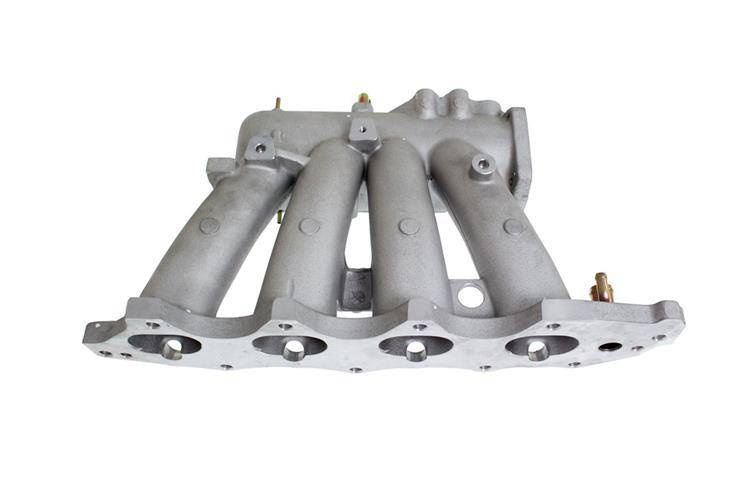
اثر تبلور فازهای حاوی آهن بر دوام اتصال دوفلزی بین رینگ داخلی و پیستون ریختگی
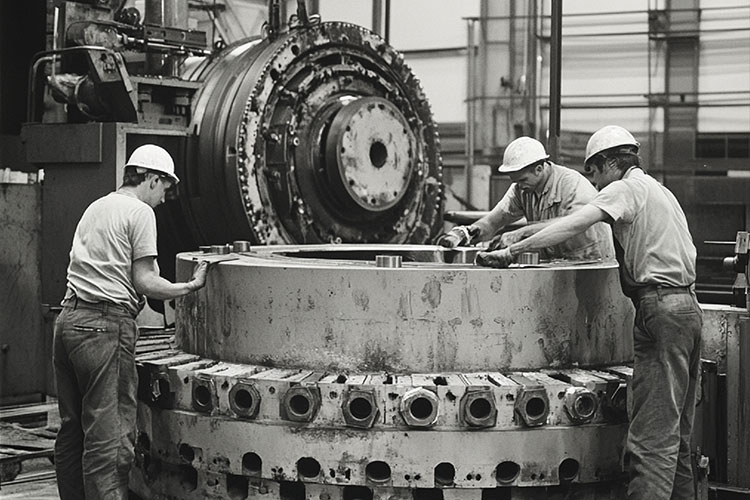
چکیده:
در مقاله حاضر مهمترین علل اتصال ناپایدار بین رینگ چدنی داخل پیستون با سیلومین ارائه شده است. نشان داده شده که عیوب تولید عمدتاً مرتبط با فرآیند آلفین کردن رینگ های چدنی در آلیاژ (AS9)Al-Si است. افزایش مقدار آهن بیشتر از حد مجاز در آلیاژ AS9 موجب تبلور فازهای شکننده β-Al5FeSi می گردد و این مورفولوژی ناخواسته با اندازه های بزرگ، علل عمده تضعیف اتصال بین رینگ های داخلی و پیستون و معیوب شدن محصولات تولیدی خواهد شد. تحقیق حاضر بر روی ۱۰ هزار پیستون در شرایط تولیدی انجام شده است.
داده های کنترل کیفی پارامترها و عوامل تولید وهمچنین ساختارهای میکروسکوپی و ماکروسکوپی رینگ های چدنی و ناحیه فصل مشترک بین رینگ ها و پیستون از آلیاژسیلومین مورد بررسی و آنالیز قرار گرفت و برای کاهش بروز عیوب ریختگی در اتصال رینگ و پیستون راه حلهای آلیاژی وفنی ارائه گردید. این موارد شامل معرفی اصلاح کننده های موفولوژیک و ساختاری فازهای β-Al5FeSi، کاهش ناخالصی های گازی در آلیاژ AS9 و بهینه سازی درجه حرارت آلیاژ آلفین نیزاست.
1-مقدمه
در صنعت خودرو الزامات برای کیفیت بالا، درجه بالای استاندارد شدن و در بیشتر موارد تولید در حجم های بزرگ وجود دارد.اجزای فلزی برای خودروها به سه روش ریخته گری، شکل دادن یا فرآیندهای هایبرید تولید می شوند (1).
روش ریخته گری یکی از ارزان ترین و بهره ورترین روش ها برای تولید قطعات خودرو بوده که دارای شرایط مورد تقاضا است. یک نمونه این قطعات پیستون موتورها احتراق داخلی از جنس سیلومین است. در قسمت بالای چنین پیستونی ناحیه رینگ بوده که در موتورهای ۲ زمانه دارای ۱ تا ۴ رینگ و در موتورهای ۴ زمانه رینگ ها ۲ تا ۴ عدد خواهند بود. تعداد رینگ ها عمدتاً متناسب با نسبت کمپرس و طراحی موتور است.
کارکرد این رینگ ها آبندی محفظه احتراق و تمیز کردن دیواره سیلندر از روغن اضافی می باشد. به این دلیل این رینگ ها اغلب از جنس چدن های نشکن یا چکش خوار (مالیبل) ساخته می شود ( ۳و ۲). برای تقویت و استحکام دهی ناحیه کاری و خارج کردن مؤثر حرارت از بالای پیستون، آنها در یک مغزی چدنی (حامل رینگ) که یک دندانه برای رینگ اصلی ایجاد شده، نصب می شوند. برای ایجاد یک اتصال با دوام بین چدن و آلیاژپیستون مغزی ها تحت فرآیندی به نام آلفین قرار می گیرند.در این فرآیند مغزی درون یک آلیاژ Al-Si که در جدول ۱ ترکیب آن ارائه شده (AS9) جهت تشکیل یک لایه نفوذی (۶ تا ۴) فرو برده میشوند.
پس از خنک شدن، مغزی ها (رینگ ها) درون قالب ریژه مستقر شده و سپس بارریزی با آلیاژ پیستون انجام می گردد. در گذشته طراحی پیستون با مغزی (رینگ)فقط برای موتورهای دیزل سنگین با فشارهای کمپرس ۵/ ۲تا ۵/ ۳ مگاپاسکال و برای موتورهای بنزینی با فشار کمپرس۱ تا ۵/ ۱ مگاپاسکال استفاده میشد. اما امروزه مغزی (رینگ)برای تمامی پیستون موتورها هم بنزینی و هم دیزلی شامل موتورهای کوچک و بزرگ به کار می رود.
2-مشکل تحقیق
آمار نهایی کنترل کیفی به دست آمده از شریک صنعتی این تحقیق یعنی شرکت Federal – Mogul Gorzyce sp.z.o.o نشان می دهد که علاوه بر خطای ماشینکاری، مهمترین علل برگشت پیستون ها عیوب ریختگی است (درصد تمامی عیوب حدود ۸درصد است).
با در نظر گرفتن محصولات شرکت که حدود ۲۶ میلیون پیستون در سال می باشد و متوسط عیوب که در حدود ۳درصد است، تعداد پیستو ن های برگشتی به دلیل عیوب حدود 4/62 هزار در سال خواهد بود.این مشکلات کیفی در انتهای فرآیند تولید و در جریان کنترل نهایی پیستو ن ها تشخیص داده می شود که موجب تلفات اضافی می گردد.
در تحقیق (۸) نشان داده شده که عیوب عمده ریخته گری مرتبط با حضور فازهای آهن (خصوصاً فازهای) β-Al5FeSi درفرآیند آلفین کردن و لایه های نفوذ کرده است. به لحاظ تردی و مورفولوژی نامطلوب، این فازها موجب تضعیف فصل مشترک پیستون و رینگ شده و باعث بالا رفتن ضایعات می گردد.
فازهای حاوی آهن هنگامی تشکیل می شود که میزان آهن در آلیاژ AS9 از حد مجاز تجاوز می کند، بنابراین مقدار آهن در آلیاژ آلفین یک عامل تعیین کننده برای اطمینان از قابلیت کارکرد سیستم پیستون – رینگ – سیلندر است. البته ضروری است که ارتباط بین عوامل فرآیندی آلفین و پایداری فرآیند تولید و همچنین کیفیت محصولات نهایی روشن و شفاف گردد.
حذف یا کاهش تبلورفاز های β-Al5FeSiاز طریق جلوگیری ازتجاوز مقدار آهن از حد مجاز در آلیاژ AS9 بوده که منجر به کاهش هزینه ها می گردد. نکته حائز توجه این که به لحاظ سیکل تولید و نیاز برای فواصل مناسب تولید بین ایستگاه های آلفین و کنترل کیفی نهایی، زمان برای افزایش مقدار آهن درآلیاژ AS9 می تواند طولانی شود.
این امر بدین معنی است که یک اپراتور بدون آگاهی از مشکلات، می تواند رینگ ها / پیستون هایی تولید کند که انطباق با استانداردهای کیفی برای سیکل های زیاد را ندارند. تشخیص اتصالات معیوب رینگ – پیستون در زمان تشکیل آنها می تواند موجب توقف در هزینه ها برای فرآیندهای بعدی تولید گردد. بدین ترتیب بار بر روی تجهیزات، انرژی و مصرف مواد در مراحل بعدی تولید (ماشینکاری و عملیات سطحی) کاهش یافته که در مورد محصولات معیوب غیرضروری است.
براساس اطلاعات فوق به نظر می رسد منطقی است علل تشکیل یک اتصال ناپایدار بین پیستون و رینگ به صورت مشروح تجزیه و تحلیل شود و همچنین راه حلی برای رفع این مشکل از طریق مراحل اصلاحی و پیشگیرانه ارائه گردد.
3-روش و متدولوژی تحقیق
3-1- هدف و دامنه تحقیق
هدف از تحقیق حاضر تجزیه و تحلیل عوامل و پارامترهای کلیدی کنترل کیفی فرآیند آلفین بر این اساس بوده تا علل بروز عیوب در فصل مشترک رینگ – پیستون مشخص گردد تعیین منابع این عیوب باعث مزایای اقتصادی ملموسی در قالب کاهش هزینه های تولید خواهد شد.
تولید پیستون موتورهای بنزینی با حجم ۱۴۰۰ سی سی (بیشترین سهم سفارشات) برای ارزیابی مسیر فرآیند آلفین رینگ ها، انتخاب شده تحقیق در یک خط ایزوله شده فرآیند آلفین در شرکت Federal-Mogul Gorzyce در یک حجم تولید ۱۰ هزار پیستون انجام گردید. چهارچوب و دامنه تحقیق شامل موارد زیر بود:
– تعیین سهم عیوب ریختگی که در فصل مشترک رینگ های چدنی با پیستون از آلیاژ سیلومین ظاهر می گردد.
– بررسی و تجزیه و تحلیل فرآیند آلفین
– تعیین دلایل بالقوه برای عدم چسبندگی – بین رینگ وپیستون
– پیشنهاد را ه حل های بالقوه برای رفع مشکل
2-3- سایت آزمایش
فرآیند آلفین مورد بررسی در یک ایستگاه نیمه اتوماتیک آلفین مطابق شکل ۱ انجام گردید. موضوع تحقیق عیوب ریختگی بوجود آمده در اتصال بین رینگ چدنی و پیستون ریختگی از آلیاژ AlSi11Cu4Ni3Mg مطابق شکل ۲ بوده است. این شکل همچنین ریزساختار صحیح اتصال رینگ – پیستون به همراه لایه قابل مشاهده بوجود آمده در اثر غوطه وری و نفوذ را نشان می دهد. تشخیص عیوب ریختگی در فصل مشترک و اتصال رینگ – پیستون با استفاده از روش های خط US Harrandt و نفوذ التراسونیک در کارخانه Federal – Mogul Gorzyce انجام شد.
علاوه بر این آزمایشات براساس استانداردهای کنترل کیفی شریک صنعتی، یک آنالیز کامل از داده های تولید صورت گرفت. عوامل و پارامترهای آلیاژها و مواد به کار رفته درتولید(آلیاژ چدن رینگ ها و آلیاژ آلومینیم AS9) همچنین فرآیند آلفین مورد بررسی قرار گرفت. سپس داده های به دست آمده با نتایج آزمایشات ریزساختار انجام شده به وسیله میکروسکوپ نوری Me F-2Reichert مجهز به یک اسپکترومتر EDS Voyager Noran X-ray مقایسه گردید.
4-نتایج
۱- ۴- آزمایشات کنترل کیفی
اولین مرحله تحقیق براساس داده های آماری از بخش کنترل کیفیت شرکت Federal-Mogul Gorzyce ، یک دسته بندی درمورد علل اصلی اتصال غیرصحیح (به حالت بروز شکست)رینگ به بدنه پیستون مطابق شکل ۳ است.
براساس دستورالعمل های شرکت Federal-Mogul و استانداردصنعتی TS1E-010-020 شرکت آلمانی( Tenneco Nurnberg)یک اتصال نفوذی بین یک رینگ چدنی و بدنه یک پیستون آلومینیمی از سیلومین به صورت دور تا دور، هنگامی کیفیت نامناسب دارد که حداقل یکی از شرایط زیر را دارا باشد:
– عدم چسبندگی در سطح بالایی (T) رینگ بیش از ۷ درصد
– عدم چسبندگی در سطح پایینی (B)بیش از ۷ درصد
– هم پوشانی عیوب (O) بیش از ۳ درصد
آزمایشات کنترل کیفی اتصال رینگ – پیستون به دور محور ۱۰۰درصد محصولات انجام می شود.
پیستون ها به وسیله التراسونیک بر روی تمامی محیط رینگ با چرخش پیستون به درو محور آن انجام می شود. قرار گرفتن پیستون ها از بالا به پایین (تاج پیستون رو به پایین) بوده وآزمایش چسبندگی بر روی قسمت سطوح بالایی (T)و پایینی (B) رینگ ها مطابق شکل ۴ انجام می گردد.
هنگامی که یک عیبی تشخیص داده شد، خط التراسونیک Harrandt موقعیت عیب را که سطح بالا یا پایین بوده، به همراه درصد عیب و نوع آن (ریختگی یا مکانیکی) مطابق شکل ۵ نشان می دهد.
در شکل 5a عیب به وجود آمده در سطح بالایی رینگ را که حدود ۳۹ / ۱۰ درصد محیط پیستون است مشاهده می شود.
بنابراین این عیب یک عیب ریخته گری بوده و مطابق شکل ۳تا ۳۰ درصد محیط پیستون ادامه دارد. با توجه به قطر اسمی پیستون مورد بررسی که ۶۹ میلیمتر (محیط ۲۱۷ میلیمتر )است لذا عیب در حدود ۵/ ۲۲ میلیمتر از پیرامون پیستون به وجود آمده است (شکل 5a)
به همین روش تشخیص تمامی عیوب در فصل مشترک بین رینگ و پیستون (در تحقیق فعلی) انجام شد و ۲۴ پیستون از بین کل پیستون های مورد بررسی یعنی ۱۰ هزار عدد با دارا بودن یک اشکال کیفی در اتصال نفوذی بین رینگ چدنی و پیستون آلومینومی به عنوان پیستون های معیوب جدا شدند.
4-2 آنالیز داده های تولید و آزمایشات میکروسکوپی
برای تعیین علل بالقوه این پدیده ناخواسته، براساس متدولوژی به کار گرفته در تحقیق عوامل و پارامترهای آلیاژ AS9(جدول ۱)، رینگ های چدن پر نیکل آستنیتی (جدول ۲) و فرآیند آلفین (جدول ۳) مورد بررسی و تجزیه و تحلیل قرار گرفت.
براساس بررسی داده های آماری بخش کنترل کیفی کارخانه Federal – Mogul Gorzyce مهمترین عوامل و پارامترهای در مورد آلیاژ9 AS برای فرآیند آلفین کردن رینگ ها عبارتند از:
– تجاوز مقدار آهن در مقادیر بیشتر از ۳۵ / ۰ درصد (شکل ۶)
– تجاوز مقدار نیکل بیش از ۵/ ۰ درصد وزنی
– افزودن گازها به آلیاژ AS9 که عمدتاً موجب تشکیل هیدرات
افزایش مقدار آهن در آلیاژ و به دنبال آن تشکیل فازهای βمی تواند اتصال دو فلزی را ضعیف کرده همچنین موجب عدم اتصال کامل بین رینگ چدنی و پیستون می گردد.مکانیزم برای پدیده دوم دوگانه است زیرا رسوبات فاز ورق های β-Al5FeSi با طولی حدود بیش از ۵۰۰ میکرون می تواند جریان مذاب رسانی )تغذیه( را محدود کرده و موجب بروز تخلخل های انقباضی نیز گردد (شکل ۸) (۸).
وجه دوم این که بر روی رسوبات حاوی آهن، لایه های اکسید نشسته پر کردن آلیاژ آلومینیم در ناحیه اطراف رینگ را مانع می شوند و باعث تشکیل عیوبی مانند نیامد کردن می شوند.
از سویی دیگر حضور اکسیدها در آلیاژ آلفین می تواند باعث جوانه زنی ناهمگن ترکیبات بین فلزی غنی از آهن شود. این اکسیدها به عنوان محل هایی برای جوانه زنی فازهای اولیه عمل می کنند. محققین مقالات ۱۱ تا ۹ به طور خاص نشان داده اند که فیلم های دوتایی اکسید در آلیاژهای آلومینیم محل های بالقوه جوانی زنی هستند، زیرا سطح خارجی آنها انرژی مناسبی برای تشکیل فازهای آهن دارند. آنالیز و بررسی داده های ارائه شده در جدول ۲ امکان این نتیجه گیری را فراهم می کند که مهمترین عوامل و پارامترهای چدن برای تولید رینگ عبارتند از:
– ترکیب شیمیایی ناهماهنگ و ریزساختار نامناسب از نظر اندازه
– ایجاد درج های مناسبی از زبری بر روی سطح رینگ ها پس ازشات پلاست کردن (شکل ۱۰) نکته قابل ذکر این که رینگ ها به وسیله یک فرآیند فنی جداگانهای )ریخته گری گریز ازمرکز(تولید می شوند و رینگ ها به صورت یک لوله طویل ریخته گری شده سپس به اندازه رینگ ها سربریده می شوند. سپس رینگ برای حذف آثار ماشینکاری تحت شات بلاست قرارمی گیرند (شکل 10a) البته برای اطمینان از تماس و چسبندگی مناسب آلیاژ آلفین ضروری است سطح رینگ ها زبری لازم راداشته باشند (شکل 10b)
با بررسی پارامترها و عوامل ارائه شده در جدول ۳ و همچنین فرآیند الفین مهمترین مواردی که بر کیفیت اتصال رینگ وپیستون مؤثر است بدین شرح هستند:
– درجه حرارت آلیاژ AS9 در کوره پیش گرم
– ضخامت لایه ها نفوذی و غوطه وری
– زمان فرآیند آلفین
– اطمینان از تمیزی سطحی رینگ ها (شکل ۱۱)
– کنترل مستمر افزایش مقدار آهن در آلیاژ AS9
– حذف احتمال افتادن رینگ در آلیاژ AS9
– اطمینان از کنترل فرآیند و قابلیت تکرارپذیری آن
آنالیز و بررسی فرآیند آلفین تحت شرایط صنعتی این امکان را فراهم نمود تا علل افزایش مقدار آهن در آلیاژ AS9تعیین گردد. علاوه بر فرآیند فرو بردن رینگ در مذاب آلومینیم، افزایش مقدار آهن تحت تأثیر ابزارهای فولادی به کار رفته و عوامل انسانی نیز قرار می گیرد.
به عنوان مثال افتادن اتفاقی رینگ ها در حمام مذاب آلفین که در آن دیگر نمی توان آن را از کوره خارج نمود و بدین ترتیب موجب افزایش تدریجی مقدارآهن خواهد شد. باید توجه داشت که عامل اصلی مؤثر برمیزان نفوذ آهن در فرآیند آلفین درجه حرارت آلیاژ AS9وزمان انجام فرآیند است.(12)
5 – نتیجه گیری و چشم انداز
سهم عیوب ریختگی در سطح تماس بین رینگ های چدنی و پیستون آلومینیمی نشان می دهد که مشکل اتصال صحیح بین این دو هم از جهت فرآیند و هم از نقطه نظر اقتصادی اهمیت دارد. آنالیز و بررسی داده های تولید نشان می دهد که علل عمده عیوب عبارتند از مواد، فرآیند و تکنولوژی و مشکلات ناشی از خطای انسانی در جریان فرآیند آلفین (فرو بردن رینگ ها در آلیاژ آلفین).
بدین ترتیب پس از گذشت زمانی مقدار آهن آلیاژ AS9افزایش می یابد و پس از تجاوز از حدمجاز ضروری است آلیاژ مذکور تعویض گردد. آلیاژ استفاده شده ( AS9 + Fe ) به عنوان ضایعات با قیمتی ارزا ن تر از مواد اولیه فروخته خواهد شد. با توجه به تداوم تولید و ابعاد آن،برآورد می شود که شرکت Federal – Mogul Gorzyce در هر ماه ۶۰۰ تن آلیاژ AS9مصرف می کند که اهمیت تحقیق انجام شده در این خصوص را نشان می دهد.
براساس داده های تولید و بررسی های انجام شده مشخص گردید که از نقطه نظر مواد آلیاژی، دلیل عمده برای عیوب ریختگی به وجود آمده تجاوز مقدار آهن از ۳۵ / ۰ درصد در آلیاژ AS9است. در مقادیر در حدود ۳۵ / ۰ درصد آهن هیچ عیب ریختگی در فصل مشترک رینگ و پیستون مشاهده نگردید.
از سوی دیگر از نقطه نظر تکنولوژی فرآیند آلفین رعایت موارد زیر ضروری است:
– توجه ویژه به کاهش امکان ورود ناخالصی های گازی به آلیاژ AS9 ، که موجب تخلخل در فصل مشترک بین رینگ و پیستون می گردد.
– انجام تحقیق بر روی بهینه کردن درجه حرارت آلیاژ AS9 درکروه پیش گرم در جهت کاهش مقدار آن
-5-1 مسیر و جهت تغییرات آلیاژ
براساس تحقیقات ( ۱۳ و ۸ و ۶ و ۴) فازهای بین فلزی نوع AlXFeYSiZ با نسبت های استوکیومتری متفاوت عمدتاً عامل دوام اتصال بین رینگ و پیستون هستند. موفولوژی این ترکیبات ناشی از شرایط تبلور، انجماد و مقدار آهن است. بیشتر این فازها در شرایط بار ریزی، به صورت ورق های منجمد می شوند (در زیر میکروسکوپ به صورت سوزنی دیده می شوند)و با لبه های تیز موجب بروز ترک های میکروسکوپی و تمرکز تنش و ضعف و بی دوامی لایه نفوذی می گردند.
در آلیاژهای Al-Siسرعت شده با سرعت آرام (حدود 1°C در ثانیه) با مقدار آهن بیش از ۴/ ۰ درصد در کنار موارد دیگر رسوبات ناخواسته فاز β-Al5FeSiبه دلیل چسبندگی پایین با ساختار زمینه و اندازه بزرگ، تردی آلیاژ را افزایش می دهند. مشاهده ریزساختارهای آلیاژ AS9خصوصاً با بیش از ۴/ ۰ درصدآهن نشان می دهد که رسوبات فازهای طویل β-Fe حاوی ترک های مرکزی و لبه ای، عمدتاً طولی و یا عرضی هستند.
این ترک ها اغلب همراه با تخلخل انقباضی تا ۷۰ درصد بوده که خصوصیات انعطاف پذیری آلیاژ AS9را کاهش بیشتری میدهد .داده های مقالات( ۱۶ تا ۱۴ ) نشان می دهد یک راه خوب برای کاهش اثر منفی فازهای آهن در آلیاژهای Al-Si روش هایی است که در آن اصلاح کننده هایی برای تغییر مورفولوژی فازهای β-Fe به مذاب اضافه می شود. مانند افزودن Mn ،Mo ، Cr و Co که در ترکیب با آهن فازهایی با لبه های گرد، شکل های کروی و اندازه های کوچکتر به وجود می آورند. یک نمونه از این فازها با نقطه ذوب بالا عبارتند از: Al12CrMn(آلیاژ های Al-Si-Cr) و Al6FeMn یا Al15(Fe,Mn)3Si2 (در آلیاژهای Al-Si-Fe-Mn)
بنابراین تحقیقات بیشتر باید در جهت انتخاب اثربخش ترین افزودنی آلیاژی، تعیین مقدار آن در ارتباط با آهن و توسعه فن آوری برای افزودن به آلیاژ AS9 تحت شرایط صنعتی انجام شود. البته مطالعات در این زمینه هم اکنون در حال انجام است.
2 – 5 مسیرهای ارتقای فرآیند
روش دیگر برای کاهش عیوب ریختگی در فصل مشترک پیستون و رینگ طراحی یک فرآیند تکنولوژیک و کنترل کیفی مناسب است. در این خصوص موارد کلیدی محدود کردن ورود ناخالصی های گازی (اکسیدها، هیدرات ها) به آلیاژ AS9 بوده که موجب تخلخل در لایه های به وجود آمده در اثر نفوذ و غوطه وری در مذاب می گردد. در بررسی شرایط تولید در کارخانه Federal – Mogul Gorzyce راه حل هایی بدین شرح پیشنهاد گردید:
– استفاده از پوشش برای کوره در جریان فرآیند آلفین برای کاهش نفوذ آخال های گازی درون آلیاژ AS9
– انجام تصفیه میانی در جریان فرآیند آلفین
– بهینه کردن درجه حرارت آلیاژ AS9 در کوره پیش گرم
نکته جالب توجه خصوصاً از نظر اقتصادی پایین آوردن درجه حرارت آلیاژ AS9کند کردن نفوذ آهن و در نتیجه طولانی شدن زمان کاری آلیاژ AS9 از نظر افزایش مقدار آهن است. مطالعات اولیه نشان می دهد که کاهش درجه حرارت آلیاژ AS9 امکان پذیر بوده و موجب دستیابی به اهداف دلخواه بدون افزایش درصد ریختگی می گردد. تحقیق در این مورد نیز در حال انجام است.
منبع فارسی: ماهنامه مهر 1402 – صنعت ریخته گری
ترجمه: عبدالحمید قدیمی
منبع خارجی: 2/2023 Issue Engineering Foundry of Archives
منابع:
[1] Szucki, M., Dziubinska, A., Winiarski, G., Majerski, K.,
Drozdowski, K., Górny, M. & Buras, J. (2020). Application of
2XXX and 7XXX series alloys as input material for the new
casting-forging hybrid process. Indian Journal of Engineering
and Materials Sciences. 27(3), 795-801. DOI: 10.56042/
ijems.v27i3.45099.
[2] Kammer, C. (2011). Aluminium Handbook. Vol. 1: Fundamentals
and Materials. Beuth Verlag GmbH.
[3] Rowe, J. (2021). Advanced Materials in Automotive Engineering.
Woodhead Publishing.
[4] Pietrowski, S. & Szymczak, T. (2004). Structure of the
connection of alfin layer coating with the Al-Si cast alloy.
Archives of Foundry. 4(14), 393-404. (in Polish).
[5] Pietrowski, S. & Szymczak, T. (2006). The influence
of selected technological elements on the structure of the
alfinizing coat on iron alloys. Archives of Foundry. 6(19),
251-266. (in Polish). PL ISSN 1642-5308.
118 A R C H I V E S o f F O U N D R Y E N G I N E E R I N
G V o l u m e 2 3 , I s s u e 2 / 2 0 2 3 , 1 1 2 – 1 1 8
[6] Pietrowski, S. (2004). Structure of alfinizing layer on the
gray cast iron. Archives of Foundry. 4(11), 95-104. (in Polish).
PL ISSN 1642-5308.
[7] Crolla, D.A. (2009). Automotive Engineering. Powertrain,
Chassis System and Vehicle Body. Butterworth-Heinemann.
[8] Piątkowski, J. & Czerepak, M. (2020). The crystallization
of the AlSi9 alloy designed for the alfin processing of ring
supports in engine piston. Archives of Foundry Engineering.
20(2), 65-70. DOI: 10.24425/afe.2020.131304.
[9] Schoß, J.P., Schramm, E., Schönherr, P., Mrowka, N.,
Schumann, H., Becker, H., Keßler, A., Szucki, M. & Wolf, G.
(2023). Investigation of the formation of iron-rich intermetallic
phases in Al-Si alloys via thermal analysis cooling curves, including
a real-time detection for filtration process. Advanced
Engineering Materials. 2201576, 1-20. DOI: 10.1002/
adem.202201576.
[10] Cao, X. & Campbell, J. (2004). The solidification characteristics
of Fe-rich intermetallics in Al-11.5Si-0.4Mg cast
alloys. Metallurgical and Materials Transactions. A 35, 1425-
- DOI: 10.1007/s11661-004-0251-0.
[11] Campbell, J. (2006). Entrainment defects. Materials
Science and Technology. 22(2), 127-145. DOI:
10.1179/174328406X74248.
[12] Bas, E.N. Alper, S., Tuncay, T., Dispinar, D. & Kirtay,
- (2022). Influence of Melt Quality on the Formation of Fe
Intermetallic in A360 Alloy. Archives of Foundry Engineering.
22(3), 53-59. DOI: 10.24425/afe.2022.140236.
[13] Pietrowski, S., Klimek, L. & Szymczak, T. (2006),
Diffraction research of the alfininizing coat on iron alloys.
Archives of Foundry. 6(22), 392-404. (in Polish). PL ISSN
1642-5308.
[14] Mahta, M., Emamy, M., Daman, A., Keyvani A. &
Campbell J. (2005) Precipitation of Fe rich intermetallics
in Cr- and Co-modified A413 alloy. International
Journal of Cast Metals Research. 18(2), 73-79. DOI:
10.1179/136404605225022928.
[15] Baldan, R., Malavazi, J. & Couto, A.A. (2017) Microstructure
and mechanical behavior of Al9Si0.8Fe alloy with
different Mn contents. Materials Science and Technology.
33(10), 1192-1199, DOI: 10.1080/02670836.2016.1271966.
[16] Shabestari, S.G. (2004) The effect of iron and manganese
on the formation of intermetallic compounds in aluminum–
silicon alloys. Materials Science and Engineering: A.
383(2), 289-298. DOI: 10.1016/j.msea.2004.06.022
مقالات و اخبار
یک نظر در “اثر تبلور فازهای حاوی آهن بر دوام اتصال دوفلزی بین رینگ داخلی و پیستون ریختگی”
به نظرم این مطلب خیلی کاربردیه، مخصوصاً برای کسایی که توی صنایع فلزی کار میکنن. کاش یه جدول مقایسهای از تأثیر انواع فازهای آهنی روی استحکام اتصال هم میذاشتید.