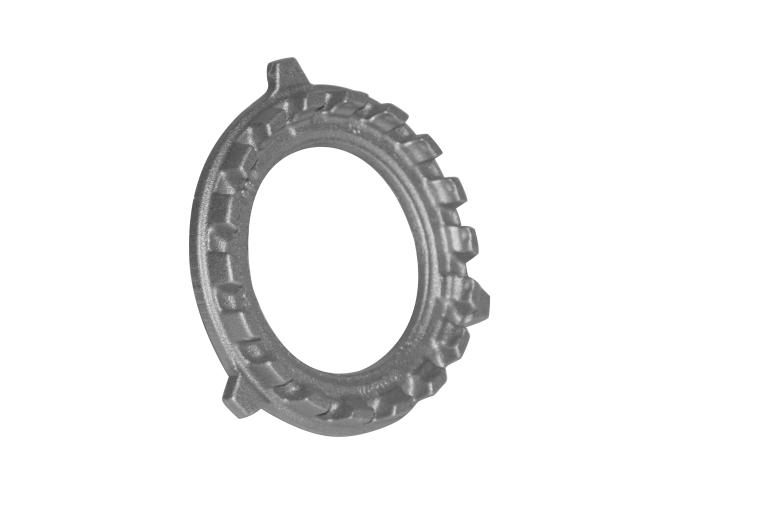
کنترل اثرپوستی در قطعات چدن با گرافیت فشرده
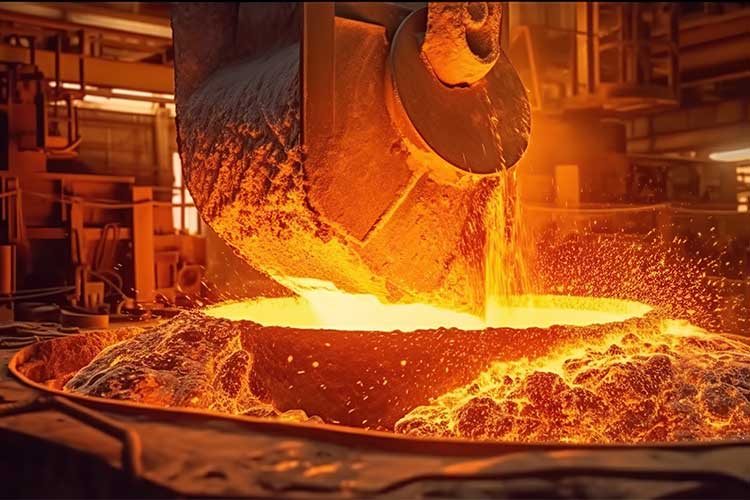
چکیده
درک چگونگــی تشــکیل اثرپوســتی در صورت نیــاز به کاهش و یا حذف آن ضروری و لازم اســت. در قســمت دوم تحقیق حاضر به بررســی مکانیزم های تشــکیل اثرپوستی بر اساس یافته های ارایه شــده در قســمت اول مقاله پرداخته خواهد شد.
عوامل موثر در مکانیزم های تشکیل اثرپوستی مانند زبری سطح، تهی شدن از گرافیت، تغییر شکل گرافیت و به وجود آمدن هاله های فریتی و پرلیتی تشــریح گردید. دو مکانیزم برای تغییر شکل گرافیت مطرح گردید:
یکی تهی شدن از منیزیم در اثر واکنش های شیمیایی با اکسیژن و گوگرد و دیگری اثرات سینتیک انجماد بر انجماد آستنیت اولیه. یک مدل دو بعدی نفوذ حرارتی برای پیشبینی ضخامت اثرپوستی بر مبنای مکانیزم اکســید شدن منیزیم توسعه یافت.
دیاگرام فازی غیرمتقارن Fe-C اثر سینتیک انجماد بر مقدار آستنیت اولیه تولید شده در دیواره نزدیک به قالب را تشریح مینماید. اگر آستنیت اولیه تولید شود منیزیم در مذاب بیرون زده و در نتیجه آن ناحیه تهی از منیزیم شده و بدین ترتیب لایه با اثرپوستی تشکیل میشود.
مقدمه
در قســمت اول مقاله اهميت اثرپوســتی بر خصوصيــات مکانيکی چدن با گرافيت فشــرده (CG) و چدن نشــکن به طور خلاصه ارايه شــده و در قسمت دوم مــروری بر يافته های مهم از تحقيقات اخير نگارندگان و ســاير محققين در خصوص درک مکانيزم های تشــکيل اثرپوستی ارايه گرديده است.
بديهی است آگاهی از عوامل تشــديدكننده تشکيل اثرپوســتی و درک مکانيزم تشکيل برای توسعه بهترين روش ها و راه حل ها جهت به حداقل رساندن اثرپوستی مفيد خواهد بود.
پیش زمینه
-
علائم اثرپوستی
تحقيقات قبلی (1) علائم اثرپوستی را به دو دسته تقسيم میكنند:
- علائم سطحی شامل زبری سطحی
- علائم زيرسطحی كه شــامل تهی شدن از گرافيت، تغيير شکل گرافيت، فريــت و پرليت هاله ای، كه اين علائم نســبت به علائم قبلی بيشــتر مرتبط با عوامل متالورژيکی است.
زبــری ســطحی میتواند به صورت عددی به شــکل متوســط زبری Ra (ميانگين زبری) محاسبه شود. در منبع 2 چگونگی محاسبه رياضی آن ارايه شده و به تفصيل توضيح داده شده است.
زبری در هنگامی كه قطعه تحت تنش مکانيکی قرار میگيرد موجب تمركز تنش میشود. تحت بارهای متناوب زبری سطح، تشکيل ترک را تشديد میكند و علاوه بر آن زبری ســطحی ناپايداری كششی را افزايش داده و موجب كاهش خصوصيات كششی میگردد.
پايين تر آمدن درصد گرافيت در زير ســطح نســبت به مركز قطعه مرتبط با پديده تهی شــدن از گرافيت اســت. تعيين مقدار تهی شدن گرافيت میتواند به وسيله آناليز تصويری نمونه اچ نشده انجام گردد و در شکل 1 نمونه ای برای يک چدن CG ارايه شده است.
تهی شــدن از گرافيت برای خصوصيات كششی زيان آور نيست زيرا در اين صورت زمينه، تبديل به يک فولاد كربنی میشود. هرچند كه عدم حضور گرافيت بر رفتار سايش (تريبولوژيک) چدن نيز اثر خواهد داشت.تغيير شــکل گرافيت مرتبط با تبديل گرافيت كروی به فشرده و ورقه ای در پوسته قطعه می باشــد.
در مطالعات قبلی نشان داده شده كه تغيير شکل گرافيت باعث كاهش خصوصيات كششی و خستگی میگردد. تعيين ميزان كمی تغيير شکل گرافيت را همچنين میتوان به وسيله آناليز تصويری انجام داد.
برای تعيين ضخامت اثرپوســتی از ضرايب شکلی گرافيت (كروی بودن، فشرده بودن، نسبت ظاهريی و ميزان گرد بودن) استفاده میشود. در شکل 2 ميزان تغيير شکل گرافيت از طريق تغييرات ضرايب شکلی نشان داده شده است.
مشروح كامل اين روش اندازه گيری كمی در مقاله (6) ارايه گرديده است. امــا هاله پرليتی به صورت يک نوار پرليت در زير ســطح قطع ریخته گری به وجود می آيد و برعکس هاله پرليتی، هاله فريتی نيز يک لايه فريت است كه در فصل مشــترک قالب/ فلز در چدن به وجود می آيد. هاله های فريتی و پرليتی نيز قابل اندازه گيری كمی به وسيله آناليز تصويری می باشند.
مرور و بررسی مکانیزم های مطرح شده برای تشکیل اثرپوستی
-
زبری سطح
زبری سطحی نتيجه نفوذ فلز مذاب به داخل ماسه قالب است و میتوان آن را در قالب تعادل بين فشار متالواستاتيک Pst كه مذاب را به داخل دانه های ماسه فشار میدهد و فشار موئينه كه در تقابل با فشار متالواستاتيک است، بررسی نمود.
اگر Pst> باشــد باعث يک واكنش متقابل آرام شــده كه در آن از نفوذ مذاب به داخل لايه اوليه دانه های ماسه جلوگيری میشود (شکل 3) اما اگر Pst>
باشــد موجب واكنش شــديد و نفوذ عميق تر مذاب به داخل قالب و در نتيجه زبری سطح قطعه ريختگی میگردد.
فشار مذاب بدين روش محاسبه میشود: معادله
P = وزن مخصوص، =g شتاب ثقل و h ارتفاع متالواستاتيک ريختن مذاب معادله 2
انرژی سطحی بين مذاب و فاز بخار، θ زاويه تر شدن،
فاصله بين ذرات اين معادلات نشان میدهند زبری سطحی با افزايش ارتفاع متالواستاتيکی و درشتی دانه های ماسه افزايش میيابد كه البته اين موارد به صورت تجربی نيز اثبات شده است.
-
هاله فريتی و تهی شدن از گرافيت
هــر دوی اين مــوارد از يک مکانيزم پيروی میكنند. بروز لايه پوســتهای دكربوره شــده در قطعات چدن خاكستری ابتدا در سال 1962 توسط Reisener بر اســاس پديده واكنش شيميايی كربن در چدن با رطوبت و اكسيژن قالب مطرح گرديد.
احتمال بروز واكنش مستقيم كربن با هيدروژن و تشکيل CxHy نســبت به واكنش كربن با بخار آب(قالب) بســيار كمتر اســت. بنابراين واكنش های شيميايی محتمل عبارتند از:
اين واكنش میتواند منجر به تهی شــدن لايه پوســته ای از كربن گردد و مسلما اين اثر بيشتر در قالب های ماسه تر به دليل وجود رطوبت مطرح می باشد. بديهی اســت لايه دكربوره (كربن از دست داده) به صورت هاله فريتی و يا ناحيه تهــی از گرافيت ظاهر میگردد.
Matijasevic و همکارانش گزارش نمودند كه به كارگيری پودر زغال ســنگ به عنوان افزودنی به ماســه تر موجب كاهش ضخامت هاله فريتی در چدن خاكســتری میشــود. اما Swamy Narasimha و همــکاران گزارش داده اند كه افزايش مقدار سيليســيم تاثير معکوس بر ضخامت هاله فريتی دارد زيرا سيليســيم يک فريت زای قوی اســت.
دكر بوره شدن شديد سطح قطعه ريختگی نيز میتواند موجب تهی شدن از گرافيت گردد. همچنين گزارش شــده اســت كه ضخامت لايه تهــی از گرافيت در چدن خاكســتری با ضخامت قطعه افزايش میيابــد. Rickards دريافت ضخامــت لايه تهــی از گرافيت همچنين به توان دوم زمــان در محدوده درجه حرارت oC 1050-1150 (شکل 5) دارد.
-
هاله پرليتی
برخلاف تشکيل هاله فريتی، هاله پرليتی به دليل كربوره شدن لايه پوسته ای به وجود می آيد. مکانيزم های مطرح شده (1) برای تشکيل هاله پرليتی عبارتند از:
- اكسيداسيون كربن در مذاب به وسيله اكسيژن و يا بخار آب اتمسفر قالب بوده كه موجب جوانه زنی فريت و رشد در درجه حرارت استحاله A1 میگردد.
- كربوريزه شــدن لايه زير ســطحی با كربن همراه مواد قالبگيری است.
محاسبه نفوذ برای كربن قالب (1) در مقايسه با مشاهدات ميکروسکوپی ضخامت منطقی برای هاله پرليتی را پيشبينی مینمايد.
-
تغيير شکل گرافيت
چندين مکانيزم برای تشــريح تغيير شکل گرافيت در لايه سطحی قطعات چدنی پيشــنهاد شده و همه اين موارد بر پايه تهی شدن لايه زير سطحی قطعه از منيزيم اســت. اين پديده موجب تغيير شکل گرافيت از طريق تبديل گرافيت كروی به فشرده و گرافيت فشرده به گرافيت ورقه ای میگردد. دو علت نيز برای تهی شــدن لايه زير سطحی از منيزيم مطرح شده يکی واكنش Mg با گوگرد و ديگری واكنش Mg با اكسيژن است.
-
تهی شدن از منيزيم در اثر واكنش با گوگرد
قديمیتريــن نظريه به وســيله Marti و Karsoy ارايه شــده و آن ســوختن اسيد پاراتولوئن سولفوتيک (PTSA) بهكار رفته به عنوان كاتاليست در چســب های رزين فنوليک و فوران كه توليــد SO2 میكند و باعث بروز واكنش Mg-S در چدن میگردد.
اين واكنش باعث تهی شــدن پوسته قطعه ريختگی از Mg شــده و در نتيجه موجب تغيير شکل گرافيت میشود. در واقع اين محققين دريافتند نسبت از مركز تا سطح قطعه پنج برابر يعنی از 0/5 به 2/5 رسيده اســت.
اخيرا نيز Riposan و همکارانش نقش گوگرد در تهی شدن پوسته قطعه از منيزيم را تاييد نمودند. Xiaogam گــزارش نموده كه اســتفاده از يک درصد بالای ماســه برگشــتی (با چســب فوران و اورتان فنول) ضخامت لايه با گرافيت تغيير شکل يافته را افزايش داده است.
به منظور به حداقل رســاندن اثر گوگرد موجود در مواد قالبگيری، پوشــان قالب با موادی گوگردزدا مانند MgO يا CaO میتواند مفيد باشــد. واكنش های گوگردزدايی مذاب چدن به وســيله CaO توســط Voronova بدين شرح مطرح شده است:
بدين ترتيب پوشــان حاوی CaO هنگام حضور گوگرد در مواد قالبگيری بايد ضخامت اثرپوستی را كاهش دهد. به درستی اثر مفيد CaO برای قالب های دارای چســب فوران از طريق آزمايشات انجام شــده در قسمت اول مقاله تاييد گرديد، به طوریكه ضخامت اثرپوستی چدن CG فنجان های آناليز حرارتی (حاوی چســب فوران) هنگام افزودن پوشان CaO به داخل قالب فنجان از 145 ميکرون به حدود 110 ميکرون كاهش يافته است.
البته در قالب ها با چسب سيليکات سديم پوشان CaO نسبت به نمونه بدون پوشــان باعث افزايش ضخامت اثرپوستی شده زيرا پوشان CaO هدايت حرارتی بالاتری دارد. اثر پوشــان MgO نســبت به CaO متفاوت بوده و اين به خاطر مطلوب نبــودن ترموديناميک گوگردزدايی به وســيله MgO اســت.
جدول 1 گرمای تشــکيل MgS، MgO و MnS را در 298 و oK 1500 نشان میدهد و در آن مشــاهده میشود كه در تشکيل MgS نسبت به MgO در درجه حرارت اتاق، انرژی بيشــتری آزاد میگردد درحالیكه در 1500°K MgO انرژی بيشــتری آزاد میكند.
بدين ترتيب مشــخص میگردد كه MgO يک عامل گوگردزدای غير موثر است. به علاوه MgO هدايت حرارتی بالايی دارد كه موجب يک اثر معکوس در تشــکيل اثرپوستی میگردد. نتايج در شکل های 6 و 7 اين بررسی را تاييــد میكنند.
نکته حائز توجه اينكه هــر دو مورد افزودن منيزيم در لايه پوســته از طريق پوشان FeSiMg به طور چشــمگيری ضخامت اثرپوستی را كاهش میدهد.
-
تهی شدن از منيزم از طريق واكنش با اكسيژن
در قالب های با چســب ســيليکات ســديم هيچ گوگردی نــه در رزين و يا كاتاليســت وجود ندارد بنابراين اكسيداسيون عامل اصلی تلفات و كاهش منيزيم است. Tinebar و Wilson گزارش نموده اند كه در سيستم های قالبگيری با چســب های پايه آبی در پوسته قطعات چدن نشکن، گرافيت فشرده و يا ورقه ای به وجود می آيد.
آنها نتيجه گيری كردند كه رطوبت در قالب شــرايط اكســيدی به وجود میآورد كه موجب يک تلفات برای منيزيم میگردد. تهی شــدن منيزيم نيز توســط Goodrich و Lobenhofer مســتند گرديد و آناليز نقطه ای با الکترون ميکروســکوپ عدم حضور و يا كاهش ميزان منيزيم را در ناحيه ســطحی نشان داده و بدين ترتيب اكسيداسيون منيزيم دليلی برای تهی شــدن ناحيه پوستی از منيزيم مطرح شده است.
در يک تحقيق قبلی نيز مشــخص شده كه لايهای كه گرافيت تغيير شکل يافته تهی از منيزيم گرديده اســت. شکل 8 نتيجه ميکرو آناليز با ميکروسکوپ الکترونی 1(EPMA) را در طول يک تصوير ريزســاختار اچ رنگی شده را نشان میدهد.
در اين تصوير كه ناحيه آبی ساختار دندريتی و ناحيه صورتی بين دندريتی دارد، مشاهده میشود كــه منيزيم در ناحيه بين دندريتی جدايش يافتــه (با علامت های A، B و C) و همچنين اين تصوير اثبات میكند كه تغيير شکل گرافيت و تهی شدن از منيزيم با هم اتفاق میافتد.
اكسيداسيون منيزيم به طور عمده در شرايط مذاب و مذاب – جامد (خميری) هنگامی كه سرعت نفوذ چشمگير است به وجود می آيد. واكنش های عمدهای كه در اين شرايط ايجاد میشود بدين شرح میباشد:
در جدول 2 انرژی آزاد گيپس تشــکيل اين واكنش ها ارايه شــده و در آن مشــاهده میشــود كه واكنش دوم دارای پايين ترين انرژی آزاد گيپس است كه باعث میشود محتمل ترين واكنش باشد. البته اين واكنش فقط هنگامی رخ دهد كه رطوبت در دســترس باشد و در ماسه خشــک با رطوبت اندک مانند ماسه با چسب سيليکات سديم واكنش سوم را بايد به عنوان واكنش غالب در نظر گرفت.
هنگامی كه منيزيم از ســطح مذاب در اثر تشــکيل MgO حذف میشود، منيزيم اضافی از داخل چدن به وســيله نفوذ تامين میگردد بنابراين اين فرآيند به وســيله مکانيزم نفوذ كنترل میشود. مدل يک بعدی نفوذ Mg كه قبلا توسط نگارندگان توســعه يافته نيز نظريه تهی شــدن Mg در اثر اكسيداسيون را تاييــد مینمايد.
درجــه حرارت بالاتر باريزی نيز به نظر میرســد به دليل زمان طولانی تر و سرعت بالاتر نفوذ اكسيژن، موجب ايجاد اثرپوستی ضخيم تر شود. به همين دليل قطعات ريخته گری با ضخامت بيشتر كه زمان انجماد طولانی تری دارند انتظار میرود اثرپوســتی ضخيم تری داشته باشــند.
اين ارتباط توسط آزمايشات Duncan و Kroker و همچنين تحقيق مقاله حاضر قسمت اول تاييد گرديده اســت. پوشان های غير فعال بايد جريان نفوذ را كاهش دهند هر چند كه هدايت حرارتی مواد پوشان نيز نقش مهمی را ايفا مینمايد. درحالیكه نظريه تهی شــدن از منيزيم به طور موفقيت آميزی بســياری از يافته های آزمايشــی را تاييد مینمايد ليکن تمامی مشاهدات را نمیتواند تشريح كند.
برای مثال بهوجود آمدن اثرپوســتی نشــان داده شده در شکل 9 در فصل مشــترک چدن و ماسه سيليســی در فنجان آناليز حرارتی با نظريه تهی شدن از منيزيم قابل توجيه نيســت زيرا هيچ اثر و دليلی از هر گونه واكنش چدن و ماسه سيليسی به داخل چدن نفوذ نمايد نيز در تصوير وجود ندارد. نظريه تهی شدن از منيزيم همچنين در تشريح اثر كربن معادل و پوشان های غيراكتيو و اكتيو كه بر ميزان اكســيژن يا گوگرد در فصل مشــترک اثری ندارد نيز موثر نيست.
تکمله های جدید به نظریه تشکیل اثر بخشی
دو مورد جديد به نظريه تشــکيل اثرپوســتی قابل افزودن است كه در ادامه توضيح داده خواهند شد.
- يک مدل دو بعدی ارتقا يافته برای الگوی اكسيداسيون منيزيم -2 تشريح اثرات سينتيک انجماد
- مــدل دوبعدی بــرای پيشبينی ضخامت اثرپوســتی از طريق مدل اكسيداسيون منيزيم
در يــک تحقيق قديمیتر يک مــدل نفوذ يک بعدی مطرح گرديد. اين مدل دارای تعدادی محدوديت بود.
- مــدل تک بعدی نمیتواند اثر جريان حرارتی شــامل اثر جريان همگرا و واگرای حرارت و جرم در گوشه ها باشد
- نفوذ منيزيم به صورت مقدار ثابت در نظر گرفته شده است
- زمــان انجماد به طور جداگانه از طريق يک نرم افزار تجاری انجماد برآورد گرديد و به عنوان زمان نفوذ در نظر گرفته شده است.
براساس همين دلايل يک مدل دوبعدی با توجه به موارد زير طراحی گرديد: – به منظور كپی كردن اندازه اســتاندارد فنجان های آناليز حرارتی 33×33( ميلیمتر) مقطع عرضی مدل پيشبينی شــده 17×17 ميلیمتر و يک لايه ماسه به ضخامت 8 ميلیمتر در اطراف آن در نظر گرفته شد. برای كاهش بار محاسبات از صفحات متقارن استفاده گرديد.
- ميدان حرارتی متقارن با ميدان نفوذ شبيه ســازی شد تا توزيع حرارتی در تمامی پله های زمانی مشــخص شود. زمان انجماد نيز مستقيما از ميدان حرارتی برآورد گرديد.
- از نفوذپذيری به عنوان تابعی از درجه حرارت و شــرايط مذاب/جامد چدن استفاده شد.
- مقدار اوليه منيزيم 0/02 درصد در نظر گرفته شد.
- يک نشت برای منيزيم در فصل مشترک قالب/فلز به حساب آورده شد. – جابه جايی مذاب در قطعه ريختگی در نظر گرفته نشد.
- مقدار بحرانی منيزيم برای تغيير شکل گرافيت 0/015 درصد نظر گرفته شد. – تركيب چدن يوتکتيک بود.
در جدول 3 عوامل به كار رفته برای شبيه سازی به طور خلاصه ارايه شده است. روش محاســباتی به كار رفته روش تفاضل اجــزای محدود (FDM 2) بوده اســت. با در نظر گرفتن اينكه نفوذپذيری و قابليت هدايت حرارتی تابع موقعيت مکانيکی نيستند معادله پوششدهنده انتقال جرم بدين صورت خواهد بود:
معادله (3):
معادله پوشش دهنده انتقال حرارت – معادله (4) :
شارژ حرارت در فصل مشترک قالب/فلز – معادله (5):
هنگامی كه درجه حرارت در محدوده انجماد است (TS<T<TL) معادله (6) :
يکی از عوامل مهم اين مدل طراحی شده قابليت نفوذ منيزيم در چدن مذاب اســت. تحقيق اخير (21) نشان داد كه قابليت نفوذ عناصر آلياژی در مذاب چدن بســتگی به قابليت انحلال آنها در جامد دارد. با در نظر گرفتن 0/17 درصد به عنوان قابليت انحلال منيزيم در فاز جامد قابليت نفوذ منيزيم در 0K 1600 معادل 1/49×10-8 متر مربع بر ثانيه محاسبه گرديد.
همچنين ثابت (D0) و انرژی اكتيو شدن (Q) در معادله آرنئوس به ترتيب 4/35×10-7 متر مربع بر ثانيه 44/9×103 ژول بــر مول برآورد گرديده بدين ترتيب قابليــت نفوذ منيزيم در مذاب چدن را میتوان از معادله 7 محاسبه نمود:
معادله (7):
نفوذپذيری منيزيم در جامد نيز در مقدار ثابت در نظر گرفته شد. قابليت نفوذ منيزيم حد مذاب و جامد نيز از معادله 8 محاسبه گرديد:
معادله (8):
TS و TL به ترتيب درجه حرارت های جامد و مذاب هستند. نکته حايز توجه اينكه اين مدل به طور خاص برای اكسيداســيون منيزيم و اثرات ســينتيک انجماد را نمیتواند محاسبه نمايد. بنابراين اين مدل نمیتواند برای تشريح اثرات پوشانه ای قالب استفاده شود. و
يک ترموكوپل مجازی در داخل گوشــه شــبکه برای كپیبرداری موقعيت واقعی ترموكوپل قرار داده شــد. (شــکل 10 و در شــکل 11) نيز مقايسه بين منحنی های سردشدن محاسبه شد و اندازه گيری شده ارايه گرديده است.
در شــکل 12a توزيع محاسبه شده منيزيم در گوشــه فنجان آناليز حرارتی نشان داده شده و در آن مشاهده میشود تهی شدن از منيزيم در لبه خارجی مدل مجازی شــبکهای به وجود آمده است.
با در نظر گرفتن 0/015 درصد منيزيم به عنوان مقدار بحرانی برای تهی شدن منيزيم (خطچين) ضخامت پيشبينی شده برای لايه گرافيت تغيير شــکل يافته بســته به موقعيت در محدود 250 تا 300 ميکرون اســت كه اين مقدار همان محدوده اندازه گيری ضخامت اثرپوســتی در شکل 12b میباشــد.
بدين ترتيب نظريه اكسيداسيون منيزيم برای تغيير شکل گرافيت در لايه پوستهای تاييد میگردد. پيشبينی وضعيت توزيع منيزيم نشــان میدهد در ناحيه نزديک گوشــه تهی شدن از منيزيم اندكی كمتر است، كه اين امر به دليل واگرا بودن جريان حــرارت و كوتاهتر بودن زمان انجماد میباشــد.
زمــان كوتاه تر انجماد زمان كمتــری را برای نفوذ منيزيم فراهم میكند البته متاســفانه نمونه در گوشــه دارای شــعاع قوس بزرگی است و به همين خاطر اين اثر در نمونه واقعی قابل مشاهده نيست.
اثرات سنتیک انجماد
به جز اثرات تهی شــدن از منيزيم، به وجود آمدن اثرپوستی همچنين تحت تاثير اثرات سنتيک انجماد است. به همين دليل Mampaey و همکارانش وجود گرافيت نوع D را در پوســته قطعه چدن خاكستری كه حاوی گرافيت A گزارش نموده اند.
از آنجا كه در چدن خاكســتری هيچ منيزيمی وجود ندارد تشکيل اثرپوســتی بايد مرتبط به برخی آثار سينتيک انجماد مانند مادون تبريد بالاتر در فصل مشــترک قالب با قطعه داشته باشد. همچنين نقش اكسيژن را نيز میتوان در تبديل گرافيت نوع A به D در نظر گرفت.
در سيستم اســتاندارد دوتايی آهن- گرافيت برای چدن هيپويوتکتيک فاز اوليه آســتنيت () و برای چدن هايپريوتکتيک گرافيت (Gr) اســت. هر چند كه در چدن های با گرافيت فشــرده (CG) و نشــکن (DI) انجماد با آستنيت آغاز میگردد.
البته حتی برای چدن هــای هايپريوتکتيک نيز مقداری گرافيت اوليه تشکيل میشــود ولی تا احاطه گرافيت به وسيله آستنيت رخ ندهد، رشد چشمگيری اتفاق نمیافتد. اين پديده در قالب دياگرام نامتقارن فازی در شکل 13 قابل درک است.
دياگرام فازی نامتقارن هنگامی كه مادون تبريد و تفاوت ها در ســرعت های رشــد فازی چشمگير باشند رفتار انجماد را تشريح میكند. در شکل 13 مشاهده میگردد با افزايش مادون تبريد مناطق زوج (يوتکتيک) به ســمت راست كشيده میشــوند.
بدين ترتيب با افزايش مادون تبريد و يا كاهش كربن معادل مقدار فاز اوليه آستنيت افزايش میيابد. انجماد آستنيت اوليه در فصل مشــترک قالب/فلز میتواند يک علت عمده برای تشکيل اثرپوستی باشد.
همانطور كه در شکل 14 مشاهده میشود در مورد چدن نشکن، انجماد آستنيت در سطح قطعه ريختگی منيزيم را در فصل مشترک مذاب/جامد بيرون میزند و اين امر موجب ايجاد يک لايه تهی از منيزيم شده و در نتيجه باعث تغيير شکل گرافيت میگردد. عواملی كه بر مقدار آســتنيت در فصل مشترک موثر هستند عبارتند از:
- كربن معادل
- جوانه زايی
- هدايت حرارتی
تاثير كربن معادل
نتايج تحقيقات اخير نشــان میدهد كــه كربن معادل نقش مهمی بر ضخامت لايه تهی از گرافيت دارد. اين تحليل با شــرايط بدون پوشــان شروع می شــود. در يک مقدار مشخص مادون تبريد (در شــکل 13 با خط چين افقی) چدن هيپويوتکتيک با كربن پايين (نقطه A) دارای آســتنيت دندريتی بيشــتری نسبت به كربن معادل متوســط (نقطه B) است.
چدن هايپريوتکتيک (نقطه C) نيز همانطور كه در نمودار اســتاندارد دوتايی Fe-Gr پيشبينی شده انجمادش را با منجمد شــدن آستنيت و نه گرافيت اوليه شــروع میكند. در تحقيق حاضر مقادير كربن معادل 4/06 و 4/33 و 4/53 بوده اســت.
اندازه گيری های ضخامت اثرپوســتی در نمونه های صفحه ای (بدون پوشان) در پايين شکل 13 برای نشان دادن ارتباط بين كربن معادل، مقدار آستنيت اوليه و ضخامت اثرپوستی ارايه شده است.
در اين شکل مشاهده میشــود با افزايش كربن معادل و نزديک شدن به ناحيه زوج های يوتکتيک ضخامت اثرپوســتی كاهــش میيابد. اندازه گيری های ديگری بر روی نمونه پلکانی كه در شــکل 15 ارايه شــده ايــن نظريه را تاييد مینمايد.
نتايج مقطع 7 ميلیمتری به دليل به وجود آمدن ســمانتيت از شــکل حذف گرديده است. هنگامی كه از پوشان گرافيتی استفاده میشود كربن به طور موضعی با نفوذ از پوشان به چدن انتقال میيابد. افزايش موضعی كربن معادل، تركيب شيميايی شــکل 13 را به سمت راست (با نقاط سبز نشان داده شده) میكشد.
برای كربن معادله ای پايين و متوســط (نقاط A و B) موقعيت را به ناحيه زوج (يوتکتيک) نزديک شــده و در نتيجه اثرپوستی كمتر میگردد. اما در كربن معادل بالا (نقطه C) موقعيت ممکن اســت از ناحيه زوج (يوتکتيک) گذشته و دور شود كه موجب بزرگتر شدن اثرپوستی خواهد شد.
نتايج آزمايشات عمل برای گرافيت در شکل 15 اين مکانيزم را تاييد مینمايد. پوشان فروسيليسيم نيز بايد اندكی كربن معادل را افزايش دهد زيرا سيليسيم فقط معادل كربن در ميزان كربن معادل اثر میگذارد. البته فروسيليســيم دارای يک اثر قویتر جوانهزايی نسبت به گرافيت است كه اين موضوع در ادامه تشريح خواهد شد.
اثر جوانهزايی
پوشان فروسيليســيم به دليل اثر جوانهزايی مادون تبريد را كاهش میدهد و موقعيت ها در دياگرام فازی نامتقارن كه با مربع های زرد در شــکل 13 نشــان داده شده به ســمت بالا كشيده میشود. بدين ترتيب مقدار آستنيت اوليه مرتبط كمتر شــده و در نتيجه اثرپوستی نازکتر میگردد.
البته اين بهبود انتظار میرود برای چدن های با كربن معادل متوســط و بالا (نقاط C و B) اثربخش تر باشــد درحالیكه برای چدن با كربن معادل پايين (نقطه A ) تاثير بســيار اندک اســت.
اين فرضيه با نتايج ارايه شــده در شــکل 15 هماهنگ میباشد و ديده شده كه پوشان فروسيلســيم برای چدن با كربن معادل پايين نسبت به كربن معادل بالا اثربخشــی كمتری دارد. در شکل 16 ريزساختارهای چدنهای با گرافيت فشرده (CG) دارای ضخامــت 21 ميلیمتر با انواع پوشــان و كربن معادله ای مختلف نشان داده شده است.
اثر هدايت حرارتی
از بررسی دياگرام نامتقارن Fe-Gr در شکل 13 می توان پيشبينی نمود كه مادون تبريد بالاتر باعث میشود آستنيت بيشتری در ابتدای انجماد تشکيل شود و در نتيجه ضخامت اثرپوســتی بيشتر گردد.
بنابراين اين برآورد منطقی است كه پوشانه ای غيرفعال با هدايت حرارتی بالا موجب افزايش مادون تبريد در فصل مشترک قالب/فلز شده و منجر به ضخيمتر شدن اثرپوستی میشود. شــکل 17 اثر هدايت حرارتی بر ضخامت اثرپوســتی بــرای نمونه های بدون پوشان و دارای پوشانهايی غيرفعال را نشان میدهد.
افزايش ضخامت اثرپوســتی با هدايت حرارتــی بالاتر برای تمامی مقاديــر كربن معادل به جز يک مورد استثنا يعنی پوشــان ميکا در كربن معادل 53/4 درصد (نقطه سبز)، مشاهده میشود.
اثر زمان فرو بردن در پوشان زيركن نيز اين خط فکری را تاييد میكند و در مقاله قسمت اول نشان داده شد كه زمان طولانی تر غوطه وری در پوشان زيركن باعث افزايش ضخامت اثرپوستی میشود زيرا ضخيمتر شدن لايه پوشان و نفوذ عميق تر پوشان موجب افزايش هدايت میگردد.
مجددا دياگرام فازی نامتقارن میتواند برای تشــريح اثر استفاده گردد بدين ترتيب كه مادون تبريد نقاط بر روی دياگرام فازی را به سمت پايين میكشد (مثلث های آبی) و به دليلی به وجود آمدن فاز اوليه بيشتر لايه اثرپوستی ضخيمتر میگردد.
بر اســاس اين تجزيه و تحليل يک پوشــان قالب كه سرعت سرد شدن را كاهش دهد و در نتيجه مادون تبريد كاهش يابد، باعث نازک تر شــدن اثرپوستی میگردد. البته Kroker و Duncan اعلام نمودند كه سرعت پايينتر سرد شدن ناشی از مقاطع ضخيم قطعات ريختگی موجب افزايش اثرپوستی میگردد.
اين تناقض آشــکار میتواند با ارتباط اكسيداســيون منيزيم با مکانيزم تشکيل اثرپوستی توضيح داده شود زيرا با كاهش سرعت سرد شدن زمان انجماد افزايش می يابد كه اين امر همچنين زمان تماس منيزيم برای اكسيداســيون را افزايش خواهد داد.
خلاصه ای از مکانیزم های تشکیل اثرپوستی
در مقاله حاضر دو مکانيزم در حال رقابت برای تشکيل اثرپوستی و تغيير شکل گرافيت مطــرح گرديد كه عبارتند از لايه افزايش يافته آســتنيت (به دليل اثرات ســينتيک انجماد) و تهی شــدن از منيزيم (به دليل واكنش با اكسيژن يا گوگرد).
سينتيک انجماد بر تشکيل اثرپوستی از طريق مادون تبريد در فصل مشترک قالب/ فلز و اثرگذاری بر مقدار آستنيت اوليه موثر است. در واقع پوشانه ای قالب با سرعت هدايت حرارتی بالا موجب ضخيمتر شدن اثرپوستی میگردند. از سوی ديگر تهی شــدن از منيزيم در زمان های طولانی تر انجماد (قطعات بزرگ ريختگی) مکانيزم غالب خواهد گرديد و به درستی در قطعات ضخيم و سنگين اثرپوستی عميق تری مشــاهده شــده اســت.
به طور كلی مادون تبريد بالا كمک به تشکيل يک لايه ضخيمتر آستنيت اوليه كرده ولی اكسيد شدن منيزيم را برعکس كاهش میدهد. شکل 18 يک نمودار شــماتيک است كه تاثير تلفيقی دو مکانيزم برای قالب های بدون گوگرد (مانند قالب با چسب سيليکات سديم) را نشان میدهد.
در اين نمودار ديده میشود كه تشکيل اثرپوســتی با اكسيداسيون منيزيم در سرعت سرد شدن پايين و به وسيله تشکيل لايه آستنيت در فصل مشترک قالب/ فلز با سرعت سرد شدن بالا كنترل میشود. از آنجا كه مدل نفوذ دو بعدی كه قبلا ارايه شده بر مبنای اكسيد شــدن منيزيم است بدين ترتيب نمودار شکل 18 بايد فقط در سرعت سرد شدن پايين معتبر باشد.
نتیجه گیری
مقاله حاضر مکانيزم های تشــکيل علائم اثرپوســتی را بر مبنای يافته های تحقيقات قبلی و پيشــبرد يک نظريه پيچيده تر كه شــامل نه فقط واكنش های شــيميايی در فصل مشترک بلکه اثرات ســينتيک انجماد است، مرور مینمايد. مکانيزم های تشکيل اثرپوستی به صورت خلاصه بدين شرح هستند:
– زبری ســطح بستگی به دانه بندی ماســه و ارتفاع متالواستاتيکی بارريزی دارد. محاسبه رياضی اين پديده در مقاله قبلی كاملا تشريح گرديد.
– دكربوره شــدن در ســطح قطعات ريختگی به دليل به وجود آمدن پديده تهی شــدن از گرافيت و تشکيل هاله فريتی است. رطوبت و درجه حرارت بالاتر بارريزی دكربوره شدن را توســعه میدهد و از سويی ديگر كربوره شدن موجب تشکيل هاله پرليتی میگردد.
– تغيير شــکل گرافيت میتواند يا در اثر تهی شــدن لايه از منيزيم در اثر واكنش های شــيميايی با قالب و اتمسفر آن و يا در اثر افزايش مقدار آستنيت در لايه ســطحی توجيه شود. اين مکانيزم آخر را میتوان با استفاده از نمودار فازی غير متقارن Fe-Gr تشريح و درک نمود.
– مدل نفوذ دو بعدی قادر به پيشبينی ضخامت اثرپوستی بر مبنای اكسيد شدن منيزيم است.
شکل 19 به طور خلاصه مکانيزم های تشکيل اثرپوستی مطرح شده در مقاله حاضر را نشان میدهد.
منابع:
منبع خارجی: A.F.S. Trans. 2013
منبع فارسی: فروردین و اردیبهشت 1396 – مجله صنعت ریخته گری
ترجمه : محمدجواد توسلی کیلانی
1.Stefanescu, D.M., Wills, S., Massone, J., Duncan, F., “Quantifi- cation of Casting Skin in Ductile and Compacted Graphite Irons and Its Effect on Tensile Properties,” International J. of Metalcasting,
pp. 7-26 (Fall, 2008).
2.Schey J.A., Introduction to Manufacturing Processes, McGraw Hill, Boston, p.65 (2000).
3.Boonmee, S., Stefanescu, D.M., “Casting Skin of Compacted Graphite Iron Part II: Influence on Tensile Mechanical Proper- ties,” AFS Transactions, 118, pp. 217-224 (2010).
4.Labrecque, C., Gagne, M., Cabanne, P., Francois, C., Beret, C., Hoffmann, F., “Comparative Study of Fatigue Endurance Limit for 4 and 6 mm Thin Wall Ductile Iron Castings,” International Journal of Metalcasting, pp. 7-17 (Spring, 2008).
5.Starkey, M.S. Irving, P.E., “A Comparison of the Fatigue Strength of Machined and As-Cast Surfaces of SG Iron,” Interna- tional Journal of Fatigue, pp. 129-136 (July, 1982).
6.Boonmee, S., Gyesi, B., Stefanescu, D.M., “Casting Skin of Compacted Graphite Iron Part I: Evaluation and Mechanism for Formation,” Trans. AFS, 118, pp. 205-216 (2010).
7.Stefanescu, D.M., Giese, S.R., Piwonka, T.S., Lane, A., “Cast Iron Penetration in Sand Molds Part I: Physics of Penetration De- fects and Penetration Model,” Trans. AFS, pp. 1233-1248 (1996).
8.H. O. Reisener, H.O., “Some Aspects of the Formation and Structure of a Skin on Iron Castings and a Method Used to Obvi- ate Its Occurrence,” The British Foundryman, pp. 362-369 (Sep- tember, 1962).
9.Matijasevic, S., Gomez-Gallard, J., Wallace, J.F., “Ferritic Surface Layers on Gray Iron Castings,” Trans. AFS, pp. 571-592 (1974).
10.Narasimha Swamy, G.S., Wallace, J.F., “Factors Influencing the Ferrictic Layer on the Surface of Gray Iron Castings,”, Trans. AFS, pp. 531-550 (1975).
11.Rickards, P.J., “Suppression of Ferrite in Shell Molded Gray Iron Castings,” Trans. AFS, pp. 101-108 (1976).
12.Rickards, P.J., “The Formation and Avoidance of Graphite- Free Surfaces on Grey Iron Castings,” The British Foundryman,
pp. 53-60 (March, 1975).
13.Marti, F., Karsay, S.I., “Localized Flake Graphite Structure as a Result of a Reaction Between Molten Ductile Iron and Some Components of the Mold,” Trans. AFS 87, pp. 221-226 (1979).
14.Riposan, L., Chisamera, M., Stan, S., Skaland, T., “Surface Graphite Degeneration in Ductile Iron Castings for Resin Molds,” Tsinghua Science and Technology, 13, pp. 157-163 (April, 2008).
15.Xiaogan, H., “Nodular Iron Surface Deterioration Due to PTSA in Resin,” Trans. AFS, 100, pp. 9-15 (1992).
16.Voronova, N.A., Desulfurization of Hot Metal by Magnesium, The International Magnesium Association, Dayton (1983).
17.Boonmee, S., Stefanescu, D.M., “Casting Skin Management in Compacted Graphite Iron, Part I: Effect of Mold Coating and Section Thickness,” Trans. AFS, 121, paper 1391 (2013).
18.Tinebar, J.P., Wilson, S.J., “Nobake Chemical Binder Sys- tems: Their Effect on Microstructural and Physical Properties of Ductile Iron,” Trans. AFS, 101, pp. 169-174 (1993).
19.Goodrich, G.M., Lobenhofer, R.W., “Effect of Cooling Rate on Ductile Iron Mechanical Properties,” Trans. AFS, 110, pp. 1003-1032 (2002).
20.Boonmee, S., Moran, M.K., Stefanescu, D.M., “On the Effect of the Casting Skin on the Fatigue Properties on CG Iron,” Trans. AFS, 119, pp. 421-430 (2011).
21.Boonmee, S., Stefanescu, D.M., “On the Mechanism of Cast- ing Skin Formation in Compacted Graphite Iron,” International J. of Metalcasting, pp. 19-24 (Fall, 2009).
22.Duncan, F.C., Kroker, J., “A New Test Casting to Evaluate Skin Formation in CGI,” Trans. AFS, 119, paper 10-023 (2011).
23.Mampaey, F., Li, P.Y., Wettinck, E., “Variation ofGray Iron Strength along the Casting Diameter,” Trans. AFS, 101, paper 03- 056 (1993).
مقالات و اخبار