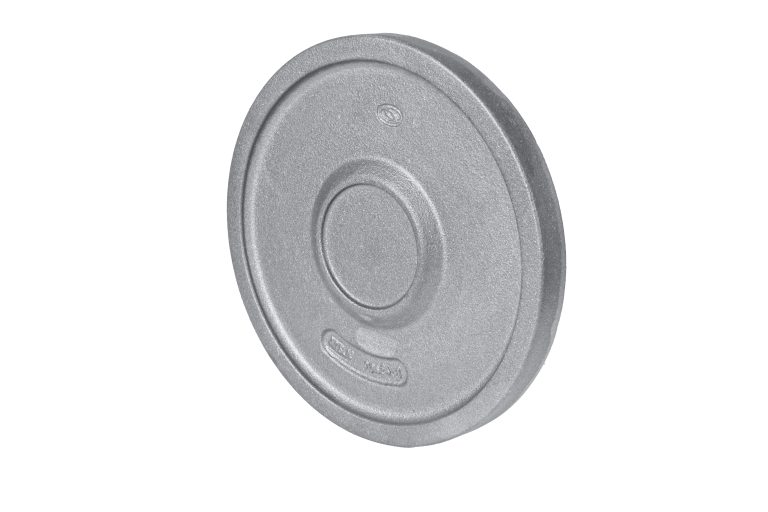
مقاومت به خستگی و سایر خصوصیات کاربردی چدن نشکن آستنیتی نوع Ni-Mn
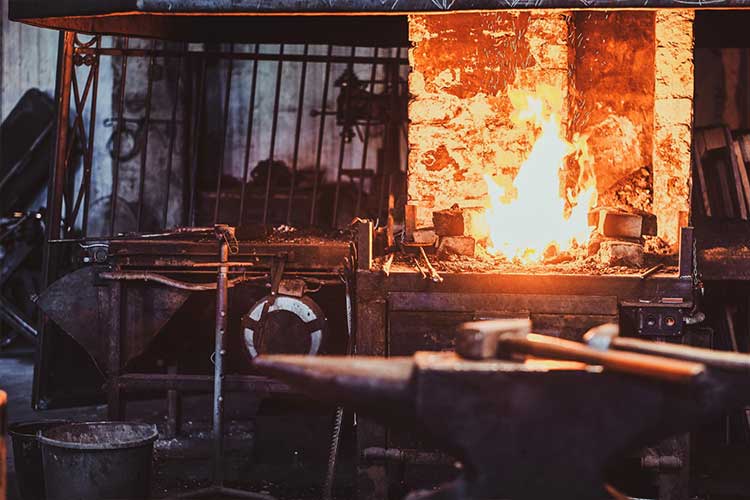
چکیده:
هدف از تحقیق حاضر بررسی مقاومت به خستگی چدن نشکن آستنیتی و مقایسه آن با سایر انواع چدن شکن است. چدن نشکن آستنیتی مورد بررسی آلیاژ (7- 13EN-GJSA-XNiMn) حاوی 13 درصد نیکل و 7 درصد منگنز بوده و دارای ساختار زمینه آستنیت می باشد. ریز ساختار با استفاده از میکروسکوپی نوری بررسی شد و خصوصیات مکانیکی با آزمایش کشش، آزمایش خمش ضرب های و سختی سنجی برینل تعیین گردید.
آزمایشات خستگی نیز در درجه حرارت محیط (اتاق) تحت اعمال بار کشش و فشار متناوب سینوسی انجام و نتایج با خصوصیات خستگی چدن نشکن فریتی –پرلیتی و پرلیتی – فریتی مقایسه شد. نتایج آزمایشات نشان داد که چدن نشکن آستنیتی حاوی Ni-Mn دارای استحکام کششی و سختی پایین ولی ازدیاد طول نسبی و انرژی ضربه بالاتر نسبت به سایر چدن های نشکن است. البته حد خستگی چدن نشکن آستنیتی نیز پایین تر بود.
مقدمه
چدن نشکن دارای استحکام، ازدیاد طول نسبی، مقاومت به خستگی، مقاومت به شوک و مقاومت به فرسایش و خوردگی بالایی است. سایر امتیازات مانند قابلیت تولید محصولات با اندازه های مختلف و اشکال پیچیده همچنین قابلیت ریخته گری و ماشینکاری خوب و قابلیت بالای بازیابی موجب شده تا چدن های نشکن در بسیاری از کاربردها آلیاژی، اقتصادی باشد(2 و 1) چدن نشکن آستنیتی گروهی از آلیاژهای ریختگی با یک زمینه آستنیتی بوده و حاوی مقادیر بالایی از نیکل، منگنز و برخی اوقات مس یا کروم برای پایداری زمینه آستنیت در درجه حرارت محیط (اتاق) است.
در این آلیاژها کربن به صورت گرافیت کروی است. آستنیت در اثر عناصر آلیاژی خاص، به طور غالب نیکل به وجود می آید که باعث می شود درجه حرارت تجزیه یوتکتوئیدی آستنیت تا درجه حرارت محیط (اتاق) پایین بیاید. این آلیاژها با مقادیر نیکل 15 تا 36 درصد در گروه چدن های Ni-Resist در نظر گرفته می شود. چدن های نشکن آستنیتی بر اساس استاندارد STN EN13835 دسته بندی شده و در استاندارد اروپایی 10 گرید چدن نشکن بر اساس ترکیب شیمیایی، ساختار خصوصیات مکانیکی (استحکام تسلیم، استحکام کشش، ازدیاد طول نسبی، انرژی شکست و سختی برینل) و خصوصیات فیزیکی شناخته شده است. البته در استاندارد خصوصیات خستگی این چدن ها ارائه نشده است.
برای تحقیق حاضر چدن نشکن آستنیتی حاوی نیکل و منگنز و شناسه استاندارد EN-GJSA-X NiMn 13- 7 انتخاب شد. در چدن های نشکن آستنیتی نیکل عنصر اصلی آلیاژی بوده و برای پایداری آستنیت در درجه حرار ت های پایین مقدار آن باید حدود 20 درصد باشد که این مقدار از میزان نیکل فولادهای ضد زنگ متداول بالاتر است. این امر بدلیل فقدان تاثیر مقدار بالای کروم ضروری است، زیرا کروم در چدن های گرافیتی فقط در مقادیر محدود استفاده می شود در غیر این صورت تشکیل کاربید اضافی، افزایش سختی و در نتیجه دشواری ماشینکاری را ایجاد خواهد کرد.
بنابر شرایط و دلایلی از جمله ضرورت های اقتصادی بخشی از نیکل می تواند با سایر عناصر آستنیت زا مانند منگنز و مس جایگزین می شود، زیرا قیمت منگنز بسیار پایین تر از نیکل بوده و جایگزینی آن در برخی گریدهای چدن آستنیتی ایجاد مزیت اقتصادی می کند. البته منگنز مرتبط با مقاومت به سرد به کار می رود. اما مس فقط در چدن های خاکستری می تواند جایگزین نیکل شود و نه در چدن های نشکن زیرا از تشکیل گرافیت کروی جلوگیری می کند. مقدار کروم و نیکل را می توان در نیکل معادل مطابق معادله ( 1)خلاصه نمود:
معادله (1)
در مواردی که ساختار آستنیت پایدار در دمایی پایین تر از درجه حرارت محیط (اتاق) موردنیاز باشد وجود نیکل معادل حداقل23.5 درصد ضروری است. البته ناپایداری معمولا یک مشکل نیست بنابراین به لحاظ دلایل اقتصادی و هزینه ها مقدار نیکل در دامنه و محدوده پایینی حفظ می شود. به دلیل احتمال افت نیکل در نواحی دچار جدایش شده، برای بخش های ضخیم مقدار نیکل باید اندکی بالاتر باشد.
منگنز یک پایدار کننده موثر آستنیت بوده ولی ارتقاء دهنده مقاومت به خوردگی و حرارت نیست بنابراین فقط در گرید غیرمغناطیسی 7-13 GJSA-X NiMn در جایگزین نیکل استفاده می شود. اگر مقاومت به خوردگی هم موردنظر باشد گریدهایی با مقدار کروم و منگنز پایین باید انتخاب گردد. افزودن 4 درصد منگنز پایداری آستینت را افزایش می دهد بنابراین کاربردها در درجه حرار ت های زیر صفر امکا ن پذیر خواهد شد. جایگزینی قسمتی از نیکل با 7 درصد منگنز موجب تولید یک چدن نشکن ضد مغناطیس با قیمت مناسب می شود تا از میدان آستنیت فرومغناطیس با مقادیر بالای نیکل پرهیز شود.
چدن نشکن آستنیتی معمولا با مقاومت بالا در برابر درجه حرارت بالا و همچنین پایین، مقاومت خوب خوردگی در برابر آب دریا و محیط های قلیایی، مقاومت به خوردگی مکانیکی، ازدیاد طول نسبی بالا و غیرمغناطیسی بودن شناخته می شود. چدن نشکن حاوی Ni و Mn برای قطعات ریختگی غیرمغناطیسی مانند در پوش و پوسته توربوشارژها، پوسته های سیستم های سوئیچینگ، فلانج های عایق، کلامپ ها و اتصالات، به کار می رود.
برخی از این قطعات در معرض تنش خستگی قرار می گیرند بنابراین ضروری است مقاومت به خستگی آن ها مشخص شود به را ه های افزایش خصوصیات خستگی این قطعات توجه گردد. تحقیقات مختلفی مانند ( 19 تا 11 ) در خصوص ارتباط بین ترکیب شیمیایی، ساختار، خصوصیات مکانیکی، مقاومت به حرارت یا خوردگی چدن های نشکن آستنیتی انجام شده ولی فقط تعداد اندکی مرتبط با خصوصیات خستگی هستند. به این علت در مقاله حاضر مقاومت به خستگی چدن نشکن آستنیتی مورد بررسی قرار گرفت.
روش آزمایش و آلیاژ
در تحقیق حاضر از چدن نشکن آستنیتی آلیاژ شده با 13 درصد نیکل و 7 درصد منگنز استفاده شد. بر اساس استاندارد STN EN 13835 این گرید چدن نشکن EN-G JSA-X Ni Mi 13- 7 و به صورت عددی 5.3506 است. فرآیند ریخته گری در کارگاه دانشکده مهندسی ریخته گری دانشگاه تکنولوژی Brno انجام شد. آلیاژ نیز در یک کوره القایی ذوب گردید. عملیات تلقیح و جوانه زدایی به روش ساندویچی درون پاتیل صورت گرفت. نمونه های ریختگی مطابق شکل 1 بلوک های Y شکل بوده که درون قالب ماسه ای ریخته گری شدند.
ترکیب شیمیایی ذوب در جدول 1 ارائه شده و مواد اولیه شارژ شامل قراضه آهنی، شمش آهن خام و افزودنی برای تنظیم ترکیب شیمیایی (مقدار کربن، سیلیسیم، نیکل و منگنز) عبارت بودند از مواد کربن ده، فروسیلیسیم Fe Si 75 نیکل و فرومنگنز FeMn80 تلقیح (نشکن سازی) با استفاده از Fe Si Mg7 و جوانه زایی یا Fe Si75 انجام گردید. مقادیر مواد به شارژ نیز برای دستیابی به ترکیب شیمیایی و ساختار آستنیتی انتخاب شد. ترکیب شیمیایی مذاب در جدول 2 ارائه شده است.
با روش ماشین کاری بلو ک های Y شکل، نمونه های متالوگرافی، نمونه برای آزمایشات مکانیکی(آزمایش کشش، آزمایش خمش ضرب های، سختی سنجی) و آزمایش خستگی تهیه گردید. برای آزمون کشش 3 استوانه به قطر 10 و طول 50 میلیمتر و برای آزمون ضربه 3 نمونه با مقطع مربع به ابعاد 10 و طول میلیمتر بدون شکاف آماده شده.
برای سختی سنجی از نمونه های آزمون ضربه استفاده گردید به طوری که میانگین پنج انداز ه گیری از پنج نقطه به عنوان سختی ثبت شد. آزمون خستگی بر روی پانزده نمونه یا مقطع دایره به قطر 8 میلیمتر انجام گردید. آزمایشات متالوگرافی و آزمون خستگی و مطالعات شکست نگاری در آزمایشگا ه های دپارتمان مهندسی مواد دانشگاه Zilina انجام شد.مطالعات متالوگرافی با یک میکروسکوپ نوری Neophot32 مجهز به نرم افزار آنالیز تصویری Elements (20)AR 5.20 مطابق استاندارد (STN 42046) STN EN ISO 945صورت گرفت.
برای آزمایش کشش و تعیین استحکام تسلیم ،RP0.2 استحکام کشش و ازدیاد طول نسبی A مطابق استاندارد(STN EN ISO 6892-1) یک دستگاه کشش Zwick Roell Z250 به کار گرفته شد. آزمون ضربه با یک دستگاه چارپی چکشی PSW 300 مطابق استاندارد 1 STN EN ISO 148- بر مبنای انرژی جذب شده K انجام شد. سختی برینل نمونه ها نیز با یک دستگاه CV-3000 LDB بر اساس استاندارد (STN EN ISO -6506) 1 تعیین گردید.
اما آزمایش تعیین حد خستگی با فرکانس پایین متناوب سینوسی اعمال بار کشش – فشار ( push-pull)نسبت تنش R = -1 (، فرکانس 75 هرتز در درجه حرارت محیط ) ( بوسیله یک دستگاه انداز ه گیری خستگی Zwick/Roell Amsler 150 HFP5100 (شکل c 2 ، b 2 )مطابق استاندارد (0362STN 40) و منحنیWohler ارتباط بین درجه تنش و تعداد سیکل ها تا گسیختگی Nf و حد خستگی c 5 برای سیکل تعیین شد.شکست نگاری بر روی سطوح شکست نمونه های آزمون خستگی با به کارگیری میکروسکوپ الکترونی روبشی VEGA II LMU صورت گر فت.
نتایج وسگالش
بررسی متالوگرافی نشان داد که ریزساختار نمونه EN.GJSA X NiMn13-7 (5.3506) متشکل از آستنیت و گرافیت های کروی بوده )شکل 3( و زمینه آستنیت در اثر افزودن نیکل و منگنز به وجود آمده است. گرافیت ها نیز بخوبی به شکل کروی هستند فقط در موارد اندکی شکل غیرکروی دارند. ناحیه آبی روش در زمینه نشان دهنده جدایش عناصر اصلی(مانند سیلیسیم، منگنز، نیکل) حل شده در محلول جامد است.
در این ناحیه همچنین آخال ها و ناخالصی هایی نیز وجود دارد. ارزیابی کمی ریزساختار بر اساس یک استاندارد و به وسیله آنالیز تصویری تعیین گردید. بر اساس استاندارد 80 945 STN EN ISO درصد گرافیت ها با انداز های معادل 30 تا 60 میکرون کاما کروی بوده و 20 درصد غیرکروی هستند. ضریب شکل گرافیت 0.72 ، قطر معادل 36.3 میکرون، تعداد گرافیت کروی در هر میلیمتر مربع 78.1 و مقدار گرافیت 9.4 درصد بوده است.
ریزساختار که دارای تاثیری مستقیم بر خصوصیات مکانیکی دارد به وسیله آزمون های کشش، ضربه خمشی و سختی سنجی برنیل تعیین می شود. الزامات خصوصیات مکانیکی بر اساس استاندارد، خصوصیات مکانیکی اندازه گیری شده در جدول 4 ارائه شده است. منحنی های کشش بدست آمده از آزمایش کشش بر روی سه نمونه در شکل 4 نشان داده شده که در آن استحکام تسلیم RP0.2معادل 7/ 237 مگاپاسکال، استحکام کشش Rm معادل 475.3 مگاپاسکال، ازدیاد طول نسبی A معادل 29 درصد ، کاهش سطح ناحیه Z معادل 5/ 21 درصد، K انرژی جذب شده 197.3 ژول (نمونه بدون شکاف) و سختی برینل138.7 (HBW 10/3000/10) بوده که خصوصیات اندازه گیری شده در محدوده الزامات استاندارد بوده است.
آزمایشات خستگی در فرکانس پایین به صورت اعمال بار کششی – فشاری ( push-pull ) متناوب با فرکانس 75 هرتز بر روی 15 نمونه انجام شد. برای تمامی سطوح انتخاب شده درجه تنش 2 یا 3 نمونه برای دقت بالاتر نتایج انتخاب شدند. از مقادیر اندازه گیری شده σa و تعداد سیکل ها Nf تا گسیختگی(شکل 5) منحنی خستگی Wohler ترسیم شده داده های به دست آمده با تابع نمایی و استفاده از روش حداقل مربع(23) بهم نزدیک شدند. از روی منحنی خستگی، حد خستگی σcبرای سیکل و نسبت حد خستگی به استحکام کششRm σc تعیین گردید. حد خستگی بالاترین تنشی است که آلیاژ به طور نظری می تواند در برابر تعداد نامحدود سیکل اعمال بار مقاومت کند.
تعداد سیکل های اعمال بار با کاهش درجه تنشσa افزایش می یابد. آزمایشات خستگی نشان داد که حد خستگی σc معادل 150 مگاپاسکال و نسبت حد خستگی به استحکام کششی یعنی σc/Rm معادل 0.32 است.
خصوصیات خستگی چدن نشکن آستنیتی با دو چدن نشکن فریتی – پریتی و پریتی – فریتی مقایسه شد(شکل 6). نوع اول که با سیلیسیم و مولیبدن آلیاژ شده(EN-GJS-X300 SiMo 4-1 ) و چدن نشکن فریتی – پرلیتی و نوع دوم با سیلیسیم و مس آلیاژ شده (EN-GJS-X300 Si Cu 4-1.5) پرلیتی-فریتی بود. خصوصیات خستگی هر دو چدن نشکن تحت همان شرایط آزمون بر روی چدن نشکن آستنیتی اندازه گیری شد.
بنابر نتایج به دست آمده خصوصیات خستگی چد ن های نشکن گرید Si Mo و Si Cu نسبت به چدن نشکن آستینتی حد خستگی σc بالاتری دارد و گرید SiCu (σc = 270 Mpa, σc /Rm = 0.41) دارای حد خستگی و نسبت به استحکام کشش σc /Rm بالاتری نسبت به گرید Si Mo (σc = 210 Mpa, σc /Rm = 0.37) است. منحنی های Wohler
چدن نشکن در شکل 6 ارائه شده، نتایج نشان می دهد که حد خستگی σc مرتبط با استحکام کششی Rm بوده بدین معنی که حد خستگی با افزایش استحکام کشش بالا می رود. آزمایشات خستگی هر سه نوع چدن نشکن فقط در سیکل متقارن اعمال بار کشش فشار ( push-pull )تنش متوسط سیکل ( σm = 0 ) انجام شد.
البته این نوع ساده اعمال بار نسبتاً کمتر در شرایط عملی واقع می شود. به خصوص اجزای ماشین معمولا تحت بارهای متناوب با یک مقدار تنش متوسط سیکل قرار می گیرد. به منظور بدست آوردن یک تصویر کامل از مقاومت به خستگی، ضروری است آزمایشات در مقادیر متفاوت تنش متوسط σm انجام شود و یک نمودار از حد سیکل های اعمال شده ایجاد شود.
جایگزین این امر نمودار خستگی Smith است که مقادیر حد خستگی را برای انواع مستقل اعمال بار متناوب تعریف میکند(متقارن، غیرمتقارن، ناپدید شونده، ارتعاشی). ناحیه نمودار نشان دهنده زمینه ایمن اعمال بار به قطعه در انواع متفاوت بار متناوب بوده به طوری که اگر بار از این ناحیه بیشتر نباشد تحت اعمال آن خستگی و شکست اتفاق نمی افتد.
در شکل 7 نمودارهای ساده شده خستگی Smith برای هر سه نوع از چد ن های نشکن نشان داده شده که در آن مقدار حد خستگی بستگی به نوع بار اعمالی متناوب (متقارن، غیرمتقارن، ناپدید شونده، ارتعاشی) دارد. سیکل متقارن σc متناوب دارای کوچک ترین مقدار مطلق از حد خستگی است. با افزایش تنش متوسط σm مقدار مطلق حد خستگی σc = σm + σa افزایش می نماید اما هم زمان بالاترین درجه تنش σa کاهش می یابد.
مقایسه سه نمودار (شکل 7) نشان می دهد که چدن های نشکن گرید SiMo و Si-Cu نسبت به چدن هستند در نتیجه در انواع مختلف اعمال بار متناوب دارای حد نشکن آستنیتی در نمودار خستگی Smith دارای یک ناحیه قابل ملاحظه ای بزر گ تر خستگی بالاتری می باشند. البته گرید Si Cu نسبت به Si Mo ناحیه بزرگتری از نمودار خستگی Smith را دارد.
پس از آزمایشات خستگی بررسی شکست نگاری نمونه های منتخب چدن شکن آستنیتی انجام شده مکانیزم های میکروسکوپی گسیختگی نمونه های شکسته شده تحت تنش خستگی در شکل 8 نشان داده شده است. در شکل a 8 یک مرور کلی از سطح شکست پس از گسیختگی در اثر خستگی ارائه شده که در آن ناحیه توسعه ترک خستگی از منطقه بیشتر خرد شده از گسیختگی نهایی قابل تشخیص است.
شکست های خستگی از یک مک (عیب ریختگی) آغاز شده که به عنوان یک شکاف اولیه (شکل b 8) یا یک ترک زیر سطح ( شکل8c ) عمل می کند. شکست خستگی از نوع گسیختگی خستگی از بین دانه آستنیت(شکل d 8)بوده و گسیختگی خستگی درون دان های مشاهده نشد. ناحیه نهایی گسیختگی نیز با وجود فرو رفتگی (دیمپل( در مورفولوژی سطح شکست نشان از شکست و گسیختگی نرم است (شکل e 8).مکانیزم های میکروسکوپی گسیختگی خستگی چدن نشکن آستنیتی مرتبط با ریزساختار آن می باشد.
نتیجه گیری
استاندارد اروپایی چدن های نشکن آستنیتی ترکیب شیمیایی، خصوصیات مکانیکی و فیزیکی مشخص شده لیکن خصوصیات خستگی ارائه نگردیده است. بنابراین هدف اصلی تحقیق حاضر تعیین مقاومت به خستگی گرید NiMn چدن نشکن آستنیتی و مقایسه آن با چد ن های نشکن با ساختار زمینه دیگر است.
آزمایشات نشان داد که حد خستگی چدن نشکن آستنیتی در سیکل اعمال بار کشش – فشار ( push-pull) متقارن و متناوب نسبت به چدن های نشکن با زمینه فریتی – پرلیتی و پرلیتی– فریتی پایین تر می باشد. چدن نشکن آستینتی نسبت به چدن های نشکن با زمینه فریتی – پرلیتی و پرلیتی – فریتی دارای ناحیه کوچک تری از نمودار ساده Smith )ناحیه ای ایمن در اعمال انواع بارهای متفاوت متناوب(است. این بدان معنی بوده که چدن نشکن آستنیتی مقاومت به خستگی کمتری دارد و علت آن نیز استحکام کشش کمتر به لحاظ ریزساختار می باشد.
مقایسه چدن آستنیتی گرید NiMn ، فریتی – پرلیتی SiMo و پرلیتی – فریتی ( SiCu ) نشان می دهد که استحکام تسلیم، استحکام کششی، سختی و حد خستگی افزایش ولی ازدیاد طول نسبی، کاهش سطح مقطع و انرژی جذب شده شکست ضربه، کاهش می یابد. چدن نشکن آستنیتی دارای استحکام و خصوصیات خستگی پایین ولی پلاستیسیته عالی است. البته این چدن دارای بسیاری مزیت های دیگر خصوصاً مقاومت بالا به خوردگی در محیط های مهاجم و اکسیدی و امکان استفاده در درجه حرار ت های پایین یا بالا و امکان استفاده به عنوان قطعات ریختگی غیرمغناطیسی است.
منابع:
منبع خارجی: 3 .Mater .Metall .Arc
منبع فارسی: تیرماه 1403- مجله صنعت ریخته گری
ترجمه: محمدجواد توسلی کیالنی
[1] S . Věchet, J. Kohout, O. Bokůvka, Fatigue Properties of Ductile Cast Iron, EDIS , Žilina, Slovakia (2002).
[2] O . Bokůvka, G. Nicoletto, M. Guagliano, L. Kunz, P. Palček,F. Nový, M. Chalupová, Fatigue of Materials at Low and High Frequency Loading, EDIS , Žilina, Slovakia (2014).
[3] Giessereilexikon, https://www.giessereilexikon.com/en, accessed:15.6.2022
[4] D.M. Stefanescu, AS M Handbook 1A: Cast Iron Science andTechnology, AS M International, Materials Park, USA(2017).
[5] K . Röhrig, Konstruieren + Giessen 29 (2), 2-33 (2004).
[6] V. Kaňa, Slévárenství 65 (1-2), 6-11 (2017).
[7] H . Berns, W. Theisen, Ferrous Materials: Steel and Cast Iron,Springer, Bochum, Germany (2008).
[8] S . Franke, Pocket Guide Foundry, Schiele & Schön, Berlin, Germany (2015).
[9] S . Franke, Giesserei-Lexikon, Schiele & Schön, Berlin, Germany (2019).
[10] J.R. Davis, AS M Specialty Handbook: Cast Irons, AS M International, Materials Park, USA (1999).
[11] N. Fatahalla, A. AbuElEzz, M. Semeida, Materials Sci nce and Engineering A 504, 81-89 (2009).
[12] M.M. Rashidi, M.H. Idris, Materials Science and Engi neering A 574, 226-234 (2013).
[13] M.M. Rashidi, M.H. Idris, Materials Science and Engi neering A 597, 395-407 (2014).
[14] E . Guzik, D. Kopycinski, Archives of Foundry 4 (12), 115-120 (2004).
[15] A . Tabor, P. Putyra, K. Zarebski, T. Maguda, Archives of Foundry Engineering 9 (1), 163-168 (2009).
[16] D. Medyński, A. Janus, S. Zaborski, Archives of Foundry Engineering 17 (1), 121-126 (2017).
[17] Y .X. Zhou, Y.D. Qu, K. Jiang, R.D. Li, Zhuzao/Foundry66 (10), 1095-1099 (2017).
[18] M. Shi, D.L. Xu, Y. Tian, Y.L. Xiong, Zhuzao/Foundry 67(1),62-65 (2018).
[19] R . Singh, T. Matsuo, K. Hayashi, M. Endo, International Journal of Fatigue 163, 107015 (2022).
[20] P . Skočovský, A. Vaško, Quantitative Evaluation of Structure of Cast Irons, EDIS , Žilina, Slovakia (2007).
[21] J. Belan, L. Kuchariková, E. Tillová, D. Závodská, M. Chalupová, Polytechnica Transportation Engineering 47 (4), 335-341(2019).
[22] P . Kopas, M. Vaško, M. Handrik, Applied Mechanics and Materials474, 285-290 (2014).
[23] I . Pobočíková, Z. Sedliačková, Communications 14, 88-93 (2012).
[24] A . Vaško, Materials Today: Proceedings 32, 168-173(2020).
مقالات و اخبار
یک نظر در “مقاومت به خستگی و سایر خصوصیات کاربردی چدن نشکن آستنیتی نوع Ni-Mn”
عالی بود