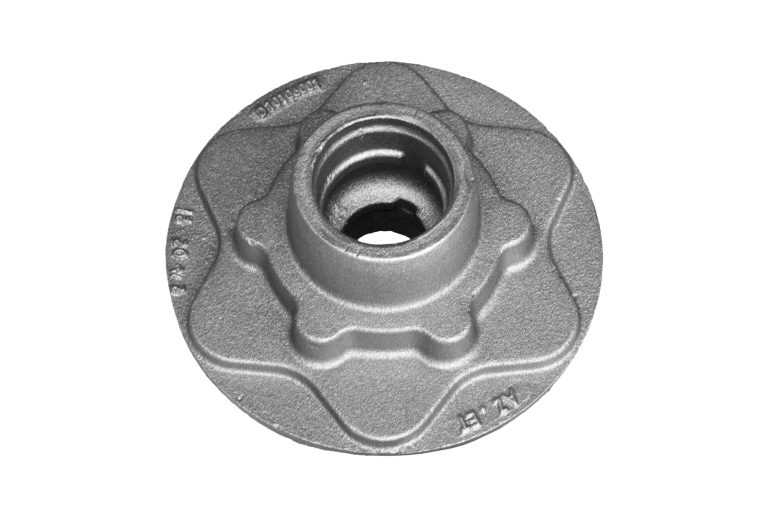
ریخته گری دقیق آلیاژهای منیزیم
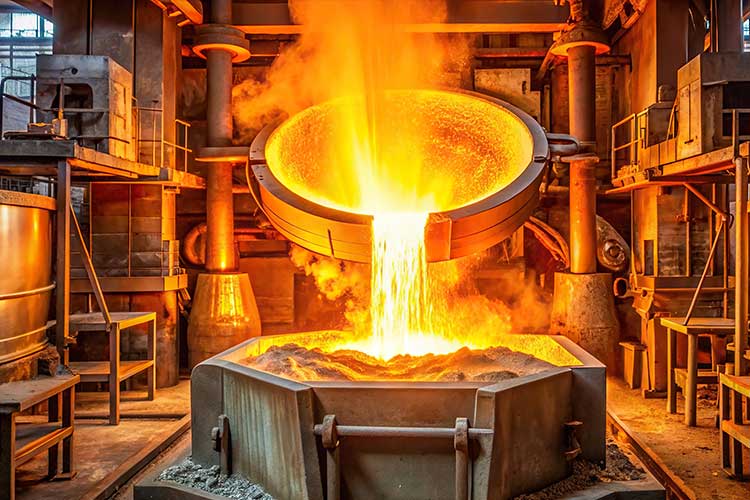
نقشه راه و چالش ها
چکیده
در بخش تولید به دلیل خواص مکانیکی منیزیم همراه با وزن کم فرآوری این آلیاژها به روش ریخته گری یکی از روش های مناسب برای تولید قطعات خودرو و هواپیما می باشد. فرایند ریخته گری دقیق دارای قابلیت زیادی جهت تولید قطعات ریخته گری با اشکال پیچیده و نزدیک به نهایی برای کاربردهای خودرویی و هوافضا است. خواص مهندسی متمایز و جذاب آلیاژ منیزیم آنها را به واسطه پتانسیل شان برای جایگزینی آلیاژهایی نظیر ،چدن فولاد و آلومینیم مطرح نموده است.
در این رابطه با توسعه فن آوری فرایند برای این آلیاژها به جهت دامنه گسترده کاربردها در صنایع توسط جوامع مهندسی در سرشماری سالیانه ریخته گری ارائه شده توسط و علمی تلاش هایی انجام شده است. تولید موفقیت آمیز (AFS (Amencan Foundry Society در ۵ سال اخیر تفاوت قطعات ریخته گری آلیاژهای منیزیم به دلیل خواص فیزیکی وسیعی در تولید آلیاژهای آلومینیم و منیزیم در سراسر جهان و شیمیایی ویژه منیزیم به خصوص طبیعت فعال و اکسیده میتوان مشاهده نمود که در شکل ۱۵ نشان داده شده است.
شونده این آلیاژها نیازمند روش ریخته گری خاصی میباشد. سهم قطعات ریختگی آلومینیم از تولید کل قطعات ریخته گری البته باید توجه داشت که این صنعت برای بالقوه شدن هنوز در سراسر جهان ۱۵ درصد بوده در حالی که در سال ۲۰۲۰ سهم جوان و نوپا است.
1- مقدمه
صنایع خودرویی بر پتانسیل کاربردهای مواد سبک متمرکز می باشند. آلیاژهای آلومینیم به واسطه کاربردها بسیار جلوتر از آلیاژهای منیزیم میباشند.
اگرچه آلیاژهای منیزیم دارای قابلیت ریخته گری خصوصیات ماشین کاری قابلیت اصلاح مقاومت به کاهش در تولید منیزیم ریختگی ممکن است ناشی از عوارض خوردگی، نسبت استحکام به وزن بالاتر عملکرد در درجه حرارت بالاتر و پتانسیل بازیابی بیشتر بسیار مناسب هستند.
در سرشماری سالیانه ریخته گری ارائه شده توسط (AFS (Amencan Foundry Society در ۵ سال اخیر تفاوت وسیعی در تولید آلیاژ های آلومینیوم و منیزیم در سراسر جهان میتوان مشاهده نمود که در شکل 1a نشان داده شده است.
سهم قطعات ریختگی آلومینیم از تولید کل قطعات ریخته گری البته باید توجه داشت که این صنعت برای بالقوه شدن هنوز در سراسر جهان ۱۵ درصد بوده در حالی که در سال ۲۰۲۰ سهم تولید قطعات ریختگی منیزیم تنها ۰٫۳۵ درصد آلومینیم بوده است. (شکل ۱b)
آینده منیزیم در صنعت خودرو توسط Miller در سال ۱۹۹۹ (شکل (۲) پیشنهاد گردید و پیش بینی شده که آلومینیم یا منیزیم به در دو یا سه دهه آینده پیشگام خواهند شد. (۲)
کاهــش در تولیــد منیزیــم ریختگــی ممکــن اســت ناشــی از عــوارض فراینــد یــا فقــدان دانــش فنــی آنهــا باشــد. بــه هرحــال ایــن یــک حقیقت است که شرکت فولکس واگن حتی پیش از جهانی جنگ دوم در Beetle از آلیاژهای منیزیم استفاده کرده بود. (۳)
۲- نقشه راه برای توسعه ریخته گری منیزیم
نگرانی اصلی میتواند توسط حضور آهن آلومینیم ریختگی برای فرایند ریخته گری ماسه ای مرسوم اگرچه تولید اقتصادی تبدیل به ریخته گری منیزیم به صورت تصویری نقشه راه را که در حجم پایین را تامین کرده لیکن کیفیت سطحی و دقت در شکل ۳ نشان داده شده عنوان شود.
بر اساس سرشماری AFS ابعادی ضعیفی را ارایه می نماید. در حالیکه پیامدهای مربوط کشورهای عمده تولید کننده منیزیم ایالات متحده ایتالیا، آلمان به تشکیل تخلخل طی ریخته گری پرفشار (دایکست) و هزینه انگلستان، روسیه و کانادا هستند کشور هند نیازمند اعتماد بر بالای آن استفاده گسترده را محدود می سازد.
این کشورها برای منیزیم به صورت خالص یا به شکل شمش می باشد. علاوه بر این در دسترس بودن شمش های فلزی با کیفیت ذاتی نیز مهم است. حضور اکسیدها در شمش های منیزیم تشکیل سرباره طی ذوب کردن را افزایش داده که به تشکیل عیوب ریختگی منجر میشود.
فرایند کار با منیزیم به دلیل طبیعت واکنش پذیر و احتراقی خطرناک است. آگاه بودن از خطرات و پذیرش ایمنی برای ذوب کردن انتقال مذاب و ریخته گری به منظور حذف خطرات بروز حادثه اهمیت دارد. از نقطه نظر زیست محیطی، نشر گازهای گل خانه ای و روانسازهای مورد استفاده حین ذوب کردن و انتقال مذاب منیزیم نیز باید کاهش باید جنبه های هندسی مانند. جداره نازک یا ضخیم همچنین انتخاب مواد پوشش دهنده سطح نهایی قالب نفوذپذیری قالب و استحکام قالب در توسعه آن باید مورد توجه قرار گیرد. (۴-۶)
در جدا کردن سیستم راهگاهی و تمیزکاری اجتناب از سوختن براده ها و پلیسه ها باید مورد توجه قرار گیرد روش های بازیابی به طور کلی منیزیم و آلیاژهای آن در محدوده دمایی مناسب باید توسعه یابد زیرا افزایش میزان اکسید طی فرآیند ۶۵۰ تا ۷۵۰ درجه سانتی گراد ذوب میشوند ولی سوختن و حقیقت است که شرکت فولکس واگن حتی پیش از جنگ ذوب و ذوب مجدد منجر به تنزل کیفیت می گردد.
3- چالش های توسعه ریخته گری دقیق آلیاژ منیزیم
رای فرایند ریخته گری ماسه ای مرسوم اگرچه تولید اقتصادی تبدیل به ریخته گری منیزیم به صورت تصویری نقشه راه را که در حجم پایین را تامین کرده لیکن کیفیت سطحی و دقت در شکل ۳ نشان داده شده عنوان شود. بر اساس سرشماری AFS ابعادی ضعیفی را ارایه می نماید. در حالیکه پیامدهای مربوط کشورهای عمده تولید کننده منیزیم ایالات متحده ایتالیا، آلمان به تشکیل تخلخل طی ریخته گری پرفشار (دایکست) و هزینه انگلستان، روسیه و کانادا هستند کشور هند نیازمند اعتماد بر بالای آن استفاده گسترده را محدود می سازد.
به نظر میرسد نیاز روشنی برای توسعه فرایند ریخته گری دقیق جهت دستیابی به تقاضای فعلی به منظور تولید اقتصادی قطعات پیچیده با دقت بالا و تعداد کم وجود دارد.
صنایع ریخته گری دقیق با مشکلات متعددی طی ذوب و ریخته گری آلیاژ منیزیم مواجه هستند. دلیل اصلی این امر میل ترکیبی بالای منیزیم به اکسیژن است. بر خلاف الومينيوم طی ذوب کردن منیزیم، باید از تماس آن با اکسیژن در هوا جلوگیری نمود زیرا به سرعت اکسید شده و شعله های خطرناک ایجاد میکند.
به جز این موضوع در مورد ریخته گری دقیق واکنش های ناحیه فصل مشترک مذاب قالب موانعی برای تولید موفق قطعات ریخته گری هستند. بنابراین در ذوب و ریخته گری آلیاژهای منیزیم استفاده از گاز محافظ یا اعمال فلاکس (روانساز) ضروری است.
1-3- محافظت طی عملیات ذوب
بــه طــور کلــی منیزیــم و آلیاژهــای آن در محــدوده دمایــی 650 تــا 750 درجــه ســانتی گراد ذوب می شــوند ولــی ســوختن و اکسیداسیون این آلیاژها در درجه حرارتهای بالاتر مشاهده شده است. فشار بخار بالای منیزیم در درجه حرارت های بالاتر موجب آغاز اشتعال میشود. بنابراین یک محیط محافظت شده طی ذوب و ریخته گری به جهت جلوگیری از اشتعال و در نتیجه سوختن و اکسید شدن ضروری است.
(۷) علی رغم توسعه بسیاری از روشهای امروزی ذوب کردن بدون فلاکس (روانساز) برای ایجاد یک محیط محافظ بسیاری از کارخانجات ریخته گری هنوز از روان سازهای مرسوم طی ریخته گری استفاده میکنند ترکیبات شیمیایی فلاکس به طریقی باید باشد که بیش از ذوب شدن فلز مذاب ذوب شده و بر روی سطح مذاب شناور گردد.
تا سطح مذاب را از اتمسفر محافظت نماید. علاوه بر این فلاکس ذوب شده باید ضخیم بوده و به اندازه کافی گران روی (ویسکوزیته) داشته به اصطلاح inspissation یا غلظت فلاکس می باشد (۸) در ابتدا فلاکس با ترکیب شیمیایی MgC و KC برای جلوگیری از اکسیداسیون و سوختن استفاده شده است.
سپس کاربرد فلورین حاوی ترکیباتی به شکل مخلوط روانساز به عنوان یک عامل مقاوم به ذوب شدن و اکسیداسیون اثبات شده است. افزودن ترکیباتی نظیر فلوئور منیزیم (MgF2)، فلوتور سدیم (NaF) یا فلوئور پتاسیم (KF) کشش سطحی را کاهش داده و قابلیت خیس شوندگی بین مذاب و فلاکس افزایش یافته و تشکیل فیلم اکسیدی محافظ را تسهیل می سازد که از اکسیداسیون بیشتر مذاب جلوگیری نماید. (۹-۱۱)
استفاده از مخلوط گاز طی ذوب و ریخته گری به عنوان یک قالب ها در ریخته گری دقیق ابتدا با مواد اکسید نسوز سرامیکی روش ذوب کردن بدون فلاکس مطرح گردیده و مخلوط So2 و تهیه شده اند. طی انجماد واکنش ها در فصل مشترک قالب هوا متداول ترین روش بدون فلاکس در زمان های گذشته بوده است.
طبیعت سمی و خورنده این گاز کاربرد آن را در صنایع ریخته گری محدود کرده و نیاز به اعمال برخی گازهای دیگر را مطرح شده است. اعمال گازهای خنثی نظیر دی اکسید کربن آرگون نیتروژن به عنوان گاز حامل با مقدار کمی از هگزافلورید گوگرد توسط بسیاری از محققین نیز گزارش شده است. نتیجه گرفته شده مخلوط ۲ درصد تا ۴ درصد SF با CO به عنوان یک روش بدون فلاکس برای ذوب منیزیم عمل میکند. (۱۲)
عملکرد محافظتی فلاکس ها میتواند توسط عامل Pilling and Bedworth تشریح گردد. این ضریب حجم سلول اولیه اکسید فلزی به حجم سلول اولیه فلز مربوطه که اکسید را تشکیل می دهد بوده است.
میزان بزرگ تر از یک بودن این ضریب مبین تشکیل بهتر فیلم پیوسته و چگال بر سطح مذاب است.
ضرایب Pilling and Beaworth برای فیلم های گوناگون در جدول ا ارائه شده است. از این جدول میتوان نتیجه گرفت که بهترین محافظت مذاب از اکسیداسیون را فیلم های حاوی فلورین ارائه میدهند.
2-3- واکنش فصل مشترک مذاب – قالب در جریان ریخته گری دقیق
قالب ها در ریخته گری دقیق ابتدا بـا مواد اکسید نسوز سرامیکی تهیــه شـده اند. طی انجماد، واکنش ها در فصــل مشــترک قالب- فلز ناشی از میل ترکیبی قوی فلز منیزیم با اکسیژن رخ داده زیرا قالب ها از مواد اکسیدی هستند. این واکنش ها باعث سوختن قطعات ریخته گری گردیده و کیفیت به دلیل لایه های اکسیدی (MgO) بر سطح قطعه ریخته گری تخریب می شود. طی فرایند ریخته گری اکسیژن قالب میتواند تجزیه و در داخل مذاب حل شود. این اکسیژن حل شده در مذاب سختی سطح قطعه ریخته گری منجمد شده را افزایش داده و موجب ضايع شدن قطعه ریخته گری می گردد.
واکنش های فصل مشترک در ریخته گری دقیق آلیاژها و فلزات فعال می تواند به صورت کلی به شرح زیر طبقه بندی شود. :(۱۴)
1- تجزیه مواد قالب در حضور فلز مذاب به شدت فعال و واکنش مذاب با عناصر حل شده قالب
2- تشکیل یک لایه نازک از ترکیبات واکنش بر سطح قطعه ریخته گری توسط واکنش بین قالب و فلز در فصل مشترک
3- واکنش فلز با اتمسفر محفظه قالب یا با هر گازی که در محفظه قالب حضور دارد
4- نفوذ مذاب به داخل قالب که به یک کیفیت سطحی ضعیف قطعه ریخته گری منجر می شود
5- واکنش فلز مذاب با اتمسفر طی انجماد
3-3- پایداری اکسیدهای سطحی در برابر واکنش ها عنوان
اکسیدهای سرامیکی برای مواد مخلوط (دوغاب) اولیه پوشش عناصر سطحی در قالب های ریخته گری دقیق به کار می روند. به سیلیکات زیر کنیم (ZrSiO4) یک مورد مرسوم مورد استفاده در به کارخانجات ریخته گری دقیق است.
این پوشش سطحی برای به تولید قطعات ریخته گری پیچیده نزدیک به شکل نهایی به طور موفقیت آمیزی اثبات شده اند (۱۵) به هر حال طی ریخته گری آلیاژهای فعال نظیر منیزیم یا تیتانیم مشاهده را شده این پوشان سطحی به دلیل واکنش با مذاب نمیتواند آلیاژ کیفیت سطحی خوبی ایجاد نماید. مصرف برخی اکسیدهای شده سرامیکی جدیدتر به عنوان مواد پوشان سطحی برای این آلیاژ را همراه با قابلیت ریخته گری بهبود می بخشد. (۲۲)
ریخته گری آلیاژهای فعال مورد نیاز است. اکسیدهای سرامیکی دیگر از قبیل , Al, ro MgO و Cao و غیره وجود دارد که میتوانند به عنوان مواد دوغاب برای پوشان سطحی به کار روند. این اکسیدها باید از نظر حرارتی و شیمیایی در درجه حرارت های بالا پایدار باشند تا واکنش هایی که با فلز مذاب از تجزیه مواد قالب رخ میدهد حذف یا جلوگیری شود.
پایداری اکسیدها از دیدگاه نظری میتواند توسط انرژی آزاد کییس تشکیل ترکیبات بررسی شود. تغییر انرژی آزاد گیبس برای تشکیل ترکیبات در درجه حرارت های بالا مربوط به اکسیدهای مختلف در نمودار الینگهام در شکل ۴ نشان داده شده است. ترکیباتی مانند CaO و MgO که دارای مقادیر تغییرات انرژی آزاد گیبس منفی تری برای تشکیل ترکیب بوده پایدارتر هستند. اکسیدهای غیر مرسوم متعددی مثل ALO CaO 20,0 CarO MgO و غیره به عنوان مواد پوشان به جای Zrsio متداول استفاده شده اند که برخی از آنها برای جلوگیری از واکنش های قالب و مذاب موثر بوده اند. البته باید توجه داشت نتایج با پایداری تئوریک پوشان های سطحی در برخی موارد سازگار نیست (۲۰۱۷)
4 – آلیاژهای منیزیم و کاربردهای آن
به طور کلی استفاده از منیزیم خالص برای کاربردهای تجاری امکان پذیر نیست زیرا بسیار ضعیف بوده و دارای استحکام کششی نهایی پایینی است. طبق استاندارد ASTM ، آلیاژهای منیزیم میتوانند به سه دسته اصلی آلیاژهای آلومینیوم منیزیم روی منیزیم و آلیاژهای عناصر نادر خاکی منیزیم تقسیم شوند.
در گروه اول سری AZ و AM به طور گسترده ای در کاربردهای خودرویی و هوافضا به کار رفته که به ترتیب عنصر ثانویه Zn و M می باشند. این آلیاژها حاوی ۱۰۰۸ درصد آلومینیم به عنوان عنصر آلیاژی اصلی هستند. برای گروه دوم سری 2K الیاژهای منیزیم شناخته شده ترین بوده که عنصر روی تا ۸ درصد به عنصر اصلی آلیاژی اضافه شده است.
در گروه سوم EK EZ. QE و WE (الکترون) گروه های شناخته شده بوده که در آنها نادر خاکی از قبیل سریم توریم زیر کنیم، ایتریم و غیره عنوان عنصر آلیاژی استفاده شده اند. آلیاژهای سری AZ طور گسترده ای برای ترکیب بهینه استحکام و چکش خواری کار می روند. این آلیاژها به خاطر تشکیل AIO در فیلم سطحی این آلیاژها دارابی مقاومت به خوردگی خوب هستند. افزایش در مقدار Al و Zn ، سیالیت و در نتیجه قابلیت ریخته گری افزایش میدهد (۲۱)
بنابراین منیزیم AZ91 به عنوان یک قابل ریخته گری با ۹ درصد آلومینیم و ادرصد Zn ملاحظه است. افزودن Si در یک مقدار کوچک مقاومت به خزش سرامیکی جدیدتر به عنوان مواد پوشان سطحی برای این آلیاژ را همراه با قابلیت ریخته گری بهبود می بخشد. (۲۲)
اکثر کاربردهای آلیاژهای منیزیم در صنایع خودرویی، هوافضا و بخش های مهندسی پزشکی مشاهده شده است (۲۳) نمونه های کمی از قطعات ریخته گری منیزیم تولیدی در وسایل نقلیه توسط تولید کنندگان خودرو در جدول ۲ ارائه شده است. (۲۶-۲۴)
مقاومت به خزش دمایی بالاتر و مقاومت به خوردگی بیشتر آلیاژهای منیزیم را برای کاربردهای هواپیمایی مناسب ساخته است. قطعات ریخته گری منیزیم در کاربردهای فضایی گوناگون در جدول ۳ فهرست شده است (۲۷).
امروزه تقاضا برای آلیاژهای ریخته گری منیزیم در کاربردهای مهندسی پزشکی در حال افزایش است. چگالی و مدول الاستیک مشابه با یافت استخوان انسانی از اثر تنشی کاهش چگالی استخوان ایجاد شده توسط ایمپلنت های معمولی جلوگیری می کند. ایمپلنتهای ارتوپدی منیزیم حامل بار تجزیه پذیر در بدن باقی مانده و طی یک دوره زمانی ۱۲-۱۸ هفته به صورت یکپارچه حذف میشوند در حالیکه احیای بافت استخوانی به طور کلی توسط بافت طبیعی جایگزین میشوند (۲۸-۲۹)
5 – نتایج و تصویر آینده
مرور مقالات در مورد حوزه اصلاح توسعه تولید قطعات ریخته گری دقیق با کیفیت از الیاژهای منیزیم فعال گشوده شده است. مهندسان ریخته گری که با ریخته گری دقیق آلیاژهای منیزیم سروکار داشته اند با مشکلات مربوط به واکنش های فصل مشترک قالب ٫ مذاب مواجه شده اند. لازم است موارد زیر تشریح گردد.
5-1- تعیین و توسعه روشهای ذوب و ریخته گری با هزینه پایین که موجب گرمایش کلی نشود
5-2- بررسی اثر هندسی قطعه ریخته گری بر واکنشهای فصل مشترک
5-3- جستجوی کاربردهای امکان پذیر بر پوشان های اکسیدی سرامیکی غیر متداول برای جلوگیری از واکنش ها
منبع فارسی: ماهنامه شهریور 1402 – صنعت ریخته گری
منبع خارجی: Archives Foundry Engineering Issue 4٫2022
ترجمه: علیرضا سلطانی
منابع:
[1] Kulekci, M.K. (2008). Magnesium and its alloys applications in automotive industry. The International Journal of Advanced Manu- facturing Technology. 39(9), 851-865. DOI: https:٫٫doi.org٫10.1007٫ s00170-007-1279-2
[2] Miller, L. (1999), Casting the new millennium. Proceedings 31st Australian Foundry Institute Convention. Wollongong, NSW, Key- note Address. (p.14) ARCHIVESotFOUNDRYENGINE ERING Volume22.Issue4٫2022,19-23 23
[3] Avedesian, M.M. & Baker, H. (1999). Magnesium and magne- sium alloys. ASM Speciality Handbook Series. ASM International, Materials Park, Ohio, USA,
[4] Vyas, A.V. & Sutaria, M.P. (2021). Investigation on influence of the cast part thickness on interfacial mold-metal reactions during the investment casting of AZ91 magnesium alloy. International Jour- nal of Metalcasting. 15(3), 1021-1030. DOI https:٫٫doi.org٫10.1007٫ 540962-020-00530-2
[5] Vyas, A.V. & Sutaria, M. (2020). Investigation on reactions at comers of cast part during investment casting of reactive AZ91 Magnesium Alloy. Archives of Foundry Engineering. 20(4), 139-144. DOI: 10.24425٫afe 2020, 133360.
[6] Vyas, A.V., Ayar, V.S. & Sutaria, M.P. (2020), Investigation on reactive wetting during investment casting of magnesium alloy AZ91. Materials Today: Proceedings. 26. 2452-2457. DOI: https:٫٫ doi.org٫10.1016٫j.matpr 2020.02.521.
[7] Kumar, N.R., Blandin, J.J., Suery, M. & Grosjean, E. (2003) Effect of alloying elements on the ignition resistance of magne- sium alloys. Scripta Materialia. 49(3), 225-230. DOI: https:٫٫doi. org٫10.1016٫S1359-6462(03)00263-Χ.
[8] Allen, F. & Brace, A. (1957) Magnesium Casting Technology. Reinhold Publishing Corporation, New York.
[9] Jafari, H., Idris, M.H., Ourdjini. A. & Farahany, S. (2013). In situ melting and solidification assessment of AZ91D granules by computer-aided thermal analysis during investment casting process Materials and Design. 50, 181-190. DOI: https:٫٫doi.org٫10.1016٫j. matdes.2013.02.035.
[10] Jafari, H., Idris, M.H., Ourdjini, A. & Kadir, M.A. (2012). Effect of flux on in-situ melting shell investment casting of AZ91D magnesium alloy, In international Conference on Thermal Material and Mechan ical Engineering (ICTMME 2012), July, 15-16.
[11] Jafan, H.. Idris, M.H., Curdjini, A. & Kadir, M.R.A. (2013). Infiu- ence of flux on melting characteristics and surface quality of in-situ melling AZ910. Materials and Manufacturing Processes. 28(2), 148- 153. DOI: https:٫٫doi.org٫10.1080٫10426914.2012.746787.
[12] Pettersen, G., Ovrelid, E., Tranell, G., Fenstad, J. & Gjestland, H. (2002), Charactensation of the surface films formed on molten magnesium in different protective atmospheres. Materials Science and Engineering. A. 332(1-2), 285-294, DOI: https:٫٫doi.org٫10.1016٫ 50921-5093(0101750-6.
[13] Friedrich, H., Mordike, B. (2006). Magnesium Technology Metallurgy. Design Data, Applications. Springer Berlin, Heidelberg. https:٫٫doi.org٫10.1007٫3-540-30812-1.
[14] Piwonka. T.S. (1994). Reactions at the mold٫metal interface in
مقالات و اخبار