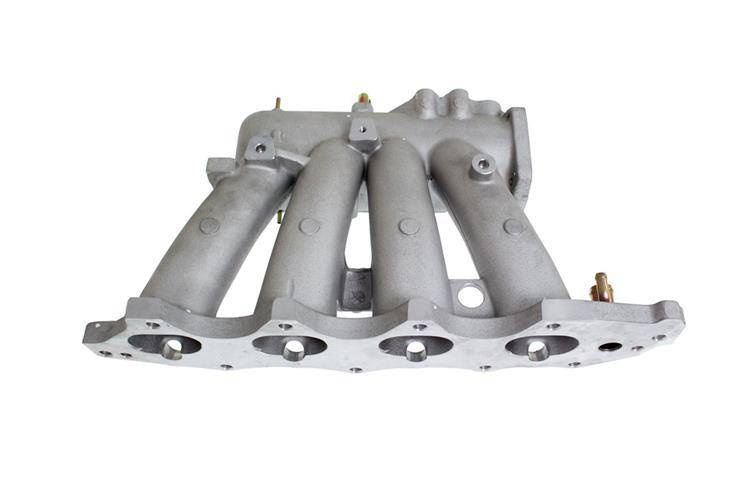
توسعه کمک های تغذیه با عملکرد بالا برای بهبود کیفیت قطعه ریختگی
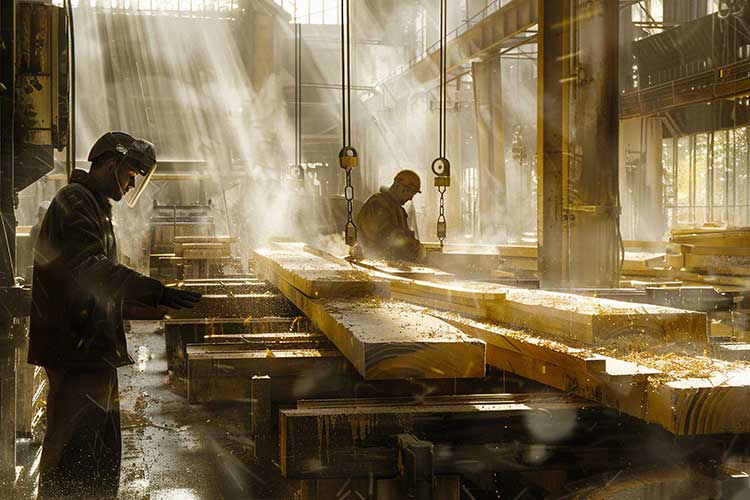
چکیده:
امروزه ریخته گران به منظور رقابت با همتایان خود همواره در جست و جوی روش هایی برای افزایش بهره وری، بهبود کیفیت ریخته گری و کاهش عیوب هستند. مواد کمک کننده ی تغذیه به ویژه غلاف های تغذیه، در طول سا ل های گذشته تحول یافتند تا پاسخگوی نیازهای موجود باشند. این مقاله مروری بر پیشرفت های حاصل در زمینه طراحی این غلاف ها (اِسلیو ها) خواهد بود که به جزئیات جدیدترین پیشرفت ها به وسیله فناوری استفاده از تغذیه های کوچک نیز می پردازد.
مقدمه:
ریخته گران عموماً به تغذیه ها به عنوان یک ابزار ضروری هرچند چالش برانگیز می نگرند. آن ها برای جلوگیری از حفرات انقباضی در ریخته گری مورد نیاز هستند، اگرچه بازده ریخته گری را کاهش می دهند و حذف و تمیزکاری پس از فرآیند ریخته گری پرهزینه است.
برای اینکه تغذیه ها عملکرد مناسبی داشته باشند، باید دارای دو مشخصه مهم باشند. یکی از این ویژگی ها مدول مناسب یعنی نسبت سطح به حجم مناسب است، به طوریکه تغذیه دیرتر از قسمت قطعه ریختگی که برای آن تعبیه شده است، سرد شود. از طرفی تغذیه ها باید مقدار ماده (فلز)تغذیه کننده کافی برای جبران کاهش حجم در اثر انقباض را دارا باشند.
این دو معیار در طول زمان منجر به دستورالعمل های متعددی برای طراحی نحوه قرارگیری و شکل هندسی تغذیه ها شده اند. تغذیه ها در ابتدا در قالب به شکل تغذیه های «طبیعی » ایجاد می شدند، به این معنی که آن ها توسط همان مواد قالب مانند محفظه قالب و سیستم راهگاهی تشکیل می شدند.
این به این معنی است که میزان اتلاف حرارت از سطح تغذیه مانند بقیه قسمت های قطعه ریختگی است، بنابراین مدول تغذیه عاملی به شدت کنترل کننده بود. تغذیه های “طبیعی” امروزه هنوز هم مورد استفاده قرار می گیرند، اما روز به روز بیشتر تسلیم برخی از انواع کمک کننده های تغذیه می شوند. یک تغذیه “طبیعی” تنها از بخش کوچکی از حجم کل خود برای تامین و مذاب رسانی به قطعه استفاده می کند وحجم باقی مانده “هدر رفت” تلقی می شود اگرچه برای نگه داشتن یک تش سر لازم است.
تش سر یا سر تغذیه:
در طول سال ها تعدادی از انواع کمک کننده های تغذیه به منظور بهبود کارایی تغذیه از طریق کنترل اتلاف حرارت از تغذیه یا تامین یک منبع گرمای اضافی برای فلز در آن، ایجاد شدند. پوشش گرمازا احتمالا اولین نوع کم کننده تغذیه بود.
رویه های داغ موادی هستند که پس از ریخته گری به قسمت بالایی تغذیه های باز اضافه می شوند. آن ها از اتلاف گرمای تابشی از تغذیه جلوگیری می کنند و عایق یا گرمای اضافی را برای سطح تغذیه فراهم می کنند. رویه های داغ عایق شامل موادی مانند پوسته برنج یا پرلیت منبسط یا ورمیکولیت هستند که چگالی کم و خواص عایق عالی دارند. علاوه براین مواد می توان از مواد گرمازا نیز استفاده کرد. مواد گرمازا معمولاً بر مبنای واکنش “ترمیت” به عنوان منبع گرما هستند:
4Fe2O3 + 8Al → 4Al2O3 + 8Fe + heat (2400C, 4500F)
ترمیت را می توان به تنهایی یا مخلوط با یک ماده عایق استفاده کرد. این واکنش نه تنها گرما و عایق را فراهم می کند، بلکه منبع آهن مذاب برای تامین فلز خوراک اضافی به تغذیه است.
اگرچه فرمول های متعدد و انواع مختلف رویه های داغ وجود دارند، اما استفاده از آن ها به دلیل شکل فیزیکی آن ها تا حدودی مشکل ساز بوده است. بیشتر رویه های داغ دانه های یا پودری هستند. آن ها باید پس از ریخته گری اضافه شوند و به سختی می توان آن ها را به دقت و به صورت کاملا ایمن اضافه کرد. پیشرفت اخیر این مسائل را بر طرف می کند. درپوش های پوششی شناور ۲FCL به عنوان جایگزینی برای مواد رویه داغ پودری سنتی یا سرتغذیه طراحی شدهاند.
آن ها می توانند با هر دو خاصیت عایق و یا نسوز گرمازا تولید شوند FCL ها از ماده سرامیکی سیلیکات آلومینیم با چگالی کم LDASC ساخته شد ه اند و با سیستم رزین سرد درجه یورتان فنولیک (PUCB) متصل می شوند. آن ها به شکل دیسک های گرد ساخته می شوند و اندازه آن ها به گونه ای است که در داخل تغذیه های قدیمی که در قسمت بالایی باز و گرد هستند، قرار گیرند. اشکال دیگر را می توان در صورت نیاز برای سایر شکل های تغذیه ساخت. شکل ۱ چند اندازه از پوشش شناور گرد را نشان می دهد.
استفاده از FCL ها می تواند به طور چشمگیری ثبات و پایداری کارایی تغذیه را بهبود بخشد. بسیاری از متغیرهای ریخته گری هنگام استفاده از FCL حذف می شوند، مثلا اینکه چه مقدار از رویه استفاده شده است؟ چه زمانی رویه اعمال شده است و آیا واقعاً سطح تغذیه را به طور یکنواخت پوشانده است؟ آزمایش های انجام شده در آزمایشگاه و کارخانه های ریخته گری بهبود عملکرد کلی و پایداری این درپوش ها را در مقایسه با استفاده از ترکیبات رویه های داغ سنتی، تأیید می کنند. شکل۲ یک FCL را روی یک قالب تازه ریخته شده نشان می دهد.
اِسلیوها یا غلاف های تغذیه:
اِسلیوهای تغذیه بهبود چشمگیرتری در کارایی تغذیه ایجاد کرده اند. اِسلیوهای تغذیه می توانند عایق، گرمازا یا ترکیبی از این خواص باشند. آن ها به طور کلی سطح استوان های تغذیه، یعنی بزرگترین سطح را پوشش می دهند. اگرچه درصورت استفاده از اِسلیوهای الحاق شدنی ۳ یا کلاهکی ۴ کل ناحیه می تواند پوشش داده شود. همانند روکش داغ، اِسلیوها نیز از طریق ایجاد عایق و افزودن حرارت، از دست دادن گرما از تغذیه را کاهش می دهند.
یکی از روش های توصیف کردن اِسلیوهای تغذیه، در نظر گرفتن تأثیر آن بر مدول نسبی تغذیه است. در واقع از طریق کاهش سرعت سرد شدن تغذیه، تغذیه ها به طوری منجمد می شوند که گویی بزرگتر هستند یا مدول بالاتری دارند. این موضوع باعث ایجاد مفهوم “ضریب گسترش مدول” یا MEF شده است. به عنوان مثال، اگر یک اِسلیو تغذیه مانند یک تغذیه”طبیعی” با مدول دو برابر منجمد شود، به آن اِسلیو باید عدد ۲ MEF داده شود.
اگر یک اِسلیو دارای 5/1MEF باشد، تغذیه دارای اِسلیو باید در همان زمانی منجمد شود که یک تغذیه طبیعی با مدول ۵/ ۱ برابر بزرگ تر منجمد می شود. به طور کلی MEF یک اِسلیو گرمازا بزرگتر از یک اِسلیو عایق است و امکان استفاده از تغذیه های کوچک تر با عملکرد بهتر را فراهم می کند.
در ساخت برخی از اولین اِسلیوهای تغذیه از مخلوط یک ماده عایق به همراه یک چسب استفاده می شد، احتمالا مخلوط ماسه سبز با خاک رس و آب یا روغن و نشاسته که شبیه به یک ماهیچه پخته و خشک بود. این مخلوط می توانست در اطراف “چرخ۵” تغذیه روی یک مدل کوبیده شود ۶ تا یک اِسلیو ایجاد شود. اگرچه این کار موثر بود، اما بسیار زمان بر بود و کارایی بالایی نداشت. در نهایت در سال ۱۹۴۷ ترکیبات گرمازا ایجاد شد که عملکرد تغذیه را بهبود بخشید.
اِسلیوهای گرمازای پیش ساخته شده برای اولین بار در سال۱۹۴۸ از دوغاب بر پایه آب حاوی چسب و الیاف نسوز تولید شدند. در واقع این اِسلیوها به وسیله ایجاد یک خلاء روی یک قالب با شبکه بندی ریز به منظور رسوب دادن الیاف روی قالب و حذف آب ساخته شدند.
سپس اِسلیوها پخته شدند تا آب اضافی خارج شود و استحکام لازم ایجاد شود. شکل ۳ قالب خلا و اِسلیوهای الیافی نهایی را نشان می دهد. اِسلیوهای الیافی را می توان در چندین درجه از عایق تا بسیار گرمازا، بسته به مقدار مواد گرمازای اضافه شده به دوغاب تولید کرد. این اِسلیوها معمولاً سطح خارجی زبر و ناهمواری دارند که این ویژگی برای کاربردهای کوبیدنی مناسب است و تداخل خوبی با مواد قالب برای نگه داشتن اِسلیو در جای خود فراهم می کند.
سطح اِسلیو همچنین می تواند سنگ زده شود تا سطح صا ف تر و کنترل ابعادی بهتری برای کاربردهای قابل نصب (۷) فراهم شود. گام بعدی در تحولات اِسلیوهای کارایی بالا، معرفی اِسلیوهای تولید شده به روش دمیدن (۸) بود که از ریز کوره های (۹) سیلیکات آلومینیم با چگالی کم (LDASC) با استفاده از فرآیند کلد باکس ۱۰ ساخته شدند. این اِسلیوها مزایای زیادی به همراه داشتند.
در واقع از آنجایی که این اِسلیوها به روش کلد باکس شکل می گیرند، از نظر ابعادی دقیق تر از اِسلیوهای الیافی استاندارد هستند. علاوه بر این، اِسلیوهای LDASC یکنواختیِ ترکیبِ بیشتری از یک اِسلیو به اِسلیوی دیگر نشان می دهند و مانند اِسلیوهای الیافی رایج می توانند در طیف وسیعی از ترکیبات از عایق تا بسیار گرمازا تولید شوند. این اِسلیوها میتوانند در کاربردهای سنتی کوبیدنی یا به عنوان اِسلیوهای مغزی( insert) مورد استفاده قرار گیرند.
اِسلیوهای LDASC برای اولین بار در سال ۱۹۹۷ معرفی شدند و به مرور تغییرات و پیشرفت های زیادی در آن ها ایجاد شد. یکی از مهمترین پیشرفت ها مربوط به فرمولاسیون بسته های گرمازا بوده است. همانطور که قبلاً اشاره شد، تمام کمک تغذیه های گرمازا به واکنش ترمیت متشکل از پودر آلومینیم و اکسید آهن متکی بوده هر چند مواد شیمیایی دیگری نیز معمولا برای تقویت واکنش اضافه می شوند مانند کریولیت Na3AlF6 یا ترکیبات فلورایدهای مشابه که اغلب به عنوان”آغازگر واکنش” اضافه می شوند. این ترکیبات سطح ذرات آلومینیم را مانند فلاکس تمیز می کنند تا واکنش ها سریع تر و با حرارت بیشتری صورت بگیرد.
هنگام آزمایش با فرمولاسیون مخصوص چدن نشکن مشخص شد که تغذیه های دارای اِسلیو می توانند باعث کاهش کرویت شوند. بررسی های بیشتر نشان داد جذب آلومینیم از اِسلیو به درون تغذیه موجب تغییر شکل گرافیت های کروی گردیده است. نمونه هایی از تغییر شکل گرافیت در تغذیه های دارای اِسلیو در شکل ۵ نشان داده شده است.
جذب آلومینیم به صورت بالقوه می تواند در مناطقی گرافیت ورق های بر روی سطح چدن نشکن ریخته گری شده ایجاد کند که سبب از دست دادن خواص فیزیکی قطعه نهایی می گردد. شکل ۶ یک قطعه چدن نشکن بزرگ ریخته گری شده را به همراه گرافیت ورق های روی سطح ماشینکاری شده از اِسلیو نشان می دهد. تقریباً در همان زمان، مشکل دیگری در مورد اِسلیوهای گرمازا مورد استفاده در چدن نشکن ایجاد شد.
یک کارخانه ریخته گری چدن نشکن در قطعات ریختگی به روش ماسه تر تولید شده بودند عیوبی را مشاهده کرد که بعدا آن را “چشم ماهی” نامیدند. تصور می شد که فلوئور از کریولیت موجود در اِسلیوها به نحوی ماسه قالب گیری را آلوده کرده و باعث ایجاد این عیب شده بود. نمونه ای از عیب”چشم ماهی” در شکل ۷ نشان داده شده است. آزمایش های بسیاری در آن کارخانه برای تعیین علت واقعی این عیب انجام شد. بدین منظور مقادیری ماسه قالب گیری عمداً با کریولیت خالص، اِسلیوهای نسوخته و سوخته ی شکسته آلوده شدند.
در نهایت معلوم شد که اِسلیوهای سوخته علت ایجاد این عیوب بوده اند. در ادامه این نظریه مطرح شد که آلومینیم فلوراید ناشی از واکنش گرمازا هم علتی هم برای عیب “چشم ماهی” و هم تغییر شکل گرافیت در چدن نشکن بوده است. برای رفع این مشکل حذف کریولیت و هر ترکیب فلوراید دیگر در مخلوط های گرمازا ضروری بود که در نهایت به کارگیری ترکیب فلزات واکنش پذیر دیگر به عنوان «سوخت » و سایر نمک های واکنش پذیر برای شروع واکنش گرمازا، محقق شد. فرمولاسیون بدون فلوئور در حال حاضر چندین سال است که با نتایج خوبی در ریخته گری استفاده می شود.
توسعه تغذیه های کوچک:
در حالیکه LDASC ، اِسلیوهای تولید شده به روش کلدباکس در حال توسعه و بهبود بودند، پیشرفت های موازی دیگری نیز در حال رخ دادن بود. توسعه تغذیه های کوچک در اوایل دهه ۱۹۷۰ در کارخانه ریخته گری Rexroth در شهر لور ۱۱ آلمان گام مهمی در مسیر بهبود مستمر سیستم های تغذیه بود. این تغذیه های جدید بازدهی فو ق العاده ۷۰ درصدی را در تغذیه یک قطعه ریخته گری ایجاد می کنند و در عین حال اندازه کلی تغذیه را نیز کاهش می دهد، بنابراین همانطور که در شکل ۸ مشاهده می شود، فضای کمتری برای به کارگیری آن ها مورد نیاز است. اما همچنان اصل اساسی “واکنش ترمیت” بود زیرا هنگامی که آلومینیم با اکسید آهن میسوزد، حرارتی آزاد می کند که دما را تا ۲۴۰۰ درجه سانتیگراد (حدود ۴۲۵۰ فارنهایت) بالا می برد.
در این مثال حجم یک تغذیه طبیعی ۲۳ کیلوگرمی با استفاده از کلاهک گرمازا به ۴/ ۸ کیلوگرم و با استفاده از تغذیه کوچک به ۳/ ۱ کیلوگرم کاهش می یابد. همچنین سطح تمیزکاری ۱۲ با استفاده از کلاهک گرمازا از ۸/ ۱۵۸ سانتی متر مربع به ۵/ ۷۳ سانتی متر مربع و با استفاده از تغذیه کوچک حتی به ۶/ ۱۹ سانتی متر مربع کاهش می یابد. این یک بهینه سازی قابل توجه در بازده ریخته گری است که امکان عملکرد بسیار بهتر خط قالب گیری را فراهم می کند و می تواند هزینه های مربوط به دوباره کاری و سنگ زنی را کاهش دهد.
برای اینکه تغذیه این دمای بالا را ایجاد کند و مقدار فلز مورد نیاز برای تغذیه را حفظ کند، تغذیه کوچک دارای موادی مانند ماسه و یا سایر مواد عایق است. در واقع این مواد سرعت واکنش را کاهش داده و اتلاف دمای کمتر در مدت زمان بیشتری در طول انجماد خواهد داشت. این امر اجازه می دهدتا حجم چدن مذاب در تغذیه از طریق جبران اتلاف حرارت با مواد گرمازا به میزان قابل توجهی کاهش یابد. این نوع از تغذیه کوچک ابتدا با همکاری شرکت ریخته گری Rexroth آلمان ساخته و مورد استفاده قرار گرفت و امروزه نیز در اشکال و صورت های مختلف کاربرد فراوانی دارد.
هنگامی که تغذیه کوچک توسعه یافت، بهینه ساز یها به همین جا ختم نشد. اولین گام، معرفی پین های فنری بود که یک لایه ماسه بین تغذیه و قطعه ی ریختگی ایجاد می کردند تا از تماس مواد گرمازا و ماسه جلوگیری شود. در واقع هدف از این کار افزایش کیفیت سطح قطعات ریختگی بود که می تواند توسط واکنش های گرمازا در طول انجماد به خطر بیفتد. معرفی ماهیچه های برشی ساخته شده با ماسه(کرونینگ)چراغی که در تماس مستقیم با قطعه ریختگی هستند، هزینه های تمیز کاری را بیش از پیش کاهش می دهد.
با این حال با افزایش محبوبیت خطوط قالب گیری پر فشار و مدرن با قابلیت فشرده سازی بیشتر ماسه قالب گیری، تغذیه های مجهز به ماهیچه های برشی نهایت پیشرفت را بدست آوردند. ماهیچه های برشی را می تواند در اثر فشار ماسه قالب گیری تخریب گردد که می تواند باعث ایجاد عیب آخال ماسه در قطعه ریختگی شود. استفاده از ماهیچه های برشی همچنین می تواند سطح مدل را فرسوده کند.
تغذیه ها با پین فنری:
با استفاده از ماهیچه های برشی گرمازا می توان به صورت ترکیبی از مزایای پین فنری و تغذیه استفاده کرد. این ماهیچه ی گرمازا گلوی تغذیه را کم کرده و همراه با پین فنری یک لایه ماسه بین تغذیه و قطعه ریختگی ایجاد می کند. دراستفاده از این ماهیچه هیچ تکیه گاهی روی مدل ایجاد نکرده و تغذیه نیز به راحتی جدا می شود. اگرچه گاهی اوقات بخشی از گلوی تغذیه پس از ضربه زدن باقی می ماند و برای برداشتن آن و تمیزکاری قطعه باید کارهای بیشتری انجام شود.
فرمولاسیون گرمازای بهینه:
یکی دیگر از پیشرفت های مهم در توسعه تغذیه کوچک، ادغام فناوری کلد باکس LDASC با تغذیه های کوچک بود. این فرمول تولید تغذیه های سبک وزن را بدون استفاده از الیاف سرامیکی که معمولاً در تغذیه های دوغاب سنتی گنجانده می شوند، امکان پذیر می سازد. البته برخی از آن ها در جامعه اروپا خطرناک تلقی می شوند. تغذیه کوچک اولیه به دلیل استفاده از ماسه به عنوان سرامیک در اِسلیوها بسیار سنگین بود.
جایگزینی ماسه با LDASC وزن را نزدیک به ۷۵ درصد کاهش داد. با نسوز کمتر مواد گرمازای کمتری هم برای رساندن اِسلیو به همان دما نیاز بود. فرمول های بدون فلوراید توسعه یافته برای کاربردهای چدن نشکن نیز می توانند در تغذیه های کوچک گنجانده شوند. بنابراین احتمال آلودگی آلومینیم و تخریب کروی شدن کاهش می یابد.
تغذیه کوچک با گلوگاه فلزی:
به منظور استفاده از مزایای این اصول و استفاده حداکثری از این پتانسیل تغذیه کوچک با گلو گاه برشی فلزی ساخته شد.
این تغذیه روی یک پین فنری با یک تیوب فلزی مخروطی قرار گرفته است که یک گلوگاه تغذیه دقیق ایجاد می کند. تغذیه به سمت پایین حرکت می کند و در حالی که ماسه فشرده شده و روی تیوب فلزی می لغزد. نتیجه حاصل یک گلوگاه تغذیه بسیار کوچک با لبه قابل شکستن بهینه است که ضربه زدن و تمیز کاری را بسیار آسان می کند. بسیاری از کارخانه های ریخته گری با این پیشرفت در تکنولوژی تغذیه پس از حذف تغذیه تمیزکاری را به طور کامل حذف کردند.
به دلیل حرکت تغذیه ها رو به پایین ماسه قالب گیری در زیر تغذیه به خوبی فشرده شده و قطعه ریختگی سطح تماسی عالی دارد(شکل۱۱ )این نوع سیستم امروزه بسیار متداول است و تقریباً همه تامین کنندگان تغذیه از انواعی از این سیستم تغذیه استفاده می کنند که مزایای مشابهی برای ریخته گران دارد. پیاده سازی موفقیت آمیز تغذیه کوچک با گلوگاه فلزی تمایل به بهبود و پیشرفت سیستم های تغذیه را متوقف نکرد.
توسعه بعدی یک تغذیه دو قسمتی بود که یک تیوب فلزی را به عنوان یک قسمت آزاد در داخل حمل می کند. این تیوب هنگام استفاده از تغذیه به طور خودکار روی پین فنری می افتد. این که خود تغذیه در دو قسمت ساخته شده، بسته به نیاز ریخته گری، استفاده از را ه حل های متغیر با حجم های مختلف تغذیه را امکان پذیر می سازد. البته بزرگترین مزیت این تغذیه ها سهولت در استفاده بوده، زیرا تقریباً غیرممکن است که اشتباهات کاربردی در طول تغذیه انجام شود.
همزمان با پیاده سازی تغذیه کوچک دو قسمتی یک تکنولوژی جدید دیگر در حال توسعه بود. این بار هدف ایجاد یک گلوگاه برشی با سطح تماسِ کاهش یافته و بهینه بدون نیاز به ماهیچه برش جداگانه بود (شکل ۱۳). شکل گلوگاه برشی در اِسلیو گرمازا ادغام و با آن یکپارچه شده است و یک درپوش پلاستیکی بالای تغذیه قرار داده شده است تا ماسه هنگام فشرده سازی از تغذیه خارج نشود. با استفاده از این طراحی می توان تغذیه را به شیوه های اقتصادی تر از برخی سیستم های تغذیه دو و سه تکه تولید کرد. این نوع تغذیه می تواند با یا بدون پین فنری استفاده شود.
ترکیبی از تکنولوژی های تغذیه های موجود:
اگرچه از قبل چندین پیشرفت بزرگ در تغذیه ها برای استفاده در کارخانه های ریخته گری ایجاد شده بود، پیشرفت های اخیر مزایای چندین تکنولوژی را برای ایجاد نسل جدیدی از تغذیه ها گرد هم آورده است. در واقع این تغذیه کوچک جدید بهترین مزایای تکنولوژی های تغذیه را که قبلا در این مقاله مورد بحث قرار گرفت، تلفیق می کند. تکنولوژی گلو شکن فلزی هزینه های بارگیری را کاهش می دهد و اجازه می دهد تا سطح تماس بسیار کوچکی برای قرار دادن تغذیه در هندسه های پیچیده ریخته گری ایجاد شود.
استفاده از گلوهای فلزی تلسکوپی، کار با تغذیه را برای اپراتورهای ریخته گری بسیار آسان می سازد و تغییرات حجمی متعددی را ارائه می دهد که منجر به بسیاری از امکانات مختلف می شود. آخرین تکنولوژی اما نه کم اهمیت ترین آن ها، فرآیند تولید و درپوش پلاستیکی است که می تواند به کاهش هزینه کلی سیستم تغذیه کمک کند و در عین حال مزایای تغذیه های سبک وزن و کارایی بالا را ارائه دهد (شکل ۱۴ ). این تغذیه ها در حال حاضر در چندین کارخانه ریخته گری اروپایی در مراحل تایید هستند.
سلامت و پایداری: بهبود در کمک تغذیه ها
همانطور که امروزه کارایی بالا و سهولت استفاده برای کارگران ریخته گری مهم است، سلامت و ایمنی کارگر باید در درجه اول اهمیت داشته باشد. تمام تغذیه های کوچکی که در این مقاله مورد بحث قرار گرفته اند فاقد الیاف سرطان زا هستند تا از سلامت افرادی که از آن ها استفاده می کنند محافظت کنند. بسیار شبیه محصولات اسلیو LDASC که قبلاً توضیح داده شد، این تغذیه های کوچک هم اکنون بدون فلوئور تولید می شوند که ماده خطرناک دیگری است. حذف فلوئور از تغذیه ها در نهایت باعث کاهش مقدار فلوئور در ماسه قالب گیری می شودبه طوری که از عیوب سطحی ایجاد شده توسط فلوئور همانطور که در شکل ۱۵ مشاهده می شود جلوگیری می شود. فرمولاسیون تغذیه گرمازا بدون فلوئور بهر ه وری ریخته گری را بهبود می بخشد. با مقادیر کمتر فلوئور در ماسه قالب گیری، می توان از عیوب سطحی جلوگیری کرد و کیفیت ریخته گری را افزایش داد. تغذیه های کوچک بدون فلوئور همچنین می توانند به کاهش تغییر شکل گرافیت در اطراف گلوگاه تغذیه ۱۳ در ریخته گری چدن نشکن کمک کنند ( شکل ۱۶) فلوئور همچنین می تواند هنگام دفع ماسه ریخته گری استفاده شده مشکل ساز شود. با استفاده از تغذیه های بدون فلوئور، میزان فلوئور در ماسه قالب گیری استفاده شده بسیار کمتر می شود، به طوریکه دفع ماسه در محل دفع زباله قابل قبول می شود. در نهایت، استفاده از تغذیه های بدون فلوئور در فرآیند تغذیه گذاری می تواند یک مزیت اقتصادی برای ریخته گری و گامی در جهت مثبت برای حفاظت از محیط زیست باشد.
نتیجه گیری:
همانطور که از تاریخ طولانی پیشرفت و بهبود در عملکرد و کارایی کمک تغذیه ها مشاهده می شود، نیاز به بهبود مستمر، به ابتکارات فرآیندی محدود نمی شود. مواد مصرفی کارخانه های ریخته گری نه تنها می تواند کیفیت و عملکرد ریخته گری را بهبود بخشد، بلکه هزینه های کلی را به روشی ایمن و کارآمد کاهش می دهد. پیشرفت های اخیر در طراحی تغذیه ها منجر به ساخت تغذیه های کوچک جدید شده است که چندین مزیت را در یک محصول واحد ترکیب می کند.
اکنون ریخته گران می توانند اندازه و وزن تغذیه را کاهش داده و رد تغذیه را که روی قطعه ی ریخته گری باقی مانده است، حاصل حذف کنند. اختراع تکنولوژی بدون فلوئور که ابتدا در تغذیه های بزرگتر LDASC آغاز شد، اکنون به تغذیه های کوچک تر و کارآمدتر نیز منتقل شده است. در واقع می توان از این طریق نه تنها از تغییر شکل گرافیت که گاهی در چدن نشکن توسط اسلیوهای تغذیه حاوی فلوئور ایجاد می شود، جلوگیری شود، بلکه از مزایای وزن کمتر، ابعاد دقیق و کاهش اثرات مخرب زیست محیطی بهره مند شد.
ترکیبی از کارآیی، عملکرد و کاهش هزینه در تغذیه های کوچک امروزی انتظارات را در مورد توانایی تغذیه ها بالا برده اند. این نوع تغذیه ها راه حلی نوین برای چندین مشکل است که امروزه کارخانه های ریخته گری با آن دست و پنجه نرم می کنند و به ریخته گران اجازه می دهند تا قطعات ریخته گری را در سطح جهانی با قیمت بسیار پایین تری تولید کند.
منبع فارسی: ماهنامه مهر 1402 – صنعت ریخته گری
منبع خارجی: ASK Chemicals
ترجمه: وحید آقازاده؛ شرکت مواد ایتوک (IGMCO)
منابع:
- Aufderheide, R.C., Mathias, J.M., Waters, K., “New Hot
Topping Techniques Improve Riser Feeding Consistency”,
AFS Transaction 2007, Paper 07-098.
- Aufderheide, R.C., Showman, R.E., Twardowska, H, “New
Developments in Riser Sleeve Technology”, AFS Transactions1998, Paper 98-07.
- Showman, R.E., Lute, C.A., Aufderheide, R.C., “Exothermic
Riser Sleeves Can Cause Flake Graphite in Ductile
Iron”, AFS Transactions 2001, Paper 01-086. Aufderheide,
R.C., Showman, R.E., Close, J.,
- Aufderheide, R.C., Showman, R.E., Close, J., Zins, E.J.,
“Eliminating Fish-Eye Defects in Ductile Castings”, AFS
Transactions 2002, Paper 02-047.
- Aufderheide, R.C., Showman, R.E., Jain, N., “Breaker
Core Optimization”, FS Transactions 2010, Paper 10-017
مقالات و اخبار
یک نظر در “توسعه کمک های تغذیه با عملکرد بالا برای بهبود کیفیت قطعه ریختگی”
استفاده از تغذیههای کوچیکتر واقعاً تأثیر داره؟ یعنی میشه با این روش هزینه مواد اولیه رو هم کمتر کرد؟