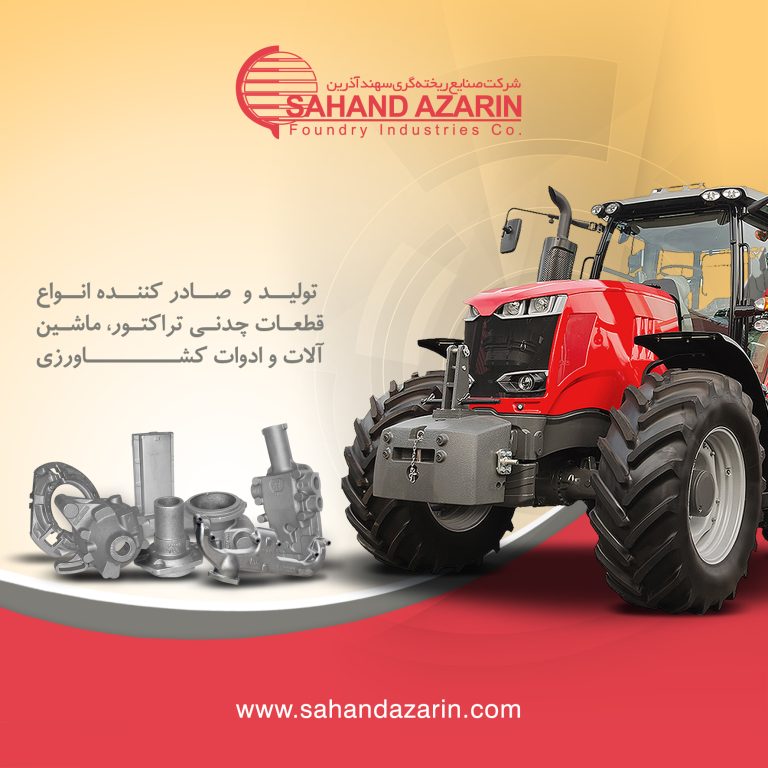
تاثیر جوانه زا بر ریخته گری
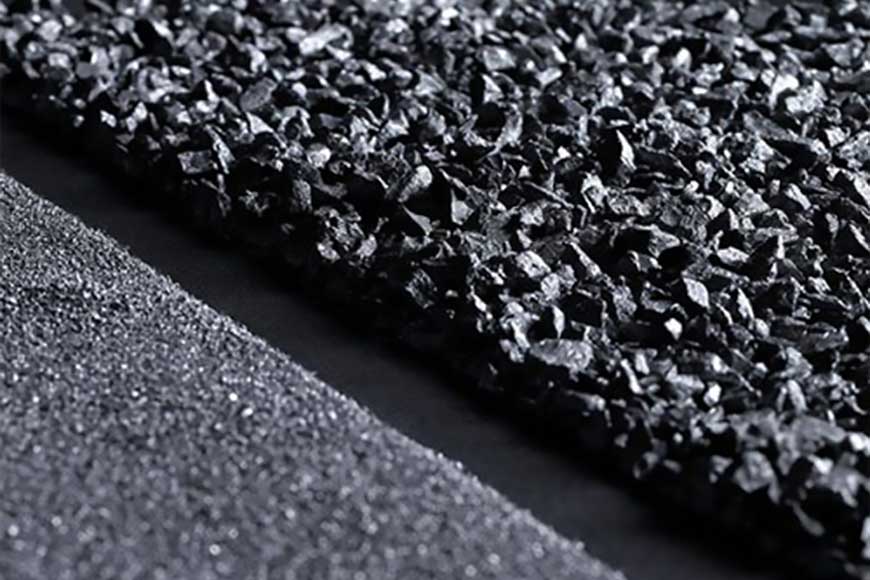
جهت دریافت مشاوره تماس بگیرید.
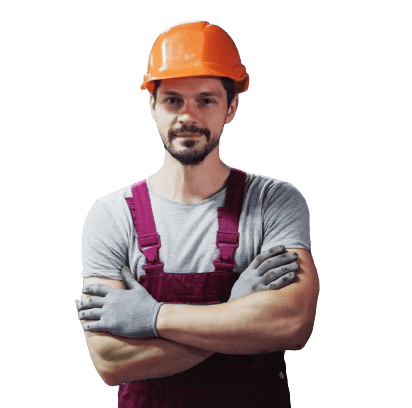
ریخته گری چدن خاکستری با مواد جوانه زا
چدنهای خاکستری آلیاژهای هستند که مبنای آنها سیستم آهن و کربن بعلاوه تعداد دیگری از عناصر است که که مهمترین آنها سیلیس، منگنز، گوگرد و فسفر میباشد. سیستم آهن و کربن داری یک یوتکتیک میباشد و چدن خاکستری طبق یک قانون عمومی بوسیله کربن بالای آن از فولادها متمایز می گردد که باعث ایجاد اجزای یوتکتیک در حالت ریختگی میشود.
ساختار گرافیت در چدن خاکستری ممکن است در اثر تغییرات ذوب ،جوانه زائی، سرعت انجماد و تاثیر بعضی از عناصر هر چند جزئی (ولی بحرانی)تغییر زیادی پیدا کند.
بیشترین مقدار مصرف را در بین چدنها را چدن خاکستری دارد و تولید آن به تنهایی چند برابر دیگر انواع فلزات ریخته گری است. نام این چدن از رنگ خاکستری مقطع شکست آن که خود به دلیل حضور گرافیت ورقه ای می باشد گرفته شده است.
چدنهای خاکستری دارای خواص مکانیکی نسبتاً خوب، قابلیت ماشینکاری عالی، مقاومت مطلوب در برابر سایش و قابلیت بالای جذب ارتعاش هستند.
یک دلیل واضح بر خواص عالی آنها در ساخت قطعات پیچیده نظیر قطعات مصرفی در صنایع اتومبیل سازی، قطعات تراکتورها و… با قیمت تمام شده نسبتاً پایینی می باشد.
هنگامی که ترکیب شیمیایی مذاب در ردیف مربوط به چدنهای خاکستری قرار گرفته و دامنه سرد شدن مذاب در حد معینی باشد کربن موجود در چدن (در جریان انجماد) از مذاب جدا شده و در قطعه جامد شده به صورت ورقه ای شده و به این دلیل نام چدن خاکستری را چدن با گرافیت ورقه ای نیز می گویند.
مشخصات چدن خاکستری بستگی به اندازه، مقدار و نحوه توزیع گرافیت های ورقه ای و سختی نسبی زمینه ای دارد که این گرافیتها روی آن توزیع شده اند. این عوامل عموماً توسط میزان کربن و سیلیسم به همراه میزان سرعت سرد شدن مذاب و قطعات کاهش می یابد.
عملیات تلقیح:
مقدار سیلیسم چدن اولیه به حد کافی پایین نگه داشته می شود تا سیلیسی که از طریق آلیاژ منیزیم و نیز از طریق عملیات تلقیح به مذاب وارد می شود، در مجموع مقدار سیلیسم محتوی را به محدوده مطلوب برساند. مقدار سیلیسم در چدن اولیه در محدوده 1% الی 18% است و این مقدار به نوع آلیاژ منیزیمی که به مذاب اضافه می شود، بستگی دارد.
پایین بودن میزان سیلیسم در چدن اولیه این امکان را بوجود می آورد که به هنگام افزودن آلیاژ منیزیم به مذاب مقداری سیلیسم وارد آن شود و مقداری سیلیسم نیز تا بیش از 6/0% به عنوان ماده جوانه را به مذاب تلقیح شود.
شکل، اندازه و نحوه توزیع گرافیت در چدنها بستگی به تعداد جوانه هایی دارد که قبل از شروع انجماد در مذاب وجود دارد. جوانه زنی و رشد گرافیت بر روی این جوانه انجام یافته و لذا هر قدر تعداد این جوانه ها بیشتر باشد تعداد گرافیتهای ایجاد شده بیشتر شده و در نتیجه این گرافیتها کوچکتر نیز می گردند.
این جوانه ها توسط عناصری که مواد تلقیحی نام دارند تأمین می گردد، در مقادیر 1/0% تا 1% به مذاب چدن افزوده شده (مقدار متداول بین 2/0% تا 5/0% است).
وظیفه مواد تلقیح جلوگیری از ایجاد کاربید آهن و تشویق مراحل گرافیت زایی و کنترل شکل، اندازه و نحوه پخش گرافیت در چدنها است. مصرف این مواد جوانه زا اکثراً محدود به چدنهایی با ترکیب هیپویوتکتیک بوده زیرا تأثیر آنها بر چدنهای هیپویوتکتیک به مراتب کمتر است یا حتی بی تأثیر است.
مصرف مواد تلقیحی علاوه بر خواص گفته شده بالا باعث افزایش استحکام، کاهش عیوب در قطعات ریختگی نظیر حفره های انقباضی و تقلیل مقدار تغذیه های بکار رفته و افزایش سیالیت مذاب می گردد.
دو روش اساسی جوانه زایی وجود دارد، یکی جوانه زنی در پاتیل و دیگری جوانه زنی در آخرین مرحله ممکن در اولی ماده جوانه زا به جریان مذاب ورودی به پاتیل یا بعد از آن زده می شود. جوانه زنی در آخرین مرحله به هر گونه روش تلقیحی گفته می شود که پس از ترک مذاب از پاتیل به قالب است.
مؤثر بودن یک جوانه زا توسط توانایی جوانه زنی در قدرت ماندگاری اثرات آن در طول فاصله زمانی بین تلقیح و تکمیل انجماد یوتکتیک بوده و اندازه گیری می شود.
مزایای جوانه زایی شامل یک تمایل به کاهش تشکیل سفیدی در مقاطع نازک، یکنواختی بیشتر ساختار، اجتناب از گرافیت فوق تبریدی ریز که با مزیت همراه است و از بین بردن گرافیتهای درشت در مقاطع ضخیم می شود. با زدن جوانه زا می توان چدنهای خاکستری مقاوم با کربن معادل کم را بدون ریسک تشکیل سمانتیت ریخته گری نمود.
کاربرد روشهای جوانه زایی در آخرین مراحل به حذف واقعی یا بالقوه میرابی منجر می شود. استفاده از این جوانه زنی باعث مصرف کمتر جوانه زا شده و لذا در هزینه صرفه جویی می شود. از طرفی جوانه زا تغییر کمتری در ترکیب چدن گذاشته و قادر می سازد که از برگشتن بیشتری در شارژ جهت تولید چدن نشکن تلقیح گشته با فروسیلیسم منیزیم استفاده کرده لذا صرفه جویی بیشتر می شود.
زدن جوانه زا در آخرین مراحل خیلی مؤثرتر از جوانه زنی در پاتیل در جلوگیری از تشکیل کاربید در مقاطع نازک بوده و کاهش قابل توجهی نیز در تولید دود و روشنایی خیره کننده به همراه خواهد داشت.
زدن جوانه زا در درون قالب در شکلهای گوناگونی است. جوانه زای پودر شده در حوضچه ریختن یا در لوله راهگاه قرار داده می شود. جوانه زای آسیاب و درجه بندی شده 300-30 مش نیز می تواند در کف لوله راهگاه گذاشته شود. به گونه ای دیگر می تواند به صورت گلوله های به شکل ریختگی نیز به کار برده شود.
عمق سفیدی بدون جوانه زنی بالغ بر mm10 و mm7/3 قابل قبول برای قطعات ریختگی است.
دمای ریختگی روی عملکرد جوانه زا تأثیر گذارده و اندازه بهینه دانه های آن را mm4-1 پیشنهاد می کند. اگر خیلی ریز باشد انحلال اولیه خیلی سریع و تند است و اگر خیلی درشت باشند، انحلال با تأخیری اولیه خواهد بود. مشکل پتانسیل می تواند جوانه زا و آخالها را به داخل قطعه ریختگی بفرستد.
طراحی صحیح سیستم راهگاهی و محفظه می تواند تلاطم را به حداقل رسانده و باعث سادگی انحلال جوانه زا گردد.
در طول انحلال جوانه زا ممکن است آخالهای نامطلوبی تولید شوند جهت جلوگیری از ورود آخال به قطعه ریختگی می توان با بکاربردن صافی هایی با سطح مقطع کشیده (افزایش سطح مقطع باعث کندی حرکت فلز مذاب شده و آخالها را جدا کرده و در خود نگه می دارد) تله های چرخشی گریز از مرکز و تغذیه های گرم در ورودی قطعه ریختگی، باعث عدم ورود آخالها به درون قطعه گردید.
راندمان جوانه زنی می تواند توسط افزایش فوق تبرید و نه بیشتر شدن سطح خمیدگی فصل مشترک و وجود سازنده های فوق تبرید و کاهش در سینتیک آن، بهبود و اصلاح گردد. با بکار بردن هرچه کمتر ماده کروی کننده (بدون کاهش در مراکز جوانه زنی غیر همگن و بدون انحطاط روی کره های گرافیت) می توان از سینتیک فوق تبرید کاست.
جوانهزایی در چدن داکتیل
جوانهزایی در چدن داکتیل فرآیندی است که به موجب آن گرافیتهای کروی در داخل چدن نشکن بهطور یکنواخت توزیع میشوند و ویژگیهای مکانیکی این آلیاژ را بهبود میبخشند.
این فرآیند بهویژه با افزودن عناصری مانند منیزیم به مذاب چدن، باعث ایجاد هستههای ریز گرافیتی میشود که به شکل گویها یا جوانهها رشد میکنند. جوانهزایی، که یکی از مراحل کلیدی در تولید چدن داکتیل است، به کاهش احتمال بروز ترک و شکست در قطعات کمک میکند و از ایجاد تنشهای داخلی در هنگام انجماد جلوگیری میکند.
با استفاده از این تکنیک، چدن داکتیل از استحکام و چقرمگی بالاتری برخوردار میشود که این ویژگیها آن را به گزینهای ایدهآل برای استفاده در صنایع خودروسازی، ماشینآلات سنگین و تجهیزات صنعتی تبدیل میکند. بنابراین، کنترل دقیق فرآیند جوانهزایی در تولید چدن داکتیل به افزایش عمر مفید قطعات و کارایی بالاتر آنها میانجامد.
تأثیر بعضی عناصر روی تلقیح:
وجود Ce در جوانه زاها باعث افزایش تعداد جوانه ها و مقاومت به میرایی است. این امر به دلیل کاهش انرژی در فصل مشترک مایع- گرافیت توسط Ce است.
افزایش Ce با خلق محلهای هسته زنی پتانسیل هسته زایی را می افزاید اما با بالارفتن میزان آن باعث کاهش انرژی فصل مشترک، افزایش در سینتیک فوق تبرید و کاهش فعالیت C در مایع مذاب می شود. وجود Bi تا یک حد معینی در جوانه زا به طور مداوم باعث افزایش تعداد کره ها شده و سپس با بالا رفتن مقدار Bi مورد برعکس شده و از تعداد کره ها گرافیت کم می شود.
این رفتار دو گانه به همکاری آن با سازندهای تحت فوق ترید و نیز کاهش در انرژی فصل مشترک نسبت داده می شود. Bi و sb در غلظتهای کم باعث افت و کاهش زیاد در انرژی فصل مشترک می شوند.
در هنگام استفاده از عناصر تلقیحی بایستی نکات زیر را در نظر داشت:
1- فروسیلیسم 75% ساده ترین نوع جوانه زای مصرفی بوده در حالی که نوع متداول و مناسبتر آن محتوی 1% تا 5/1% آلومینیوم و همین مقدار کلسیم است.
2- اندازه Fe-si در اندازه مناسب انتخاب کرده و در صورتی که کلوخه آن را در اختیار دارید باید آن را خرد کرده و در اندازه حدود ماش یا عدس (mm2 تا mm3) درآورده و سپس مصرف کنید.
3- فروسیلیسم را حدود 2/0% تا 5/0% وزن مذاب لحظه ای قبل از ریختن بار به داخل قالب به مذاب موجود در بوته یا پاتیل افزوده (بایستی قبلاً شیره و شلاکه روی مذاب را گرفته و یا حداقل آن را به طرفی بکشانید) و سریعاً اقدام به ریخته گری مذاب نمایید. در صورتی که فاصله زمانی بین اضافه کردن Fe-si به مذاب و ریختن آن طولانی باشد (معمولاً min10) تأثیر جوانه زایی Fe-si از بین می رود. در اینگونه موارد مواد تلقیحی را در فواصل بارریزی و در چند مرحله زمانی به مذاب چدن بیافزایید.
4- در بعضی از موارد بخصوص در مورد قطعات حجیم و سنگین اضافه کردن مواد تلقیحی ممکن است مضر بوده و نه تنها باعث ریزتر کردن گرافیتها نگردد بلکه آنها را درشت تر سازد. لذا تأثیر مصرف مواد تلقیحی را از طریق مطالعه مقطع شکست قطعات و یا بررسی های میکروسکوپی قبلاً تجربه کنید.
عملیات ذوب و ریخته گری:
برای انجام تلقیح و همچنین بررسی تاثیر ضخامت بر تعداد ، شکل، اندازه و نحوه توزیع گرافیت از مدل گوه ای شکل استفاده شد .بدین ترتیب که از نمونه های گوه ای قالب با ماسه تر تهیه و مذاب از طرف قاعده گوه ریخته شد. ابعاد گوه در قاعده mm25، ارتفاع mm60 و طول mm150 بودند.
زمان حرارت دادن شارژ حدود یک ساعت و 15 دقیقه بود که بعد از این زمان مقدار 250 گرم فروسیلیسم که حدود 2% از وزن کل مذاب بود اضافه و گوه ریخته شد
سپس نمونه با ضربه شکستنه شد و سنگ زنی اولیه در کارگاه صورت گرفت.
متالو گرافی و تحلیل ساختار:
برای بررسی ساختار نمونه و انجام عملیات متالو گرافی عملیات سمباده زنی و براده برداری انجام شد و در دستگاه پولیش دیسکی قطعه پولیش داده شد.
گوه که نمونه تلقیح شده چدن می باشد در نوک شامل گرافیت های نوع D در زمینه ای فریتی بود شکل 4 تا عمق 3 میلیمتری. بعد از این عمق زمینه تماماً پرلیتی و گرافیت ها از نوع A بودند.
عناصر موجود در چدن خاکستری به دو دسته اصلی و جزئی تقسیم می شوند،عناصر اصلی عبارت اند از:کربن، سیلیسیم و آهن از این رو چدن خاکستری را آلیاژی از آهن،کربن و سیلیسیم می دانند.
عناصرجزئی شامل سه عنصرفسفر،گوگرد و منگنز می باشند که فسفر و گوگرد به ندرت بطور عمدی به چدن خاکستری افزوده می شوند.
فسفر تا حدودی موجب افزایش سیالیت می شود و میزان بالای آن موجب افزایش تخلخل های انقباضی می شود،در حالیکه میزان کم آن موجب افزایش نفوز فلز در قالب می شود میزان آن را حدود 0.1-0.02 درصد نگه می دارند.فسفر تا حدود 0.1 درصد در آهن محلول می باشد مقادیر بیشتر آن با آهن ترکیب شده و فسفید آهن Fe3P تشکیل می شود.
این ترکیب با آستنیت و سمنتیت یوتکتیک سه تائی موسوم به استید را بوجود می آورد.نقطه ذوب استدیت بین 980-954 درجه سانتی گراد می باشدکه موجب انجماد آن در آخرین مراحل انجماد چدن ها فسفر دار می شود،در نتیجه در مرز بین سلولهای یوتکتیک تشکیل خواهد شد.
در چدن های خاکستری حاوی 0.2 درصد فسفر یا کمتر استدیت معمولا در مرز دانه ها تشکیل می شود که تاثیر خیلی زیادی روی خواص مکانیکی چدن ندارد ولی با افزایش فسفر از 0.2 درصد به 0.5 درصد،یک شبکه بسته از استدیت در مرز بین سلول ها تشکیل می شود که به علت ترد و شکننده بودن آن ساختار نهایی از قابلیت استحکام،ماشینکاری و مقاومت به ضربه پایینی برخوردار خواهد بود.
مزیت چدن های پر فسفر در افزایش مقاومت به سایش این چدن هاست.این چدن ها در برخی از قطعات که در معرض سایش قرار می گیرند،کاربرد دارند و همچنین از چدن های فسفر دار با میزان فسفر 0.25 درصد در تولید قطعات چدنی با کیفیت سطحی خوب استفاده می شود،از اثرات دیگر فسفر افزایش سیالیت چدن های فسفر دار نسبت به چدن های بدون فسفر می باشد.
همانطوری که در قسمت های قبل اشاره شد،گوگرد یکی از عناصر جزئی موجود در چدن های خاکستری است و در چدن هائی که دارای کمتر از 0.05 درصد گوگرد هستند،بجای تشکیل چدن با گرافیت ورقه ای نوع A امکان بوجود آمدن گرافیت نوع D بیشتر می شود،زیرا واکنش تلقیح گرافیت بخوبی صورت نمی گیرد.
از این رو ساختار زمینه فریت و گرافیت نوع D می شود. باتوجه به اینکه محققان بسیاری نشان داده اند که گوگرد نقش مهمی در هسته سازی گرافیت در چدن خاکستری دارد.از این رو در برخی از ریخته گری ها سعی به تنظیم میزان گوگرد موجود در چدن های خاکستری می شود.
با افزودن مواد گوگرد دار می توان میزان گوگورد چدن را به 0.5 درصد افزایش داد تا اینکه در اثر تلقیح بتوان از عمق سفیدی چدن کاست و ساختا با گرافیت مطلوب به دست آورد،در نهایت می توان نتیجه گرفت که میزان کم گوگرد برای کنترل عمل گرافیت زائی لازم است(0.06 – 0.04 درصد).افزایش گوگرد موجب کاهش سیالیت می شود و همچنین موجب افزایش تعداد شبکه های یوتکتیکی و انقباض می گردد و چنانچه بیشتر از 0.15 درصد باشد ایجاد تخلخل و فرج می نماید.در صورت حضور منگنز،تا حدود زیادی اثرات مضر گوگرد خنثی می شود.همچنین منگنز موجب ظریفت تر شدن ساختار پرلیت و بهبود خواص مکانیکی قطعه ریختگی می شود.
در چدن های خاکستری از عناصر آلیاژی به منظور افزایش استحکام کششی و بهبود بخشیدن به چقرمگی استفاده می شود.
با توجه به تحقیقات بسیاری از محققین در مورد تاثیر عناصر مختلف بر روی استحکام در چدن های خاکستری، می توان نتیجه گرفت که عناصر مولیبدن و وانادیم بیشترین تاثیر را در افزایش استحکام چدن خاکستری دارند ولی از آنجایی که دو عنصر فوق موجب تمایل چدن به سفید شدن می شوند،بهتر است که به همراه آنها از عناصر دیگری مانند:مس و یا نیکل نیز استفاده گردد تا از سفید شدم این چدن ها جلوگیری شود.
افزودن مولیبدن به میزان 0.25 الی 0.75 درصد اثر مهمی بر مقاومت چدن های خاکستری و بهبود ورقه های گرافیت دارد و معمولا در چدن هاب خاکستری از افزودن بیش از میزانی که برای تثبیت پرلیت لازم است خودداری می شود.
در رابطه با بهبود چقرمگی چدن های خاکستری به ترتیب باثیر از زیاد به کم عبارتند زا :(مولیبدن – مس – مولیبدن، نیکل – کرم – قلع – وانادیم – نیکل).در استفاده از قلع توجه به دقیق بودن میزان مصرف خیلی مهم است،زیرا موجب پایداری پرلیت می شود و در صورتی که نیاز به ساختار فریتی بعد از عملیات تابکاری باشد،نبایستی مصرف شود.
همچنین از این عنصر معمولا بصورت خالص و عاری از سرب استفاده می شود تا موجب تنزل خواص مکانیکی نشود.مصرف بیش از حد آن موجب ایجاد زمینه پرلیتی می شود که می تواند تردی و شکنندگی چدن را همراه داشته باشد.
حضور سرب در قطعات ریختگی احتمال ایجاد عیوب را افزایش می دهد.بطوریکه با تغییر در ساخت گرافیت های ورقه ای موجب تنزل خواص مکانیکی و فیزیکی چدن می شود.سرب در چدن های خاکستری موجب ایجاد گرافیت های نامطلوب(غیر نرمال)می شود.این عنصر معمولا توسط مواد شارژ آلوده به سرب وارد مذاب می شود.ساختار گرافیت غیر نرمال مشابه ساختار ویدمن اشتان در قطعات با مقاطع قطور و شبکه بهم پیوسته ورقه ای در مقاطع نازک شده است.
این ساختار ها معمولا در بزرگنمائی کم به سختی قابل مشاهده بوده و فقط در بزرگنمایی های بالا قابل مشاهده هستند.مقاطع قطور قطعه ریختگی نسبت به تاثیر سرب حساس تر هستند،زیرا این مقاطع با سرعت کمتری سد می شوند و همین امر موجب ایجاد جدایش سرب می شود.
مقدار سرب باقی مانده به میزان 0.004 درصد در مقاطع قطور قطعه ریختگی می تواند موجب ایجاد نقص گردد. حضور عناصری مانند:هیدروژن و آلومینیوم(که میزان هیدروژن مذاب را افزایش می دهند)موجب تشدید اثر سرب می شوند،به همین دلیل قطعات ریخته گری شده در قالب های ماسه تر به ایجاد این عیوب در حضور سرب مستعدترند.
بهترین راه برای جلوگیری از آلوده شدن مذاب به سرب استفاده از مواد شارژ تمیز می باشد،زیرا عنصر خنثی کننده ای برای سرب شناخته نشده است.
قلع تا 0.1 درصد موجب افزایش استحکام کششی و سختی می گردد و بیش از 0.1 درصد تولید کاربید می نماید و مقاومت به ضربه را کاهش می دهد.
برخی از عناصر در ایجا خواص یکنواخت در تمامیمقاطع چدن ریختگی مخصوصا قطعات ضخیم موثرند که مهمترین آنها مولیبدن سپس وانادیم،کرم و مس می باشند.البته تاثیر نیکل نیز همانندمس است و توصیه شده است برای حصول نتیجه بهتر از چند عنصر همواره با هم استفاده شود،مانند:افزودن مولیبدن و کرم با هم و وانادیم،مس و کرم باهم و استفاده از مولیبدن،وانادیم و نیکل در تهیه قطعات با مقاطع ضخیم.
به منظور کاهش حساسیت به سطح مقطع قطعه ریختگی از عناصر نیکل ومس که بیشترین تاثیر را دارند استفاده می شود.
برای بالا بردن استحکام چدن در درجه حرارت های بالا که بستگی به عناصر آلیاژی با توجه به ساختار مقاوم به تجزیه شدن آنها در درجه حرارت های بالا دارد،می توان ار عناصری مانند:کرم که بهترین عنصر آلیاژی برای افزایش مقاومت به حرارت در چدن های خاکستری است،استفاده نمود.البته به کاربردن دو عنصر کرم و مولیبدن و همچنین مولیبدن و وانادیم با هم که بیشترین تاثیر را دارند نیز مفید است.
در هنگام استفاده از کرم باید به میزان وجود عناصر دیگر مانند:نیکل توجه نمود،زیرا درصورتی که میزان نیکل موجود در چدن به حدود 1.45 درصد برسد تاثیر کرم کاهش می یابد.زیرا نیکل در کاهش پایداری کاربید و پرلیت تاثیر کمی دارد.
تاثیر عناصر آلیاژی در افزایش سختی قطعات ریختگی چدن خاکستری پس از عملیات حرارتی به ترتیب موثر بودن آنها عبارت اند از کرم،مولیبدن،وانادیم،بر و …(در صورتی که عناصر کرم و مولیبدن با هم استفاده شوند بیشترین تاثیر را دارند.)
در افزایش مقاومت به سایش چدن ها مهمترین عنصر کرم است و در چدن های مقاوم به سایش معمولا از کرم و نیکل بعنوان عناصر آلیاژی استفاده می کنند.
در مورد افزایش مقاومت به ضربه چدن های خاکستری در درجه حرارت های پایین افزودن عناصر آلیاژی وانادیم،نیکل،مس و مولیبدن موثر است.
حضور ازت در چدن های خاکستری موجب پایدار شدن پرلیت و کاربید می شود.در مقاطع ضخیم در مقادیر بیش از 0.008 درصد،بجای گرافیت ورقه ای موجب تشکیل گرافیت قشرده می شود.
مقالات و اخبار
یک نظر در “تاثیر جوانه زا بر ریخته گری”
در چه مرحلهای از فرآیند ریخته گری چدن باید جوانهزاها را به مذاب اضافه کرد تا بیشترین تأثیر را در کنترل ساختار و بهینهسازی خواص مکانیکی قطعه داشته باشد؟