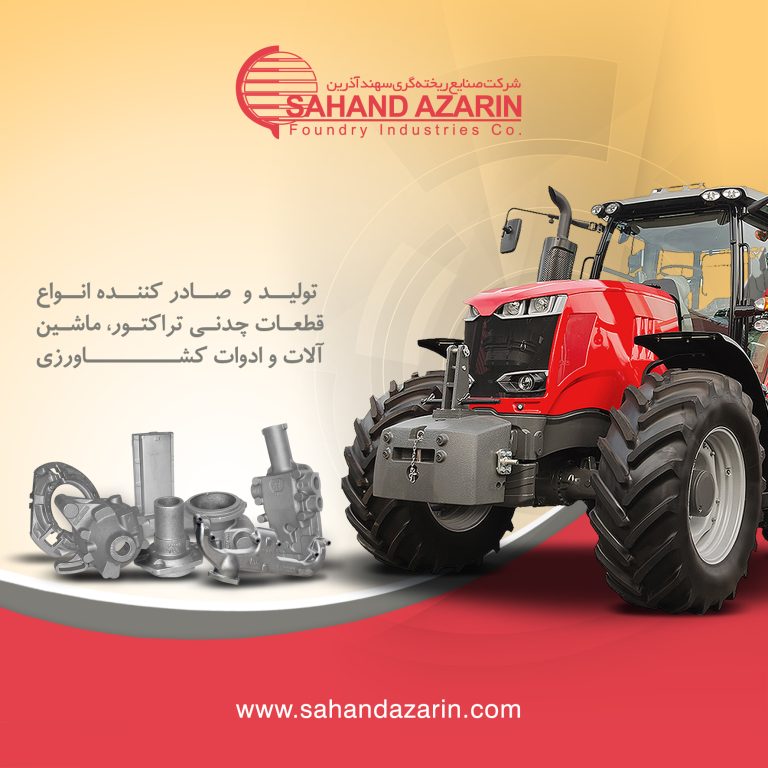
خانه » مقالات » ریخته گری پیستون های موتورهای احتراقی در گذشته و امروزه در ریخته گری Gorzyce FM لهســتان
ریخته گری پیستون های موتورهای احتراقی در گذشته و امروزه در ریخته گری Gorzyce FM لهســتان
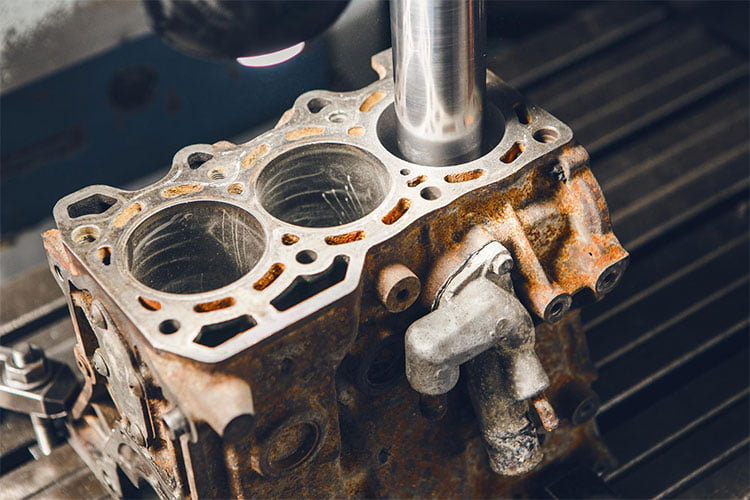
منبع: ماهنامه شهریور 1402 – صنعت ریخته گری
منبع مقاله: 2/2023 Issue Engineering Foundry of Archives
ترجمه: عبدالحمید قدیمی
چکیده
در تحقیق حاضر مهمترین تغییرات ماشین های ریزه ریزی و همچنین روش ریخته گری پیستون ها و ساختار آن ها در شرکت ریخته گری Federal-Magul (FM) Gorzyce تشریح شده است.
سیستم اتوماتیک سرد شدن در ماشین ریژه ریزی روبات های بار ریز در شرایط کنونی موجب اطمینان از تبلــور و انجماد یکنواخت پیستون ها و بهره وری بهینه فرآیند می گردد.
به عنوان نتیجه ضرورت ارتقای راندمان و موتورهای احتراقی و در نتیجه کاهش مصرف سوخت مواد آلاینده در ساختار پیستون ها تغییراتی ایجاد شده در طول سال ها پیستون ها که در قالب های ریژه فلزی به تقلی ریخته گری می شوند دچار یک تحولات اساسی گردیده است.
طرح های معمول پیستون برای موتورهای بنزینی و دیزلی در بخش های مهم مانند تاج در تماس با محفظه احتراق و قسمت هادی (پوسته) هر دو نشان داده شده متناسب با نوع موتور پیستون های امروزی اشکال قسمت تاج یک ساختار داخلی ظریف در قسمت کانال خنک کن و رینگ های قرار گرفته شده داشته و پوسته بیرونی پیستون نیز تحت فرآیندهای خاص قرار می گیرد.
۱- مقدمه
الزامات برای پیستون های موتورهای احتراقی در سال های اخیر به طور نظام مند در حال افزایش است. علت این امر عمدتاً مرتبط با افزایش بارهای ترمو مکانیکی و همچنین نشر کمتر گازهای احتراق و کاهش سوخت مصرفی میباشد.
نیاز به کاهش وزن خودرو و افزایش سرعت دورانی موتور موجب یک افزایش متوسط و حداکثر فشارهای محفظه کاری احتراق و نیروهای مربوط به اینرسی گشته است.
این انتظارات از طریق راه حل های مختلف در درون موتور تامین می شود. این موارد شامل افزایش مقادیر درجه حرارت و فشار در سیلندرها بوده که باعث بالاترین الزامات برای قلب احتراق موتور یعنی پیستون است. خواهد شد.
پس جنگ جهانی دوم شرکت WSK برای تولید تجهیزات و وسایل حمل و نقل در لهستان ایجاد شد که در آن قطعات ریختگی از آلیاژهای آلومینیم، منیزیم و مس برای صنایع خودرو و هواپیما تولید میگردید.
در دهه ۷۰ میلادی شرکت WSK از آلیاژهای Al SIM شروع به تولید رینگ خودرو نمود.
از دهه ۸۰ در واحد Gorzyce پیستون و اجزای آن شامل بین و رینگ نمود.
در سال ۲۰۰۱ شرکت WSK Gorzyce توسط Power train-Mogul- Federal خریداری شد و در شرایط کنونی تحت تملک FMG) Tenneco) قرار دارد.
در ابتدا ریخته گری در قالب های ریژه به روش نقلی با سیستم عمودی انجام می شد. قالب های تک بر روی ماشین های ریخته گری قرار گرفته و پر شدن قالب با استفاده از پاتیل های ویژه به صورت دستی انجام میگردید.
شکل (۱) تبلور و انجماد فلز در قالب ریزه مجهز به سیستم های ساده سرد شدن مهمترین اجزاء یعنی ماهیچه اصلی و ماهیچه های بین بوده که جهت انجماد قطعه ریختگی را به سمت کله تغذیه در مقطع بالایی هدایت می کند. آلیاژ استفاده شده برای پیستون موتورهای بنزینی و دیزلی عمدتاً سیلومینAISI12 (۶ تا ۱) بوده است.
اجزای قالب ریزه قدیمی عمدتاً متشکل از ماهیچه اصلی ماهیچه های بین بلوک های دایکست و ماهیچه بالایی است.
در فاصله دهه ۸۰ و ۹۰ میلادی کم کم ماشین های پیستون ریزی مدرن شد هر چند که هنوز به صورت تک محفظه بودند. پس از عملیات مکانیکی پوسته بیرونی پیستون ها با هیچ لایه محافظ پوشش داده نمیشود. در شکل های ۳ و ۴ نمونه هایی از پیستون موتورهای احتراقی بنزینی و دیزلی با طرح قدیمی ارائه شده است.
پس از برش سیستم راهگاهی پیستون تحت عملیات حرارتی و عملیات مکانیکی قرار میگرفت تا به شکل و ابعاد نهایی برسد.
۲- هدف تحقیقات
هدف مطالعات تعیین تغییرات اصلی در ساختار ماشین ریزه ریزی و ریخته گری پیستون موتورهای احتراقی یا آلیاژ سیلومین در یک دوره ۵۰ ساله در ریخته گری بوده است اهداف این مطالعات Federal Mogul – Gorzyce عبارتند از:
۲-۱- دو تشریح تغییرات ساختار ماشین های ریخته گری و قالب های ریژه ریزی برای ریخته گری پیستون ها از آلیاژ سیلومین.
۲-۲- مدرن کردن سیستم های خنک کردن اجزای اصلی قالب ریژه.
۲-۳- تغییرات در ساختار پیستون های موتورهای بنزینی و دیزلی.
۳- توسعه ماشین های ریخته گری
در حال حاظر ایستگاه های کاملا اتوماتیک ریخته گری با ریخته گری مداوم پیستونها هماهنگ گردیده است. پیمانه کردن دقیق مذاب و قرار دادن اجزای پیستون در قالب ریژه ماشین ریخته گری مانند رینگ ماهیچه های نمکی و تخلیه قالب به وسیله ربات ها انجام میشود شکل (۵) ماشین های ریزه ریزی مجهز به یک سیستم هیدرولیک با باز و بسته کننده های اتوماتیک عناصر خاص قالب ریژه هستند. دارا بودن سیستم کمپلکس خنک کردن دستگاه زمان بندی تبلور و انجماد پیستون را یکنواخت کرده و بهره وری فرآیند را ارتقاء داده است.
ماشین های ریزه ریزی مجهز به دو قالب ریژه (یک قالب در هر طرف) بوده که این امکان فراهم میشود دو عدد پیستون هم زمان تولید گردد (شکل ۶)
بر اساس شکل ۶ یک قالب ریژه بیستون دارای ۸ مدار خنک کننده و مجهز به چندین شیر الکتریکی با کنترل برنامه ریزی شده است.
این امکانات موجب یکنواخت شدن سرد شدن پیستون های ریختگی به همراه باز و بسته شدن اتوماتیک قالب های ریژه در زمان و درجه حرارت های تنظیم شده خواهد شکل کلگی پیستون تعیین کننده روش چرخش مخلوط هوا و گردید.
این کنترل سیستم خنک کننده آب در یک مدار بسته سوخت و در نتیجه بهره وری احتراق در سیلندر و تخلیه صحیح متصل به مبدل های حرارتی بوده که درجه حرارت آب نازل ها حرارت مربوطه از پیستون بوده خصوصاً در موتورهای خود جرقه در محل ورودی و خروجی قالب ریژه را تنظیم میکند.
چنیــن سیسـتم خنـک کنندگـی باعـث اطمینـان از تبلـور و انجمـاد یکنواخـت پیسـتون ریختگـی ایجـاد کـرده و متصـل کـردن زمـان سـرد شـدن بــا یــک مقــدار مشــخص مــذاب و بارریــزی آن درون قالــب ریــژه باعــث بهینــه شــدن بهــره وری فرآینــد ریخته گــری خواهــد شــد.
4- تغییرات در ساختار و سیستم پیستون
یک مجموعه ای از الزامات برای پیستونها مانند جرم کمتر کلگی پیستون معمولاً تخت بود با اندکی برای افزایش استحکام بالاتر در درجه حرارتهای بالا و قدرت بالاتر موتور موجب ایجاد نیاز به یک تحول در ساختار پیستون شده است.
این تغییرات مرتبط با پیستون های ریختگی از آلیاژهای AI-SI با ترکیبی عمدتاً نزدیک به یوتکتیک (جدول ۱) خنک شوندگی بهتر قسمت اصلی پیستون از طریق شکل های مختلف کلگی پیستون و به کارگیری رینگ در درون پیستون و ماهیچه های نمکی و همچنین پوشش های محافظ است.
شـکل کلگـی پیسـتون تعییـن کننـده روش چرخـش مخلـوط هـوا و ســوخت و در نتیجــه بهــره وری احتــراق در ســیلندر و تخلیــه صحیــح در موتورهـای خـود جرقـه حـرارت مربوطـه از پیسـتون بـوده خصوصـاً زن مشـخص کننده نـوع محفظـه احتـراق نیـز می باشـد.
در موتورهـای بــا تزریــق مســتقیم یــک بخــش بزرگ تــر از مخلــوط ســوخت و هــوا روی قســمت صــاف کلگــی پیســتون بــه حالــت احتــراق در می آیــد و بــه ایــن دلیــل فرورفتگی هــای ایجــاد در ســطح رویــی پیســتون ایــن فرآینــد را تســهیل می کنــد (شــکل ۷).
در عــوض در موتورهایــی کـه جرقـه زنـی غیـر مسـتقیم اسـت (فضـای احتـراق بـه دو قسـمت محفظــه توربولانســی و محفظــه پیــش احتــراق تقســیم می شــود)
کلگــی پیســتون معمــولا تخــت بــود یــا اندکــی بــرای افزایــش اســتحکام، تحــدب دارد (شــکل 1).
یــک تغییــر هــم در ســاختار داخلــی پیســتون بــه وجــود آمــده کــه بـه دلیـل نیـاز بـه ارتقـای خنـک شـدن مقطـع کاهـش جـرم عمدتـاً آن اســت. درون پیســتون شــکل های ۷ و ۸ در شــکل 9 نشــان داده شـده اسـت.
_رینگ قرار گرفته در پیستون به صورت مغزی_
رینگ هــای درونــی پیســتون کــه بــه نــام آلفیــن هــم نامیــده می شــوند در کلگــی پیســتون در هنــگام ریخته گــری قــرار داده می شــود کــه دو نقــش اصلــی دارنــد:
• آب بندی پیستون در سیلندر
• حذف و تخلیه حرارت از پیستون و هدایت آن به سمت دیواره ها
رینگ هـای پیسـتون (معمـولا 2 یـا 3 و حتـی 4 عـدد) اغلـب از چـدن، خاکســتری، چــدن نشــکن یــا چــدن آلیــاژ شــده بــا نیــکل، کــروم و مولیبــدن ســاخته می شــود.
در قســمت محیطــی، رینگ هــا دارای یــک شــکل دندانــه ای هســتند تــا ایــن امــکان فراهــم شــود درون پیسـتون مسـتقر شـوند و ضمـن قفـل شـدن الاستیسـیته صحیحـی داشـته باشـند. اولیـن رینـگ از بالای پیسـتون نقـش آب بنـدی دارد.
رینـگ وسـطی نقـش یـک آب بنـد و جمع کننـده کمپـرس دارد. رینـگ بعــدی روغــن اضافــی از دیــواره ســیلندر را جمــع مــی کنــد تــا وارد محفظـه احتـراق نشـود.
عملکــرد صحیــح پیســتون عمدتــاً بســتگی بــه انبســاط حرارتــی و عملکــرد صحیــح پیســتون عمدتــاً فاصلـه بیـن آن و دیـواره سـیلندر دارد. بسـیار کـم بـودن ایـن فاصلـه پــس از گــرم شــدن و انبســاط موجــب آســیب بــه پیســتون شــده و بسـیار بـزرگ بـودن ایـن فاصلـه باعـث اسـتقرار نامناسـب در سـیلندر شـده و میـزان آب بنـدی کاهـش می یابـد.
بـه منظـور اجتنـاب از ایـن مــوارد در پیســتون های جدیــد و مــدرن، رینگ هــای ویــژه اســتفاده در مــورد رینــگ بالایی (شــکل 1). ایــن رینگ هــا می شــود خصوصــا باعـث اسـتحکام در هنـگام اعمـال بارهـای حرارتـی شـده و بـه عنـوان یـک محدودکننـده و همچنیـن کنتـرل کننـده انبسـاط حرارتـی پوسـته پیســتون عمــل می کننــد. البتــه نکتــه منفــی آن هــا انتقــال حــرارت بـه مقطـع پایینـی پوسـته اسـت.
ایــن رینگ هــا از چــدن آســتنیتی (جــدول ۲) تهیــه شــده و پــس از عملیــات ســطحی بــه نــام آلفیــن یــا رینگ هــای تریگــر نامیــده می شــوند (شــکل 5 تــا 11). در ایــن فرآینــد یــک غوطــه وری کوتــاه در آلیــاژ Si-Al انجــام می شــود تــا یــک الیــه نفــوذی بــر روی رینــگ بـه وجـود آیـد تـا قابلیـت چسـبندگی آن بـه پیسـتون افزایـش یابـد (12)
-
ماهیچه های نمکی
ماهیچه های نمکی با روش زینتر کردن ساخته میشوند و از ۹ درصد هستند. نمک در یک قالب تحت فشار پرس شستن و اکتیو کردن میشود تا شکل نهایی ماهیچه به وجود آید.
قبل از استقرار – فسفاته و منگنز فسفاته کردن ماهیچه درون قالب ریژه به منظور پیشگیری از بروز تنش ها پوشش گرافیت دادن که میتواند هنگام بارریزی موجب آسیب شود، ماهیچه ها تا حدود ۴۵۰ پیش گرم میشوند.
مطابق شکل ۱۰ آن ها بر روی پوشش قلع دادن روی پین های خاصی مستقر میشوند تا موقعیت آن ها نسبت به قطعه ریختگی ثابت باشد و در ادامه فرایند ریخته گری به وسیله شستن با آب تخلیه میگردند.
پس از تخلیه در کلگی پیستون یک کانالی به وجود می آید (شکل ۹) که در جریان کار پیستون درون موتور روغن تحت فشار داخل آن جریان می یابد.
و موجب خنک شدن کلکی پیستون و مقطع استقرار رینگ (خصوصاً درون رینگ اولی در محفظه احتراق) میشود.
شکل و ابعاد ماهیچه های نمکی عمدنا بستگی به ساختار پیستون و الزامات مشتری دارد.
در دوره های دهه ۸۰ و ۹۰ میلادی کانالهای خنک کننده فقط برای موتورهای با بار بالای دیزل با جرقه زنی تحت کمپرس فسفات روی کلسیم روی منگنز و فسفات آهن ایجاد میگردد. استفاده میشد اما امروزه پیستون های موتورهای بنزینی نیز مجهز به کانال های خنک کننده و همچنین رینگ های آلفین هستند.
عمليات سطحی پیستون ها
پیستون ها پس از ماشین کاری تحت فرآیندهای عملیاتی سطحی قرار میگیرند که شامل موارد زیر است:
• شستن اولیه درون فرآیندی
• شستن و اکتیو کردن
• فسفاته و منگنز فسفاته کردن
• پوشش گرافیت دادن
• پوشش قلع دادن
• آنودایز کردن
• آب کروم دادن و غیره
• فسفاته و منگنز فسفاته (MAP) کردن پیستون ها (شکل ۱۱)
بــا هــدف محافظــت ســطحی از خوردگــی و آمــاده ســازی ســطحی بــرای پوشــش گرافیــت پیســتون ها تحــت فرآینــد فســفاته قــرار می گیرنــد. الیــه تبدیلــی شــیمیایی شــکل گرفتــه بــا ضخامتــی در حـد 1 میکـرون یـک سـطح مناسـبی اسـت (سـوزن ها، صفحـات یـا دانه هــا) کــه چســبندگی گرافیــت بــه پیســتون را افزایــش می دهــد. متناسـب بـا افزودنـی هنـگام فسـفاته کـردن پوشـآن هایی بـه صـورت فسـفات- روی، کلسـیم- روی، منگنـز و فسـفات- آهـن ایجـاد می گردد. بــر روی پیســتون هایی کــه از آلیاژهــای فســفاته کــردن انحصــارا آلومینیمــی اســت انجــام می شــود.
فســفات منگنــز(MnP) برخـلاف پوشــش فســفات معمولــی، بــر روی پیســتون های فــوالدی افــزوده می شــود.
لایه MnP بــه خوبــی جــذب روغــن موتــور می شــود و موجــب محافظــت بهتــر شــیارهای رینــگ و ورودی پیــن شــده تــا از قفــل شــدن و خوردگــی هنــگام کار کــردن پیســتون جلوگیــری گــردد.
به کارگیــری الیــه MnP یــک فرآینــد شــیمیایی بــوده کــه بعــد از عملیــات مکانیکــی و ماشــین کاری و همچنیــن آماده ســازی صحیــح سـطح و خشـک کـردن آن افـزوده می گـردد. بلورهـای MnP از محلـول آبـی بـر روی پیسـتون نشـانده می شـود و یـک کیفیـت خـوب الیـه MnP دارای رنــگ مشــکی یــا خاکســتری تیــره اســت (شــکل d11)
-
پوشش گرافیت بر روی پوسته پیستون
فرآیند پوشش گرافیت بر روی پوسته پیستون نشاندن یک خمیر گرافیت حاوی رزین فنول بر روی سطح آماده شده پیستون است. نشاندن گرافیت به روش چاپ غربال شکل انجام میشود و پس از اینکه یک شکل مناسب گرافیت بر روی پیستون نشانده شد پیستون در کوره تحت اتیل قرار می گیرد تا رزین به حالت شبکه ای درآمده و گرافیت بر روی سطح پیستون مستحکم گردد. هدف از پوشش گرافیت تشکیل یک لایه نازک بر روی سطح پیستون با ضخامت ۵ تا ۱۵ میکرون بوده تا مقطع کاید و راهنمای پیستون حفاظت شود و اصطکاک بین پیستون و سیلندر کاهش یابد (شکل ۱۲) .
لایه سطحی گرافیت همچنین قابلیت ترشوندگی روغن را ارتقاء داده، تمامی ناهمواری های میکروسکوپی سطح را پر میکند.
و شرایط پرداخت را بهبود می بخشد به خصوص در هنگام ضربات ناشی از انبساط باعث کاهش نیروی اصطکاک شده و همچنین درجه حرارت سطوح را نیز پایین می آورد که این امر از آنها در لحظه اصطکاک مخلوط و اصطکاک مرز دانه محافظت مینماید.
لایه گرافیتی پوسته پیستون را از چسبیدن هنگام توقف موتور جلوگیری میکند. این پوشش یکی از انواع بسیار زیاد پوشش های ضد چسبندگی بر روی پیستون های تولید شده از آلیاژ AL-S است.
-
پوشش قلع و آندایزینگ سطح پیستون
فرآیند پوشش قلع با هدف حفاظت سطوح پیستون از اکسید شدن انجام میشود. خصوصیات فلزی قلع با قابلیت لغزش خوب موجب کاهش اصطکاک در سیلندر موتور می گردد. در حال حاضر پوشش قلع جایگزین پوشش فسفات و منگنز فسفات شده است.
فرآیند آندایزینگ شامل اکسید کردن آلومینیم در یک محلول مناسب الکترولیت می باشد. هدف تشکیل یک لایه ALO با سختی بیش از ۲۷۰ ویکرز و ضخامت ۱۰ تا ۲۵ میکرون است. این لایه نشیمنگاه رینگ اول از تغییر شکل و فرسایش در جریان پیستونهای فولادی افزوده میشود. لایه Mnp به خوبی کارکرد پیستون محافظت مینماید. آندایزینگ برای پیستون جذب روغن موتور میشود و موجب محافظت بهتر شیارهای موتورهای بنزینی استفاده میشود. در مورد آندایز کردن کلگی رینگ و ورودی پین شده تا از قفل شدن و خوردگی هنگام کار پیستون لایه به وجود آمده به عنوان عایق حرارتی عمل می کند.
آبکاری با کرم
این روش متداول ترین شیوه برای افزایش سختی سطوح لغزش رینگ پیستون و سطوح سیلندر است. لایه کروم در تماس در برابر خوردگی مکانیکی با ایجاد یک سطح عاری از خش و ترک های میکروسکوپی که میتواند منشأ خوردگی و در نتیجه ایجاد حفره باشد، محافظت مینماید (۱۳) ضخامت مفید پوشش کروم ۲۰ تا ۲۵ میکرون است.
ضخامت بیشتر مزیتی ندارد زیرا اغلب باعث جدا شدن و از دست دادن چسبندگی میگردد. پوششهای کروم دارای نقطه ذوب بالا (۱۹۲۰)، ضریب اصطکاک پایین مقاومت به سایش خوب و مقاومت به فرسایش چسبنده همچنین ضریب هدایت حرارت بالاتر نسبت به چدن است. سختی و حداکثر درجه حرارت کاری پوشش های کروم به ترتیب ۱۸۰۰ تا ۳۵۰۰ ویکرز و از ۳۵۰ تا ۹۰۰ می باشد (۱۳) لایه کروم به منظور کاهش اثر ناصافی سطحی باید با الکترو پولیش و سمباده مکانیکی پرداخت گردد تا از خط و خش افتادن سطوح سیلندر جلوگیری گردد.
-
پوشش مولیبدن
یک لایه از سولفور مولیبدن به روش مثال اسپری به همراه شعله اکسی استیلن و یا یک گاز سوختنی پوشش داده می شود. پوشش های MOS دارای نقطه ذوب بالا (حدود ۲۶۲۰) و همچنین سختی بالا حدود ۱۰۷۶(ویکرز) بوده که در لغزش سطوح رینگ ها و پوسته پیستون خطر چسبیدن را هنگام استحکام اولیه مخلوط و استحکام مرزی محدود کرده و از این نظر نقش مهمی دارد. بیستون ها با پوشش MOS در موتورها با بار سنگین و سرعت دورانی بالا استفاده میشوند (۱۳)
-
پوشش های سرامیک
یکی از روش هایی است که در آن دیواره های پیستون از درجه حرارت بالا هنگام احتراق مخلوط سوخت و هوا عایق میشود تا بدین ترتیب جریان نفوذ گرما از این سطوح به اجرای سیستم خنک کننده محدود گردد. این پوشش ها به روش پلاسما اسپری ایجاد میشود و دارای پایداری حرارتی بالا و یک ساختار متخلخل در لایه سطحی هستند. به همین لحاظ یک درجه حرارت بالاتری را میتوان در محفظه احتراق هم زمان یک درجه حرارت پایین تری در پیستون و رینگ ها داشت (۱۴) معمولاً پوششهای سرامیک شامل اکسید زیر کنیم با یک افزودنی مانند … است اهداف عمدتا از اقدامات زیر قابل دستیابی است. (۱۲).
ضریب انبساط حرارتی این پوشش ها با افزایش درجه حرارت لایه بالا میرود. البته ضریب حدود ۲۵ برابر کمتر از الیاژهای چدنی و حدود ۷۵ برابر کمتر از الیاژهای Al-Si است – بهینه کردن فواصل و لقی ها در سیستم PRC (۱۳).
-
پوشش ها به روش آبکاری
این پوششها اغلب بر پایه نیکل بوده و حاوی لایه های سطحی از یک عامل فلزی نشانده شده به روش آبکاری است و دارای افزودنی هایی از پودرهای غیر فلزی با یکنواختی بالا مانند پودر الماس، پودرهای Al Or Fe0 یا کاربیدهای TIC WC (۵) میباشند.
ضخامت این پوشش های آبکاری شده روی آلیاژ AI-S پیستون ها دارای تا ۲۰۰ میکرون ضخامت، سختی بالا مقاومت به فرسایش سایشی و مقاومت به خوردگی مکانیکی و حفره ای شدن است. در حال حاضر اغلب بر روی سطوح لغزشی رینگ های پیستون و سطح جانبی پیستون پوشش هایی بدین شرح نشانده میشود پوشش های تک لایه، مانند AITISIN و پوشش های مخلوط مانند ACTIN, AITIN. TIAIN. TIAICN, TICN CrN + Cr با فازهای CN CNC) پوشش های چند لایه TI٫TIN پوشش های با ضخامت های مختلف لایه سطحی ٫CN C٫CN پوشش TIN بر پایه آلیاژ NiTi و پوشش های آبکاری با روش های CVD و PVD (۱۳).
۵- جمع بندی
هدف تولید کنندگان خودرو امروزه ارتقای بهره وری عمومی مکانیکی موتور به صورت کاهش مصرف سوخت و نشر ذرات آلاینده و همچنین کاهش استهلاک ناشی از اصطکاک سیستم پیستون رینگ سیلندر (PRC) و تایمینگ مکانیزم دنده است. در قالب دوام پیستون و طولانی بودن فاصله تعمیرات هدف دستیابی به یک تعادل بین جرم اندک سیستم PRC و قدرت بالا و قابلیت عملکرد کاری بالا میباشد. در سیستم PRC این اهداف عمدتا از اقدامات زیر قابل دستیابی است.
• محدود کردن تعداد رینگ های آب بندی
• بهینه کردن فواصل و لقی ها در سیستم PRC
• کاهش ارتفاع پیستون و رینگ های آن
• تغییر شکل پروفیل پوسته پیستون و سطح لغزشی رینگ
• افزایش فشار در سرعت خطی پیستون و سرعت دورانی موتور با در نظر گرفتن فشار انجکسیون تا ۲۲۰ مگاپاسکال و فشار متوسط ۳٫۱ مگا پاسکال فشار حداکثر تا ۲۱ مگا پاسکال، فشار ویژه اولیه تا ۱۰۰ کیلو وات بر لیتر و حداقل بودن نشر گازهای حاصل از احتراق
• اعمال کردن پوشش های محافظ با زیری سطحی پایین و مقاومت به سایش بالا تحت اصطکاک
• کاهش تلفات در اثر اصطکاک با محدود کردن تلرانس سیستم PRC با در نظر گرفتن حداقل کردن ضخامت فیلم روغنی بین سطح لغزنده رینگ و پوسته پیستون و سطح در تماس سیلندر
• استفاده از آلیاژهای پیستون بر پایه آلومینیم کاهش جرم و ابعاد هندسی با مقاومت مناسب ترمومکانیکی
در اولین ماشین های ریژه ریزی برای ریخته گری پیستون زمان انجماد پیستونی با قطر ۸۰ میلی متر حدود ۶۰ ثانیه بود.
تولید تنها یک پیستون و فقدان اتوماسیون موجب گردید تا متوسط تولید بیستون ها با یک آلیاژ آلومینیم در سال های ۱۹۹۰ تا ۲۰۰۵ در حدود ۴ میلیون با روندی با افزایش اندک بوده است.
پس از ۲۰۰۱ شرکت Federal – Mogul شرکت WSK Gorzyce را خرید. خطوط پیوسته مدرن برای ریخته گری پیستون ایجاد شد.
اتوماسیون و همزمان سازی (سنکرونیزه) ماشین های ریزه ریزی با ربات های ریخته گر بهره وری فرآیند را بالا برد. به کارگیری سیستم های اضافی آب گرد زمان سرد شدن آلیاژ را به حدود 13 ثانیه و کمتر رساند انجماد پیستون را یکنواخت نمود و اثر جریان گردابی بار موجود در سیلندر و زمان احتراق مخلوط تعداد تولید محصول را افزایش داد (شکل ۱۳).
یک تغییر نیز در ساختمان و ساختار پیستون به وجود آمد. هدف روندهای جاری در ساختار پیستون های موتورهای احراقی افزایش اثر بخشی هزینه ای و سازگاری بیشتر با محیط زیست از طريق بالا بردن بهره وری عمومی از ۴۰ به ۵۲ درصد بوده است.
دستیابی به اندیس های بهتر اثر بخشی هزینه ای از طریق افزایش بهره وری مکانیکی میسر است. این بهره وری یک شاخص از افت ناشی از اصطکاک در مکانیزم متحرک موتور احتراقی که حدود ۷۰ تا ۸۰ درصد میباشد.
چنین به نظر می رسد سیستم PRC حدود ۵۰ درصد تحت تأثیر افت کلی اصطکاک موتور بوده و به همین دلیل اجرای راه حلهایی که موجب کاهش افت اصطکاک میگردد ضروری است.
این را محلها شامل استفاده از ماهیچه های نمکی و رینگ های داخلی پیستون کاهش جرم و ارتفاع پیستون پوشش پوسته پیستون با لایه های محافظ مانند فسفانه کردن پوشش گرافیت قلع آندایز کردن و آب کروم می باشند.
تلاش های فعلی تولیدکنندگان پیستون موتورهای احتراقی با هدف محدود کردن میزان مصرف سوخت و نشر CO از طریق ایجاد تعادل بین موتورها با کاهش حجم و افزایش قدرت به همراه کسب دوام کاری است.
این امر منجر به تولید پیستون های نسل جدید با وزن کم ضریب اصطکاک پایین و افزایش مقاومت به درجه حرارت بالا خصوصاً در مقطع بالایی تاج پیستون که بالاترین درجه حرارت را دارد و اما در این ناحیه به چند صد درجه سانتیگراد می رسد.
استفاده از کانال های خنک کننده رینگهای داخلی آلفینه شده و اشکال هندسی متفاوت در کلگی پیستون موجب گردیده پیستونهای فعلی خصوصاً در موتورهای جدید با نسبت کمپرس بالا، استحکام بیشتری داشته باشند و درجه حرارت تاج پیستون در مقایسه با پیستون های تولیدی در دهه های ۸۰ و ۹۰ میلادی حدود ۲۵ تا ۳۰۰ درجه سانتیگراد پایین تر باشد.
پایین آمدن درجه حرارت پیستون امری کلیدی و مهم در طولانی کردن عمر پیستون است. همچنین به کارگیری رینگ های داخلی درجه حرارت رینگ بالایی را به زیر ۲۵۰ می رساند که این امر کمک به محدود کردن مصرف روغن می نماید.
مقادیر بالای فشار در سیلندرهای امروزی و بار حرارتی ناشی از قدرت بالا نیازمند استفاده از فن آوریهای پیشرفته تولید پیستون است. یک مورد خاص پیستون های موتورهای دیزل دارای سوپر شارژی میباشد که تحت بارهای بالای ترمو مکانیکی قرار دارند.
علت این امر سطح بزرگ ناحیه انتقال حرارت ناشی از گازهای احتراق و شدت انتقال حرارت در اثر جریان گردابی بار موجود در سیلندر و زمان احتراق مخلوط سوخت و هوا است.
برای اطمینان از شرایط کارکرد در پیستونهای سیلومین ریختگی به صورت موضعی اغلب توسط اشعه لیزر لبه های محفظه احتراق ذوب شده و همچنین در معرض سرد شدن سریع قرار داده میشوند که موجب به وجود آمدن ساختاری بلوری با دانه های ظریف میگردد.
بــا ایــن فــن آوری امــکان دســتیابی بــه یــک ســاختار محلــول جامــد Al)α) و ظریــف شــدن بلورهــای سیلیســیم (β)از حــدود 50 بــه 5 میکــرون فراهــم شــده (1۶) کــه ایـن امـر باعـث افزایـش مقاومـت بـه بـروز تـرک در لبه هـای کلگـی پیســتون خواهــد شــد. بــا انجــام ایــن فرآینــد ایــن امــکان فراهــم می شــود تــا درجــه حــرارت پیســتون در ناحیــه لبه هــای محفظــه احتــراق تــا حــدود 4۲0 درجه سانتی گراد بالا رود.
منابع:
1X. Liu. D. Huang. C. Yan. Y. Zhou. W. Yan. Multi-direcional
forging and aging treatment effects on friction and wear
characterization of aluminium-bronze alloy, Mater. Charact
.167, 110511 (2020)
2M. Ienciu, P. Moldovan, N. Panait, M. Buzatu, Development
and casting of non-ferrous alloys, EDP , Bucure؛ti
(1982).
3L . Wen-sheng, W. Zhi-ping, L. Yang, G. Yong, X. Jian-lin
of novel aluminium bronze for dies, Trans. Nonferrous Met
Soc. China 16, 607-612 (2006)
4Z. Han, Y.F. He, H.C. Lin, H. Zhao, Dealloying characterizations
of Cu-Al alloy in marine environment, J. Mater. Sci.Lett. 19, 393-395 (2000)
5H .J. Meigh, Rought aluminium bronzes properties
processes and structure, Maney Publishing, IS BN 978-1-
906540-20-3 (2008).
6M . Makeshkumar, S.R. Surender, S. Arunprakash, R.
Madesh, M. Sasi Kumar, K. Sudharsan, Microstructural and
mechanical properties evaluation of dissimilar aluminum
alloy and bronze joints using friction stir welding, Materials
Today: Proceeding (2021). DOI: https://doi.org/10.1016/j.
matpr.2021.05.563
7Y. Li, Y. Lian, Y Sun, Comparison of cavitation erosion
behaviors between the as-cast and friction stir processed Ni-
Al bronze in distilled water and artificial seawater, J. Mater.
Res. Technol. 13, 906-918 (2021).
8N . Cimpoesu, S. Stanciu, D. Tesloianu, R. Cimpoesu, R.
Popa, E. Moraru, A study of the damping capacity of mechanically
processed Cu-9.2Al-5.3Mn-0.6Fe shape memory
alloys, Met. Sci. Heat Treat. 58 (11-12), 729-733 (2017).
DOI : https://doi.org/10.1007/s11041-017-0086-0
9Y .-R. Su, T.-H. Wu, I.-C. Cheng, Synthesis and catalytical
properties of hierarchical nanoporous copper from è and
ç phases in CuAl alloys, J. Phys. Chem. Solids 151, 109915
(2021).
10V .H.C. de Albuquerque, T.A. de A. Melo, R.M. Gomes,
S.J.G. de Lima, J.M.R.S. Tavares, Grain size and temperature
influence on the toughness of a CuAlBe shape memory
alloy, Mater. Sci. Eng. A 528, 459-466 (2010).
11C. Bejinariu, D.C. Darabont, E.R. Baciu, I. Ionita, M.-A.
Bernevig- Sava, C. Baciu, Considerations on the Method for
Self Assessment of Safety at Work. Environ. Eng. Manag. J.
16, 1395-1400, (2017).
12D.-C. Darabont, R.I. Moraru, A.E. Antonov, C. Bejinariu,
Managing new and emerging risks in the context of ISO
45001 standard, Qual.-Access Success 18, 11-14 (2017).
13D.C. Darabont, A.E. Antonov, C. Bejinariu, Key elements
on implementing an occupational health and safety management
14system using ISO 45001 standard. In 8th International
Conference on Manufacturing Science and Education (MSE
2017) – Trends in New Industrial Revolution, Bondrea, I.,
Simion, C., Inta, M., Eds., E D P Sciences: Cedex A, 2017,
Vol. 121, p. UNSP 11007.
15M.G. Zaharia, S. Stanciu, R. Cimpoesu, I. Ionita, N.
Cimpoesu, Preliminary results on effect of H2S on P265GH
commercial material for natural gases and petroleum transportation,
Appl. Surf. Sci. 438, 20-32 (2018).
16C. Panaghie, R. Cimpoesu, B. Istrate, N. Cimpoesu,
M.-A. Bernevig, G. Zegan, A.-M. Roman, R. Chelariu, A.
Sodor, New Zn3mg-xy alloys: Characteristics, microstructural
evolution and corrosion behavior, Materials 14 (10), 2505
(2021).
17Z. Song, S. Kishimoto, J. Zhu, Y. Wang, Study of stabilization
of CuAlBe alloy during martensitic transformation by
internal friction, Solid State Commun. 139, 235-239 (2006).
18V . Nedeff, C. Bejenariu, G. Lazar, M. Agop, Generalized
lift force for complex fluid, Powder Technol. 235, 685-
695 (2013).
مقالات و اخبار