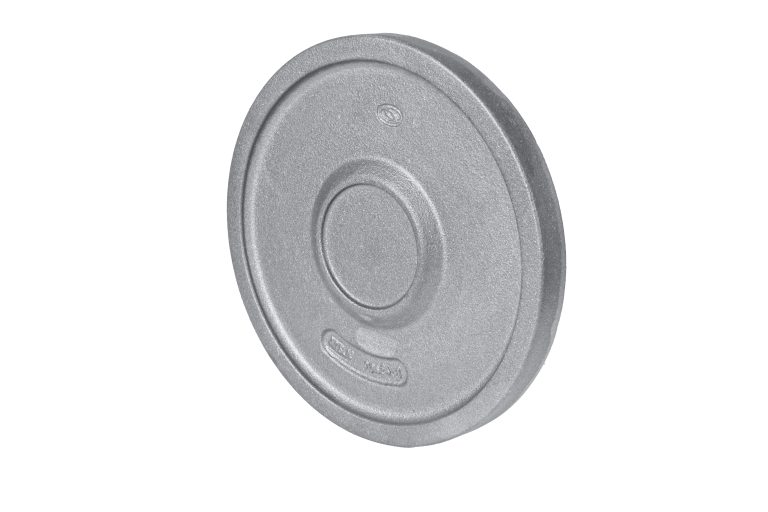
تعیین محدوده ضخامت برای قطعات چدن با ساختار ریختگی آسفریت
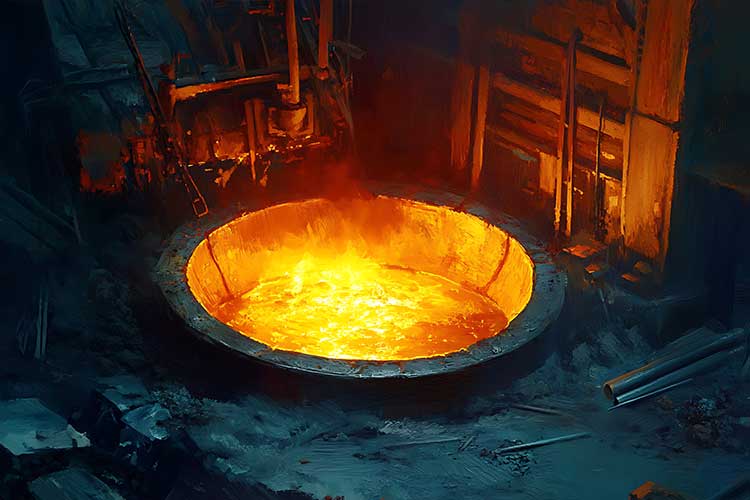
چکیده
فرآیندی به منظور دســتیابی به ریزســاختارهای آسفریت در شرایط ریخته گری از طریق مهندسی کردن خنک شدن پس از انجماد (بدون عملیات حرارتی) در مطالعات قبلی برای یک تک آلیاژ و برای یک قطعه خاص (سگدســت) توســعه یافت. البته بسیاری از قطعات ریختگی صنعت خودرو که کاندیدای تولید با این فناوری هستند دارای اشکالی با ضخامت های مختلف و در نتیجه سرعت های متفاوت سرد شدن می باشند که این تفاوت ها میتواند تولید قطعات کاملا آسفریتی در شرایط ریختگی را به وسیله مهندسی سرد کردن پیچیده و یا حتی غیرممکن نماید.
هدف از تحقیق حاضر توسعه یک مدل تجربی است که مشخص میکند در چه محدودهای از ضخامت، یک ریزساختار ریختگی آسفریت را میتوان بدون به کارگیری عملیات حرارتی آستمپر کردن فقط با تنظیمات ترکیب شیمیایی ایجاد نمود. قطعات ریختگی با مدول های حرارتی بین 0/4 تا 1/5 سانتیمتر با سه ترکیب شیمیایی (در محدوده Ni 3-5 %، 0/2Mo % و Cu 0/1-1 %) با اعمال سرد کردن مهندسی شده پس از انجماد تولید گردید.
ارتباط خواص مکانیکی این قطعات با ضخامت های مختلف، مدول حرارتی و یا ســرعت های ســرد کردن مطابق با الزامات اســتانداردهای (2011) ASTM-A897/A897M-06 و 1564-12 UNE-EN برقرار شــد. دامنه درجه حرارت تخلیه قطعات با درنظر گرفتن مدول های متفاوت حرارتی هر قطعه تعیین گردید و یک محدوده دمای استحاله که در آن ریزساختارهای کاملا آسفریتی به دست می آید مشخص شد. یک برنامه کامپیوتری اکسل درجه حرارت استحاله را در مقاطع مختلف قطعات ریختگی محاسبه کرده و در صورتی که در محدوده صحیح قرار داشته باشند آنها را ثبت میکند.
مقدمه
چشــم انداز جايگزينی برخی كاربردهای قطعات فولادی موجب توسعه يک فرآيند جديد برای توليد چدن نشکن با يک زمينه آسفريتی (چدن نشکن آستمپر ADI) گرديد. اين چدن از نظر نســبت استحکام به چقرمگی عالی بوده و قابليت جايگزينــی با فولادهــای ريختگی و يا آهنگری شــده و حتی قطعات ريختگی آلومينيــم را دارد و با اين آلياژ جديد قطعاتی به بازار ارايه میشــود كه نســبت استحکام به وزن بالاتر و قيمت ارزان تری خواهند داشت.
فرآيند معمول برای توليد اين ريزســاختار شامل يک عمليات حرارتی است به آن عمليات آســتمپر میگويند، اما فرآيندی بر پايه يک خنک كردن مهندسی شــده بدون نياز به عمليات حرارتی مطرح شده، پيشنهاد گرديده تا قطعات ريختگی آسفريتی را میتوان با اين روش با شرايط ريختگی توليد نمود. خنک كردن مهندسی شده انرژی مورد نياز برای توليد يک قطعه را كاهش داده و ارزش افزوده قطعه را افزايش میدهد. همچنين بدين ترتيب زمان توليد و انرژی كل چرخه عمر نيز كاهش خواهد يافت.
متغيرهای فرآيند كه بايد برای دســتيابی به ريزســاختار آسفريتی در شرايط ريختگی كنترل شوند شــامل تركيب شيميايی آلياژ و سرعت های سرد شدن در مقاطع مختلف قطعه ريختگی اســت. همچنين فرآيند انجماد، عوامل اســتحاله يوتکتيک و اســتحاله در دمای ثابت (ايزوترم) نيز بايد مورد بررسی و مطالعه قرار گيرد.
اما يکی از نقاط كليدی برای دستيابی اين ريزساختارهای آسفريتی در شرايط ريختگی تعيين حداقل ســرعت سرد شدن مورد نياز برای پرهيز از ورود به ناحيه پرليتی در آلياژ اســت. به همين منظور نمودارهای اســتحاله در اثر خنک شدن مداوم (CCT) برای ســه آلياژ مختلف با محدوده تركيب شــيميايی Ni 3-5 %، Mo 0/2 تا 0 %، Cu 0/1-1 % توســعه يافت و تغيير حداقل ســرعت سرد شدن برای پيشــگيری از تشــکيل پرليت با مقدار عناصر اصلی آلياژی (Ni,Mo,Cu) مرتبط گرديد.
درجه حرارت های تخليه قطعه و استحاله در دمای ثابت (ايزوترم) يک تاثير اساسی بر ريزساختار نهايی دارد و ضخامت های مختلف در همان قطعه ريختگی نيز باعث ايجاد درجه حرارت های فرآيندی متفاوتی میگردد. براساس اين روش بايد يک ريزســاختار كاملا آستنيتی در تمامی مقاطع قطعه ريختگی و يا حداقل در مقاطعی كه به وسيله مهندس طراح مشخص شده به وجود آيد. به همين دليل چهارچوب و پنجره ضخامتی كه در آن ريزســاختارهای ريختگی كاملا آسفريتی قابل دستيابی هستند بايد به روشنی مشخص گردد.
مقاله حاضر يک مدل و الگوی آزمايشی است كه امکان تعيين اين پنجره و چهارچوب ضخامتی را كه در آن ريزساختار ريختگی به طور تضمين شده آسفريت میگردد، فراهم مینمايد. به علاوه اين مدل برای يک محدوده تركيب شــيميايی مشــخص در طی يــک فرآيند نيمه صنعتی نيز مورد تاييد قــرار گرفت. هنگامی كه مدول حرارتی يک قطعــه ريختگی در محدوده چهارچوب فرآيندی ضخامت اســت اين مدل شاخص های بهينه فرآيند را با هدف رسيدن به خواص مکانيکی (استحکام نهايی كشش و سختی) مطابق با الزامات آلياژهای ADI تعيين میكند.
روش آزمایش
ذوب در يک كوره القايی فركانس متوسط به ظرفيت 100 كيلوگرم (فركانس 250 هرتــز، توان 100 كيلووات) تهيه گرديد و شــارژ يا مــواد اوليه به كار رفته براساس درصد وزنی تركيب شيميايی بدين شرح بوده است: قراضه آهنی كم كربن C 0/007 %، Si 0/002 %، Mn 0/17 %، P 0/003 %، S 0/006 (%، نيکل بسيار خالص) حداقل خلوص 99 (%، FeMo Mo64/25 %، Si 2/05 %، C 0/019 %، S %0/042، P %0/03،) مــس حداقل خلوص 99 %، (گرافيــت) حداقل C 99 %، S كمتــر از 0/03 %، H كمتر از 0/04 %، N كمتر از (0/01 % و FeSi75 Si 74/6 %، Al 0/83 %، C 0/12 % ) بلافاصله پس از ذوب مواد اوليه، تركيب شــيميايی كنترل شده و مقادير كربن، سيليسيم، نيکل، مس و موليبدن تنظيم میگردد.
در درجــه حــرارت ˚C 1510-1530 مذاب از كوره بــه داخل پاتيل تخليه میگردد و عمليات تلقيح (نشکن ســازی) به روش ســاندويچی با استفاده از 1/2 درصد آلياژ فروسيليکومنيزيم(Si 46/21 %، Mg 6/47 %، Ca 0/98 %، Al 0/67 % و 0/97 % عناصر نادر خاكی RE) انجام شده است.
به منظور دســتيابی به سرعتهای مختلف سرد شــدن قطعات ريختگی با مدول های حرارتی متفاوت و شکل های هندسی گوناگون ريخته گری گرديدند. محدوده مدول های حرارتی مورد مطالعه 0/4 تا 1/5 سانتیمتر بوده و نمونه های توليد شــده شــامل ضخامت به ابعاد mm2 100×60 با ضخامت های 10 تا 80 ميلیمتــر در محدوده های تغيير 10 ميلیمتری، استوانه ها بــا ارتفاعی معادل قطــر (24، 38، 48، 60، 72 و 90 ميلیمتــر) و بلوک های Y شــکل مطابق با استاندارد EN1563، در شکل 1 مدلهای صفحه ای، استوانه ای مشاهده میشود. قالب های تهيه شده نيز با استفاده از ماسه و چسب های شيميايی آماده گرديدند.
پس از عمليات تلقيح، جوانه زايی آلياژها با استفاده 0/2 % شمش Germalloy ،% 69/9 Si) Amerinoc ) یا % 0/99 Ca ،% 3/93 Al ،71/7 Si( تركيــب با)% 0/19 Zr ،% 0/13 La ،% 0/24 Ce ،% 1/38 Ca ،% 0/93 Al ،% 0/49 Bi دانه بندی 0/2 تا 0/5 ميلیمتر درون محفظه قالب انجام گرديد.
محدوده تركيب شــيميايی نمونه های ريختگی شــامل (3/75C 3/58 %، ،% 0/006-0/009 S -% 0/007-0/010 P ،% 0/18-0/25 Mn ،% 2- 2/15 Si Mg -0/049 0/038 % ) بوده و عناصر آلياژی به كار رفته برای توسعه نمودارهای CCT نيز Ni، Cu و Mo در محدوده زير بوده اند:
.% 0/09-0/96 Cu و % 0/01-0/22 Mo ،%2/86-5/05 Ni در ابتدا برای توســعه نمودارهای CCT نمونه ها زودتر تخليه شــدند تا در جريان هوا ســرد شوند. منحنی سرد شــدن هريک از نمونه ها نيز به وسيله يک ترموكوپل نوع K كه در مركز آنها قرار داده شــده اندازه گيری گرديد. براساس اين اطلاعات ســرعت سرد شــدن در مدول های مختلف حرارتی به طور تجربی برای محدوده درجه حرارت استحاله يوتکتوييد محاسبه گرديد، سپس نمونه بريده شده و برای بررسی چشمی با استفاده از يک ميکروسکوپ نوری آماده گرديدند.
به منظور مشخص شدن ريزســاختار نمونه ها با نيتال 5 درصد اچ شدند و هدف از اين بررســی نيز تعيين حضور پرليت بوده تا بدين ترتيب دماغه به وجود آمدن پرليت و حداقل ســرعت سرد شــدن مورد نياز برای پيشگيری از تشکيل پرليت به صورت تابعی از تركيب شيميايی آلياژ تعيين گردد.
مرحلــه دوم تعييــن درجــه حرارت های فرآينــدی برای بهدســت آوردن ريزساختارهای ريختگی آســفريتی و ارتباط آنها با مدول های مختلف حرارتی قطعــات ريختگی اســت. بدين منظور آليــاژی كه دماغه پرليت آن براســاس نمودارهای CCT در زمان های طولانی شــکل میگيرد درنظر گرفته شــد، اين تركيب شيميايی شامل (3/63-3/75C %، Si 2/04-2/15 %، Mn 0/19-0/24 %، ،% 2/86-3/01 Ni ،% 0/042-0/049 Mg ،% 0/006-0/009 S ،% 0/007 -0/01 P) است.
% 0/09-0/19 Cu ،% 0/17-0/22 Mo درجه حــرارت بارريزی نمونه های ريختگی بيــن ˚C 1390-1410 بوده و بلافاصله پس از بارريزی و انجماد نمونه ها تحت يک فرآيند كنترل شــده ســرد شــدن قرار میگيرند. در ابتدا تمامی نمونه ها در يک زمان تخليه شده تا در درجه حرارت محدوده تشــکيل آسفريت در هوا سرد شوند. در اين زمان نمونه به وسيله موادی با هدايت حرارتی كمتر از W/mK 0/006 عايق میشود، مواد عايق به كار رفته دانه های پرليت منبســط شده با اندازه كمتر از 5 ميلیمتر و وزن مخصوص بين kg/m3 40 تا 120 اســت.
هدف از انجام اين مرحله حفظ يک درجه حرارت ثابت به منظور انجام واكنش آسفريت می باشد. استحاله در دمای ثابت (ايزوترم) بــرای تمام نمونه ها به مدت 90 دقيقه درنظر گرفته شــد و اين زمان به منظور پيشگيری از اثرگذاری در تشکيل آسفريت و اطمينان از كامل شدن واكنش ثابت نگه داشته شــد. در انتهای نگهداری در درجه حرارت ثابت (ايزوترم)نمونه ها تا درجه حرارت اتاق در هوا سرد گرديدند. در شکل 2 منحنی های سرد شدن برای مدول های مختلف حرارتی ارايه شده است.
از اين داده های آزمايشی همچنين برای تعيين ارتباط درجه حرارت تخليه و مدول حرارتی اســتفاده شد سپس درجه حرارت استحاله ايزوترم به صورت تابعی از مدول حرارتی محاســبه گرديد. همچنين خنک شدن پس از تخليه در هوا نيز در محاسبات درنظر گرفته شد. در نهايت خواص مکانيکی هم با آزمايش كشش و هم سختی سنجی بر روی نمونه های اســتوانه ای ماشينکاری شده به قطر 10 ميلیمتر تعيين گرديد.
اســتحکام نهايی كشش (UTS)، استحکام تسليم (YS) و ازدياد طول نســبی مطابق با اســتاندارد 2011 1563: EN و ســختی برينل نيز با ســاچمه به قطر 10 ميلیمتر و بار اعمالی kg 3000 براســاس اســتاندارد 2005 6506-1: ISO اندازه گيری گرديدند.
نتایج و سگالش
تركيب شــيمايی ســه آلياژ برای هر نمودار CCT در جدول 1 ارايه شده و برای به دست آوردن دياگرام های تجربی CCT هر آلياژ با سرعت های ˚C/s 0/2 تا 1/3 در محدوده دمايی ˚C 500 تا 800 ســرد گرديد كه نتايج آن در شکل 3 مشاهده میشود.
ســرعت های حداقل سرد شدن تجربی برای پيشگيری از تشکيل پرليت در هر آلياژ در جدول 2 ارايه شــده و كمترين مقادير ســرعت سرد شدن در محدود ˚C 700 تا 600 بوده زيرا اين محدوده پايين ترين ســرعت ســرد شدن استحاله يوتکتوييد می باشد. اين سرعت حداقل سرد شــدن بايد رعايت شود تا قطعه به درجه حرارت اســتحاله يوتکتوييد برسد. به منظور ســاده شدن روند محاسبات رياضی منحنیهای سرد شــدن در اين دوره های دمايی به صورت خطوط صاف درنظر گرفته میشود كه با نتايج تجربی بهدست آمده نيز انطباق خوبی دارد.
به عنوان اولين گام از مدل تجربی يک معادله برای محاســبه حداقل سرعت سرد شدن (CRmin) جهت پيشگيری از برخورد با دماغه تشکيل پرليت به صورت تابعی از مقادير نيکل، مس و منگنز جهت مطالعه در خصوص تركيب شــيميايی توسعه يافت:
معادله CRmin=2/35-0/33×%Ni-0/1×%Cu-4×%Mo :1
صحت اين معادله به طور تجربی در محدوده تركيب شــيميايی مورد بررسی تاييد گرديده است.
مرحله دوم مدل آزمايشــی مرتبط با تعيين چهارچــوب و پنجره ضخامتی اســت كه اين متدولوژی در آن محدوده معتبر می باشد و اين نياز وجود دارد كه چهارچوب فرآيندی ضخامت تعيين شــود زيرا يک قطعه ريختگی ضخامت های متفــاوت و مدول های حرارتی گوناگون دارد و مدول حرارتی بالاتر موجب فرآيند انجماد طولانی تر و سرعت سرد شدن پايين است.
اما تخليه قطعه از قالب نمیتواند در هر دمايی انجام شود به همين خاطر مرز و حد بالايی آن ˚C 1050 يعنی حدود ˚C 50 زير دمای انجماد تعيين گرديد. البته از آنجايی كه تخليه يک قطعه ريختگی كاملا منجمد نشده میتواند منجر به بروز عيوبی مانند تخلخل ميکروســکوپی و يا تنش حرارتی بالا شود رعايت اين درجه حرارت ضروری اســت. حد پايين دمای تخليه نيز ˚C 50 بالای دمای اســتحاله يوتکتوييد تعيين گرديد كه اين دمــا تابعی از مدول حرارتی و مقدار عناصر آلياژ می باشد. شــکل 4 تاثير مدول حرارتی و مقدار عناصر آلياژی را بر درجه حرارت استحاله يوتکتوييد نشان میدهد.
برای مشخص كردن حد پايين دمای تخليه قالب محدودترين منحنی ها كه مربوط به آلياژ Cu) 1 % و Ni 3 %) بود درنظر گرفته شد. معادله (2) كه بر نتايج آزمايشی انطباق دارد امکان محاسبه درجه حرارت استحاله يوتکتوييد را بر حسب ˚C بهصورت تابعی از مدول حرارتی (M) فراهم مینمايد:
معادله T =-41/93 M2+115/03 M+593/24 :2
با درنظر گرفتن قطعات ريختگی آزمايشــی بــا مدول های حرارتی مختلف، زمان انجماد و به دنبال آن ســرد شــدن در قالب تا تخليه، درجه حرارت تخليه به صورت تابعی از مدول حرارتی محاسبه گرديد. مدول حرارتی در محدوده 0/4 تا 1/5 سانتیمتر مورد مطالعه قرار گرفت و مشاهده شد كه يک خط صاف (مطابق معادله 3) درجه حرارت تخليه را با مدول حرارتی مرتبط مینمايد.
معادله Tshkout-M =568/40 M-341/04+ Tshkout-0.6cm :3
مقدار درجه حرارت تخليه برای cm M=0/6 يک ثابتی اســت كه به وسيله روش محاســبه به وسيله نرم افزار تعيين می شود و به عنوان يک مقدار مرجع برای تمامی آلياژها درنظر گرفته میشــود. اين مقدار مرجع جهت محاسبه زمان تخليه برای ضخامت های مختلف مانند درجه حرارت تخليه بر محدوده بالايی و پايينی تعيين شده، انطباق دارد.
برای يک قطعه ريختگی مشــخص اين مدل میتوانــد زمان های مختلف تخليــه را كه در آن فرآيند مورد نظر قابل اجرا باشــد، محاســبه نمايد. با روش محاسبه نرم افزاری میتوان درجه حرارت پايين تر تخليه را با هدف كاهش تنش حرارتی به دليل دمای بالا در هنگام تخليه، تعيين نمود. در شــکل 5 نتايج محاســبه درجه حرارت تخليه ارايه شده كه در آن امکان تغيير حداقل و حداكثر مدول حرارتی قطعه مورد نظر مشاهده میشود.
هدف از فرآيند سرد كردن دسترسی به ريزساختار كاملا آسفريتی در شرايط ريختگی اســت. بنابراين هنگامی كه تركيب شيمايی مناسب به منظور جلوگيری از تشــکيل پرليت و درجه حرارت تخليه بهصورت تابعــی از مدول های حرارتی مختلف قطعه ريختگی، تعيين شــد مرحله بعدی تعيين درجه حرارت استحاله در درجه حرارت ثابت (ايزوترم) اســت كه در تحقيق حاضر درجه حرارتی كه در آن مدول های مختلف حرارتی يک قطعه ريختگی بايد در محيط عايق قرار گيرد بر پايه نتايج آزمايشی محاسبه گرديد.
مانند مراحل قبل مدول درجه حرارت استحاله در درجه حرارت ثابت (ايزوترم) را به صورت تابعی از مدول حرارتی محاسبه مینمايد (معادله4):
معادله Tiso-transf-M=293/39 M-180+ Tiso-transf-0.6cm :4
با پيگيری همان متدولوژی بــرای درجه حرارت تخليه، مقدار درجه حرارت استحاله در درجه حرارت ثابت (ايزوترم) برای مدول cm M=0/6 به عنوان مقدار مرجع تعيين گرديد. اين مقدار مرجع بر درجه حرارت استحاله ايزوترم مدول های مختلف در محدوده مشخص شده، منطبق است.
استحاله ايزوترم در محدوده دمايی بايد اتفاق بيفتد كه ريزساختار دلخواه و در نتيجه خواص مکانيکی مطابق با الزامات آلياژ ADI، به دست آيد. حد بالايی اين درجه حــرارت ˚C 450 بوده و بالای اين دما نتايج آزمايش نشان میدهد كه آسفريت به دست آمده خواص مکانيکی دلخواه كه با خصوصيات مورد نظر انطباق داشته باشد، ايجاد نمیكند.
حد پايينی درجه حرارت، دمای آغاز تشــکيل مارتنزيت( TMst ) بوده كه برای آلياژ (Mo 0/2 %، Ni 3 %) اين درجه حرارت با استفاده از آزمون های ديلاتومتری تعيين گرديد ولی برای ساير آلياژها مطالعات بيشتری بايد با توجه به ارتباط اين درجه حرارت با مقدار عناصر آلياژی انجام شود.
با درنظر گرفتن معادله 4 و محدوده های اســتحاله آسفريت، اگر يک قطعه خاص ريختگی را بتوان با اين روش توليد نمود هنگامی اين مدل قابل اجراســت كــه قطعه ريختگی در درجه حرارت تعيين شــده در محيــط عايق قرار گيرد. از امکانات متفاوت ارايه شــده به وسیله محاســبه نرم افزاری راه حل بهينه آن است كه دســتيابی به خصوصيات مکانيکی دلخواه در قالب استحکام نهايی كشش و سختی را امکانپذير نمايد.
با اســتفاده از آزمايشــات كشــش و سختیســنجی خصوصيات مکانيکی نمونه های مختلف تعيين گرديد و در جدول 3 نتايج به دســت آمده در برخی از قطعات ريختگی به صورت تابعی از مدول حرارتی آنها ارايه گرديد.
متناســب با مدول حرارتی و درجــه حرارت های فرآينــدی نمونه ها، انواع چدن های ADI بهدســت آمده و در شــکل 7 ريزساختارهای بهدست آمده برای مدول های 0/65 و 1/28 ســانتیمتر ارايه شــده اســت. در اين تصاوير مشاهده میشود كه مدول حرارتی پايين تر مرتبط با مقدار بيشتر و آسفريت پايين تر است. اين نتايج در اســتحکام بالاتر برای مدول حرارتی پايين تر همراه با چکشخواری كمتر است.
آناليز آماری بر روی داده های آزمايشــی به منظور تعيين ارتباط شاخص ها و عوامل فرآيندی با خواص مکانيکی بر مبنای همبســتگی Pearson انجام شد و نتايج )جدول (4 آن نشان داد كه استحکام با دو متغير رابطه خطی دارد. مشاهده میشــود كه درجه حرارت استحاله ايزوترم )دارای مقادير همبستگی بالاتر( تاثير بزرگتری بر خواص مکانيکی دارد. شــکل 8 ارتباط بين درجه حرارت استحاله ايزوترم و خواص مکانيکی را نشان میدهد.
افزايش ازدياد طول واضح و روشــن نيســت زيرا نتايــج پراكندگی بالای دارند كه ايــن موضوع را میتوان به دليل حساســيت اين خصوصيت به عيوب ريخته گری مانند تخلخل های ميکروســکوپی دانست. نتايج استحکام تسليم هم ارتباط روشنی را نشان نمی دهند و به نظر میرسد كه كم و بيش استحکام تسليم مرتبط با درجه حرارت اســتحاله ايزوترم نيســت.
البته استحکام نهايی كشش و ســختی يک ارتباط واضحی را با درجه حرارت اســتحاله ايزوترم نشان میدهند به طوری كه با بالا رفتن اين درجه حرارت كاهش می يابند. براســاس اين فرضيه براساس گريدهای مورد نظر چدن ADI بايد درجه حرارت بهينه استحاله ايزوترم بالاتر و يا پايين تر تعيين شود.
معادله UTS=-1/2231 Tiso-transf +1308/2 :5
معادله HB=-0/483 Tiso-transf +466/34 :6
بر مبنای خواص مکانيکی دلخواه با تركيب معادلات 4، 5 و 6 درجه حرارت بهينه اســتحاله ايزوترم برای مقادير حداقلی و حداكثــری مدول حرارتی قطعه ريختگی محاسبه میشود. اين مراحل، عوامل مختلف فرآيندی كه برای دســتيابی به ريزســاختارهای كاملا آســفريتی در تمامی مقاطع قطعه ريختگی و خــواص مکانيکی مطابق با الزامات استاندارد مورد نياز است، تعيين مینمايد.
مدل
همانطور كه در قبل توضيح داده شد با مدل اكسل توسعه يافته در تحقيق حاضر میتوان پيشبينی نمود كه آيا امکان پذير است در تمامی مقاطع يک قطعه ريختگی كه ضخامت های مختلفی دارد به وسیله خنک كردن مهندسی شده به يک ساختار كاملا آسفريتی دست يافت.
ورودی های اين مــدل، مدول های حرارتی حداقل و حداكثر قطعه ريختگی است كه يک ريزساختار كاملا آسفريتی و الزامات خواص مکانيکی تضمين گردد. با درنظر گرفتن اين ورودی ها در اولين گام، مدل عناصر آلياژی مورد نياز را تعيين میكند. با استفاده از روش نرم افزاری، مدل مقادير حداقلی نيکل، موليبدن و مس را برای جلوگيری از تشــکيل پرليت (معادله 1) مشخص مینمايد. از آنجا كه تركيبــات مختلفی را میتوان درنظر گرفت، ملاک های متفاوت مانند عوامل اقتصادی و يا كيفی میتوانند در انتخاب صحيح آلياژ مطرح باشند.
در مرحلــه دوم، مدل ارتباط با مســاله تخليه قطعــه از قالب می يابد و بنابر معادلــه 3 با توجه بــه ارتباط درجه حرارت تخليه و مــدول حرارتی، مدل تعيين مینمايد كه آيا فرآيند برای حداقل و حداكثر مدول حرارتی قطعه عملی اســت و اگر هست درجه حرارت بهينه تخليه تعيين میشود.
مرحله سوم مرتبط با چهارچوب و پنجره درجه حرارت استحاله ايزوترم است. ساختار مدل در اين مرحله بسيار مشابه مرحله قبلی می باشد و برای همان حداقل و حداكثر مدول حرارتی، مدل تعيين میكند آيا امکان دســتيابی به ريزســاختار هدف وجود دارد و اگر چنين اســت درجه حرارت های بهينه اســتحاله ايزوترم بر پايه خواص مکانيکی مورد نظر در قالب استحکام نهايی كشش و سختی برينل، تعيين میگردد.
جمع بندی
تحقيق حاضــر محدوده های فنــاوری فرآيند برای توليد ريزســاختارهای آسفريتی در حالت ريختگی را مشخص مینمايد. در تحقيقات قبلی نشــان داده شده كه روش بهدست آوردن ريزساختارهای آســفريتی با استفاده از سرد كردن مهندسی شــده، امکان پذير و شدنی است. در تحقيــق حاضر نيز برای به كارگيری اين روش در يک فرآيند صنعتی يک گام به سمت جلو برداشته شد.
يک مدل آزمايشــی/ آماری برای تعيين يک راه ساده جهت مشخص كردن عوامل فرآيندی توليد قطعات آســفريتی به صــورت ريختگی با خواص مکانيکی مورد نظر، توسعه يافت. ضخامت های مختلف در يک قطعه به خصوص ريختگی و تفاوت های خنک شدن در آن درنظر گرفته شد.
مدل توسعه يافته تركيب شــيميايی بهينه و در درجه حرارت فرآيندی برای ضخامت های مختلف يعنی درجه حرارت تخليه و اســتحاله ايزوترم را مشخص مینمايد. اين دو درجه حرارت حســاس و تعيين كننده برای اينكه يک ريزســاختار آسفريتی با الزامات خواص آلياژ ADI به وجود آيد، بايد در محدوده های مشخص شده باشند.
البته متناسب با تغيير مدول حرارتی قطعه ريختگی اين درجه حرارت نيز تغيير می نمايند و براساس اين تغييرات مدل طراحی شده چهارچوب و پنجره تغييرات ضخامت كه در آن اين روش قابل اجراست محاسبه مینمايد و با توسعه آن و با يک فرآيند مهندســی شده ســرد شدن يک قطعه مشخص را میتوان با اين خصوصيات توليد نمود. اعتبار اين مدل آزمايشــی با اشــکال مختلف و در محــدوده مدول حرارتی 0/4-1/5 ســانتیمتر و برای يک محدوده خاص تركيب شيميايی (Ni 3-5 %، Mo %0-0/2، Cu 0/1-1 %) تاييد گرديد.
منابع:
منبع خارجی: A.F.S Trans.2015
منبع فارسی: آبان ماه 1395- مجله صنعت ریخته گری
ترجمه: عبدالحمید قدیمی
مقالات و اخبار
یک نظر در “تعیین محدوده ضخامت برای قطعات چدن با ساختار ریختگی آسفریت”
آیا این روش برای همه قطعات چدنی قابل اجراست یا فقط برای ضخامتهای خاصی جواب میده؟