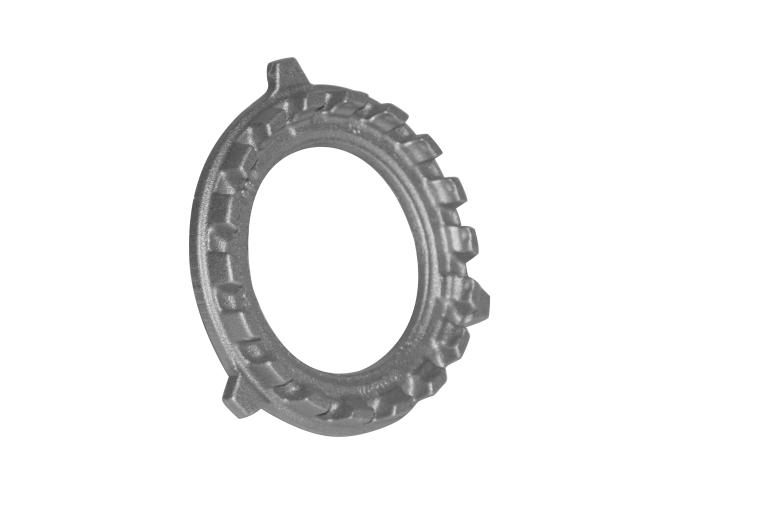
استفاده از نرم افزار شبیه سازی درحذف عیوب انقباضی درقطعات چدنی خودرو
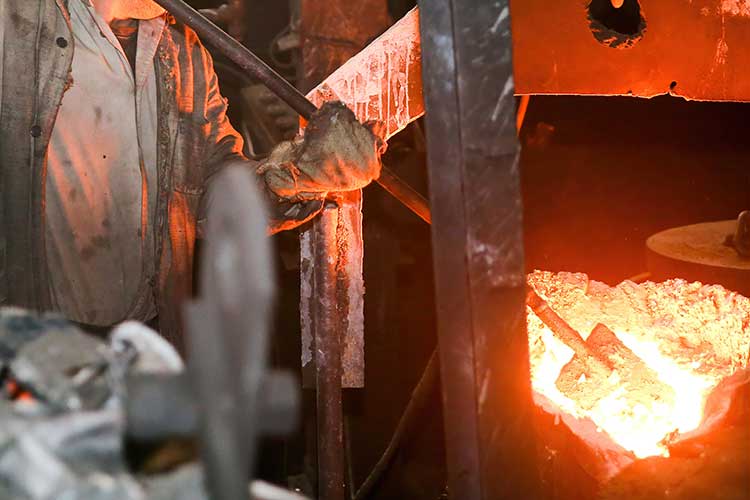
چکیده
امروزه فرآیند ریخته گری بیشــترین ســهم را در شکل دهی مواد فلزی به خود اختصاص میدهد. فرآیند ریخته گری شامل عملیات ذوب ریزی در محفظه قالب، انجماد و ســرد شــدن پس از انجماد و تخلیه از قالب می باشد. لذا این فرآیند شامل سرد شدن در حالت مذاب، یک تغییر حالت از مذاب به جامد و نهایتا سرد شدن از دمای انجماد تا دمای محیط میباشد.
طی هر کدام از این فعل انفعالات تغییرات حجمی و ساختاری تحت شرایط مختلف سرد شدن و بسته به آنالیز چدن در آن رخ میدهد. تغییرات حجمی در چدن ها بر خلاف ســایر آلیاژها دارای یک مرحله انبســاطی می باشــد ولی در کل انجماد چدن همانند کلیه آلیاژها با کاهش حجم همراه می باشد ولی از این انبساط حجمی میتوان در عملیات تغذیه گذاری استفاده به عمل آورد.
فرآیند انجماد چدن های گرافیتی به عوامل متعددی بستگی دارد همواره یکی از دغدغه های ریخته گران از مرحله ساخت مدل تا مراحل تولید قطعه بوده است. کربن وارد شده در فرآیند انجماد دارای وزن مخصوص 2/2gr/cm³ در مقایســه با gr/cm³ 7 وزن مخصوص چدن می باشــد و این باعث غوطه وری و شناوری گرافیــت در حین انجماد و انبســاط همه جانبــه در کل مذاب در حین شــکل گیری گرافیت میگردد و انقبــاض متعاقب آن عملیات تغذیه گذاری را به خصوص در چدن های نشکن با مشکلات عدیدهای همراه کرده و سالانه میلیون ها تن قطعات به دلیل عیوب انقباضی ناشی از عدم تغذیه گذاری صحیح ضایع میشوند.
ترکیب شیمیایی و درصد عناصری از قبیل کربن و و سیلیسیم و گرافیت زایی بالاتر در چدن نشــکن میزان حساســیت به بروز عیوب انقباضی را از خاکستری متمایز می ســازد که در این مقاله هم مورد بحث و بررسی قرار گرفته اســت.
در بین نواقص و عیوبی که طی این فرآیند انجماد رخ میدهد بیشــترین سهم را عیوب انقباضی دارند که به عنوان یکــی از عیوب و نواقص مهم و محتمل در قطعات ریختگی بوده و همــواره ریخته گران را به خصوص در ریخته گری قطعات با جنس چدن نشکن به چالش کشانده است.
مقدمه:
امروزه روش ریخته گری بيشترين سهم را در توليد قطعات فلزی به خود اختصاص داده است و در اين بين ریخته گری در ماسه تر و نيز ريختن قطعات چدنی بيشــترين ســهم را در بين ســاير روشها و آلياژها دارند. با پيشرفت روزافزون علم، همگام با آن درخواست مشتريان قطعات ریخته گری نيز برای بالا بودن كيفيت ظاهری و ســاختاری بالاتر رفته و اين چالش بزرگی را در بين ريخته گران برای توليد قطعات با قيمت تمام شــده پايين اما كيفيت بالا ايجاد كرده اســت.
قطعات ريختگی همواره با يکسری عيوبی مواجه هستند كه بســته به نوع عيب زيان و خساراتی را به ریخته گران وارد میكنند. برای مثال يکســری از عيوب ریخته گری در همان كارخانه ریخته گری جداسازیمی شــوند و برای ماشــينکاری و عمليات بعدی ارسال نمی شوند اما در اين ميان عيوبی هســتند امکان تشــخيص آنها قبل از ماشينکاری به طور صد در صد ممکن نيســت و اين چنين عيوبی هزینه های گزافی را به ریخته گران تحميل میكنند.
در اين مقاله ســعی بر آن شــده است تا ضمن نشان دادن حساســيت بالای قطعات ريختگی چدنی نشــکن نسبت به همان قطعات از جنس خاكســتری،كاربرد بســيار مفيد و تاثيرگذار به كارگيری سيســتم های شبيه سازی در طراحی سيستم راهگاهی را در جهت كم كردن و حتی به صفر رســاندن سيستم سعی و خطا در اين مقوله را نشان دهيم. امکان بروز عيوب انقباضی در چدن خاكستری %2/5 در مقابل %12 برای چدن نشکن میباشد.
اين تفاوت علل بســياری دارد از جمله فوق گداز بالای مورد نياز و به تبع آن جوانه زنی و گرافيت زايی كروی بيشــتر در ریخته گری چدن نشکن نسبت به چدن خاكستری می باشد. عمليات جوانهزنی و تلقيح باعث افت حرارتی از 50 تا 100°C میشود كه بايستی در دمای ذوب ريزی لحاظ گردد.
در اين ميان از جمله مســتعدترين عيوب، میتوان به عيوب انقباضی در اشــکال مختلف كــه ضمن متداول بودن آنها به دليل ذات فرآيند ریخته گری (همانطور كه در بالا بيان شــد)، اشاره كرد. عيوب انقباضی از يک كشيدگی سطحی كه با چشم غيرمسلح نيز قابل رويت میباشد تا ريز مک های انقباضی در دل قطعه میتوانند در چدن های گرافيتی رخ دهند كه در اين ميان حساسيت چدن های نشکن نســبت به چدن با گرافيت فشرده و چدن خاكستری به مراتب بيشتر اســت و اين به ســاختار گرافيت ها و زمينه و نحوه انجمــاد اين چدن ها بر میگردد كه موضوع بحث اين مقاله نيست.
در سال های نه چندان دور برای به حداقل رســاندن طراحی های سيستم راه گاهی و بسياری از عوامل مرتبط با انجماد و انتقال حرارت در حين انجماد و هدايت حرارتی كه مستقيما روی بروز عيوب انقباضی تاثيرگذارند از سيستم های شبيه سازی استفاده میشود كه در حال حاضر در كشور ما نيز در بسياری از كارخانجات ریخته گری استفاده از اين سيستم برای كاهش هزينه ها امری ضروری میباشد.
ورودی های نرم افزار شبيه سازی به شرح زير می باشد:
- فايل 3D قطعات شــامل سيستم راهگاهی طراحی شده، ماهيچه، مبرد، فيلتر و كليه ادوات داخل قالب
- جنس قالب و قطعه
- دمای ورودی مذاب و دمای قالب
- شرايط كنترل كننده شامل فشار موثر، سرعت اوليه مذاب ورودی و دبی مذاب ورودی و …
- محل ورود ذوب به قطعه
- محل ورودی ذوب به سيستم و مشخص كردن آن روی حوضچه از خروجی های نرم افزار شبيه سازی هم میتوان به موارد زير اشاره كرد: -1 زمان و دمای لحظه به لحظه در طول فرآيند پر شدن قالب
- الگوی انجمادی شامل مسير حركت جبهه مذاب -3 دمای نقاط مختلف در حين سرد شدن جامد
- تشکيل مک های انقباضی
- سرعت سيلان مذاب در هر لحظه در هر مجرايی
لذا در اين مقاله هدف در ابتدا نشــان دادن حساســيت بيشتر چدن نشکن به عيوب انقباضی در مقايسه با ديگر چدن های گرافيتی در يک قطعه ثابت و نهايتا كاربرد بسيار مفيد از سيستم نرم افزاری شبيه سازی برای حل مشکلات انجمادی و ارايه نتايج حاصل از آن را مورد بحث و بررسی قرار گرفته است.
روش انجام آزمایشات:
آزمايشات انجام پذيرفته در اين تحقيق به دو دسته به شرح ذيل تقسيم بندی میگردد:
- نشان دادن تفاوت در تمايل به بروز عيوب انقباضی در چدن های نشکن نسبت به خاكستری
- استفاده از نرم افزار شبيه ســازی جهت حذف عيوب انقباضی در قطعات ريختگی از چدن نشکن
بــرای اين منظور قطعه كپه ياتاقان را به عنوان يکی از قطعات خودرو كه از هر دو جنس چدن نشــکن و خاكستری توليد میشود انتخاب شده و در شکل 1 تصوير سه بعدی اين قطعه نيز نشان داده شده است.وزن قطعــه فوق حــدود 8 كيلوگرم و ضخامت ضخيم ترين قســمت آن 3 سانتیمتر بوده كه آن را كلا مستعد كشيدگی مینمايد.
در مرحله اول سيستم راهگاهی مطابق شکل 2 برای اين قطعه طراحی و با شــرايط مندرج در جدول 1 ریخته گری به صورت دستی با ماسه قالب گيری تر با خط اتوماتيک انجام شد.نتايــج حاصل از ریخته گری 10 قالب 6 تايــی قطعات كپه ياتاقان از جنس چدن خاكســتری حاكی از عدم وجود حفرات انقباضی و كشــيدگی سطحی در قطعات بود.
در مرحلــه بعدی همين قطعه با ذوب نشــکن و بــدون تغذيه گذاری مطابق جدول 2 ریخته گری شــد كه علاوه بر كشيدگی های شديد سطحی در برش های متعدد از مقاطع مختلف حفرات انقباضی در قطعات مشــاهده گرديــد.
آناليز قطعات ريخته شــده در جدول 2 و شــرايط قالبگيری آن و خــواص مخلوط قالبگيری در جدول 3 آورده شــده و طراحی سيســتم راهگاهی آن كه به شکل سعی و خطا صورت پذيرفته بود در شکل 3 نشان داده شده است.در طراحی اين سيستم راهگاهی با توجه به محل كشيدگی ها كه به صورت وســيع سطح زيادی از قطعه را شامل میشــد بنا به تجربه روی آناليز و شرايط قالب گيری و ذوب ريزی تغييراتی داده شــد.
بدين شــکل كه استحکام و سختی قالب ها افزايش، درصد كربن و سيليســيم در مقدار حد اكثر در نظر گرفته شــد. از جمله ديگر تغييرات اساســی در اين سيستم تغذيه گذاری آن میباشد كه برای چهار قطعه به صورت تغذيه مشــترک بزرگ و برای دو قطعه تغذيه تکی طراحی گرديد كه در شکل 3 نشان داده شده است.
همانطور كه در شــکل فوق هم ديده میشود ورودی های متصل به قطعه برای هدايت ذوب به محفظه قالب به شــکل V طراحی شــده اســت تا بتوان تغذيه گذاری را انجام داد.قطعات ريخته شــده با شرايط جدول و شکل 3 نســبت به شرايط قبلی به مراتب بهتر بودند ولی در گلويی تغذيه در محل اتصال به قطعه حفرات درشــت انقباضی هنوز قابل مشــاهده بود و در سطح رويی قطعه كشيدگی جزيی رخ داده بود.
در مرحله بعدی با استفاده از نرم افزار شبيه سازی اقدامات به شرح زير صورت پذيرفت: مطابق شکل 4 ورودی قطعه كه همان گلويی تغذيه می باشد به يک راهباره تغيير داده شــد و تمامی ورودی های شبيه سازی را كه در بخش اول توضيح داده شــده بود را به سيستم وارد كرديم در ضمن دمای ذوب ريزی را به 1370-1400 درجه ســانتیگراد تغيير داديم كه نتايج شبيه سازی همراه با جانمايی به كار گرفته شده به شرح زير میباشد.
در شــکل های زير ســرعت ورود مذاب به محفظه قالب، زمان كل پر شدن قالب، ســرعت سرد شدن پس از پر شدن قالب و نقاط گرم و … نشان داده شده است. همانطور كه در شــکل 8 نشان داده شــده است نقاط گرم و مستعد عيوب كشيدگی مشخص شدهاند كه با پايين آوردن دما اين مشکل نيز برطرف گرديد.
بحث و نتیجه گری:
حال با توجه به آنچه در اين مقاله به آن اشــاره شــد لزوم اســتفاده از سيســتم نرم افزاری شبيه سازی اكنون امری الزامی برای ریخته گران حتی در رده كارگاه های كوچک تا متوســط ضروری می باشد كه با استفاده صحيح از آن بســياری از آزمايشات ســعی و خطا كه هر كدام هزینه های سربار بالايی را بــه كارخانجات تحميل میكنند حذف میشــود زيــرا در غير اين صورت مجموع هزینه های دوباره كاری و سربار از هزینه های مستقيم ضايعات بالاتر هم می باشــد.
شايان ذكر است امروزه برای ساير صنايع نيز از قبيل مهندسی عمران و ســازه، الکترونيک و … بســته به نياز آن مجموعــه نرم افزارهای شبيه سازی جايگاه ويژهای را به خود اختصاص دادند.
منابع:
منبع فارسی: آذر ماه 1395- مجله صنعت ریخته گری
ترجمه و تدوین: واحد نجاتی مازگر، حمیدرضا معصومی
مقالات و اخبار