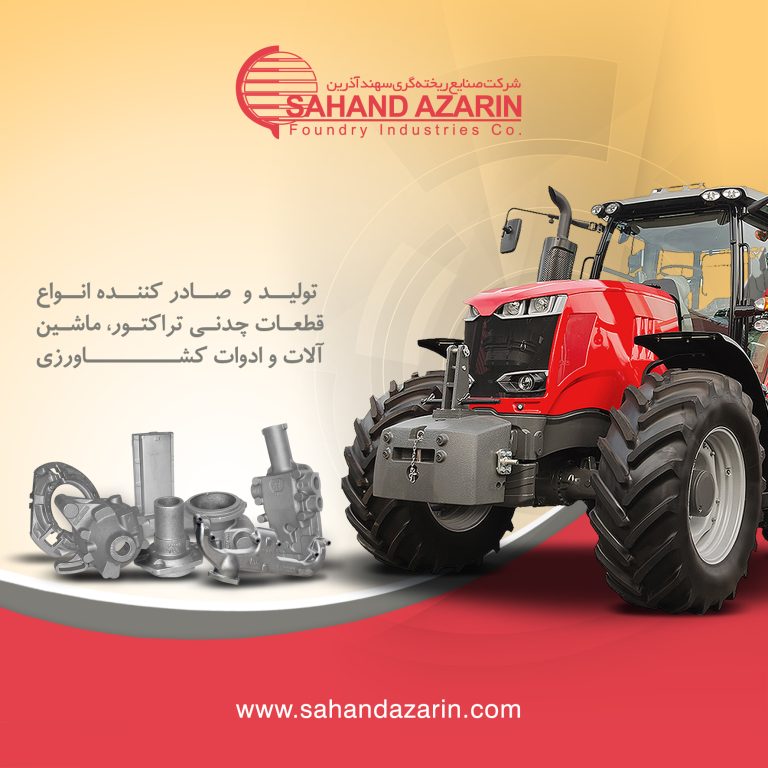
خانه » مقالات » طراحی یک نمونه ریختگی به روش دایکست برای ارزیابی دقیق منحنی تزریق و اثرات حرارتی بر خواص مکانیکی به عنوان تابعی از طول جریان
طراحی یک نمونه ریختگی به روش دایکست برای ارزیابی دقیق منحنی تزریق و اثرات حرارتی بر خواص مکانیکی به عنوان تابعی از طول جریان
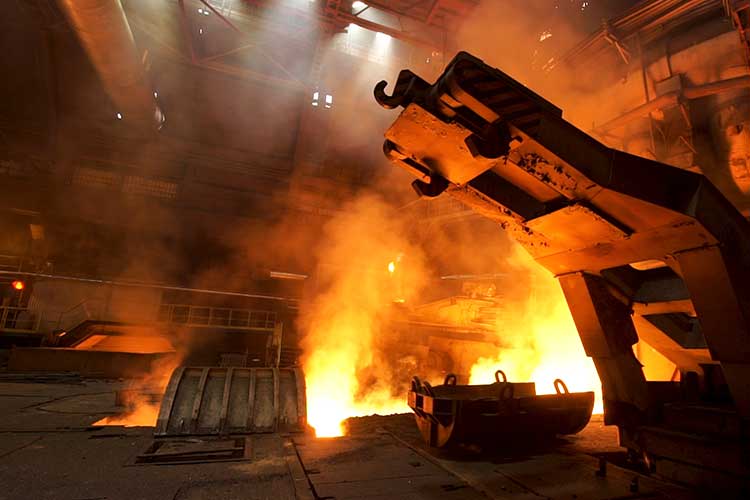
خلاصه:
پارامترها و عوامل و مورد مطالعه در فرآیند ریخته گری پر فشار (دایکست) یک ابزار متداول است و قطعات ریختگی با این روش و قالبهایشان دارای طرحهای بسیار خاص می باشند. اغلب مشخص نیست تنظیم یک پارامتر مشخصی که عموماً توصیه شده یا یک تغییر در کیفیت قطعه ریختگی در اثر طرح قالب باشد. نمونه جدید مورد بررسی دارای هندسه موجی می باشد که این امر امکان برداشت 9 نمونه تخت برای آزمایش کشش، خمش و خستگی را فراهم می کند.
اولین نمونه تقریباً در فاصله 30 میلیمتری راهباره قرار گرفته در حالی که نمونه نهم 450 میلیمتر از راهباره فاصله دارد. با توجه به هندسه مواج، حالت مکانیکی سیال در تمام نمونهها برای آزمون خواص مکانیکی بسیار مشابه است. بنابراین عوامل موثر بر خواص مکانیکی تابعی محض از منحنی شات (تزریق) مانند گاز حبس شده، پوسته منجمد شده در سیلندر تزریق و دمای قالب می باشد. شبیه سازی ریخته گری در این شرایط این طراحی را تایید خواهد کرد.
1-مقدمه
از زمان استفاده و بکارگیری ماشین دایکست محفظه سرد افقی، مهندسان و محققین تلاش نموده اند قواعدی برای تعیین یک قانون ایده آل در مورد زمان و سرعت تزریق جهت حرکت پلانژر در سیلندر تزریق تعیین نمایند. این آگاهی وجود دارد که تنظیمات صحیح مقدار هر پیمانه مذاب در دایکست محفظه سرد، زمان تزریق و منحنی تزریق دارای اثر چشمگیری بر خصوصیت کیفی قطعه ریختگی و زمان سیکل کاری دارد. در دایکست عیوبی مانند گاز حبس شده در اثر تشکیل حالت نامطلوب موجی مذاب، پوسته منجمد شده و اکسیدها رایج می باشد.
عیب گاز حبس شده و تشکیل اکسید اضافی می تواند نتیجه نامناسب بودن شتاب پلانژر و سرعت نهایی فاز تزریق آرام مطابق شکل 1 باشد. اگر شتاب و سرعت نهایی تزریق بالا باشد مذاب به صورت موج برگشتی گاز را در خود حبس خواهد نمود. همچنین اگر شتاب و سرعت تزریق نهایی برای فاز اول بسیار کم باشد مذاب از پیشانی پلانژر فاصله گرفته و در انتهای سیلندر تزریق برگشت می کند. هنگامی که موج برگشتی طول سیلندر را طی کرده و به پلانژر در حال حرکت برخورد می کند باعث ایجاد جریان آشفته (توربلانس) میگردد. در هر دوحالت همان اثر منفی ورود هوا و اکسید به سیستم راهگاهی و محفظه قالب رخ خواهد شد.
برای تعیین منحنیهای تزریق جهت شروع یک برنامه جدید دورویکرد اساسی وجود دارد. رویکرد سنتی بیشتر بر مبنای محاسبات ساده شده بوده که متکی به مبانی مانند صرفه جویی انرژی یا ارتباطات هندسی درون سیستم محفظه سرد می باشد. رویکرد جدیدتر بطور خالص بر اساس شبیه سازی مبنای می باشد که اجازه می دهد اثرات فیزیکی ماننده اصطکاک و ویسکوزیته در مذاب و در فصل مشترکها به صورت دقیق تر محاسبه شود.
مثالهایی برای تعیین حرکت پلانژر در فاز تزریق آرام در تحقیقات Faura و همکارانش (1) ارائه شده که بر مبنای شبیه سازی آب کم عمق به وسیله آنالیز عددی است. بعدها Zamora و همکارانش(2) تحقیقاتی با استفاده از آب به عنوان سیال انجام دادند. مدل آنالیز Garber اغلب در تحقیقاتی در خصوص پارامترهای تزریق آرام بکار رفته است . Laouar و همکارانش (4) مطالعاتی را به وسیله آنالیز عددی انجام داده است. ( Barkhudarov) 5 و (Frings) 6 و ( Fiorese) 7 و همکارانشان یک مرور همه جانبهای بر مقالات موجود نموده و برخی موارد کلیدی از تحقیق قبلی تاکنون را خاطر نشان کردند.
اما اغلب مواردی اساسی در فرآیند نادیده گرفته می شود به عنوان مثال مقایسه سرعتهای HPDC نهایی برای فازهای آرام و سریع انجام می شود ولی سینتیک و عوامل وابسته به زمان درنظر گرفته نمی شود. در نتایج اکثر مطالعات تجربی زمان توقف سیلندر، شرایط حرارتی سیلندر یا بررسی تاثیر محل نمونه برداری برای آنالیز متالورژیکی و آزمایش مکانیکی اشاره نمی شود. در حالی که هوای حبس شده تاثیر قابل اندازه گیری بر خواص مکانیکی دارد اما به هیچ وجه تنها نقص منشعب از سیلندر تزریق نیست. پوسته منجمد شده که نتیجه بلورهای منجمد شده بیرونی است می تواند فقط به اندازه هوای حبس شده تاثیر منفی بر خواص مکانیکی داشته باشد. اما ایجاد آنها تفاوت عمدهای با هوای حبس شده دارد.
البته پوسته منجمده شده عیب ذاتی در فرآیند دایکست می باشد. سیلندر تزریق در حین کار یک دمای شبه پایدار را به عنوان فولاد گرم کار تحمل می کند. دمای داخلی سیلندر به حدود450 سانتی گراد و دمای سطح بیرونی آن به دمای 150 درجه سانتی گراد می رسد که به طور تجربی توسط Hartmann و همکارانش (8) نشان داده شده است. آلیاژهای آلومینیم رایج دایکستی با دمای( ~ C °700 ) در سیلندر تزریق قرار می گیرند و به محض برخورد مذاب به سیلندر سرد، انجماد شروع خواهد شد که نتیجه آن تشکیل پوستههای منجمد شده بر روی دیواره سیلندر خواهد بود.
با حرکت پلانژر در پیستون تمام پوستههای منجمد شده به درون سیستم راهگاهی هدایت خواهد شد و بسته به شرایط طراحی سیستم راهگاهی و ضخامت بیسکوئیت این پوسته منجمد شده ممکن است وارد محفظه قالب گردد که در این صورت، برای خواص مکانیکی قطعه ریخته گری مضر است یا می تواند باعث نشتی شود نزدیک مسیر جریان فشار بالا روغن پوسته موتور شکل 2 تصویری ازیک بیسکویت قطعه دایکس تیبا وجود پوستههای انجمادی را نشان می دهد.
فلزی که پوسته منجمد شده را شکل داده به صورت پوستهای با ساختار بسیار ظریفتر نسبت به سایر آلیاژ بوده که تحت شرایط متفاوت سرد شدن در بیسکوئیت بعد از پایان تزریق فاز سریع، منجمد شده است. در داخل قطعه ریختگی، پوستههای انجمادی بسیار کوچک تر هستند زیرا ممکن است در حین پرشدن قالب ذوب مجدد رخ دهد. علاوه بر این، نیروهای برشی درون سیستم راهگاهی باعث شکسته شدن بخشهای بزرگ پوستههای انجمادی می شود.
تحقیقات مختلفی در رابطه با تاثیر پوستههای انجمادی بر کیفیت قطعات ریختگی توسط محققین مختلفی انجام شده است. Kato (9) و همکارانشانAhmad (10 و 11) و همکارانشان اثر پوستههای جامد بر خصوصیات مکانیکی شامل کشش و خستگی را در آلیاژ ADC12 اندازه گیری کمی نمودند. نمونههای نشان داده شده در تصویر 3 توسط محققان برای تاثیر منحنیهای مختلف تزریق و سایر پارامترهای فرآیند ریخته گری تحت فشار استفاده شده است. باید بین الزامات کاربردی و قابلیت ریخته گری الزامات نمونه قطعات تصویر 3 برای حذف یا تضعیف اثرات جریان ذوب یا افزایش قابلیت ردیابی عیوب تا نقطه منشاء آن طراحی نشده اند.
در عوض، طراحی آنها شبیه قالبهای صنعتی است زیرا اثرات جریان ذوب و انفصال در جریان مذاب در راهباره (گیت) رخ می دهد. اثرات جریان در داخل قالب موضوع مهمی است که تحقیقات باید به آن بپردازد زیرا تلاطم و انفصال جریان ذوب تقریبا در هر نوع قطعه ریختگی رخ می دهد و همیشه باید بین الزامات کاربردی و قابلیت ریخته گری تعادل ایجاد شود Gunasegaram و همکارانش(12) در مورد انقباضهای درون راهگاه تحقیقات بسیاری انجام داده اند.
همانطور که در تصویر 3a نشان داده شده است این انقباض موجب پخش کردن عناصر تشکیل دهنده عیوب درون آلیاژ شده و باعث کاهش تاثیر منفی بر روی خواص مکانیکی قطعه خواهد شد. از این نتایج می توان نتیجه گرفت که در صورت بررسی عیوبی که از سیلندر تزریق منشاء می گیرند، طراحی راهگاه، راهباره و نمونه می تواند نتایج تا حدودی مبهم به دست آورد. در نتیجه، مسئله اساسی در اعتبارسنجی منحنیهای مختلف تزریق، زمانهای توقف سیلندرو فرآیند پیمانه کردن مذاب که تاثیر آن بر جریان ذوب در قالب ممکن است اثر منحنی تزریق را بر خواص مکانیکی تضعیف یا تشدید کند.
به عنوان مثال نقص به مکان دیگر منتقل می شود که در آن نمونههای استخراج نمی شود در این حال ممکن است حتی در نمونه، شاهد افزایش خواص مکانیکی بود اما بااین حال نمی توان بطور دقیق اعلام کرد که این بهبود خواص مکانیکی می تواند ناشی از جابجایی نقص به مکان دیگر باشد یا اینکه این عیب به طورکامل برطرف شده است. آزمایشهای غیرمخرب مانند سی تی اسکن یا آزمایش اولتراسونیک می تواند به جلوگیری از این امر کمک کند. منطقی به نظر می رسد که فرض کنیم باید فاصله از ورودی راهباره (طول جریان درون قالب) و مسیر جریان را به عنوان کمیتی که در عیوبی به دلیل تنظیمات خاص فرآیند تزریق منشأ می گیرند، در نظر گرفت.
به حداقل رساندن سطح مذاب در هنگام پر شدن تاثیر مستقیمی بر عدم تلاطم ذوب و عدم تزریق پوسته منجمد شده (پوسته اکسیدی) به داخل محفظه قالب دارد همچنین یک سیستم راهباره با طول جریان داخلی کوتاه، باعث ورود پوستههای اکسیدی به داخل قالب شده و مانع حبس آنها در راهگاه می شود. این موضوع ممکن است بیانگر اثرات دریک قالب صنعتی نباشد، اما به منظور بررسی وابستگیهای متقابل عیوب، مکان عیب و فرآیند ذوب ریزی در سیلندر تزریق، کاهش متغیرها مورد نیاز است. هندسه قطعه ریخته گری HPDC جدید برای کمی سازی و ارزیابی پارامترها و عوامل مختلف تزریق با در نظر گرفتن مفروضات مورد بحث طراحی شده است. قالب ریخته گری تحت فشار جدید برای کمی سازی و بررسی پارامترهای دخیل و مختلف تزریق با در نظر گرفتن فرضیات مورد بحث طراحی شده است.
2- طراحی نمونه جدید، منحنی تزریق و عیوب ناشی از فرآیند ریخته گری تحت فشار (دایکست)
در این نمونه موجی جدید ضخامت دیواره 4 میلی متر ثابت در نظرگرفته شده است. تصویر 4 قطعه ریختگی کامل شامل بیسکوئیتی، سیستم راهگاهی وخروجی هوا به وسیله خلاء می باشد. هر خم Uاز قطعه با یک مقطع تخت به ابعاد140 mm*25mm* 4mm به یک دیگر متصل شد ه اند 9 قسمت از این مقاطع تخت در قطعه موجی شکل هستند طول جریان ذوب در امتداد قطعه تقریبا 450 میلیمتر و زاویه هر قسمت مسطح حدود 9 درجه می باشد.
نمونهها جهت انجام آزمایشات مکانیکی مطابق استاندارد DIN 50125 برای نمونههای کشش، خمش و نمونههای تخت خستگی آماده گردیدند. امکان بررسی خواص مکانیکی به عنوان تابعی از طول جریان کلی در داخل قالب فراهم می باشد. ایده اصلی برای طراحی قطعه به صورت موجی شکل، اجتناب از پاشش آزاد جت مانند در داخل محفظه قالب است.
پاشش جت مانند از اختلاف سرعت در تزریق اولیه و سرعت ورودی راهباره نشات می گیرد که این موضوع مستقل از آنچه در پیستون تزریق اتقاق می افتد می تواند بر روی خواص مکانیکی و متغیرهای آزمایش تاثیر بگذارد. هدف از طراحی قطعه به صورت موجی شکل مستقل کردن رفتار پرشدن محفظه قالب تا حدود زیادی از تغییرات در سرعت فاز دوم است. جریان موج دار شبه یک بعدی و مستقیم در جهت z است که هر نوع جریان برگشتی را از بین میبرد و تلاطم را به حداقل می رساند.
مزیت این رفتار پر شدن افزایش امکان ردیابی منشا عیب ریخته گری مانند پوسته منجمد شده به دلیل عدم حضور توزیع آشفته مذاب درون قالب است.این مطلب می تواند امکان تشخیص و ردیابی عیوب را افزایش دهد زیرا احتمال کمتری دارد که کاهش خواص مکانیکی مربوط به شکل قطعه و پارامترهای سیستم راهگاهی باشد.
ایده اصلی برای طراحی قطعه به صورت موجی شکل، اجتناب از پاشش آزاد جت مانند در داخل محفظه قالب است. پاشش جت مانند از اختاف سرعت در تزریق اولیه و سرعت ورودی راهباره نشات میگیرد که این موضوع مستقل از آنچه در پیستون تزریق اتقاق می افتد میتواند بر روی خواص مکانیکی و متغیرهای آزمایش تاثیر بگذارد. هدف از طراحی قطعه به صورت موجی شکل مستقل کردن رفتار پرشدن محفظه قالب تا حدود زیادی از تغییرات در سرعت فاز دوم است.
جریان موج دار شبه یک بعدی و مستقیم در جهت z است که هر نوع جریان برگشتی را از بین میبرد و تلاطم را به حداقل می رساند. مزیت این رفتار پر شدن افزایش امکان ردیابی منشا عیب ریخته گری مانند پوسته منجمد شده به دلیل عدم حضور توزیع آشفته مذاب درون قالب است.این مطلب می تواند امکان تشخیص و ردیابی عیوب را افزایش دهد زیرا احتمال کمتری دارد که کاهش خواص مکانیکی مربوط به شکل قطعه و پارامترهای سیستم راهگاهی باشد.
برای خارج کردن هوا از محفظه قالب سیستم خلا درنظرگرفته شده است. نمودار تصویر 5 رابطه بین میانگین سرعت ورود جریان به راهباره، سرعت فاز دوم و زمان پرشدن می باشد. همانطور که از نمودار مشخص می باشد مقادیر زمان پر شدن قالب در مرحله شتاب پلانژر محاسبه گردیده است بنابراین بین آن با میانگین سرعت ورود جریان به راهباره ارتباط خطی وجود ندارد. دو نوع طراحی برای ورودی راهباره وجود دارد که در تصویر 6 نشان داده شده است. در قسمت چپ تصویر یک طرح نسبتاً سنتی و مرسوم نشان داده شده است، طرح پیش فرض برای تخمین اثرات متقابل هوای حبس شده و پوستههای منجمد شده خواهد بود.
راهگاه بهینه شده در سمت راست تصویر 6 با هدف کاهش تلاطم داخلی، افزایش یکنواختی سرعت در راهگاه و انحراف هوای محبوس شده به خارج از بخش گیج به دلیل افزایش اصطکاک و مقاومت ناشی از فشار در مرکز ورودی، طراحی شده است. در سمت راست تصویر راهباره بهینه شده نشان داده شده است این طراحی به دلیل افزایش فشار و اصطکاک در قسمت مرکزی ورودی راهباره باعث خارج کردن هوای حبس شده از قسمت اصلی قطعه شده، تلاطم داخلی جریان در حفره قالب را کاهش داده و همچنین باعث یکنواختی سرعت خروجی جریان از راهباره خواهد شد. این طراحی شامل یک فرورفتگی در وسط ورودی راهباره می باشد.
3- نتایج شبیه سازی
شبیه سازی در نرم افزار MAGMA 5.3,1,0 انجام شده است. کمیت * smooth filling * در نرم افزار نتیجه را برای جبهه جریان در محفظه قالب را در هر مرحله زمانی اضافه می کند و سپس آن را بر تعداد مراحل زمانی شبیه سازی تقسیم می کند. این عدد تا حدودی انتزاعی می باشد که مقدار کل سطح آزاد را در طول پر شدن قالب توصیف می کند.
مقادیر رایج کمیت * smooth filling * برای قطعه دارای محفظه قالب دوگانه مانند قطعه ارائه شده در تصویر 3d ، از 20000 – 28000 بسته به اینکه پارامترهای تزریق چگونه باشد تغییر می کند. تصویر 7 نتیجه شبیه سازی قالب دو محفظه ای در جبهه جریان ذوب را نشان می دهد. اثر پاشش جت مانند ذوب که در بخش قبلی تشریح شد و پخش شدن کلی جبهه مذاب به وضوح نمایان می باشد. شکل موجی نمونه جدید دارای برخی ویژگیها در نحوه جریان درون قالب می باشد.
مقادیر * smooth filling * حدود3500 تا 5000 بسته به نقطه تغییر فاز تزریق و سرعت فاز دوم می باشد که به کاهش سطح آزاد مذاب~ 75 درصد در محفظه قالب ارتباط دارد. شکل 8 نتیجه شبیه سازی قطعه موجی جدید می باشد. همانطور که نمایان است جبهه جریان مذاب در نمونه موجی شکل کاملاً صاف و آرام می باشد به دلیل عدم پراکندگی جبهه مذاب تاثیر اثرات جریان داخلی درون قالب کاهش می یابد.
نتایج همچنین نشان می دهد جریان ذوب تمایلی به آشفتگی و تلاطم درون قالب را ندارد. عدم تغییر جریان جهت دار در داخل راهبار و قطعه ریختگی در جهت y باعث می شود پس از عبور ذوب خروجی از نوک راهگاه عیوب به طور غیریکنواخت در قالب پراکنده نشوند. به احتمال بسیار زیاد در این شرایط عیوب از یک موقعیت مرکزی وارد بیسکوئیتی شده و در امتداد خط تقارن مرکزی حرکت خواهند کرد. مدل موجی از تشکیل معمول جریان جت مانند و اثرات آشفتگی هنگام برگشت جریان جت مانند به دیواره قالب جلوگیری کرده است (شکل ).
این موضوع همان جریان نیمه یک بعدی است که در بخش قبلی توضیح داده شد. جریان ردیاب در یک خط موجی محور z را تعقیب می کند.در تلفیق با 9 موقعیت مستقل برای نمونه برداری، این امر امکان پاسخ در مورد طول جریان، اثر و منشاء عیوب بادقت بالا در مقایسه نمونههای معمول تخت را فراهم می نماید. تصویر 9 توزیع سرعت در حین فرآیند پرشدن محفظه قالب در مرحله فاز دو با سرعت پلانژر 3.5 متر بر ثانیه را نشان می دهد. بدیهی است که توزیع سرعت در مناطق مسطح قطعه بدون درنظرگرفتن فاصله آنها از راهباره یکسان می باشد. این مطلب جریان داخلی ذوب را به عنوان متغیری که خواص مکانیکی را در مکانهای مختلف تغییر می دهد حذف خواهد کرد.
همانطور که در تصویر 8 مشاهده می شود جبهه جریان ذوب آرام و بدون تلاطم می باشد. تصویر 10 نتیجه شبیه سازی حبس هوا پس از پر شدن کامل قالب با تخلیه هوا رایج می باشد. همانطور که مشخص می باشد احتمال زیادی وجود دارد که هوای حبس شده در نمونههای 8 و 9 باقی بماند. به طور تجربی میتوان گفت که میزان هوا حبس شده تا 2 درصد تاثیر منفی زیادی بر خواص مکانیکی نخواهد گذاشت اما با اینحال در حین مقایسه نمونه 9 و 8 این نکته را باید در نظرگرفت که نمونه شماره 9 به مکان تهویه هوا از قالب نزدیکتر می باشد و این مقایسه نمی تواند صحیح باشد. این نتیجه نشان می دهد که به دلیل طراحی هندسی قطعه ریختگی، حبس هوا در داخل حفره ایجاد نخواهد شد.
این موضوع تاثیر هوای حبس شده در سیلندر تزریق و قابلیت شناسایی حرکت غیر ایده آل پلانژر را افزایش خواهد داد. تصویر 11 و 12 نتایج طول قطعه ریختگی و مسافت کلی که ذوب در حفره قالب حرکت کرده را نشان میدهد.
سرعتهای تزریق در فاز دو برای قطعه موجی شکل 3.5 و 5 متر بر ثانیه می باشد. قالب دو حفره با سرعت تزریق فاز دو 2 و 3 متر بر ثانیه شبیه سازی شده است. سرعت تزریق در راهباره برای هر دو قطعه در شبیه سازی حدود 40 متر بر ثانیه برای فاز 1 و 55 متر بر ثانیه برای فاز دوم تزریق می باشد. مشخص می باشد که تغییر سرعت پلانژر و سرعت راهباره در قطعه موجی شکل به ندرت باعث جریان متلاطم در محفظه قالب می شود در حالی که قالب دو محفظهای به وضوح تلاطم جریان در قالب مشهود می باشد.
اگر در یک تحقیق در مورد پارامترهای مختلف تزریق در یک قالب چند محفظه ای از همان محل و موقعیت برای برداشتن نمونه استفاده شود نمی توان دقیقا تشخیص داد چه چیزی خصوصیات مکانیکی را تغییر داده است. اثر مسافت طی شده ذوب، اثرات جریان داخلی و اثر حرکت پلانژر روی هم اثر گذاشته اند و تکفیک علت عیوب دشوار و یا ناممکن خواهد بود. اما این موضوع در مورد نمونه موجی شکل صادق نخواهد بود. توزیع جریان مذاب همیشه ثابت خواهد ماند. شرایط جریان داخلی بسیار یکسان باقی می ماند که این امر با نتایج سرعت شبیه سازی نشان داده خواهد شد.
در این حال تنها اثر خالص منحنی تزریق، زمان توقف در سیلندر و فرآیند تخلیه پیمانه کردن مذاب باقی می مانند.
راهبارههای پهن همانند تصویر6 (چپ) باعث ناهمگنی سرعت های توزیع جریان راهگاه در محل خروجی خواهند شد. به دلیل اصطکاک و فشارهای داخلی نابرابر، سرعتهای بالای جریان در مرکز و سرعتهای پایین تر در لبههای بیرونی ایجاد خواهد شد. تصویر 13 نتایج شبیه سازی با سرعت پلانژر 3.5 متر بر ثانیه درفاز دو را نمایش می دهد.این نوع راهباره رایج و بهینه نشد در شکل 6 باعث ایجاد یک گرادیان سرعتی 17.3 متر بر ثانیه بین مرکز تا لبه خارجی می شود.
توپولوژی راهبار بهینه شده گرادیان سرعت بین مرکز و لبه بیرونی را تا 8.7 متر بر ثانیه کاهش می دهد، که این حدود 50 درصد کاهش می باشد. همچنین راهباره سنتی در ناحیه انتقالی بین ضخامت 2 میلیمتری نوک راهبار و قسمت بسیار ضخیم تر عمقی که به راهگاه متصل می شود موجب ایجاد جریان با آشفتگی بالا می گردد. تصویر 14 نشان می دهد که راهبار بهینه شده نه تنها باعث افزایش یکنواختی سرعت جریان ذوب خروجی از شده بلکه تلاطم داخلی را هم کاهش می دهد.
4- نتیجه گیری
قطعه جدید ریخته گری شده به روش HPDC با هدف افزایش اثر و قابلیت ردیابی منشاء عیوب در سیلندر تزریق به دلیل حرکت نامناسب پلانژر، سرعتهای متفاوت پیمانه کردن مذاب و زمانهای توقف طراحی گردید. قطعه طراحی شده طولی معادل 450 میلیمتر داشته که با این طول، ارزیابی خصوصیات مکانیکی را تحت شرایط بسیار مشابه جریان داخلی امکان پذیر می نماید. به لحاظ این شکل هندسی محفظه قالب از تشکیل جریان جت مانند
در راهبار جلوگیری می کند تا امکان یک رفتار نیمه یک بعدی در پر شدن قالب فراهم شود. تمامی جنبههای طراحی قطعه با هدف حساس سازی بیشتر قالب به عیوب شکل گرفته در سیلندر تزریق، بهینه سازی شده است. این شکل هندسی همچنین اجازه میدهد تا میزان کاهش زمان توقف در سیلندر تزریق یا افزایش سرعت مذاب و پلانژر و در نتیجه نیروهای برشی که بر خصوصیات مکانیکی قطعه دایکست شده موثر است تشریح گردد.
شاید از نقطه نظر صنعتی در اولین نگاه این طراحی جالب توجه نباشد زیرا قطعات دایکست شده دارای تاثرات مختلف از جریان داخلی مذاب هستند لیکن تفکیک ارتباطات داخلی که در ذات فرایند دایکست می باشند امری با ارزش است. در حال حاضر هیچ مدلی که بتواند خصوصیات یک قطعه دایکست شده را پیش بینی کند و چنین دقت مورد نیازی داشته و مرتبط با شرایط صنعتی باشد، وجود ندارد.
پیش بینی خصوصیات یک قطعه دایکست شده دشوار است زیرا اطلاعاتی در مورد نوع و تعداد عیوب شکل گرفته قبل از ورود مذاب به سیستم راهگاهی برای هر تزریق مستقل وجود ندارد. ایجاد یک درک بهتر از مکانیزمهای زیربنایی با استفاده آزمایشی از این طرح جدید شاید اولین قدم برای دور شدن از مطالعات بر پایه سعی و خطا باشد که بسیاری از متغیرها را پوشش می دهد تا نتیجه گیریهای روشنی از فرآیند دایکست حاصل شود.
هدف عمده و فراگیر از این طرح جدید در شرایط کنونی اعتبار بخشی و بهینه سازی نظریهها در خصوص بهینه کردن پارامترها و عوامل فرآیند پیمانه کردن مذاب و عملیات پلانژر و کسب قابلیت تفکیک اثر این عیوب به عنوان تابعی از طول جریان مذاب است. قالب در یک ماشین دایکست افقی با محفظه سرد و قدرت نهایی 500 تن استفاده شده و یک سیستم پیمانه کردن مذاب با تنظیمات دقیق برای وزن هر تزریق پیش بینی شده است.
سیلندر تزریق مجهز به بیش از 20 ترموکوپل گردید و هر اندازه گیری و سیگنال از فرآیند از PLC ماشین دایکست استخراج شده به ثبات دادهها ( OPC-UA )* انتقال می یابد تا امکان کامل ردیابی و ارتباطات در هر سیکل کاری فراهم شود. این تنظیم اجازه می دهد تغیرات در درجه حرارت، زمان توقف در سیلندر تزریق و توزین مذاب تزریقی در کنار ماشین دایکست و سیستمهای جانبی مدیریت گردد.
آزمایشات ریخته گری با این مدل جدید متمرکز بر بررسی روشهای تعیین نقاط بهینه فرآیند تزریق نهایی برای ماشین دایکست با محفظه سرد خواهد بود. نهایی 500 تن استفاده شده و یک سیستم پیمانه کردن مذاب با تنظیمات دقیق برای وزن هر تزریق پیش بینی شده است. سیلندر تزریق مجهز به بیش از 20 ترموکوپل گردید و هر انداز ه گیری و سیگنال از فرآیند از PLC ماشین دایکست استخراج شده به ثبات دادهها ( OPC-UA )* انتقال می یابد تا امکان کامل ردیابی و ارتباطات در هر سیکل کاری فراهم شود.
این تنظیم اجازه می دهد تغیرات در درجه حرارت، زمان توقف در سیلندر تزریق و توزین مذاب تزریقی در کنار ماشین دایکست و سیستمهای جانبی مدیریت گردد.آزمایشات ریخته گری با این مدل جدید متمرکز بر بررسی روشهای تعیین نقاط بهینه فرآیند تزریق نهایی برای ماشین دایکست با محفظه سرد خواهد بود.
*OPC Unified Architecture
منبع خارجی: 2019 .Trans .S.F.A
منبع فارسی: ماهنامه آبان 1402 – صنعت ریخته گری
ترجمه: محسن قورچی (بازرگانی آروین تک)
منابع:
- Faura, F., López, J., Hernández, J., “On the Optimum
Acceleration Law in the Slow Shot Phase of Pressure
Die Casting Machines,” International Journal of Machine
Tools and Manufacture, vol. 41(2), pp. 173–191 (2001).
- Zamora, R., Hernandez-Ortega, J.J., Faura, F., Lopez
J., Hernandez, J., “Experimental Investigation of Porosity
Formation During the Slow Injection Phase in High-Pressure
Die-Casting Processes,” Journal of Manufacturing
Science and Engineering, vol. 130(5), pp. 051009-1−051009-10 (2008).
- Garber, L.W., “Theoretical Analysis and Experimental
Observation of Air Entrapment During Cold Chamber
Filling,” Die Cast Eng., vol. 26(3), pp. 14–22 (1982).
- Laouar, R., Wünsch, O., “Numerical Simulation and
Analysis of Molten Flow in the Shot Sleeve of Die Casting
Process,” Proc. Appl. Math. Mech., vol. 10(1), pp471–472 (2010).
- Barkudarov, M., Pirovano, R., “Minimizing Air Entrainment
in High Pressure Die Casting Shot Sleeves,”
GIFA-Forum, Düsseldorf, Germany (June 2015).
- Frings, M., Berkels, B., Behr, M., Elgeti, S., “Comparison
of Optimization Algorithms for the Slow Shot Phase
in HPDC,” AIP Conference Proceedings, vol. 1960(1),
- 110005 (2018).
- Fiorese, E., Bonollo F., “Plunger Kinematic Parameters
Affecting Quality of High-Pressure Die-Cast Aluminum
Alloys,” Metallurgical and Materials Transactions A, vol47(7), pp. 3731−3743 (2016).
- Hartmann, W., Marcard K., Klein, F., “Thermal- and
Stress Measurements on a Horizontal Cold Chamber,”
Giesserei-Praxis, issue 3, pp. 21−25 (1980).
- Kato, H., Suzuki, T., Annou, Y., Kageyama, K., “Nondestructive
Detection of Cold Flakes in Aluminum Alloy
Die-Cast Plate with Ultrasonic Measurement,” Materials
Transactions, vol. 45(7), pp. 2403−2409 (2004).
- Ahamed, A., Kato, H., “Influence of Casting Defects
on Tensile Properties of ADC12 Aluminum Alloy
Die-Castings,” Materials Transactions, vol. 49(7), pp1621‒1628 (2008).
- Ahamed, A., Kato, H., “Effect of Cold Flakes on
Mechanical Properties of Aluminium Alloy Die Casts,”
International Journal of Cast Metals Research, vol. 21(1-4), pp. 162-167 (2008).
- Gunasegaram, D.R., Givord, M., O’Donnell, R.G.,
Finnin, B.R., “Improvements Engineered in UTS and
Elongation of Aluminum Alloy High Pressure Die Castings
Through the Alteration of Runner Geometry and
Plunger Velocity,” Materials Science and Engineering: A,
vol. 559, pp. 176−286 (2012).
- 13. Fiorese, E., Richiedei, D., Bonollo, F., “Improving the
Quality of Die Castings Through Optimal Plunger Motion
Planning: Analytical Computation and Experimental Validation,”
The International Journal of Advanced Manufacturing
Technology, vol. 88(5-8), pp. 1475−1484 (2016).
مقالات و اخبار
یک نظر در “طراحی یک نمونه ریختگی به روش دایکست برای ارزیابی دقیق منحنی تزریق و اثرات حرارتی بر خواص مکانیکی به عنوان تابعی از طول جریان”
مقاله خیلی خوب بود، کاش یه بخش هم درباره مقایسه دایکست با روشهای دیگه مثل ریختهگری ماسهای میذاشتید تا بهتر بفهمیم چه فرقی دارن.