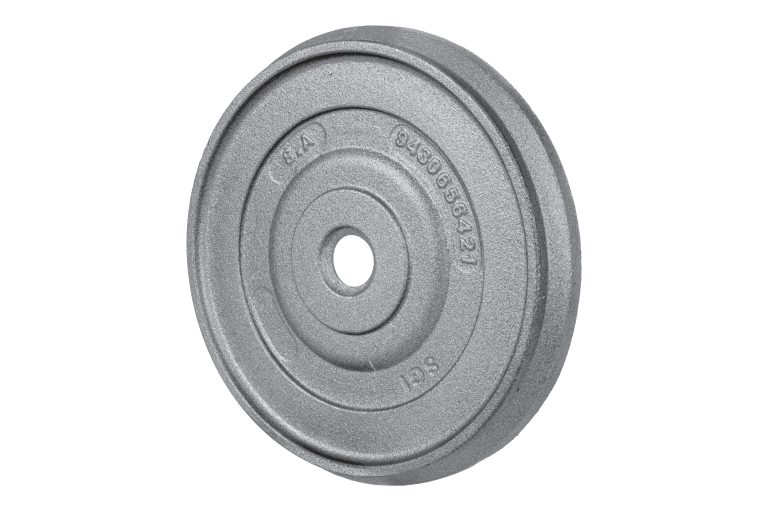
خانه » مقالات » تأثیر درجه حرارت آستنیته کردن بر تحولات ریز ساختار، خصوصیات مکانیکی نوع شکست و مکانیزم فرسایش فولاد منگنزی هدفیلد
تأثیر درجه حرارت آستنیته کردن بر تحولات ریز ساختار، خصوصیات مکانیکی نوع شکست و مکانیزم فرسایش فولاد منگنزی هدفیلد
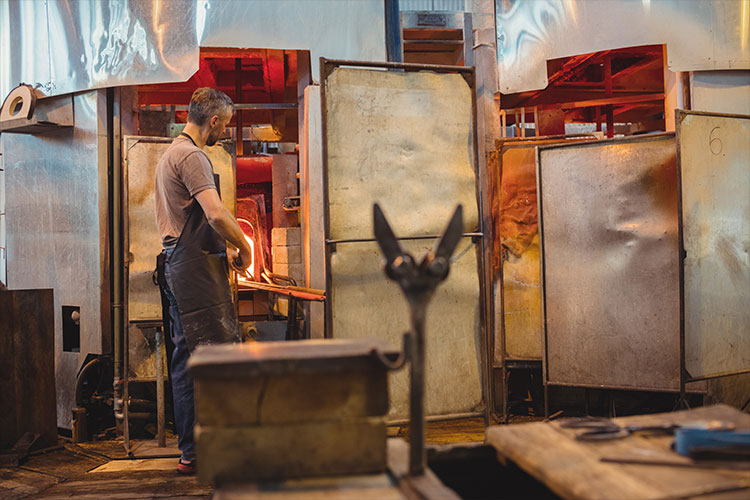
چکیده:
در مقاله حاضر اثر درجه حرارت آستنیته شدن بر تحولات ریزساختاری، خصوصیات مکانیکی، شکل شکست و مکانیزم فرسایش یک فولاد هدفیلد پرکربن بررسی شده است. چهار نمونه بلوکی از فولاد هدفیلد پس از ذوب در کوره القایی ریخته گری و سپس یک ساعت در درجه حرارت های 1000، 1075، 1150 و 1225 درجه سانتی گراد آستنیته و سپس در آب کوئنچ گردید.
آزمایش کشش هم محور، آزمون فرسایش پین بر روی دیسک و سختی سنجی بر روی نمونه ها انجام شد و جهت مطالعه تغییرات ریزساختاری از یک میکروسکوپ نوری، یک الکترون میکروسکوپ روبشی با زمینه روشن استفاده گردید. جهت مشاهده کاربیدهای شکل گرفته نیز الکترون میکروسکوپ به کار گرفته شد. همچنین نوع شکست به وسیله الکترون میکروسکوپ روبشی بررسی گردید و نتایج نشان داد که افزایش درجه حرارت آستنیته کردن، کاربیدها را کاهش داده ولی اندازه دانه های آستنیت را افزایش می دهد.
خصوصیات مکانیکی نیز با بالارفتن درجه حرارت آستنیته کردن مانند استحکام تسلیم، کشش، سختی و مقاومت به فرسایش افزایش یافت البته این افزایش در برابر کاهش انعطاف پذیری ایجاد شده لیکن نتایج شکست انگاری نشان دهنده شکست بسیار نرم بود به طوری که سهم شکست نرم با کاهش درجه حرارت آستنیته کردن از 1225 به 1000 درجه سانتی گراد کاهش یافت.
1-مقدمه
رابرت هدفیلد در سال 1882 اولین فولاد هدفیلد را با 2/ 1 درصد کربن و 12 درصد منگنز ابداع نمود. فولاد هدفیلد غیرمغناطیسی بوده و معمولاً حاوی 1 تا 4/ 1 درصد کربن، 10 تا 14 درصد منگنز و یک قابلیت سختی پذیری خوب است. این فولاد به طور گسترده در صنایعی مانند سیمان، معدن، ساختمان و ریلی به دلیل استحکام بالا، شکل پذیری خوب و مقاومت به فرسایش عالی به کار می رود.
در این نوع فولادها عناصر آلیاژی عموماً متناسب با کاربرد افزوده می شود. به عنوان مثال تیتانیم برای ریز کردن دانه بندی و افزایش استحکام (2 و 1) اضافه می شود البته افزودن تیتانیم با تشکیل کاربیدهای پایدار (4 و 3) موجب افزایش سختی و ارتقای مقاومت به فرسایش می شود لیکن تشکیل TiC باعث افت شکل پذیری فولاد می گردد Srivastava (5) و همکارانش گزارش نموده اند (6) مقاومت به فرسایش فولادهای هدفیلد اساساً با یک کمپوزیتی به صورت زمینه فولاد و تقویت آن توسط ذرات TiC افزایش می یابد. همچنین Srivastava و همکارانش (7) در خصوص اثر TiC بر رفتار خوردگی کمپوزیت ها با فولاد هدفیلد به عنوان ساختار زمین های تحقیق نمودند و نشان دادند که مقاومت به خوردگی چنین کمپوزیتی با افزایش مقدار ذرات TiC کاهش می یابد.
Zakharava و همکارانش (8) بر روی تأثیر آلومینیم در تغییرات ریزساختار فولادهای هدفیلد تحقیق نمودند و دریافتند که اضافه کردن آلومینیوم به ترکیب شیمیایی می تواند تعداد کاربیدها در مرز دانه ها را کاهش دهد و مورفولوژی کاربیدها را از پیوسته به صورت ناپیوسته درآورد.
در کنار این تحقیقات بررسی ها نشان داد که افزایش آلومینیم در فولادهای هدفیلد باعث زیاد شدن نیروی محرکه استحاله آستنیت به مارتنزیت شده و هم زمان درجه حرارت آغاز تشکیل مارتنزیت (Ms) را نیز کاهش میدهد (9) به دلیل میزان کربن و منگنز بالا در فولادهای هدفیلد، ساختار ریختگی متشکل از دانه آستنیت و کاربیدهایی در مرز دانه ها است و چنین ساختاری شکننده و اغلب غیرقابل استفاده می باشد. برای مقابله با این مشکل Hossein و همکارانی (10 و11) گزارش نمودند که بوسیله کوئنچ کردن سریع فولاد هدفیلد پس از عملیات آستنیته کردن در یک حمام نمک می توان از تشکیل کاربیدها در مرز دانه ها جلوگیری نمود.
از آنجا که به دلیل مقاومت به فرسایش عالی یکی از کاربردهای فولادهای هدفیلد اجرای سیستم های حفاری است خصوصیات فرسایشی این فولادها مهم می باشد. در این خصوص Moghadam و همکارانش اعلام نمودند افزودن وانادیم به فولاد هدفیلد به لحاظ تشکیل ذرات VC موجب مقاومت به فرسایش می شود. همچنین در تحقیقات مختلف (15 تا 12) خصوصیات فولادهای هدفیلد با آلیاژهای Fe – Cr مقایسه گردیده که نتایج آنها نشان داد فولادهای هدفیلد عموماً سختی پائینی دارند.
به علاوه Azadi و همکارانش بر روی اثر یک عملیات انحلالی دوتایی بر خصوصیات فولاد هدفیلد مطالعه نمودند و نشان دادند که یک فرآیند آنیل دو پل های می تواند انحلال رسوبات در فاز آستنیت را بهتر انجام دهد ، هرچند که با این فرآیند آنیل دو مرحله ای سختی فولاد کاهش یافته بود. استفاده از محیط های متفاوت کوئنچ نشان داد که با افزایش سرعت کوئنچ اندازه دانه های آستنیت با تلفیقی از آب و یخ کاهش می یابد.
به دلیل خصوصیات استثنایی فولادهای منگنزی هدفیلد در حال حاضر یکی از آلیاژهای حساس مهندسی است. قابلیت کارپذیری گرم با چقرمگی خوب یکی از خصوصیات ویژه ای می باشد که موجب مناسب بودن و جاذبه آن در شرایط تنش بالا است. ساختار ریختگی این فولاد شامل کاربیدهای کمپلکس Fe- Mn- C بوده که می تواند با انجام عملیات حرارتی صحیح با وجود یک ساختار آستنیتی کامل استفاده شود. خصوصیت چقرمگی این فولاد پرآلیاژ نتیجه انجام یک عملیات مناسب است (10 تا 12).
بدین ترتیب درجه حرارت انحلال باید به اندازه کافی بالا باشد تا کاربیدها در آستنیت حل گردد و یک کوئنچ کردن سریع یک ساختار تک فازی برای دستیابی به یک زمینه فوق اشباع مورد نیاز است. البته پس از عملیات حرارتی یک ساختار کاملاً آستنیتی قابل دسترس نیست و خصوصاً در قطعات ضخیم برخی کاربیدها نیز می تواند در مرز دانه ها یافت شود. برای انحلال کامل کاربیدها درجه حرارت و زمان نگهداری عملیات انحلال تعیین کننده است.
به علاوه جهت جلوگیری از ترک های داخلی گرم کردن باید به آرامی انجام شود. سرعت کوئنچ کردن نیز باید به اندازه کافی سریع باشد تا مقدار کاربیدها به حداقل برسد. عوامل و پارامترهای متعددی شامل درجه حرارت آستنیته کردن و سرعت کوئنچ بر عملیات حرارتی فولاد هدفیلد مؤثر است (13 تا 15) هدف اولیه تحقیق حاضر تعیین اثر درجه حرارت آستنیته کردن در کاهش مقدار کاربیدها و اندازه دانه آستنیت می باشد.
در گذشته تحقیقات فقط متمرکز بر اثر عملیات حرارتی بر ریزساختار یا خصوصیات مکانیکی فولاد هدفیلد بوده که این موضوع در مقاله مرجع 10 گزارش شده است. البته تاکنون این حقیقت گزارش نگردیده که فولاد هدفیلد به عنوان یک قطعه راهبردی و استراتژیک تحت فرسایش و ضربه به طور همزمان به کار گرفته شده است. به عبارتی یک تلفیق مناسب از استحکام، سختی و مقاومت به ضربه و فرسایش در فولاد هدفیلد مورد نیاز می باشد و این امر فقط از طریق عملیات آستنیته کردن و یا افزودن عناصر مختلف آلیاژی به ترکیب شیمیایی فولاد امکان پذیر است (11).
از آنجا که امکان کنترل خصوصیات فو ق الذکر با کنترل دقیق ریز ساختار میسر می باشد این موضوع در فرآیند آستنیته کردن در نظر گرفته می شود. همچنین به دلیل کاربرد فولادهای هدفیلد در بسیاری از کاربردهای مهم مانند تاش حفاری، صنایع ریلی و خردکننده های صنعتی، تعویض آنها در حین کار پرهزینه خواهد بود. در تحقیقات گذشته بیشتر تأثیر درجه حرارت آستنیته کردن بر خصوصیات کششی فولادهای هدفیلد مشخص شده است.
اما خصوصیات فرسایشی این فولادها خصوصاً ارتباط آن با خصوصیات کششی بیشترین اهمیت را دارد. از آنجا که تلفیق تحولات ریزساختاری، خصوصیات مکانیکی و مقاومت به فرسایش در تحقیقات گذشته گزارش نگردیده تمرکز اولیه در تحقیق حاضر بر این موضوع قرار گرفت. بنابراین در این مطالعه هدف تضمین اثر درجه حرارت آستنیته کردن بر خصوصیات مکانیکی، تحولات ساختاری و مقاومت به فرسایش فولاد هدفیلد جهت پیشنهاد یک پنجره واحد فرآیندی انتخاب گردید.
2- روش آزمایش مواد
1-2-آلیاژ فرآیند ریخته گری و عملیات حرارتی فولاد Fe- Mn مورد استفاده در تحقیق حاضر از یکی از فولادهای آستنیتی هدفیلد مطابق استاندارد ASTM-A 128 انتخاب (17) و بوسیله کوره القایی 4 نمونه بلوکی شکل ذوب و ریخته گری شد که ترکیب شیمیایی نمونه های تهیه شده نیز به وسیله یک اسپکترومتر نشر نوری ساخت آلمان تعیین گردید ابعاد بلو ک های ریخته گری Cm 30 × 15 × 5 بوده و ترکیب شیمیایی آنها هم در جدول 1 ارائه شده است. پس از ریخته گری یکی از نمونه ها در درجه حرار ت های 1000 ، 1075 ، 1150 و 1225 به مدت1 ساعت آستنیته شده و در آب به سرعت کوئنچ گردید.
2-2- مطالعه ریزساختاری
برای تهیه نمونه های متالوگرافی از یک دستگاه میکروکاتر مدل MC25 مجهز به خنک کننده آب و صابون استفاده شد. نمونه ها به ابعاد mm 10 × 20 × 8 از قطعات آستنیته شده بریده شد. به روش تر از کاغذ سمباده ای با زبری 60 تا 1500 برای پرداخت نمونه های قالبگیری شده استفاده گردید و پولیش نهایی نیز با محلول حاوی ذرات آلومینا به قطر 2/ 0 میکرون انجام شد. در انتها نمونه ها با محلول 2 درصد نایتال اچ گردیدند.
از میکروسکوپ نوری شرکت Olympus برای بررسی تغییرات ریزساختاری و آنالیز تصویری جهت اندازه گیری اندازه دانه های آستنیت و نرم افزار Image J جهت تعیین مقدار کاربیدها استفاده شد. به منظور تعیین اندازه دانه های آستنیت با آنالیز تصویری روش تقاطع خطی به کار گرفته شد. برای مطالعه رسوبات شکل گرفته در مرز دانه های آستنیت از یک الکترون میکروسکوپ با زمینه روشن (FE – SEM) مدل 3 MIR A ساخت شرکت TESCAN مجهز به سیستم نشر انرژی اشعه X (EDS) با قدرت تفکیک 5/ 1 نانومتر تحت ولتاژ 15 کیلو ولت استفاده گردید اشعه EDS با قدرت تفکیک 500 نانومتر تا 1 میکرون و قدرت نفوذ و پهنای اشعه X 2 و 1 میکرون بوده است.
برای مطالعه با میکروسکوپ الکترونی عبوری (TEM) فویل های نازک به قطر 3 میلی متر با ضخامت 100 میکرون ابتدا به وسیله پولیش با کاغذ سمباد ه های بسیار نرم تهیه شد. سپس این فویل ها با پولیش جت الکترولیتی در pct15 اسید پر کلریک در اسید استیک بادمای (15-)آماده گردیدند. نمونه ها از ناحیه نزدیک سطح برداشته شده بودند. برای TEM از سیستم FEI- Tecnai G2F20 با ولتاژ kV 200 استفاده شد.
-2-3 اندازه خصوصیات مکانیکی
اندازه گیری سختی بر روی 4 نمونه بوسیله یک دستگاه انیورسال مطابق استاندارد ASTM E 92 انجام شد (18) جهت تعیین نوسانات سختی از یک میکروسختی سنج TECH- FUTURE ویکرز مدل 800 FM-ساخت ژاپن با اعمال بار 100 نیوتن برای مدت 25 ثانیه استفاده گردید. در هر موقعیت مختلف 5 اندازه گیری انجام و مقادیر میانگین ثبت شد. پس از آستنیته کردن نمونه های کشش مطابق استاندارد ASTM (19) – E8 ماشین کاری شدند. نمونه های آزمایش مقاومت به ضربه چارپی هم براساس استاندارد ASTM – A 370 تهیه و مورد آزمایش قرار گرفتند (20).
در شکل 1 ابعاد نمونه های آماده شده برای آزمایش کشش ارائه شده که از وسط بلو ک های ریختگی برداشته شد ه اند. از یک دستگاه کشش SANTAM مدل AST-400 یک محوره با سرعت کرنش 2- 10 بر ثانیه در درجه حرارت محیط (اتاق) استفاده شد. نکته قابل توجه این که در آزمایش کشش از انداز ه گیری تغییر طول استفاده نگردید و منحنی های تنش – کرنش از حد الاستیک در نظر گرفته شد Lindroos. و همکارانش (14) برای فولادهای هدفیلد سرعت های کرنش 1- 10 و 3- 10 بر ثانیه را پیشنهاد کردهاند.
بنابراین در تحقیق حاضر از سرعت کرنش اولیه اسمی 2- 10 بر ثانیه استفاده شد. نکته مهم این که جهت اطمینان از دقت، آزمایشات کشش 3 بار تکرار شد و نتایج به همراه انحراف استاندارد معیار گزارش گردید. برای مطالعه نوع شکست فولاد هدفیلد، سطوح شکست تمامی 4 نمونه پس از آزمون کشش به وسیله الکترون میکروسکوپ (SEM) مورد مطالعه قرار گرفت. آزمایش مقاومت به ضربه چارپی نیز با استفاده از یک دستگاه SANTAM با توان 200 J انجام شد.
4-2- آزمایش مقاومت به فرسایش
آزمایش فرسایش پین بر روی دیسک در درجه حرارت محیط (اتاق) بدون روانکار با نیروی عمودی اعمال شده 35 نیوتن و سرعت خطی 45 / 0 متر بر ثانیه انجام شد. پین به شکل استوانه ای از فولاد بلبرینگ با قطر 100 میلیمتر و طول4 سانتیمتر و سختی 70 راکول C بوده و جرم از دست رفته دیسک پس از مسافت های 500 ، 1000 ، 1500 و 200 متر با دقت0/1 میلی گرم اندازه گیری شد.
3- نتایج
-3 -1 مشاهدات میکروسکوپی
شکل 2 تصاویر میکروسکوپ نوری از فولاد هدفیلد با درجه حرارت های مختلف آستنیته شدن را نشان می دهد. در این تصویر می توان مشاهده نمود ریزساختار در شرایط مختلف آستنیته شدن متشکل از زمینه آستنیت و مقادیر متفاوت از کاربیدهای پیوسته خصوصاً در مرز دانه ها است. از تصاویر ریزساختاری قابل تشخیص است که مقدار کاربیدها با افزایش درجه حرارت آستنیته کردن به سرعت کاهش می یابد.
آنالیز تصویری نشان داده که اندازه دانه در درجه حرارت آستنیته کردن 1000درجه سانتی گراد(حد پائین) از 6 ± 2/83 میکرون پس از افزایش درجه حرارت به 1225 درجه سانتی گراد به 9 ± 8/ 239 میکرون رسیده است و در درجه حرارت آستنیته 1150 معادل 5 ± 184 میکرون بوده است. فاز غالب در ریزساختار در این فولاد آستنیت می باشد و متناسب با مقدار کربن و عناصر کاربیدزا موجود در ترکیب شیمیایی مقادیر متفاوتی نیز کاربید در فاز زمینه به وجود می آید (10 تا 12). البته عناصر کاربیدزا مانند Mn و Fe در ترکیب شیمیایی این فولاد وجود دارد که به همراه کربن می توانند به میزان زیادی امکان تشکیل کاربید را در ریزساختار افزایش دهند.
این موضوع به روشنی در نتایج EDS (شکل 3) نشان داده شده، در واقع در شکل 3 کاربیدهای مرزدانه با بزرگ نمایی بالا به همراه نتایج EDS گزارش شده است. شکل 3 تصویر TEM برای نمونه آستنیته شده در 1000درجه سانتی گراد و سپس کوئنچ شده همچنین یک مقدار اندکی رسوبات در زمینه آستنیت را نشان می دهد. الکترون میکروسکوپ FE- SEM مجهز به EDS برای ارزیابی بیشتر نتایج و درک بهتر ترکیبات استیومتریک بوجود آمده در زمینه فولاد هدفیلد استفاده شده است (شکل های b 3 و c 3) و شکل d 3 نیز نتایج این آنالیز را نشان می دهد.
در نتایج FE- SEM و EDS مشاهده می شود که کاربیدهای شکل گرفته در فولاد پرکربن آستنیته شده به صورت ترکیبات کاربید و یک کمپلکسی از Fe- Me- C است. کاربیدها آنالیز شده به وسیله EDS از نوع هستند و تشکیل این نوع کاربیدها در این فولاد در تحقیق Azadi و همکارانش (16) نیز گزارش گردیده است.
برای ارزیابی بهتر مقدار کاربیدها در درجه حرارت های مختلف آستنیته کردن از نرم افزار Image J در آنالیز تصویری استفاده شد. در شکل 4 نتایج اندازه گیری درصد حجمی کاربیدها به وسیله نرم افزار Image J مشاهده می شود که بنابر نتایج ارائه شده افزایش درجه حرارت آستنیته کردن منجر به کمتر شدن مقدار رسوبات در ریز ساختار فولاد هدفیلد می گردد به طوری که در 1000 و 1225 درجه سانتی گراد به ترتیب بالاترین و کمترین مقادیر کاربید وجود داشته است.
2-3- آزمایش کشش
شکل 5 و جدول 2 نتایج آزمایش کشش برای هر 4 نمونه را نشان می دهد. بنابر این نتایج نمونه آستنیته شده در 1000 درجه سانتی گراد استحکام نهایی و تسلیم پائین تر ولی انعطا ف پذیری بیشتر نسبت به نمونه آستنیته شده در 1225درجه سانتی گراد است. بدون تردید تغییر منحنی های تنش – کرنش به دلیل تغییرات ریزساختاری است که در اثر تغییر درجه حرارت آستنیته کردن بوجود آمده است.
بنابراین منحنی تنش – کرنش با بالارفتن درجه حرارت آستنیته کردن استحکام های تسلیم و نهایی کشش با شیب تندی افزایش یافته لیکن در مقابل ازدیاد طول نسبی فولاد آستنیتی هدفیلد کاهش می یابد. این امر به دلیل افزایش انداز ه های آستنیت و انحلال کاربیدها در درجه حرارت بالاتر آستنیته کردن است. در واقع با افزایش اندازه دانه های
آستنیت پلاستیسیته فولاد منگنزی هدفیلد به طور قابل توجهی کاهش می یابد (9 تا 12).
3- آزمایشات سختی و مقاومت به ضربه
شکل 6 نتایج آزمایش مقاومت به ضربه چارپی را برای 4 نمونه نشان می دهد که در آن نمونه آستنیته شده در1000 درجه سانتی گراد نسبت به نمونه آستنیته شده در 1225 درجه سانتی گراد انرژی شکست بیشتری را جذب کرده است. در شکل 7 نیز نتایج سختی اندازه گیری شده 4 نمونه ارائه شده که در آن نمونه آستنیته شده در 1000 درجه سانتی گراد نسبت به نمونه آستنیته شده در 1225 درجه سانتی گراد دارای سختی پائین تری است . با بالا رفتن درجه حرارت آستنیته کردن انحلال کربن در فاز آستنیت و به دنبال آن انداز ه های آستنیت افزایش می یابد افزایش اندازه دانه های آستنیت همچنین منجر به کاهش انرژی شکست یا چقرمگی فولاد منگنزی هدفیلد می گردد (5 تا 8).
3 -4- آزمایش فرسایش
شکل 8 نتایج آزمایشات مقاومت به فرسایش برای 4 نمونه آستنیته شده در درجه حرار ت های مختلف را نشان می دهد. بنابر نتایج می توان مشاهده نمود نمونه آستنیته شده در 1000درجه سانتی گراد نسبت به نمونه آستنیته شده در 1225 درجه سانتی گراد مقاومت به فرسایش کمتری داشته است. در شکل 9 تغییرات ضریب اصطکاک با طول فرسایش برای نمونه های فولاد هدفیلد که در درجه حرارت های مختلف آستنیته شده اند ارائه گردیده است.
دراین آزمایش بار اعمالی 35 نیوتن و سرعت دورانی دیسک 45 / 0 متر بر ثانیه و مسافت فرسایش نیز 2000 متر بوده است. مقایسه تغییرات ضریب اصطکاک برای فولاد هدفیلد در شرایط مختلف عملیات حرارتی) با توجه به داد ه ها در شکل 8) نشان می دهد فولاد آستنیته شده در 1225درجه سانتی گراد از آنجا که دارای بالاترین مقاومت به فرسایش است (براساس داده های شکل های 8 و 9) دارای پائین ترین ضریب اصطکاک می باشد.
تصاویر SEM از سطوح فرسایش یافته پس از مسافت 500 متر در آزمایش مقاومت به فرسایش در شکل 10 ارائه شده است. با توجه به خراش های به وجود آمده در سطح نمونه ها می توان نتیجه گیری کرد که مکانیزم غالب، فرسایش سایشی است که به دلیل سایش، براده ها از سطح جدا شده است.
به طور کلی میزان فرسایش سطح متناسب با ضریب اصطکاک و نرخ از دست دادن جرم می باشد. بنابر این با بالارفتن درجه حرارت آستنیته کردن میزان فرسایش سطحی به طور چشمگیری کاهش می یابد که به معنی مقاومت بیشتر در مقابل فرسایش است. آنالیز EDS بر روی سطح فرسایش یافته در نمونه آستنیته شده در 1225 درجه سانتی گراد و ذرات جدا شده در اثر فرسایش از روی سطح این نمونه انجام شده و نتایج ترکیب شیمیایی ذرات در شکل 11 ارائه گردیده است. اما نتایج EDS از سطح فرسایش یافته نشان داد که هیچ مکانیزم تریبولوژیک در جریان آزمایش مقاومت به فرسایش بوجود نیامده است.
-5 -3 بررسی نوع شکست
آنالیز SEM بر روی سطوح شکست نمونه های کشش انجام شد و در شکل 12 تصاویر شکست نگاری این موارد مشاهده می شود. بنابر تصاویر با مشاهده فرورفتگی ها(دیمپل) برروی سطوح کلیه نمونه های عملیات حرارتی شده می توان نتیجه گیری نمود همه نمونه ها دارای شکست نرم(انعطاف پذیر) هستند. علت این امر وجود فاز پایدار آستنیت به عنوان فاز غالب در ریزساختار فولاد هدفیلد می باشد (45 و 43) که این موضوع به وضوع در تصاویر متالوگرافی مشاهده می شود. هنگامی که یک آلیاژ دارای فاز آستنیت وارد ناحیه تغییر شکل پلاستیک غیریکنواخت می شود تعداد زیادی حفره و فرورفتگی (دیمپل) بر روی سطوح شکست بوجود می آید.
-4 سگالش
براساس شکل 2 ریزساختار فولاد هدفیلد متشکل از فاز آستنیت و مقادیر مختلفی فازهای کاربیدی است. حضور کاربیدها به دلیل مقدار بالای کربن و عناصر کاربیدزا مانند Mn و Fe می باشد. زمینه آستنیتی نیز به لحاظ حضور مقادیر زیاد C و Mn است. Lee و (Choi 21) گزارش نمودند Ms با افزایش مقدار Mn در آلیاژهای Fe – Mn به صورت اساسی کاهش می یابد به طوری که در آلیاژهای با Mn بالا می تواند یک ساختار کاملاً آستنیتی به وجود آید.
در شکل 2 قابل مشاهده است که با بالا رفتن درجه حرارت آستنیته کردن اندازه دانه های آستنیت درشت شده ولی مقدار کاربیدها کاهش می یابد این امر به دلیل درجه حرارت بالای آستنیته کردن است که موجب انحلال کاربیدها و افزایش اندازه دانه آستنیت می گردد(10و11) در واقع با افزایش درجه حرارت آستنیته کردن از1000 به 1225 درجه سانتی گراد مقدار کاربیدها کاهش یافته و اندازه دانه آستنیت افزایش می یابد.
در 1225 درجه سانتی گراد حرارت به میزان کافی بالاست تا همه کاربیدهایی که در مرحله ریخته گری تشکیل شده اند حل شود. در همان زمان به دلیل مقدار کمتر کاربیدها که می توانند حرکت در مرز دانه ها را قفل کنند اندازه دانه ها افزایش می یابد (5, 3, 2). بدین ترتیب با افزایش درجه حرارت آستنیته کردن یک اثر سینرژیک از افزایش قابلیت حرکت دانه ها و کاهش کاربیدها منجر به درشت تر شدن دانه های آستنیت می گردد.
رشد دانه های آستنیت و حرکت مرزدانه های آستنیت در جریان فرآیند عملیات حرارتی باعث تشکیل یک ساختار با دانه بندی درشت و به دنبال آن خصوصیات مکانیکی پائین تر می شود. بنابراین کنترل رشد دانه های آستنیت در جریان عملیات حرارتی برای ظریف کردن دانه های آستنیت اقدام متالوژیکی مهم جهت دستیابی به خصوصیات مکانیکی مناسب در فولادهای هدفیلد است.
درجه حرارت و زمان آستنیته کردن و همچنین مقدار عناصر کاربیدزا در ترکیب شیمیایی از عوامل و پارامترهای اصلی مؤثر بر اندازه دانه آستنیت در فولاد است (7 تا 9). معمولاً در فولاد هدفیلد نرخ رشد دانه و حرکت مرزدانه های آستنیت به دلیل کاهش کشش اتم هایی محلول به صورت ترکیبات کاربیدی کاهش می یابد. حضور عناصر آلیاژی منجر به تشکیل ذرات کاربید مانند (کاربید Mn و یا کاربیدهای کمپلکس) ذرات نتیرور یا ترکیبات سولفور مانند سولفور منگنز می گردد.
همچنین رشد دانه های آستنیت و حرکت مرز دانه های آستنیت به دلیل طبیعت قفل کنندگی این ذرات به تأخیر می افتد. در نتیجه الگوی رشد دانه و حرکت مرزدانه های آستنیت از حالت غیریکنواخت به حالت یکنواخت تغییر می کند. توزیع این ذرات می تواند در درجه حرارت پائین آستنیته شدن در حالی که هیچ رشد دانه ای به وجود نیامده، بسیار مؤثر باشد. ذرات کاربید با افزایش درجه حرارت آستنیته کردن حل می شوند که این امر باعث رشد سریع دانه های آستنیت و همچنین غیریکنواختی در ساختار دانه خواهد شد.
ذرات بسیار ریز کاربید به صورت مانعی برای رشد دانه های آستنیت در فولاد هدفیلد عمل می کنند (11 و 10) و کنترل رشد دانه های آستنیت در جریان فرآیند عملیات حرارتی نیز بستگی به نوع و مقدار عناصر کاربیدزا مانند Fe ، Mn و C دارد. حضور هم زمان این عناصر به همراه شرایط آستنیته کردن بر رشد دانه ها و شکل مرزدانه های آستنیت مؤثر است، در تصاویر میکروسکوپ نوری شکل 2 در درجه حرار ت های پائین آستنیته کردن مرزدانه قفل شده و هیچ فرصتی برای حرکت مرزدانه ها و تغییر شکل آنها وجود ندارد که این امر به دلیل حضور مقدار زیادی ذرات کاربید در ریزساختار است.
در چنین شرایطی، مرزدانه ها بیشتر به شکل خطوط صاف می باشد. البته با افزایش درجه حرارت آستنیته کردن انحلال ذرات کاربید بیشتر می شود که این پدیده موانع رشد را حذف کرده و باعث موجی شدن مرزدانه ها خواهد گردید. به عبارتی دیگر می توان گفت که مسیرهای آزاد بالاتری برای مرزدانه های آستنیت در محدوده درجه حرارت آستنیته کردن 1225 تا 1150 درجه سانتی گراد به لحاظ انحلال ذرات کاربید وجود دارد که منجر به موجی شدن این مرزدانه می گردد.
همانطور که در قبل گفته شد یک آنالیز تصویری در میکروسکوپ نوری برای اندازه گیری متوسط اندازه دانه های آستنیت انجام گردید و نتایج نشان داد که با بالا رفتن درجه حرارت آستنیته کردن، اندازه دانه از 6 ± 2/ 83 میکرون در درجه حرارت آستنیته 1000 درجه سانتی گراد به 9 ± 8/ 239 میکرون در 1225درجه سانتی گراد می رسد. به طور کلی نتایج میکروسکوپ نوری نیز همان الگو را نشان داد.
همانطور که در بخش قبلی اشاره شد نتایج آزمایش کشش در شکل 5 و جدول 2 ارائه شده است. مقدار پایین تر کاربید در ریزساختار به معنی انحلال بیشتر در زمینه آستنیت می باشد. این کربن اضافی در آستنیت به شکل اتم های بین نشینی حل شده است. از آنجا که با بالارفتن درجه حرارت قابلیت انحلال کربن در آستنیت افزایش می یابد این امر منجر میزان بیشتری محلول بین نشینی شده و در نتیجه استحکام کشش و تسلیم بالا می رود.
همچنین می توان مشاهده نمود نتایج آزمایش کشش در جدول 2 که با افزایش درجه حرارت آستنیته کردن ازدیاد طول نسبی فولاد هدفیلد به طور اساسی کاهش می یابد. به طور کلی محلول جامد بر استحکام تسلیم فولادها مؤثر است. همچنین نشان داده شد که اتم های بین نشین دارای اثر استحکام دهی در مقیاس سه برابر مدول برش است (22). در حالی که اتم های جانشین دارای اثر استحکام دهی با درجه 0/1 برابر مدول برش می باشند.
همچنین مرزدانه ها مکان هایی با انرژی بالا هستند که رشد ترک را محدود می کنند. بدین ترتیب افزایش درجه حرارت آستنیته کردن منجر به درشت شدن اندازه دانه و کمتر شدن مرزدانه شده در نتیجه چقرمگی، انعطاف پذیری و قابلیت تغییر شکل نمونه های آستنیته شده در درجه حرارت بالاتر، پائین تر خواهد بود (26 تا 23). این موضوع دلیل اصلی برای افزایش استحکا م ها و کاهش چقرمگی و انعطاف پذیری فولاد هدفیلد هنگام افزایش درجه حرارت آستنیته شده از 1000 به 1225درجه سانتی گراد است.
شکل های 6 و 7 همچنین نتایج آزمایش مقاومت ضربه چارپی و اندازه گیری سختی را نشان می دهند. همانطور که می توان مشاهده نمود با افزایش درجه حرارت آستنیته کردن میزان سختی و انرژی ضربه فولاد هدفیلد به ترتیب افزایش و کاهش می یابد. این امر می تواند در اثر رشد دانه در درجات حرارت آستنیته کردن بالاتر باشد که در ریزساختارها نیز مشاهده می شود و بدین ترتیب دانه های درشت تر باعث کمتر شدن مقدار قفل کنندگی نابجایی ها خواهد شد (23 تا 26).
بنابراین نتیجه گیری می شود با بالا رفتن درجه حرارت آستنیته کردن اندازه دانه آستنیت افزایش یافته و انرژی ضربه کاهش می یابد. همانگونه که در شکل 5 مشاهده می شود افزایش درجه حرارت آستنیته کردن باعث ازدیاد استحکام تسلیم گردیده و با در نظر گرفتن ارتباط مستقیم استحکام تسلیم و سختی (24 تا 27) در شکل 7 می توان مشاهده نمود که سختی فولاد هدفیلد با افزایش درجه حرارت آستنیته کردن بالا رفته است.
در شکل7 همچنین ملاحظه می شود که نمونه های آستنیته شده در1000 و 1225درجه سانتی گراد به ترتیب دارای کمترین و بیشترین سختی در بین نمونه ها هستند. بنابر شکل 8 نتایج جرم از دست رفته در آزمایش مقاومت به فرسایش نشان می دهد که یک افزایش در درجه حرارت در جریان عملیات آستنیته کردن باعث کاهش در میزان جرم از دست رفته فولاد هدفیلد گردیده است. آزمایشات کشش و سختی سنجی نیز نشان داد که نمونه آستنیته شده در 1000درجه سانتی گراد نسبت به 1225 درجه سانتی گراد دارای استحکام تسلیم و سختی پائین تر می باشد.
بنابراین نمونه آستنیته شده در 1225 درجه سانتی گراد به دلیل استحکام تسلیم و سختی بالاتر مقاومت به فرسایش و در نتیجه مقاومت به تغییر شکل پلاستیک بالاتری دارد. همچنین بنابر نتایج شکل 8 مقدار جرم از دست رفته در آغاز آزمایش فرسایش در طول 500 تا 1000 متر برای 4 نمونه بالا بود لیکن در پایان آزمایش و مسافت 1500 تا 2000 متر این کاهش در وزن کمتر شده است که این امر به دلیل بروز کارسختی در فولاد هدفیلد بوده است.
در واقع فرساش سایشی در ابتدای آزمایش مکانیزم غالب بوده و با طولانی تر شده مسافت، تغییر پلاستیک بر روی سطوح نمونه بوجود آمده و منجر به کارسختی سطحی و ارتقای مقاومت به فرسایش گردیده است. بدین ترتیب جرم از دست رفته در فولاد هدفیلد در انتهای آزمایش روند کاهشی داشته است (26 تا 30). عموماً رفتار فرسایشی و ضریب اصطکاک تحت تأثیر ریز ساختار و شرایط سطحی فولاد می باشد.
در تحقیق حاضر هر جایی استحکام تسلیم و سختی به دلیل افزایش نیروی برشی کاهش یافته، از دست دادن جرم در اثر سایش نیز کاهش یافته است. در واقع هنگامی که استحکام تسلیم و سختی پائین هستند، محصولات فرسایش با یک مقدار تغییر شکل بسیار بالا به دلیل اعمال یک مقدار نیروی برشی اساسی، از روی سطح فولاد جدا می شوند، البته با افزایش استحکام تسلیم و سختی تغییر شکل سطح فولاد پائین تر است.
در نتیجه لایه های کمتری از روی سطح جدا شده و بدین لحاظ ضریب اصطحکاک بین عامل سایشی و سطح نمونه فولادی کاهش می یابد. در شکل 9 ضریب اصطکاک برای 4 نمونه آستنیته شده گزارش شده که در آن به وضوح مشخص است که نمونه آستنیته شده در 1225 درجه سانتی گراد نسبت به سایر نمونه ها دارای یک ضریب اصطکاک بسیار پائی نتر می باشد. این پائین ترین ضریب اصطکاک به دلیل دارا بودن بالاترین سختی و استحکام تسلیم تحت موقعیت اشاره شده در قبل است.
از سویی دیگر از آنجا که فولاد هدفیلد آستنیته شده در 1000 درجه سانتی گراد یک ضریب اصطکاک بالاتری را داشته و در نتیجه مقاومت فرسایش پائین تر، سختی و استحکام تسلیم آن نیز پائین می باشد. بنابر نتایج نمونه های فولاد هدفیلد آستنیته شده در 1150 و 1075 درجه سانتی گراد بین دو شرایط توضیح داده شده خواهند بود. اثر سختی و استحکام تسلیم بر مقاومت به فرسایش و ضریب اصطکاک در مقالات35 تا 31 به خوبی تشریح شده اند.
سختی پایین تر زمینه، باعث احتمال بیشتر برای تماس بین ذرات ساینده و سطح آلیاژ بوده و این ذرات می تواند خراش های بیشتر و عمیق تری ایجاد کنند، در نتیجه سختی پائین تر به معنی جرم بیشتر از دست رفته در آزمایش فرسایش است. در شکل 10 سطوح فرسایش یافته در آزمایش مقاومت به فرسایش با تصاویر SEM نشان داده شده که در آنها ملاحظه می شود مکانیزم غالب در فرسایش فولاد هدفیلد سایش و خراش است.
نکته حائز توجه اینکه سختی ذرات آلومینا در بین فرسایش دهنده بیش از 1400 ویکرز بوده که به طور چشمگیری از سختی فولاد هدفیلد یعنی 150 تا 350 ویکرز بیشتر است در این شرایط ذرات ساینده م یتواند در سطح فولاد نفوذ کند و به وسیله ایجاد خراش موجب کنده شدن براده ها از روی سطح گردند. عمق نفوذ ذرات ساینده بستگی به سختی و استحکام تسلیم ساختار زمینه دارد (36 تا 38).
در فولاد هدفیلد آستنیته شده در 1225 ذرات ساینده دارای قابلیت نفوذ کمتری بوده در نتیجه عمق خراش شیارها کمتر است. از سویی دیگر مقدار نیروی اعمال شده نیز به اندازه کافی برای فعال شدن مکانیزم کارسختی در فولاد هدفیلد بالا نیست. مشاهدات سطوح فرسایش یافته تائید می کند به لحاظ فرسایش درجه حرارت بالاتر آستنیته کردن موجب آسیب و فرسایش کمتر می گردد.
همچنین از نتایج ارائه شده در شکل های 8 و 9 و تصاویر SEM در شکل 10 می توان مشاهده نمود به دلیل سختی و استحکام تسلیم بالاتر فولاد، عمق و تعداد شیارهای فرسایش، کاهش یافته است. به تعبیری با افزایش سختی استحکام تسلیم ساختار زمینه (آستنیت) در فولاد هدفیلد حاوی منگنز بروز تغییر شکل پلاستیک اولیه و نفوذ ذرات سخت ساینده به سطح سخت تر خواهد بود. بدین ترتیب مقاومت به فرسایش در مراحل اولیه که سختی سطح بسیار بالاست افزایش یافته است.
همچنین لازم به یادآوری است که با افزایش مسافت فرسایش (بیشتر از 1500 متر) یافته جرم از دست رفته به دلیل تغییر شکل پلاستیک و کارسختی سطحی به مقدار ثابتی می رسد. تصاویر SEM از سطوح شکست پس از آزمایش کشش در شکل12 ارائه شده و در آنها مشخص است که مکانیزم اولیه شکست گسیختگی نرم (انعطا ف پذیر) است.
این نوع شکست همراه با تشکیل فرورفتگی ها (دیمپل) بر روی سطوح شکست است و علت این امر نیز حضور غالب فاز آستنیت در ساختار زمینه تمامی تمامی نمونه می باشد. از آنجا که آستنیت یک فاز نرم است، مکانیزم شکست نرم در جریان آزمایش کشش آلیاژهای نرم جوانه زنی، رشد و بهم چسبیدن خطرات و فرورفتگی هاست. این نوع شکست همچنین با عنوان قیف و مخروط (Cup & Cone) نیز نامیده می شود که مهم ترین مکانیزم شکست برای آلیاژهای نرم می باشد (40 و 39).
در شکل 9 می توان مشاهده نمود که سطح شکست نمونه آستنیته شده در 1000درجه سانتی گراد نسبت به نمونه آستنیته شده در 1225 درجه سانتی گراد دارای فرو رفتگی های بیشتری است. این امر نشان می دهد که شکست در نمونه فولاد هدفیلد آستنیته شده در1000 درجه سانتی گراد نسبت به سایر موارد نرم تر می باشد. با کاهش اندازه دانه به طور قابل ملاحظ های چقرمگی آلیاژها بالا می رود (43 تا 41) و می توان نتیجه گیری نمود که نمونه آستنیته شده در 1000 به دلیل دارا بودن دانه های کوچکتر و فرورفتگی های بیشتر در سطح شکست، نرم تر و انعطا ف پذیرتر می باشد.
به طور کلی ملاحظات سطح شکست فولاد هدفیلد پس از آزمایش کشش نشان داد که کاهش درجه حرارت آستنیته کردن از 1225 به 1000 درجه سانتی گراد منجر به شکست نرم تر گردیده است. تصاویر SEM نیز به خوبی با نتایج آزمایشات مکانیکی که در بخش قبل ارائه شد و همچنین نتایج تحقیق Sabzi و همکارانش (44) انطباق دارد. شکست نگاری نمونه ها پس از آزمایش کشش نشان داد فرورفتگی های میکروسکوپی ثانویه در بین فرورفتگی ها (دیمپل) وجود دارد که باعث تأخیر در شکست خواهند شد.
تشکیل این فرورفتگی های میکروسکوپی نتیجه واکنش مشترک و برخورد لایه های دوقلویی میکروسکوپی است. این موارد همچنین می تواند به دلیل تشکیل رسوبات نانو در جریان پیرسختی کرنشی دینامیک باشد (44). بنابر این هرگونه تغییر در شرایط فرآیند تولید می تواند بر خصوصیات (49 تا 45). ریزساختار و فاز تعادلی (53 تا 50) قطعات مؤثر باشد.
جمع بندی
از تحقیق حاضر به نتایجی بدین شرح می توان دست یافت؛
-5 -1 مشاهدات میکروسکوپی نشان داد که افزایش درجه حرارت آستنیته کردن در جریان عملیات حرارتی فولاد هدفیلد منجر به ایجاد دانه های بزرگتر آستنیته و یک میزان کمتر کاربید می گردد. در تمامی درجه حرارت های آستنیته کردن در محدوده1225 تا 1000 فاز غالب آستنیت است.
-5 -2 با افزایش درجه حرارت آستنیته کردن فولاد هدفیلد از1000 تا به 1225 درجه سانتی گراد استحکام تسلیم و استحکام نهایی کشش افزایش و انعطا ف پذیری کاهش می یابد. این امر بنابر یک افزایش قابلیت انحلال کربن در آستنیت و رشد دانه حاصل از افزایش درجه حرارت آستنیته کردن است.
-5 -3 نتایج آزمایش مقاومت به ضربه چارپی نشان داد که افزایش درجه حرارت آستنیته کردن انرژی شکست ضربه را کاهش ولی سختی را افزایش می دهد. این موضوع به دلیل افزایش اندازه دانه آسنتیت و بالا رفتن استحکام تسلیم در درجه حرارت بالاتر آستنیته کردن است.
-5 -4 مقاومت به فرسایش فولاد هدفیلد با افزایش درجه حرارت آستنیته کردن عمدتاً به لحاظ بالا رفتن استحکام تسلیم افزایش می یابد.
-5 -5 شکست نگاری نشان داد که در تمامی درجه حرارت های آستنیته کردن یک شکست نرم از نوع قیف و مخروط (Cone & Cup) به وجود می آید و با بالا بردن درجه حرارت آستنیته کردن شکست نرم و انعطا ف پذیر افزایش می یابد.
-5 -6 تصاویر SEM از سطوح فرسایش یافته نشان داد مکانیزم غالب در فرآیند فرسایش مکانیزم سایشی است که با افزایش درجه حرارت آستنیته کردن در جریان عملیات حرارتی درجه آسیب سطحی در آزمایش مقاومت به فرسایش کاهش می یابد. در نهایت آزمایش آنالیز نقطه ای EDS برروی سطح فرسایش یافته نشان داد مکانیزم های تریبولوژیک (مالشی) در آزمایش مقاومت به فرسایش بوجود نیامده است.
منبع خارجی: Journal of Materials Research and Technology 2021
منبع فارسی: ماهنامه آذر 1402 – صنعت ریخته گری
ترجمه: محمدجواد توسلی کیالنی
منابع:
[1] Barannikova SA, Li Y, Malinovsky A, Pestsov D. Study of localized plastic
deformation of hadfield steel single crystals using speckle photography technique.
Key Eng Mater 2016;683:84e9.
[2] Chen C, Feng XY, Lv B, Yang ZN, Zhang FC. A study on aging carbide precipitation
behavior of hadfield steel by dynamic elastic modulus. Mater Sci Eng, A2016;677:446e52.
[3] Mousavi Anijdan SH, Sabzi M. The effect of heat treatment process parameters on mechanical properties, precipitation, fatigue life, and fracture mode of an austenitic Mn Hadfield steel. J Mater Eng Perform 2018;27:5246e53.
[4] Sabzi M, Moeini Far S, Mersagh Dezfuli S. Effect of melting temperature on
microstructural evolutions, behavior and corrosion morphology of Hadfield austenitic
manganese steel in the casting process. International Journal of Minerals, Metallurgy and Materials 2018;25:1431e8.
[5] Magdaluyo Jr ER, Ausa MS, Tinio RJ. Effect of titanium ongouging abrasion
behavior and hardness of austenitic manganese steel. Transactions on Engineering
Technologies 2016;12:73e81.
[6] Srivastava AK, Das K. In: In-situ synthesis and characterization of TiC-reinforced
Hadfield manganese austenitic steel matrix composite, vol. 49. Iron and Steel Institute of Japan Int.; 2009. p. 1372e7.
[7] Srivastava AK, Das K. Corrosion behaviour of TiC-reinforced hadfield manganese
austenitic steel matrix in-situcomposites. Open J Met 2015;5:11e7.
[8] Zakharova EG, Kireeva IV, Chumlyakov YI, Shul’mina AA, Sehitoglu H, Karaman I. The effect of aluminium on mechanical properties and deformation mechanisms of hadfield steel single crystals. J Phys IV : J 2004;115:243e50.
[9] Tian X, Zhang Y. Mechanism on the effect of Al upon the g/ε martensite transformation in the Fe-Mn alloys. J Mater ci Technol 1996;12:369e72.
[10] Hosseini SH, Limooei MB, Hossein Zade M, Askarnia E, Asadi Z. Optimization
of heat treatment due to austenising temperature, time and quenching solution
in Hadfield steels. Int J Materials Metallurgical Engineering 2013;7:1940e3.
[11] Sabzi M, Farzam M. Hadfield manganese austenitic steel: a review of manufacturing processes and properties. Mater Res Express 2019;6:1e15.
[12] Zorc B, Nagode A, Kosec B, Kosec L. Analysis of weld cracking in shot blasting
chambers made of Hadfield steel. Eng Fail Anal 2013;33:48e54.
[13] Agunsoye JO, Isaac TS, Abiona AA. On the comparison of microstructure
characteristics and mechanical properties of high chromium white iron with the
hadfield austenitic manganese steel. J Miner Mater Char Eng 2013;1:24e8.
[14] Lindroos M, Apostol M, Heino V, Valtonen K, Laukkanen A, Holmberg K, et
- The deformation, strain hardening, and wear behavior of chromium-alloyed
Hadfield steel in abrasive and impact conditions. Tribol Lett 2015;57:1e11.
[15] El-Mahallawi I, Abdel-karim A, Naguib A. Evaluation of effect of chromium on
wear performance of high manganese steel. Mater Sci Technol 2001;17:1385e90.
[16] Azadi M, Mirani Pazuki A, Olya MJ. The effect of new double solution heat
treatment on the high manganese hadfield steel properties. Metallography, Microstructure Analysis 2018;7:618e26.
[17] Annual book of Astm 128 A/128 M. In: Standard specification for steel castings,
austenitic manganese, vol. 1. Engineered Casting Solutions Since; 2012. p. 1e3.
[18] Annual book of Astm E92-82. Standard test method for Vickers hardness of
metallic materials. ASTM International; 2003. p. 1e9.
[19] Annual book of Astm E8/E8M-13a. In: Standard test methods for tension
testing of metallic materials, vol. 3. ASTM International; 2013. p. 1e28.
[20] Annual book of Astm A370 Standards, Astm A370-15. In: Standard test methods
and definitions for mechanical testing of steel products, vols. 20e29. ASTM
Int.; 2015. p. 1e48.
[21] Lee YK, Choi CS. Driving force for g/ε martensitic transformation and stacking
fault energy of g in Fe-Mn binary system. Metall Mater Trans 2000;31:355e60.
[22] Dieter JRGE. Mechanical metallurgy. McGraw-HILL book company; 1961. p1e615.
[23] Sabzi M, Mousavi Anijdan SH, Asadian M. The effect of substrate temperature
on microstructural evolution and hardenability of tungsten carbide coating in
hot filament chemical vapor deposition. Int J Appl Ceram Technol2018;15:1350e7.
[24] Lavvafi H, Lewandowski ME, Schwam D, Lewandowski JJ. Effects of surface
laser treatments on microstructure, tension, and fatigue behavior of AISI 316LVM
biomedical wires. Mater Sci Eng, A 2017;688:101e13.
[25] Sabzi M, Mousavi Anijdan SH, Obeydavi A. The effect of joint shape geometry
on the microstructural evolution, fracture toughness, and corrosion behavior
of the welded joints of a Hadfield steel, Mechanics of Advanced Materials and
Structures 2019;26:1053e63.
[26] Ch Chen B, Lv H, Ma D, Sun F, Zhang. In: Wear behavior and the corresponding
work hardening characteristics of Hadfield steel, vol. 121. Tribology
International; 2018. p. 389e99.
[27] Lychagin DV, Filippov AV, Kolubaev EA, Novitskaia OS, Chumlyakov YI,
Kolubaev AV. Dry sliding of Hadfield steel single crystal oriented to deformation
by slip and twinning: deformation, wear, and acoustic emission characterization.
Tribol Int 2018;119:1e18.
[28] Xu X, van der Zwaag S, Xu W. The effect of martensite volume fraction on
the scratch and abrasion resistance of a ferriteemartensite dual phase steel.
Wear 2016;348:80e8.
[29] Jafarian H. Characteristics of nano/ultrafine-grained austenitic TRIP steel
fabricated by accumulative roll bonding and subsequent annealing. Mater Char2016;114:88e96.
[30] Xu X, Xu W, Ederveen FH, van der Zwaag S. Design of low hardness abrasion
resistant steels. Wear 2013;301:89e93.
[31] Mousavi Anijdan SH, Sabzi M. The evolution of microstructure of an high Ni
HSLA X100 Forged steel slab bythermomechanical controlled processing. In:
TMS annual meeting &Exhibition; 2018. p. 145e56.
[32] Lindroos M, Laukkanen A, Cailletaud G, Kuokkala VT. Microstructure based
modeling of the strain rate history effect in wear resistant Hadfield steels. Wear2018;396e397:56e66.
[33] Feng XY, Zhang FC, Yang ZN, Zhang M. Wear behaviour of nanocrystallised
Hadfield steel. Wear 2013;305:299e304.
[34] Wang W, Song R, Peng S, Pei Z. Multiphase steel with improved impact-
abrasive wear resistance in comparison with conventional Hadfield steel.
Mater Des 2016;105:96e105.
[35] Zhang L, Guo P, Wang G, Liu Sh. Serrated flow and failure behaviors of a
Hadfield steel at various strain rates under extensometer-measured strain control
tensile load. J Materials Research Technology 2020;9:1500e8.
[36] Mousavi Anijdan SH, Sabzi M, Roghani Zadeh M, Farzam M. The effect of
electroless bath parameters and heat treatment on the properties of Ni-P and
Ni-P-Cu nano-composite coatings. Mater Res 2018;21:1e9.
[37] Sanjari M, Taheri AK, Ghaei A. Prediction of neutral plane and effects of the
process parameters in radial forging using an upper bound solution. J Mater
Process Technol 2007;186:147e53.
[38] Machado PC, Pereira JI, Penagos JJ, Yonamine T, Sinatora A. The effect of
in-service work hardening and crystallographic orientation on the micro-scratch
wear of Hadfield steel. Wear 2017;376e377:1064e73.
[39] Mousavi Anijdan SH, Sabzi M. The effect of pouring temperature and surface
angle of vortex casting on microstructural changes and mechanical properties of
7050Al-3wt% SiC composite. Mater Sci Eng, A 2018;737:230e5.
[40] Sanjari M, Hadadzadeh A, Pirgazi H, Shahriari A, Shalchi Amirkhiz B, Kestens
LAI, et al. Selective laser melted stainless steel CX: role of built orientation
on microstructure and micro-mechanical properties. Mater Sci Eng, A
2020;786:1e6.
[41] Lavvafi H. Effects of laser machining on structure and fatigue of 316LVM
biomedical wires. Case Western Reserve University; 2013.
[42] Chen C, Zhang FC, Wang F, Liu H, Yu BD. Effect of NþCr alloying on
the microstructures and tensile properties of Hadfield steel. Mater Sci Eng, A
2017;679:95e103.
[43] Mousavi Anijdan SH, Sabzi M, Ghobeiti-Hasab M, Roshan- Ghiyas A. Optimization
of spot welding process parameters in dissimilar joint of dual phase steel
DP600 and AISI 304 stainless steel to achieve the highest level of shear-tensile
strength. Mater Sci Eng, A 2018;726:120e5.
[44] Sabzi M, Mersagh Dezfuli S. Drastic improvement in mechanical properties
and weldability of 316L stainless steel weld joints by using electromagnetic vibration
during GTAW process. J Manuf Process 2018;33:74e85.
[45] Hajalilou A, Mazlan SA, Lavvafi H, Shameli K. A yield stress scaling function
for ER fluids. Field Responsive Fluids asSmart Materials 2016:109e13.
[46] Sabzi M, Mersagh Dezfuli S. Post weld heat treatment of hypereutectoid
hadfield steel: Characterization and control of microstructure, phase equilibrium,
mechanical properties and fracture mode of welding joint. J Manuf Process
2018;34:313e28.
مقالات و اخبار
یک نظر در “تأثیر درجه حرارت آستنیته کردن بر تحولات ریز ساختار، خصوصیات مکانیکی نوع شکست و مکانیزم فرسایش فولاد منگنزی هدفیلد”
مقالهٔ مفیدی بود