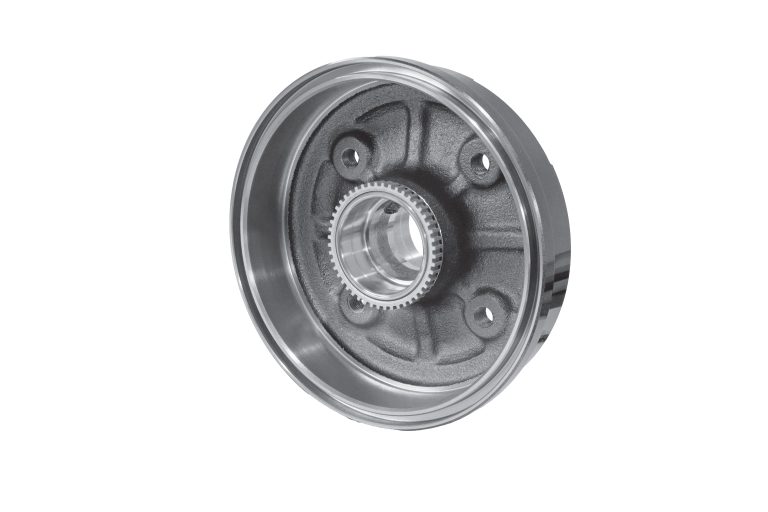
مقدمه:
فرآیندی که طی آن ذرات ساینده تحت فشار هوار روی سطح قطعات فولادی پاشیده میشود تا برای رنگکاری آماده شوند، ساب پاشی یا تمیزکاری پاششی (Abrasive blasting) نامیده میشود. متداولترین انواع ساب پاشی، شنزنی (سندبلاست)، خیسپاشی (وت بلاست)، ساچمهپاشی (شات بلاست)، سنگریزهپاشی (گریت بلاست)، مکشزنی (وکیوم بلاست)، پاشش جوش شیرین (سودا بلاست)، فرچهزنی (بریستل بلاست)، یخپاشی (آیس بلاست)، قلمیزنی (میکروبلاست) و تیلهپاشی (بید بلاست). این مقاله به منظور آشنایی با این اسباب به ویژه سندبلاست و شات بلاست تهیه شده است.
–سندبلاست (sandblast) :
ساب پاشی اغلب با عنوان سندبلاست شناخته میشود، اگرچه سندبلاست، فقط یکی از روشهای ساب پاشی و رایج ترین روش آن، مخصوصا برای مواد نرم و حساس که آماده سازی نهایی می شوند، است. در سندبلاست هوای فشرده شده به عنوان منبع انرژی و جریان پر فشار، نقش مهمی را در سایندگی در سطح قطعه ایفا می کند. سال هاست که در کشتی سازی و خودروسازی، اجزای مختلف با این فرایند از زنگ زدگی، گرد و غبار، گریس و روغن تمیز می شوند. به طور خلاصه سندبلاست را می توان شن زنی یا شن پاشی تعریف کرد. ماسه های ساینده سندبلاست معمولا از جنس سیلیس و اکسید فلزات در اندازههای مختلف هستند. فرایند سندبلاست از نظر تجهیزات و هزینه های نهایی بسیار ارزان تر از سایر روش های آماده سازی سطح خواهد بود که کیفیتی عالی را به مصرف کننده ارائه می دهد.
-پیدایش سندبلاست :
بیش از ۱۰۰ سال است که فرآیند سند بلاست مورد توجه قرار گرفته است. ضرورت اجرای این روش، زمانی مشخص شد که مواد پاک کننده معمولی قادر نبودند سطوح مورد نظر را به طور کامل برای رنگ آمیزی و اعمال پوشش آماده کنند. در حدود سال 1870 میلادی (1249 شمسی)، جرقه اختراع اولین دستگاه سندبلاستر در ذهن “” (Benjamin Chew Tilghman) نظامی درحال خدمت در یک منطقه بیابانی با مشاهده کدورت ایجاد شده روی سطح شیشه که بر اثر برخورد ماسههای بادی به آن صورت گرفته بود، زده شد. معرفی این فرایند، به سرعت تحول بزرگی در آماده سازی سطوح مختلف به ویژه سطوح فلزی ایجاد کرد و پس از آن، ذرات ساینده متداول به دنیای سایش سطوح معرفی شدند. اکنون این روش به عنوان بهترین و کارآمدترین روش های آماده سازی سطح مورد استفاده قرار می گیرد.
-اهداف استفاده از سندبلاست در صنعت فلزات:
همانطور که میدانید فلزات در مجاورت هوا با اکسیژن ترکیب می شوند بنابراین لایه ای از اکسید بر روی سطوح مینشیند که در صورت باقی ماندن اکسید سطح فلز کاملا پوسیده می شود، به وسیله سندبلاست می توان اکسید باقی مانده بر روی سطح فلز را از بین برد. البته دیگر دلایل استفاده از این فرایند به شرح ذیل است:
- رفع آلودگی
- مات کردن سطوح
- حکاکی و ایجاد نقش در سطوح
- ایجاد سطحی زبر و صاف برای چسبندگی بهتر پوشش نهایی
- زنگ زدایی، ماسه زدایی و رنگ زدایی سطوح
-ساینده و انواع آن در سند بلاست:
ساینده، مادهای جامد و سخت است که معمولا به منظور پرداخت سطوح مورد استفاده قرار میگیرد. سختی بالای مواد ساینده، باعث وجود قابلیت لایهبرداری خوب در آنها شده است. سایندهها، یکی از اجزای اصلی در فرآیند سندبلاست هستند.
بر اساس جنس سطوح، ذرات ساینده انتخاب می شوند که در سختی، مقاومت، چگالی و… با هم متفاوت هستند و معمولا سایندهها را به دو نوع اصلی فلزی و غیر فلزی تقسیم میکنند. سایندههای فلزی و غیر فلزی رایج معرفی شده در استاندارهای 1-13686 و 1-14946 ایران، مطابق جدول زیر هستند.
در ادامه به معرفی انواع سایندهها و ویژگیهای آنها میپردازیم.
الف- ماسه سیلیکا
ماسه سیلیکا یا ماسه سیلیسی، قدیمیترین و متداولترین ساینده مورد استفاده در سندبلاست است. در واقع نام سندبلاست نیز به دلیل استفاده از این ماسههای برای این فرآیند در نظر گرفته شده است. ماسه سیلیکا یا سیلیس معمولا برای ساب پاشی در محلهایی که امکان بازیابی مواد وجود ندارد استفاده میشود.
ماسه، سختی نسبتا بالایی دارد. این ویژگی، دلیل اصلی تولید گرد و خاک زیاد در حین فرآیند سندبلاست است. تنفس ذرات آزاد سیلیس توسط کارکنان، احتمال بیماریهای تنفسی در آنها را افزایش میدهد.
ب- گارنت
یکی دیگر از سایندههای متداول در تمیزکاری پاششی، گارنت است. این ماده هزینه بیشتری نسبت به ماسه سیلیسی دارد اما در صورت استفاده صحیح، کیفیتی برابر با آن خواهد داشت. به علاوه، گرد و خاک حاصل از به کارگیری گارنت در سندبلاست کمتر است و تنفس آن خطری را برای سلامت کارکنان ایجاد نمیکند.
پ- سرباره زغال سنگ
سرباره زغال سنگ از سایندههای رایج برای تمیزکاری پاششی در کارخانههای کشتیسازی است. میزان سیلیس در ترکیب سرباره پایین است. با این وجود، این ساینده باعث آزادسازی آلایندههای مختلف در هوا میشود.
ت- ساچمه و گریت
ساچمه (قطعات کروی) و ساچمه شکسته یا «گریت» (Grit)، از سایندههای فلزی مورد استفاده در تمیزکاری پاششی هستند که اغلب با استفاده از فولاد یا چدن ساخته میشوند. این سایندهها، صلبیت و قابلیت بازیابی بالایی دارند. ساچمه و گریت را میتوان بر روی انواع مختلف سطوح به منظور از بین بردن آلودگیها، برداشتن لایه رویی (قبل از پوششدهی) و ساچمهزنی استفاده کرد. ابعاد، سختی و شکل ذرات در این حالت، اهمیت بالایی در خروجی ساب پاشی دارند.
ث- استارولیت
استارولیت، مخلوطی از ماسههای ریز و درشت است که سیلیس بسیار پایینی دارد. این ساینده برای برداشتن پوسته و خوردگیهای سطوح فولادی بدون ایجاد گرد و خاک زیاد مورد استفاده قرار میگیرد.
ج- آلومینا و کاربید
مواد سنتزی نظیر کاربید سیلیسیوم و آلومینا (اکسید آلومینیوم)، به عنوان جایگزینهای رایج ماسه شناخته میشوند. این سایندهها از دوام بیشتری برخوردارند و گرد و خاک کمتری تولید میکنند. مواد سنتزی معمولا قابل بازیابی و استفاده مجدد هستند. آلومینا تقریبا برای آمادهسازی هر سطحی (شیشه، گرانیت، مرمر و فولاد) مناسب است.
د- سایندههای دیگر:
از موادی مانند پلاستیک، دانههای شیشهای، شیشه شکسته، پوست گردو و چوب بلال نیز به عنوان ساینده در تمیزکاری پاششی استفاده میشود. این مواد قابل بازیابی هستند و گرد و خاک بسیار کمتری نسبت به ماسه و سرباره تولید میکنند.
به طور کلی، سایندههایی نظیر ماسه، ساچمه، آلومینا و کاربید برای سندبلاست خشک و سایندههایی مانند ماسه، دانههای شیشهای و دیگر مواد معلق در آب برای سندبلاست مرطوب مناسب هستند.
-تاثیر مشخصات ساینده بر روی کیفیت سندبلاست:
مشخصات ساینده بر روی عمکلرد سندبلاست تاثیر مستقیم دارند. از ویژگیهای مهم سایندهها میتوان به موارد زیر اشاره کرد:
- ابعاد: هر چه ابعاد ساینده بیشتر باشد، سطح زبرتر خواهد بود.
- چگالی: چگالی پایینتر باعث نرمی بیشتر سطح میشود.
- قابلیت بازیابی: امکان جمعآوری و استفاده مجدد از ساینده، هزینه فرآیند سندبلاست را کاهش میدهد.
- سختی: سختی بالاتر، طول عمر و قابلیت استفاده مجدد از ساینده را بهبود میبخشد. در صورتی که چگالی و سختی بالا باشند، عمق نفوذ نیز افزایش مییابد.
- شکل: ذرات کروی شکل باعث ایجاد سطح صاف/شفاف و ذرات تیز باعث ایجاد سطح زبر/کدر میشوند.
-اصول اجرای فرایند سندبلاست:
برای شروع اجرای سندبلاست نیاز به یک دستگاه کمپرسور هوا برای تولید هوای فشرده برای پاشیدن مواد ساینده بر روی قطعه است. در فرایند سندبلاست، هوای فشرده از اهمیت زیادی برخوردار است به طوری که سندبلاست از لحاظ کیفی و کمی ارتباط مستقیمی با فشار هوایی دارد که کمپرسور هوا تولید می کند.
فشار هوای مطلوب برای اجرای عملیات سندبلاست ۷ بار یا 105psi است. این فشار از طریق شلنگ فشارقوی هوا به محفظه سندبلاست انتقال می یابد. دیگ سندبلاست در سایزهای مختلفی وجود دارد که سایز متوسط آن که بیشتر هم مورد استفاده قرار میگیرد ۳۰۰ لیتر گنجایش دارد.
فشار هوای تولید شده به وسیلۀ کمپرسور هوا، از طریق اتصالات بخش زیرین دیگ سندبلاست با سرعتی زیاد و به صورت مستقیم به سمت شلنگ سندبلاست هدایت می شود. این انتقال سبب ایجاد خلاء در بخش زیرین دیگ سندبلاست می شود. مواد ساینده مکش می شوند و مخلوط هوا و ماسه با فشار و سرعتی بیش از ۸۰۰ کیلومتر در ساعت به سمت سطوح قطعه پرتاب می شوند.
-اجزای سندبلاست:
سیستمهای ساب پاشی معمولا از سه بخش اصلی محفظه مواد ساینده، دستگاه هدایت کننده مواد و نازل تشکیل میشوند. مشخصات دقیق دستگاه سندبلاست به کاربری مورد نظر و نوع ساینده مورد استفاده بستگی دارد. معمولا به منظور هدایت مواد ساینده درون شلنگ و پاشیدن آنها بر روی سطح از فشار هوا، نیروی گریز از مرکز یا فشار آب استفاده میشود.
- فشار هوا: در این سیستم، با تولید هوای فشرده توسط کمپرسور، ساینده به صورت دهشی یا مکشی به دورن نازل منتقل شده و به روی سطح پاشیده میشود.
- نیروی گریز از مرکز: در این سیستم، یک پروانه دوار با ترکیب نیروهای گریز از مرکز و اینرسی، انرژی لازم برای هدایت و پرتاب مواد ساینده بر روی سطح را فراهم میکند.
- فشار آب: این سیستم، با استفاده از فشار هوا (اضافه کردن آب در نزدیکی خروجی نازل) یا فشار آب (اضافه کردن آب به محفظه)، مخلوط ماده ساینده با آب (دوغاب) را به روی سطح اعمال میکند.
-انواع دستگاه سندبلاست:
بر اساس نوع کاربری و حجم تمیزکاری، سیستم تجهیزات ساب پاشی به سه نوع سندبلاست قابل حمل، کابین سندبلاست و اتاق سندبلاست تقسیم میشوند:
الف- سندبلاست قابل:
یکی از تجهیزات پرکاربرد برای اجرای تمیزکاری پاششی سطوح کوچک تا بزرگ، دستگاه سندبلاست قابل حمل یا پرتابل است. اجزای سندبلاست پرتابل عبارت هستند از:
- کمپرسور هوا: تولید هوای فشرده
- دیزل ژنراتور: تامین انرژی مورد نیاز برای راهاندازی کمپرسور هوا
- دیگ: مخزن تحت فشار برای نگهداری ساینده و هدایت آن به سمت شلنگ
- شلنگ: واسط بین دیگ و نازل برای خروج ساینده و اعمال آن به سطح
- نازل: محل خروج ساینده با فشار بالا
سیستم سندبلاست پرتابل، معمولا توسط یک کمپرسور دیزلی تغذیه میشود. کمپرسور هوا، حجم بالایی از هوای فشرده را به دیگ سندبلاست وارد میکند. در دیگ سندبلاست، میزان ساینده خروجی قابل تنظیم است. در این سیستم میتوان از چندین دیگ تحت فشار نیز استفاده کرده. سیستمهای مجهز سندبلاست پرتابل معمولا بر روی کامیون نصب میشوند. این کار، قابلیت جابجایی راحت تجهیزات را بهبود میبخشد.
در سندبلاست مرطوب، ساینده در معرض جریان تحت فشار آب یا مایعات دیگر قرار میگیرد. این فرآیند یاعث تشکیل دوغاب میشود. استفاده از تجهیزات پرتابل در این روش، مانعی برای بازیابی ساینده ایجاد نمیکند.
ب- کابین سندبلاست:
کابین سندبلاست، یک سیستم حلقه بسته است که به اپراتور اجازه میدهد تا ضمن تمیزکاری سطح، مواد ساینده را پس از استفاده بازیابی کند. کابین سندبلاست، معمولا برای تمیزکاری قطعات مکانیکی در ابعاد کوچک تا متوسط مورد استفاده قرار میگیرد. این دستگاه معمولا از چهار جز زیر تشکیل میشود:
- مخزن یا کابین
- سیستم سندبلاست
- سیستم بازیابی ساینده
- محل جمعآوری گرد و خاک
در تمیزکاری توسط کابین سندبلاست، قطعه مورد نظر درون کابین قرار میگیرد و کابین بسته میشود. سیستم سندبلاست درون کابین قرار دارد. سپس، اپراتور دستان خود را وارد حفرههای مخصوص (دستکشها) میکند. بر روی کابین، یک بخش شیشهای وجود دارد که امکان مشاهده و کنترل فرآیند سندبلاست را فراهم میکند. در بخش پایینی دستگاه (زیر کابین) نیز پدالی برای روشن/خاموش کردن دستگاه قرار داده شده است. به منظور تمیزکاری تعداد زیادی از قطعات مشابه میتوان از مدلهای اتوماتیک کابین سندبلاست استفاده کرد.
سه سیستم سیفونی، فشاری و مرطوب، سیستمهایی هستند که معمولا برای تمیزکاری با کابین سندبلاست مورد استفاده قرار میگیرند.
- سندبلاست سیفونی یا مکشی: در این سیستم، کمپرسور هوا باعث ایجاد مکش در محفظه میشود. فشار منفی، ساینده را از درون نازل به سمت سطح مورد نظر میکشد.
- سند بلاست فشاری یا دهشی: در این سیستم، ساینده درون یک محفظه تحت فشار ذخیره میشود. فشار محفظه برابر با فشار در محل اتصال شلنگ است. میزان ساینده مورد نیاز به درون شلنگ منتقل شده و توسط هوای فشرده به سمت نازل پرتاب میشود.
- سند بلاست مرطوب: این سیستم، کابین از تجهیزاتی برای تزریق دوغاب حاوی ساینده به مسیر جریان هوای فشرده استفاده میکند. این سیستم در مواقعی به کار میورد که احتمال آسیب دیدن قطعات بر اثر گرمای ناشی از سندبلاست خشک وجود داشته باشد.
ج- اتاق سندبلاست:
اتاق سندبلاست در واقع یک مدل بسیار بزرگ از کابین سندبلاست است. در این سیستم، اپراتورها برای تمیزکاری و پرداخت سطوح مختلف وارد یک اتاق میشوند. اتاقهای سندبلاست و تجهیزات آنها، اندازههای بسیار متنوعی دارند. برخی از این اتاقها به اندازهای بزرگ هستند که میتوانند برای تمیزکاری اشیایی نظیر واگن، تجهیزات صنعتی، ماشینآلات، خودرو، تجهیزات ساختمانسازی و حتی هواپیما مورد استفاده قرار بگیرند
هر یک از کاربردهای اتاق سندبلاست، نیازمند تجهیزات متفاوتی است. با این وجود، اجزای اصلی اکثر اتاقهای سندبلاست عبارت هستند از:
- سیستم نگهدارنده یا محفظه: اتاقی که برای اجرای تمیزکاری و جلوگیری از خروج مواد طراحی شده است.
- سیستم سندبلاست: از سیستمهای فشار هوا و نیروی گریز از مرکز استفاده میشود.
- دیگ سندبلاست: محفظه تحت فشار و محل قرارگیری ساینده است.
- سیستم جمعآوری گرد و خاک: هوای درون اتاق را فیلتر کرده و از خروج ذرات جلوگیری میکند.
- سیستم بازیابی ساینده: به منظور جمعآوری سایندهها و استفاده مجدد آنها مورد استفاده قرار میگیرد. این سیستم معمولا از تجهیزات مکانیکی یا پنوماتیکی نصب شده در کف اتاق تشکیل میشود. البته، امکان جمعآوری دستی مواد ساینده و برگرداندن آنها به درون محفظه نیز وجود دارد.در سیستم اتاق سندبلاست، با اضافه کردن تجهیزات دیگری مانند جرثقیل سقفی (جابجایی و چرخاندن قطعات)، راهپلههای متصل به دیوار (جابجایی اپراتور) و عایقهای صوتی (کاهش صدا)، میتوان عملکرد و بهرهوری ساب پاشی را بهبود بخشید.
-عوامل موثر در کیفیت سندبلاست:
عوامل مختلفی نظیر فشار، طول نازل، نوع ساینده و ویژگیهای ذرات ساینده بر روی کیفیت سندبلاست تاثیرگذار هستند. پیش از اجرای فرآیند سندبلاست باید این پارامترها را با دقت کالیبره کرد. در صورت عدم نظارت کافی بر روی این موارد، احتمال آسیب رسیدن به سطح یا تمیزکاری نامناسب آن وجود دارد. به عنوان مثال، برای برداشتن پوششهای ضخیم، باید از سایندههای سخت و فشار بالا استفاده کرد. برداشتن پوششهای ظریف نیز نیازمند اعمال سایندههای نرم با فشار پایین است.
-مزایای سندبلاست:
- اجرای سریع و آسان: فرآیند سندبلاست نسبتا آسان و سریع است. با این وجود، برای رعایت الزامات ایمنی و اجرایی باید از نیروی کار ماهر استفاده کرد.
- تمیزکاری سریع و آسان: علاوه بر فرآیند اجرا، تمیز کردن محیط کار پس از اتمام سندبلاست نیز سریع و آسان است. این ویژگی بر روی کیفیت اجرایی و ایمنی محیط تاثیر میگذارد.
- کیفیت بالا: استفاده از روشهای سندبلاست برای تمیزکاری انواع مختلف سطوح، نتیجه قابل قبولی را به همراه دارد.
- تجهیزات کم: سندبلاست با استفاده از یک کمپرسور، دیگ و نازل قابل اجرا است.
- هزینه پایین: سرعت، کیفیت و نیاز به تجهیزات کم، هزینه تمام شده سندبلاست را نسبت به روشهای سنتی کاهش میدهد.
- کاربردهای متعدد: فرآیند سندبلاست در بسیاری از حوزهها نظیر مکانیک، عمران، شیمی، پلیمر و غیره مورد استفاده قرار میگیرد.
- سازگاری با محیط زیست: اکثر سایندههای سندبلاست با محیط زیست سازگار هستند و در صورت عدم بازیابی، باعث آلایندگی یا آسیبهای زیستمحیطی نمیشوند.
-معایب سندبلاست:
با وجود نوآوریهای انجام شده در فرآیند سندبلاست (ساب پاشی) و معرفی سایندههای جایگزین، روشهای قدیمی به همراه سایندههای سمی هنوز هم مورد استفاده قرار میگیرند. با توجه به این نکته، از معایب اصلی سندبلاست میتوان به موارد زیر اشاره کرد:
- بیماریهای تنفسی: در صورت استفاده از ماسه (مخصوصا نوع سیلیسی)، احتمال رخ دادن بیماری سیلیکوزیس در کارکنان افزایش مییابد.
- نیاز به تهویه: فرآیند سندبلاست خشک با تولید گرد و خاک زیاد همراه است. به همین دلیل، اجرای این فرآیند باید در یک محیط دارای تهویه صورت گیرد.
- احتمال آسیب فیزیکی: به دلیل استفاده از ساچمههای فولادی، دانههای شیشهای و دیگر مواد سخت، برخورد ذرات ساینده به پوست میتواند باعث آسیب فیزیکی شود. در صورت استفاده از تجهیزات ایمنی، این مشکل برطرف خواهد شد.
مقالات و اخبار