبات کاهش می یابد.
این رسوبات عمدتاً متشکل از و بوده و مقدار کل آنها بین ۱۵ /۱ تا ۶۴ /۱ درصد می باشد. غلظت فاز رسوبی در نمونه کوئنچ شده در آب بیشتر از نمونه کوئنچ شده در آب حاوی ۱۰ درصد NaCl است زیرا سرعت سرد شدن آن پایین تر است. اما با افزایش درجه حرارت آستنیته کردن سختی و استحکام کشش هر دو نمونه ابتدا افزایش و سپس کاهش می یابد. آزمایشات نشان می دهد بهترین خصوصیات جامع مکانیکی پس از آستنیته کردن در ۹۰۰°C و خنک کردن در آب حاوی ۱۰ درصد و سپس برگشت یا تمپر در ۲۰۰°C به دست می آید به طوری که سختی، استحکام نهایی کشش و مقاومت به فرسایش به ترتیب ۴/ ۵۵۱ برینل، ۱۴۳۸.۲ مگاپاسکال و میلی گرم بر متر خواهد بود.
1- مقدمه
صفحه پران یکی از اجزای اساسی قالب دایکست (ریخته گری پرفشار) است زیرا در جریان فرآیند دایکست اغلب تحت تنش های بالای فشاری و اصطکاک بوده و هزینه تولید و جایگزینی آن مطرح و قابل توجه می باشد. در نتیجه صفحه پران قالب دایکست باید مقاومت به فرسایش عالی داشته باشد. به همین منظور آلیاژهای مختلفی مانند فولاد پرمنگنز، چدن پرکروم و فولاد آستنیتی منگنزی برای تولید این قطعه به کار می رود (۳ تا ۱). البته فولاد پرمنگنز و چدن پر کروم به سختی در برابر فرسایش سایشی مقاومت کرده و قیمت آن ها نیز به دلیل وجود عناصر بالای آلیاژی رقابتی نیست (۳) فولاد آستنیتی منگنزی نیز تنها می تواند قابلیت سخت شوندگی بالایی در شرایط تنش بالا داشته باشد که برای صفحه پران مناسب نیست. (۴)
مشخص گردیده که فولاد مارتنزیتی کم آلیاژ مقاوم به فرسایش دارای قابلیت سخت بودن و مقاومت به فرسایش خوب، عملکرد کلی مناسب و قیمت پایینی بوده ) ۷ تا ۵( و بدین ترتیب برای صفحه پران در مقایسه با فولاد آستنیتی منگنزی و فولاد پرمنگنز آلیاژ مناسب تر است. بهینه سازی فرآیند عملیات حرارتی متداو ل ترین روش برای ارتقای ریزساختار و خصوصیات فولادهای مارتنزیتی است.
بهینه سازی فرآیند عملیات حرارتی متداو ل ترین روش برای ارتقای ریزساختار و خصوصیات فولادهای مارتنزیتی است (۹ و ۸) فرآیندهای عملیات حرارتی برای فولادهای مارتنزیتی عبارتند از آستنیته کردن، کوئنچ و برگشت (تمپر) و آستنیته کردن می تواند باعث اطمینان از انحلال رسوبات ریز در ساختار زمینه گردد. حضور رسوبات برای ممانعت از رشد دانه، ظریف شدن مارتنزیت توفالی شکل و ارتقای مقاومت به فرسایش فولاد مفید است (۱۴ تا ۱۰).
آستنیته کردن معمولاً منجر به ظریف شدن مارتنزیت های توفالی شکل در یک در درجه حرارت پایی نتر شده که باعث افزایش سختی و استحکام خواهد گردید (۱۶ و ۱۵).و ۸ فرآیندهای عملیات حرارتی برای فولادهای مارتنزیتی عبارتند از آستنیته کردن، کوئنچ و برگشت (تمپر) و آستنیته کردن می تواند باعث اطمینان از انحلال رسوبات ریز در ساختار زمینه گردد. حضور رسوبات برای ممانعت از رشد دانه، ظریف شدن مارتنزیت توفالی شکل و ارتقای مقاومت به فرسایش فولاد مفید است ( ۱۴ تا ۱۰). آستنیته کردن معمولاً منجر به ظریف شدن مارتنزیت های توفالی شکل در یک در درجه حرارت پایین تر شده که باعث افزایش سختی و استحکام خواهد گردید (۱۶ و ۱۵).
به علاوه، سرعت سرد شدن در فرآیند کوئنچ همچنین مستقیماً بر ساختار و خصوصیات مارتنزیت نیز مؤثر است. (۱۸ و ۱۷).محیط های متداول و معمول کوئنچ شامل هوا، آب، نمک و روغن بوده و ساختار مارتنزیت می تواند با کوئنچ در آب، آب نمک و روغن به دست آید.
در مقایسه با کوئنچ در آب، آب نمک سرعت سردکنندگی بیشتری داشته و میل به تغییر شکل و بروز ترک در آن کمتر است در حالی که روغن بالاترین سرعت خنک شوندگی را دارد ولی یک اثر منفی بزرگ بر محیط زیست داشته و گراتن تر نیز می باشد (19).
تیتانیم به عنوان یک عنصر کاربید زای قوی می تواند به همراه برخی عناصر غیرفلزی مانند C ، N و S تشکیل رسوبات حاوی تیتانیم داده و به میزان زیادی توزیع عناصر در فولاد را تغییر دهد (۲۴ تا ۲۰). لیکن به دلیل پایداری در درجه حرارت بالا و سختی زیاد (۳۲۰۰ ویکرز)، TiC می تواند ذرات ساینده را در جریان فرآیند فرسایش خرد کند و بدین ترتیب آسیب به ساختار زمینه کاهش می یابد.
در تحقیق قبلی نگارندگان برای ارتقای خصوصیات کشش فولادهای کم آلیاژ ۲/ ۰ درصد تیتانیم اضافه شد (۲۵). بنابراین تیتانیم یک عنصر آلیاژی مناسب برای فولاد مقاوم به فرسایش است.
اهداف تحقیق حاضر ابداع یک فرآیند عملیات حرارتی است که بتواند مقاومت به فرسایش فولاد مارتنزیتی کم آلیاژ حاوی۲/۰ درصد تیتانیم را برای صفحه پران ارتقاء دهد و ارتباط بین ریز ساختار، خصوصیات و فرآیند عملیات حرارتی نشان داده شود. پس از افزودن تیتانیم تأثیرات شرایط سرد شدن (خنک کننده آب و آب نمک) و درجه حرارت آستنیته کردن بر اندازه دانه، مقدار آستنیت باقی مانده و رسوبات به طور نظام مند مورد مطالعه قرار گرفت.
ارتباط بین مقاومت به فرسایش، رسوبات و سختی به تفصیل تشریح گردید. بدین ترتیب انتظار می رود یک مبنای نظری برای کاربرد صنعتی فولاد مقاومت به فرسایش مارتنزیتی کم آلیاژ حاوی تیتانیم از این تحقیق ایجاد شود.
2- روش آزمایش
2-1 آلیاژ
فولاد مورد مطالعه شمش های دگم های شکل بوده که در کوره تحت خلاء ذوب شدند. جدول ۱ ترکیبات شیمیایی فولاد آنالیز شده به وسیله اسپکترومتر نشر نوری SPECTRO-Max را نشان می دهد.
2-2 فرآیند عملیات حرارتی
منحنی انبساط حرارتی فولاد مورد مطالعه به وسیله یک دیلاتومتر حرارتی DIL 805 Pro مطابق استاندارد 12 – ASTM: E 831 اندازه گیری شد. بالاترین درجه حرارت و سرعت گرم کردن به ترتیب۱۰۰۰ و ۵ در دقیقه بود. درجه حرارت استحاله فازی و به ترتیب۶/ ۷۴۰ و ۵/ ۸۱۰ درجه سانتیگراد بوده که در شکل ۱ نشان داده شده است.
بر اساس درجه حرارت های استحاله اشاره شده، روند عملیات حرارتی مطابق شکل ۲ طراحی شد: ۱- آنیل کردن در C ۱۱۰۰° برای مدت ۲ ساعت و سرد کردن در کوره تا درجه حرارت محیط (اتاق) – ۲ آستنیته کردن در درجه حرارت های ۸۶۰، ۹۰۰ ، ۹۴۰ و ۹۸۰ درجه سانتیگراد برای مدت ۵ ساعت و سپس سرد کردن در آب و آب حاوی ۱۰ درصد ۳ NaCl – برگشت (تمپر)در ۲۰۰°C به مدت ۲ ساعت.
2-3 خصوصیات ریز ساختاری
پس از سنگ زنی، پولیش و خوردگی نمونه ها به وسیله میکروسکوپ نشر زمینه الکترونی ۱FESEM و میکروسکوپ نوری OM مورد مشاهده و بررسی قرار گرفتند. اندازه دانه آستنیت نمونه های سرد شده در آب پس از آستنیته کردن در درجه حرارت های مختلف به وسیله روش اکسید کردن آشکار گردید محلول استخراج الکترولیتی با ۳۷۵ میلی لیتر آب، ۱۲۰ میلی لیتر HCl و ۱۶ گرم اسید سیتریک تهیه شده پس سانتریفوژ و خشک کردن، رسوبات استخراج شده توزین و به وسیله یک دستگاه پراش اشعه Smart lab X XRD تحت سرعت اسکن ۱۰ درجه در دقیقه و زاویه اسکن تا ۱۰ مورد آنالیز قرار گرفتند.
خصوصیات ریز ساختاری به وسیله XRD مورد مطالعه واقع شد تا درصد حجمی آستنیت باقی مانده در فولاد مورد مطالعه تعیین گردد. سرعت اسکن ۱ درجه در دقیقه و زاویه اسکن ۴۰ تا ۱۰۰ بوده و پیک های( 200)α, (211)α, (200γ ( و )311 γ انتخاب شد تا شدت تجمیع شده تعیین شود. نیز از معادله به دست آمد (۴):
درصد حجمی کاربید که در این محاسبه به دلیل درصد حجمی پایین کاربیدها در نظر گرفته نشده، IA و IM شدت تجمیعی آستنیت ( A) و مارتنزیت ( M) در پیکهای پراش یافته بوده و G نیز فاکتور ساختاری مرتبط به مارتنزیت و آستنیت است.
2-4 آزمایش خصوصیات مکانیکی
با استفاده یک دستگاه آزمون اصطکاک عمودی 5000 MFT تحت بار ۶۰ نیوتن، شعاع دوران ۱۰ میلیمتر و سرعت چرخش۱۰۰ دور در دقیقه آزمایش اصطکاک خشک انجام شد. آزمایش مقاومت به فرسایش نیز با روش پین بر روی دیسک با استفاده یک دیسک از فولاد GCr15 با سختی ۶۱ راکول ‘ C انجام شد. میزان فرسایش نیز از معادله ۲ محاسبه گردید:
=E0 جرم پین قبل از آزمایش اصطکاک
=E1 جرم پین پس از آزمایش اصطکاک
=S’ فاصله و طول مسافت لغزش
نمونه های کشش نیز پس از عملیات حرارتی به روش وایرکات با ضخامت ۱ میلیمتر و پهنای ۴ میلیمتر و طول ۱۰ میلیمتر بریده و آماده شدند. نمونه های کشش در درجه حرارت محیط (اتاق) به وسیله یک دستگاه کشش الکترونیک CMT 5105 مورد آزمایش قرار گرفتند.
3- نتایج و سگالش
3-1 محاسبات ترمودینامیک
نمودار تعادل فازی به وسیله نرم افزار شبیه سازی Thermo Calc محاسبه شد (شکل ۳) که در آن می توان دریافت که رسوبات نوع MC و ( TiC برای تحقیق حاضر) به طور موفقیت آمیزی در حدود ۱۴۰۰°C هنگام انجماد تشکیل شده اند. در جریان فرآیند عملیات حرارتی درصد حجمی پایدار باقی مانده که نشان می دهد به آسانی حل نمی شود در حالی که رسوبات MC به تدریج درون ساختار زمینه در مرحله درجه حرارت بالا حل شدند. هنگامی که درجه حرارت به بالاترین حد (C ۹۸۰°) رسید مقدار زیادی رسوبات حل شده در فولاد باقی مانده بود. در هنگام فرآیند سرد شدن فاز MC به طور فزایند های رسوب کردند. در درجه حرارت محیط (اتاق) فولاد مورد آزمایش دارای فازهای ، MC و MnS است. نکته حائز توجه این که مقدار اندکی از رسوبات در درجه حرارت تجزیه شده و اتم های S خارج شده از این رسوبات تشکیل آخال های Mn S می دهند در حالی که اتم های با اتم های C ترکیب می شوند و بدین ترتیب به صورت ناگهانی درصد حجمی رسوبات MC افزایش می یابد.
3-2 ریزساختار
شکل ۴ ریزساختارهای نمونه های خنک شده در آب از درجه حرارت های مختلف آستنیته کردن را نشان می دهد که عمدتاً متشکل از مارتنزیت و یک مقدار اندکی آستنیت باقی مانده پس آستنیته و برگشت (تمپر) کردن است. هنگامی که فولاد در درجه حرارت پایین تر آستنیته می شود مارتنزیت توفالی شکل ظریف تر بوده و توزیع ریزساختار یکنواخ تتر است، در حالی که با افزایش درجه حرارت آستنیته کردن مارتنزیت توفالی شکل به تدریج درش تتر می شود.
در شکل ۵ مورفولوژی دانه های آستنیت در نمونه هایی که در درجه حرارت های مختلف آستنیته شده و در آب خنک گردیده اند ارائه شده که در آنها دانه های آستنیت موجود و مرز دانه ها به وضوح مشاهده می شود.
جدول ۲ اندازه دانه فولاد های مورد مطالعه که در درجه حرارت مختلف آستنیته شدن نشان می دهد. اندازه دانه ها با افزایش درجه حرارت آستنیته کردن روند آرام افزایشی داشته است. در درجه حرارت آستنیته اندازه دانه حداقل بوده و فقط ۳۲ / ۱۸ میکرون بوده در حالی که با افزایش درجه حرارت تا اندازه دانه آستنیت به حداکثر مقدار یعنی ۹۲ / ۲۴ میکرون رسیده است.
در جریان آستنیته کردن هم زمان انحلال و درشت شدن رسوبات نیز ایجاد م یشود. هنگامی که درجه حرارت انحلال رسوبات کمتر از درجه حرارت آستنیته کردن است رسوبات به تدریج حل م یشوند ) ۲۶ (. از سویی دیگر اگر درجه حرارت آستنیته کردن پایین تر از درجه حرارت انحلال رسوبات باشد براساس مکانیزم(۲۷ Ostwald) ذرات بزرگتر با جذب اجزای فوق اشباع درش تتر م یشوند و در نهایت ذرات کوچک تر به تدریج حل شده و ذرات بزرگتر، درشت تر می شوند.
رسوبات در جریان فرآیند گرم شدن اثر قفل کردن در مرز دانه های آستنیت را دارند.(۲۹ و ۲۸) اما این اثر بستگی به اندازه ذرات دارد و م یتواند به وسیله معادله ۳ تشریح شود. (30):
=DC اندازه دانه آستنیت ، = f درصد حجمی رسوبات
=d میانگین قطر رسوبات ، = Z ثابت
بنابراین با افزایش درجه حرارت آستنیته کردن رسوبات ظریف به آرامی حل می شوند و مقدار رسوبات با اندازه بزرگ افزایش می یابد که این امر اثر قفل کردن در مرز دانه ها را تضعیف می نماید و موجب درشت شدن دانه های آستنیت می گردد. اما در محدوده با افزایش درجه حرارت آستنیته کردن، اندازه افزایش درجه حرارت آستنیته کردن رسوبات به تدریج حل شده و میزان عناصر آلیاژی در آستنیت بالا م یرود و افزایش کربن فوق اشباع و اعوجاج شبکه بلوری در مارتنزیت پس از کوئنچ باعث بالا رفتن سختی و استحکام کششی فولاد خواهد شد.
دانه های آستنیت به تدریج افزایش می یابد ولی هیچ رشد غیر نرمال در دانه های آستنیت مشاهده نمی شود. براساس تحقیق قبلی، هر چند کاربیدهای ریز MC در هنگام آستنیته کردن در حل می شوند ولی هنوز رسوبات زیادی با اندازه بزرگ وجود داردند. که می توانند به طور مؤثری مرز دانه های آستنیت را قفل کرده تا از رشد غیرنرمال دانه ها در فولاد مورد تحقیق جلوگیری نماید.
3-3 خصوصیات مکانیکی
شکل ۶ نتایج آزمایشات سختی سنجی و کشش نمونه های فولادی عملیات حرارتی شده در شرایط مختلف را نشان می دهد. با افزایش درجه حرارت آستنیته کردن هر دو نمونه های کوئنچ شده در آب و آب نمک ابتدا روند افزایشی در سختی و استحکام کشش دارند ولی سپس این روند کاهشی می شود. این تغییر به عللی بدین شرح است:
هنگامی که درجه حرارت آستنیته کردن پایین است. انحلال کاربیدها دشوار بوده و پس از کوئنچ و تمپر (برگشت) مقدار کربن و سایر عناصر آلیاژی در زمینه مارتنزیتی پایین است که در نتیجه سختی و استحکام کشش پایین خواهد بود. اما با افزایش درجه حرارت آستنیته کردن رسوبات به تدریج حل شده و میزان عناصر آلیاژی در آستنیت بالا می رود و افزایش کربن فوق اشباع و اعوجاج شبکه بلوری در مارتنزیت پس از کوئنچ باعث بالا رفتن سختی و استحکام کششی فولاد خواهد شد.
البته هنگامی که درجه حرارت آستنیته کردن بالاست تعداد زیادی از عناصر آلیاژی در آستنیت تجمیع یافته و باعث پایداری آن شده لذا مقدار آستنیت باقی مانده نیز افزایش می یابد. به علاوه افزایش درجه حرارت آستنیته کردن موجب افزایش در انحلال کاربید می شود (۳۱).
اثر استحکام دهی رسوبات به دلیل انحلال کاربیدهای حاوی Ti تضعیف شده و اثر قفل کنندگی البته هنگامی که درجه حرارت آستنیته کردن بالاست تعداد زیادی از عناصر آلیاژی در آستنیت تجمیع یافته و باعث پایداری آن شده لذا مقدار آستنیت باقی مانده نیز افزایش م ییابد. به علاوه افزایش درجه حرارت آستنیته کردن موجب افزایش در انحلال کاربید می شود (۳۱).
اثر استحکام دهی رسوبات به دلیل انحلال کاربیدهای حاوی Ti تضعیف شده و اثر قفل کنندگی ذرات فازی ثانویه بر مرز دانه های آستنیت نیز کاهش می یابد و در نتیجه اندازه دانه ها بزرگ می شوند. به این علت با افزایش درجه حرارت آستنیته کردن اندازه مارتنزیت توفالی شکل پس از کوئنچ افزایش یافته است (شکل ۴) که تأثیر معکوس و کاهشی بر سختی و استحکام کشش خواهد داشت. در شکل ۷ مورفولوژی شکست نمونه فولادی سرد شده در آب تحت درجه حرارت های مختلف عملیات حرارتی ارائه شده که در آن ها صفحات کوچک کلیواژ و تعدادی فرو رفتگی (دیمپل) در سطح شکست نمونه فولادی آستنیته شده در (شکل ۷a) مشاهده می شود. شکست نیمه کلیواژ (ترد) بوده و ازدیاد طول نسبی فولاد مطابق شکل ۶b معادل ۸/ ۶ درصد است.
با افزایش درجه حرارت آستنیته کردن به صفحه کلیواژ بزرگترشده و تعداد فرورفتگی ها دیمپل (کمتر گردیده)شکل ۷b و بدین ترتیب ازدیاد طول نسبی فولاد هم کاهش یافته و به۷/ ۵ درصد رسیده بنابراین این شکست کلیواژ و ترد است. با افزایش درجه حرارت آستنیته کردن به سطح کلیواژ کاهش یافته و تعداد فرورفتگی ها (دیمپل) افزایش و ازدیاد طول نسبی نیز دوباره به ۱/ ۷ درصد رسیده است (شکل ۷c). هنگامی که درجه حرارت آستنیته کردن با افزایش به رسیده هرچند سطح کلیواژ زیاد شده، تعداد فرورفتگی ها (دیمپل) هم افزایش داشته و شکست نیز به صورت نیمه کلیواژ(شکل ۷d (و مقدار ازدیاد طول نسبی نیز بیشترین مقدار یعنی ۴/ ۷ درصد بوده است.
شکل ۶ همچنین نشان می دهد که سختی و استحکام کشش نمونه فولادی که در آب حاوی ۱۰ درصد NaCl سرد شده نسبت به آب معمولی اندکی بالاتر است زیرا سرعت سرد شدن درآب نسبت به آب نمک آهسته تر است. هنگامی که استحاله مارتنزیت در فولاد به وجود می آید، سرعت آرام سرد شدن نیروی پیش برنده آستنیت برای تبدیل به مارتنزیت را کم می کند و در نتیجه در این تحول تأخیری به وجود می آید. از سویی دیگر با افزایش پایداری آستنیت درصد حجمی بالاتری آستنیت در فولاد سرد شده در آب باقی می ماند. البته هنگامی که فولاد در آب حاوی ۱۰ درصد NaCl سرد شده سرعت سرد شدن بیشتر بوده آستنیت فوق تبرید شده و به سرعت در جریان سرد شدن به پایین فقط که مرتبط با استحاله مارتنزیت است، می رسد.
به طور کلی یک سرعت بالاتر سرد شدن زمان نفوذ اتمی کوتاه م یکند و در نتیجه جوانه زنی مارتنزیت و زمان رشد آن کاهش یافته و سرعت جوانه زنی و پایداری حرارتی آن افزایش می یابد و حاصل آن یک ساختار مارتنزیت ظریف تر خواهد بود. همچنین افزایش سرعت سرد شدن از رسوب ذرات کاربید از آستنیت جلوگیری کرده، قابلیت انحلال فاز جامد C افزایش یافته در حالی که درصد حجمی آستنیت باقی مانده در زمینه مارتنزیت کاهش می یابد در نتیجه سختی زمینه بالا می رود.
3-4 رسوبات
نمونه های فولادی که تحت دو شرایط سرد شدن با آب و سرد شدن در آب حاوی ۱۰ درصد NaCl و به دنبال آن تمپر (برگشت) در، تحت استخراج الکترولیتی رسوبات قرار گرفته و نتایج در شکل ۸ ارائه شده است. هنگامی که نمونه های فولادی از درجه حرارت مختلف آستینه کوئنچ شده اند رسوبات هر دو سری نمونه ها که با دو روش کوئنچ شده اند متشکل از Ti4C2S2 TiC , (شکل های ۸b و ۸a) است. TiNدر نمونه های فولادی باقی می ماند زیرا نیروی اتصال بین اتم های Ti و N نسبت به اتم های C و S بالاتر است ولی مقدار N بسیار اندک بوده به طوری که دستگاه XRD نمی تواند TiN را تشخیص دهد بدین ترتیب مقدار آن در آنالیز ارائه نشده است.
شکل ۸c نشان می دهد با افزایش درجه حرارت آستنیته کردن از ۸۶۰°C به ، مقدار رسوبات با سرد شدن در آب ۷/ ۲۹ درصد و در آب نمک ۳۵ درصد کاهش یافت. از آنجا که سرعت سرد شدن در آب نسبت به آب حاوی ۱۰ درصد NaCl آرام تر می باشد، در فرآیند سرد شدن اتم ها زمان طولانی تری برای نفوذ و تجمع در مرز دانه دارند. بنابراین در درجه حرارت های مختلف آستنیته کردن مقدار رسوبات نمونه سرد شده در آب نسبت به نمونه سرد شده در آب حاوی ۱۰ درصد NaCl بیشتر است.
درصد رسوبات از طیف های XRD محاسبه شد (شکل ۸d) و در آن می توان مشاهده نمود که رسوبات نمونه های آستنیته شده در و سرد شده در آب و آب حاوی ۱۰ درصد NaCl متشکل از TiC و یک مقدار اندک به ترتیب ۷۶ و۷۴ درصد بوده است. با افزایش درجه حرارت آستنیته کردن تا درصد رسوبات TiC به تدریج کاهش یافته و به ترتیب ۶۱ و ۵۳ درصد خواهند شد. در شکل ۳ از نتایج شبیه سازی نمودار فازی می توان مشاهده نمود غلظت TiC به تدریج کاهش یافته ولی مقدار هنگام افزایش حرارت از ثابت باقی مانده است.
3-5 آستنیت باقی مانده
آنالیز فازی XRD نمونه ها آستنیته شده در درجه حرارت های مختلف در شکل ۹ مشاهده می شود. درصد آستنیت باقی مانده Vγ محاسبه شده براساس معادله ( ۱ )به صورت خلاصه در جدول۳ ارائه شده که در هر دو نمونه های کوئنچ شده در دو روش با افزایش درجه حرارت آستنیته کردن مقدار Vγ افزایش می یابد.
علت این امر انحلال تدریجی یک مقدار اندک رسوبات حاوی Ti در آستنیت با افزایش درجه حرارت آستنیته و پایین آمدن نقطه Mf و در نتیجه افزایش آستنیت باقی مانده است. به علاوه پس از رسیدن به سرعت سرد کردن بحرانی در سرعت بیشتر سرد شدن مقدار آستنیت باقی مانده کمتر خواهد بود(۴)علت این است که سرعت سرد شدن شتاب یافته فوق تبرید را افزایش داده، در نتیجه نیروی پیش برنده استحاله آستنیت به مارتنزیت بالا می رود.
بنابراین در مقایسه با نمونه سرد شده در آب حاوی ۱۰ درصد NaCl با سرعت سرد شدن بیشتر در نمونه سرد شده در آب آستنیت باقی مانده بیشتر است.
3-6 آزمایش مقاومت به فرسایش
شکل ۱۰ مقدار مقاومت به فرسایش نمونه های فولادی آستنیته شده در درجه حرارت های مختلف و شرایط سرد شدن متفاوت را نشان می دهد. بنابر نتایج با افزایش درجه حرارت آستنیته کردن ۹۰۰°C مقاومت به فرسایش ابتدا کاهش و سپس افزایش می یابد. هنگامی که در درجه حرارت آستنیته کرده و نمونه در آب حاوی ۱۰ درصد NaCl سرد شده مقدار فرسایش کمترین میزان را داشته و معادل 2- 0.48X10 میلی گرم بر متر بوده است.
برای بررسی بیشتر اثر درجه حرارت آستنیته کردن بر مکانیزم فرسایش، سطح فرسایش یافته نمونه فولادی سرد شده در آب حاوی ۱۰ درصد NaCl به وسیله الکترون میکروسکوپ SEM مورد مطالعه قرار گرفت. براساس شکل ۱۱ مورفولوژی سطح فرسایش یافته مشاهده می شود تفاوت های قابل ملاحظ های با افزایش درجه حرارت آستنیته کردن به وجود آمده است.
به طور کلی شیارهای موازی زیادی بر روی سطح پخش شده که در اثر حرکت ذرات سخت بر روی سطح اصطکاک به وجود آمده و نشان دهنده مکانیزم فرسایش سایشی شیار ساز می باشد. هنگامی که درجه حرارت آستنیته به ۹۰۰°C رسیده توان مشاهده کرد که پهنا و عمق خراش ها کوچ کتر شده و رسوبات میکرونی و کوچک تر در مقایسه با نمونه آستنیته می شده در ۸۶۰°C ، در سطح پخش شده است. با افزایش بیشتر درجه حرارت آستنیته کردن خراشیدگی های به وجود آمده به وسیله ذرات ریز بر روی سطح فرسایش یافته پهن تر و عمیق شده و ناحیه تغییر شکل پلاستیک یافته در امتداد مسیر لغزش فرسایشی ظاهر می شود.
در مقایسه با نمونه آستنیته شده در C ° ۹۴۰ ، درجه فرسایش نمونه فولادی در C ° ۹۸۰ شدیدتر بوده که در آن خراشیدگی های عمیق، نواحی بیرون زده و یک تعداد اندکی حفره ها نمایش از کنده شدن به همراه کاهش رسوبات وجود دارد. این موضوع می تواند مرتبط با این حقیقت باشد که درجه حرارت آستنیته کردن بسیار بالاست و سختی پایین زمینه مارتنزیتی امکان بیشتری را برای تماس بین ذرات ساینده و سطح تحت فرسایش فراهم می نماید.
سطح تحت فرسایش قرار گرفته بیشتر دچار تغییر شکل پلاستیک شده و ذرات ساینده با آسانی بیشتری به ساختار زمینه می چسبند در نتیجه شیارها عمیق تر و پهن تر می شوند. به علاوه ساختار زمینه تحت عمل ذرات سخت ساینده در فرآیند اصطکاک تغییر شکل داده و سخت می شود. اما سطح زیری نیز به تدریج دچار ترک هایی شده و تحت عملکرد تنش سطح تماس، به سطح فرسایش متصل می شود و در اثر آن برخی ساختارهای لایه های نازک افتاده و از حفرات ناشی از کنده شدن پوسته جدا می شوند.
برای آگاهی از نوع و مورفولوژی رسوبات بر روی سطح فرسایش یافته نمونه های فولادی در شکل ۱۱ ، آن ها جمع آوری شده و به وسیله یک میکروسکوپ قوی الکترونی SEM تحت آنالیز قرار گرفته و نتایج به دست آمده در تصاویر ۱۲ و ۱۳ ارائه شده است.
با تلفیق شبیه سازی نمودار فازی (شکل ۳)، آزمایش XRDشکل ۸ و نتایج آنالیز EDS می توان مشاهده نمود رسوبات عمدتاً متشکل از ذرات کروی TiC و ذرات میل های دراز هستند. از آنجا که زمینه مارتنزیتی به دشواری می تواند مانع خارج شدن و فرو رفتن ذرات ساینده سخت در جریان فرآیند اصطکاک شود، سطح در تماس بین ذرات ساینده و فولاد مورد آزمایش یک تنش تماسی بزرگی را با افزایش زمان فرسایش تحمل می کند و باعث می شود ساختار سطحی زمینه دچار آسیب شده و با جدا شدن مواد، شیارهایی به وجود آید. وجود رسوبات حاوی Ti می تواند مقاومت به فرسایش را افزایش دهد و مورفولوژی سطح فرسایش را تا حدی ارتقا دهد. مکانیزم اصلی این پدیده را می توان بدین شرح خلاصه نمود:
۱- ذرات میکرونی و کوچکتر از میکرون TiC و می تواند به صورت برجستگی میکرونی در سطح، ناحیه تماس بین ذرات ساینده و ساختار زمینه را کاهش دهد و به طور اثربخشی از فرو رفتن ذرات درون ساختار زمینه جلوگیری کند. هنگامی که ذرات در تماس با سطح فرسایش قرار میگیرند ابتدا باعث ایجاد خراش شده تا این که خرد می شود و از روی سطح پایین می افتند. بنابراین رسوبات حاوی Ti نه فقط می توانند تا حد امکان زمینه را از فرسایش محافظت نمایند بلکه مقاومت به تغییر شکل زمینه را نیز توسعه داده تا بدین ترتیب از ساختار زمینه محافظت کرده و مقدار خسارت ناشی از فرسایش را کاهش دهند.
۲- رسوبات ظریف می توانند به طور مؤثری مرز دانه های آستنیت را مختل کرده و از رشد دانه های آستنیت جلوگیری کنند بدین ترتیب ناحیه مرز دانه مارتنزیتی پس از کوئنچ به میزان زیادی افزایش می یابد ( ۲۳ ). به همین دلیل ناحیه بزرگ مرز دانه می تواند انرژی بیشتری را در جریان توسعه ترک جذب کند که برای ممانعت از رشد ترک مفید است. به علاوه ماتنزیت توفال شکل با اندازه کوچک می تواند همچنین نقش ثابت نگهدارنده و حمایت ذرات حاوی تیتانیم باشد و از جدا شدن ذرات در هنگام فرآیند جلوگیری کرده و مقاومت فولاد را افزایش دهد.
۳- رسوبات حاوی تیتانیم در زمینه مارتنزیتی پخش شده که می تواند اثر استحکام دهی داشته سختی زمینه را افزایش دهد و یک نقش قابل توجه نیز در ارتقای مقاومت به فرمایش فولاد مورد بررسی ، داشته باشد. شکل ۱۴ نشان دهنده یک نمودار فرضی از سیر تحول ذرات و مکانیزم فرسایش فولاد مورد بررسی آستنیته شده در درجه حرارت های مختلف است. در فرآیند ذوب و انجماد اتم های تیتانیم ابتدا با سایر اتم ها در مرز دانه ها ترکیب می شود. متناسب با درجه حرارت رسوب دادن و انرژی آزاد استاندارد ترکیبات تولید شده، رسوبات TiC ، TiN و به وجود می آید( ۳۴ و ۳۳ ). همانطور که در شکل ۱۴a نشان داده شده هنگام آستنیته کردن در C۹۰۰° هر چند که درجه حرارت نگهداری بالای است هنوز یک تعداد زیادی از رسوبات در ناحیه مرز دانه ها به دلیل پایداری رسوبات حاوی Ti در درجه حرارت بالا می تواند از رشد غیرنرمال دانه های آستنیت جلوگیری کنند.
اما با افزایش درجه حرارت قابلیت انحلال TiC افزایش یافته و مطابق مکانیزم Ostwald ذرات کوچک تر TiC در مرز دانه و یا درون دانه در زمینه حل می شوند تا ذرات بزرگ TiC به وجود آید در نتیجه مطابق شکل ۱۴b تعداد ذرات TiC کاهش می یابد.
به علاوه ذرات درش تتر TiC و Ti4C2S2 در مرز دانه در همان ناحیه باقی می مانند زیرا نمی توانند حل شوند که این امر با نتایج آماری ذرات استخراج شده، هم خوانی دارد. همچنین انحلال ذرات کوچک TiC و تشکیل ذرات درشت TiC اثر قفل کردن در مرز دانه را تضعیف کرده اما رسوبات درشت حاوی Ti هنوز به طور مؤثری مرز دانه را قفل می کنند. دانه های آستنیت در جریان درجه حرارت بالای آستنیت درشت و خشن می شوند لیکن دچار رشد غیرنرمال نمی گردند. تحت شرایط ثابت از نظر بار اعمال شده به دلیل وجود رسوبات حاوی Ti با سختی بالا بر روی سطح نمونه فولادی مورد مطالعه فرو رفتن ذرات ساینده به درون ساختار زمینه دشوار خواهد بود. اما هنگامی سطح هنگام لغزش با رسوبات درشت در تماس قرار می گیرد، گوشه های تیز آنها از بین رفته و در نتیجه قابلیت فرسایش ساختار زمینه کاهش می یابد. از نقطه نظر مطالعه درشت ساختار (ماکروسکوپی) شیارهای مقعر بر روی سطح فرسایش نمونه فولاد مورد بررسی مطابق شکل ۱۴e کم عمق است.
با افزایش درجه حرارت آستنیته کردن از ۹۰۰ به C ° ۹۸۰ سختی نمونه فولادی و مقدار رسوبات ظریف کاهش یافته بنابراین ذرات ساینده سطح را بیشتر دچار خراش کرده، درون ساختار زمینه نفوذ می کنند و موجب ایجاد شیارهای عمیق و افزایش تلفات فرسایشی خواهند شد (شکل ۱۴f).
4- نتیجه گیری
اثرات درجه حرارت آستنیته کردن و شرایط سرد شدن بر ریز ساختار و خصوصیات یک فولاد مارتنزیتی کم آلیاژ مقاوم به فرسایش حاوی ۲/ ۰ درصد تیتانیم به طور نظامند مورد بررسی قرار گرفت و نتایجی بدین شرح به دست آمد:
۱- ۴ با خنک کردن در آب و آب حاوی ۱۰ درصد NaCl در درجه حرارت حرارت های مختلف آستنیته کردن یک ساختار مارتنزیتی با شکل توفالی به وجود آمد. اندازه دانه نمونه های فولادی سرد شده با آب با افزایش درجه حرارت آستنیته کردن به تدریج افزایش یافت تا یک مقدار حداکثر یعنی ۹۲ / ۲۴ میکرون در C ۹۸۰°. با سرد کردن در آب حاوی ۱۰ درصد NaCl فولاد آستنیته شده در C ° ۹۰۰ بهترین تلفیق خصوصیات مکانیکی یعنی سختی ۴/ ۵۵۱ برینل، استحکام نهایی کشش ۲/ ۱۴۴۸ مگاپاسکال و ازدیاد طول نسبی ۳/ ۵ درصد حاصل گردید.
۲- ۴ رسوبات به وجود آمده در فولاد مورد مطالعه عمدتاً متشکل از TiC و بوده است. با افزایش درجه حرارت آستنیته کردن، مقدار رسوبات برای هر دو شرایط سرد شدن یعنی در آب و در آب حاوی ۱۰ درصد NaCl کاهش یافت اما در فولاد سرد شده در آب نسبت به آب نمک مقدار رسوبات ۰۴ / ۰ تا ۱۵ / ۰ درصد بالاتر بود.
۳- ۴ فرسایش سایشی منجر به ایجاد شیار مکانیزم غالب و اصلی برای تمامی نمونه های فولادی آستنیته شده در درجه حرارت مختلف بود. اما با افزایش درجه حرارت آستنیته کردن تحت هر دو شرایط سرد شدن میزان فرسایش نمونه ها ابتدا کاهش سپس افزایش یافت. کمترین مقدار فرسایش 2- 0.48X10 میلی گرم در متر بوده که برای نمونه آستنیته شده در C ° ۹۰۰ و سرد شده در آب حاوی ۱۰ درصد نمک بوده است.
منبع فارسی: ماهنامه مهر 1402 – صنعت ریخته گری
ترجمه: مرتضی اسالمبلچی مقدم
منبع خارجی: 23 4/ :No Foundry China
منابع:
[1] Du X D, Yang X J, Wang Y F, et al. Impact corrosion wear
properties and mechanism of lining board steels. Journal of
Engineering Tribology, 2009, 223(4): 729-733.
[2] Chen P, Wu Z Y, Yi Y L, et al. Effect of surface Cr/C infiltration
on microstructure, mechanical properties and wear
resistance of high chromium cast iron. China Foundry, 2022,
19(3): 218-224.
[3] Xu L J, Wei S Z, Xiao F N, et al. Effects of carbides on
abrasive wear properties and failure behaviours of high speed
steels with different alloy element content. Wear, 2017, 376-
377: 968-974.
[4] Zhang J C, Zhang T, Yang Y T, et al. Microstructure and
properties evolution of Nb-bearing medium Cr wear-resistant
cast steel during heat treatment. Journal of Iron and Steel
Research International, 2021, 28(6): 739-751. 338
CHINA FOUNDRY Vol . 20 No. 4 July 2023 Research & Development
[5] Valtonen K, Ojala N, Haiko O, et al. Comparison of various
high-stress wear conditions and wear performance of
martensitic steels. Wear, 2019, 426-427: 3-13.
[6] Zou J L, Liu S L, Zheng Z B, et al. Research on impact-abrasioncorrosion
behavior of three typical wear-resistant steels
under high impact energy. Journal of Materials Engineering
and Performance, 2022, 31(6): 4343-4353.
[7] Liu L J, Liang X K, Liu J, et al. Precipitation process of TiC
in low alloy martensitic steel and its effect on wear resistance.
ISIJ International, 2020, 60(1): 168-174.
[8] Kong W X, Liang L, Chen Y L, et al. Microstructure evolution
and strengthening of a new high-nitrogen heat-resistant
martensitic steel regulated by heat treatment. JOM, 2021,
73(11): 3149-3157.
[9] Deng X, Wang Z, Han Y, et al. Microstructure and abrasive
wear behavior of medium carbon low alloy martensitic
abrasion resistant steel. Journal of Iron and Steel Research
International, 2014, 21(1): 98-103.
[10] Pawlak K, Biaobrzeska B, Konat U, et al. The influence of
austenitizing temperature on prior austenite grain size and
resistance to abrasion wear of selected low-alloy boron steel.
Archives of Civil and Mechanical Engineering, 2016, 16(4):
913-926.
[11] Huang L, Deng X T, Li C R, et al. Effect of TiC particles on
three-body abrasive wear behaviour of low alloy abrasionresistant
steel. Wear, 2019, 434-435: 202971.
[12] El-Faramawy H S, Ghali S N, Eissa M M. Effect of titanium
addition on behavior of medium carbon steel. Journal of
Minerals & Materials Characterization & Engineering, 2012,
11(11): 1108-1112.
[13] Mao X, Huo X, Sun X, et al. Strengthening mechanisms
of a new 700 MPa hot rolled Ti-microalloyed steel produced y
compact strip production. Journal of Materials Processing
Technology, 2010, 210(12): 1660-1666.
[14] Bikmukhametov I, Beladi H, Wang J, et al. The effect
of strain on interphase precipitation characteristics in a Ti-Mo
steel. Acta Materialia, 2019, 170: 75-86.
[15] Wang C F, Wang M Q, Shi H, et al. Effect of microstructure
refinement on the strength and toughness of low carbon
martensitic steel. Journal of Materials Science & Technology,
2007, 23(5): 659-664.
[16] Morito S, Saito H, Ogawa T, et al. Effect of austenite grain
size on the morphology and crystallography of lath martensite
in low carbon steels. Transactions of the Iron & Steel Institute
of Japan, 2005, 45(1): 91-94.
[17] Tsai M C, Chiou C S, Du J S, et al. Phase transformation
in AISI 410 stainless steel. Materials Science & Engineering:
A, 2002, 332(1-2): 1-10.
[18] Hu L X, Zhou J, Liu J X, et al. Effect of quenching cooling
rate on microstructure and mechanical properties of H13
die steel. Heat Treatment of Metals, 2018, 43(9): 123-128. (In
Chinese)
[19] Türker M, Ertürk A, Karakulak E, et al. Effects of different
heat treatments on microstructure, toughness and wear
behavior of G-X 10CrNiMoNb 18-10 cast austenitic stainless
steel. Transactions of the Indian Institute of Metals, 2018,
71(4): 1033-1040.
[20] Najafi H, Rassizadehghani J, Asgari S. As-cast mechanical
properties of vanadium/niobium microalloyed steels. Materials
Science & Engineering: A, 2008, 486(1-2): 1-7.
[21] Moon J, Lee J, Lee C. Prediction for the austenite grain
size in the presence of growing particles in the weld HAZ of
Ti-microalloyed steel. Materials Science & Engineering: A,
2007, 459(1-2): 40-46.
[22] Gürol U, Karadeniz E, Çoban O, et al. Casting properties
of ASTM A128 Gr. E1 steel modified with Mn-alloying and titanium
ladle treatment. China Foundry, 2021, 18(3): 199-206.
[23] Wang Z, Mao X, Yang Z, et al. Strain-induced precipitation
in a Ti micro-alloyed HSLA steel. Materials Science &
Engineering: A, 2011, 529: 459-467.
[24] Wang Z, Sun X, Yang Z, et al. Effect of Mn concentration
on the kinetics of strain induced precipitation in Ti microal
مقالات و اخبار
یک نظر در “اثر عملیات حرارتی بر ریز ساختار و خصوصیات مکانیکی فولاد مارتنزیتی کم آلیاژ مقاوم به سایش حاوی تیتانیم”
خیلی جالب بود! همیشه فکر میکردم عملیات حرارتی فقط سختی رو تغییر میده، ولی حالا فهمیدم که روی استحکام و مقاومت به سایش هم تأثیر داره.