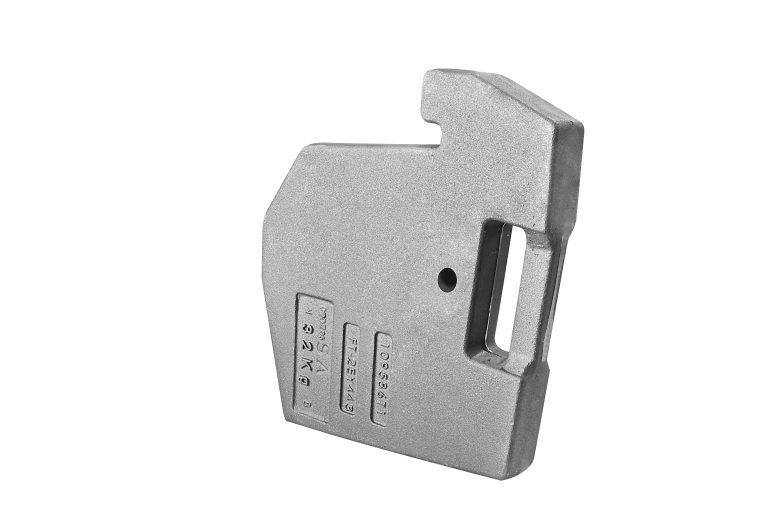
ریخته گری کوبشی چیست؟ + انواع روش های آن
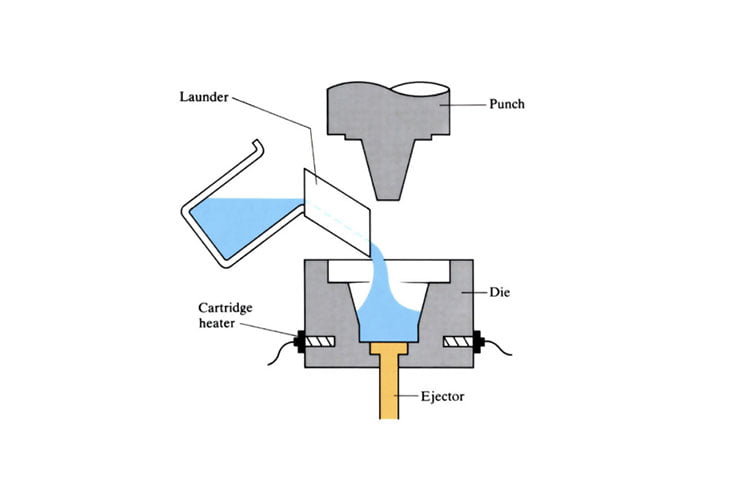
سهند آذرین: ارائه دهنده خدمات ریخته گری
جهت دریافت مشاوره تماس بگیرید.
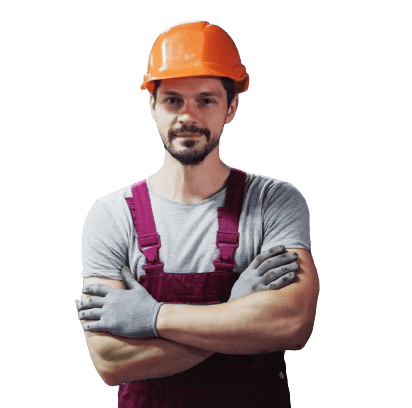
ریخته گری کوبشی نوعی از ریخته گری تحت فشار است که به شما امکان میدهد حجم بالایی از ریخته گری را برای تولید انبوه ایجاد کنید. از نظر مواد، ریخته گری فشاری میتواند شامل آلیاژها، آلومینیوم، منیزیم و غیره باشد.
انواع ریخته گری کوبشی
1 .ریختهگری کوبشی مستقیم:
- روش تزریق: در این روش متداول، فلز مذاب به طور مستقیم به داخل محفظه قالب تزریق میشود و سپس با استفاده از یک سنبه یا پرس هیدرولیک تحت فشار قرار میگیرد. این روش برای تولید قطعات با هندسههای پیچیده و ظریف که نیاز به دقت ابعادی بالایی دارند، ایدهآل است.
- روش سیل: در این روش، فلز مذاب به داخل قالب ریخته میشود و سپس با استفاده از یک سنبه یا پرس هیدرولیک تحت فشار قرار میگیرد تا حفره قالب را پر کند. این روش برای تولید قطعات بزرگتر و سادهتر مناسب است.
2 .ریختهگری کوبشی غیرمستقیم:
- روش پیستون: در این روش، فلز مذاب ابتدا درون یک محفظه نگهداری ریخته میشود و سپس با استفاده از یک پیستون به داخل قالب رانده میشود. این روش برای تولید قطعات متخلخل یا حفرهدار ایدهآل است، زیرا به فلز مذاب اجازه میدهد تا قبل از انجماد به طور کامل در قالب پخش شود.
- روش فشار گاز: در این روش، فلز مذاب با استفاده از فشار گاز به داخل قالب رانده میشود. این روش برای تولید قطعات با هندسههای نازک و ظریف که به فشار کمتری برای شکلدهی نیاز دارند، مناسب است.
3 .روشهای تخصصیتر:
- ریختهگری کوبشی با خلاء: در این روش، قبل از ریختهگری فلز مذاب، خلاء در محفظه قالب ایجاد میشود تا گازهای محلول از فلز خارج شوند. این امر به کاهش تخلخل و بهبود خواص مکانیکی قطعه نهایی کمک میکند.
- ریختهگری کوبشی با گرمایش القایی: در این روش، از گرمایش القایی برای ذوب کردن فلز و حفظ دمای آن در طول فرآیند ریختهگری استفاده میشود. این امر به اطمینان از یکنواختی دما در سراسر قطعه نهایی کمک میکند.
- ریختهگری کوبشی با سرعت بالا: در این روش، از سرعتهای ریختهگری بالا برای پر کردن سریع قالب و به حداقل رساندن زمان انجماد استفاده میشود. این امر به تولید قطعات با ساختار دانه ریزتر و خواص مکانیکی بهتر کمک میکند.
انتخاب نوع مناسب ریختهگری کوبشی به عوامل مختلفی از جمله هندسه قطعه، آلیاژ مورد استفاده، خواص مکانیکی مورد نیاز و الزامات تولیدی بستگی دارد.
تفاوت ریخته گری کوبشی(فشاری) با ریخته گری تحت فشار
درست است که در هر دو روش ریخته گری کوبشی و تحت فشار، فلز مذاب به داخل قالب تزریق و سپس جامد می شود، اما تفاوت های ظریفی در جزئیات فرآیند وجود دارد که بر کیفیت نهایی قطعه و کاربردهای مناسب هر روش تاثیر می گذارد.
فشار:
-
ریخته گری کوبشی:
فشار اعمالی در دو مرحله مجزا صورت می گیرد:
مرحله اول: فشار اولیه قبل از تزریق مذاب به قالب اعمال می شود تا هرگونه حفره یا فضای خالی موجود در قالب را فشرده و از به دام افتادن هوا در حین تزریق جلوگیری کند. این امر به تراکم بهتر ذرات مذاب و کاهش تخلخل نهایی قطعه کمک می کند.
مرحله دوم: فشار ثانویه در حین انجماد فلز مذاب اعمال می شود. این فشار مداوم به فشردهتر شدن ذرات در حال انجماد کمک میکند و از ایجاد حفرههای انقباضی و ترک خوردگی قطعه جلوگیری میکند.
میزان فشار اعمال شده در هر مرحله می تواند با توجه به نوع آلیاژ، شکل و ضخامت قطعه به طور دقیق تنظیم شود.
-
ریخته گری تحت فشار:
در این روش از یک مرحله فشار بالا استفاده می شود که فقط در ابتدای فرآیند ریختن اعمال می شود.
قالب با سرعت زیاد پر می شود و فشار تا زمانی که فلز به طور کامل جامد شود حفظ می شود.
میزان فشار اعمال شده به طور کلی به دلیل سرعت بالای فرآیند، به اندازه ریخته گری کوبشی دقیق نیست.
-
ریخته گری کوبشی:
همانطور که گفته شد، فشار در طول فرآیند انجماد به طور مداوم اعمال می شود. این امر زمان خنک شدن را افزایش می دهد و به ذرات مذاب فرصت می دهد تا به طور کامل چیده و متراکم شوند.
این فرآیند کندتر، در قطعه نهایی می شود.
-
ریخته گری تحت فشار:
فشار فقط برای مدت کوتاهی در ابتدای فرآیند اعمال می شود و پس از آن فلز به سرعت سرد می شود.
این امر می تواند منجر به ایجاد تخلخل، حفره های انقباضی و ناهمواری در سطح قطعه شود.
مراحل ریخته گری کوبشی
ریخته گری کوبشی، که به عنوان فورج فلز مایع نیز شناخته می شود، فرآیندی است که فلز مذاب را تحت فشار درون قالب قرار می دهد تا به قطعه نهایی تبدیل شود. این روش ترکیبی از روش های ریخته گری و آهنگری است و می تواند قطعاتی با جزئیات پیچیده و خواص مکانیکی عالی تولید کند.
مراحل اصلی ریخته گری کوبشی به شرح زیر است:
1 .آماده سازی قالب:
- قالب از دو نیمه تشکیل شده که از جنس فولاد یا چدن ساخته شده است.
- سطوح داخلی قالب باید تمیز و عاری از هرگونه آلودگی باشد.
- قالب قبل از ریخته گری تا دمای مورد نظر گرم می شود.
2 .شارژ مذاب:
- فلز مذاب به درون نیمه پایینی قالب ریخته می شود.
- میزان مذاب باید به گونه ای باشد که پس از اعمال فشار، تمام فضای حفره قالب را پر کند.
3 .اعمال فشار:
- با استفاده از یک پرس هیدرولیک، سنبه ای که در نیمه بالایی قالب قرار دارد، به سمت پایین حرکت می کند.
- این امر باعث اعمال فشار بر روی مذاب و فشرده شدن آن درون قالب می شود.
- فشار اعمال شده تا زمانی که فلز کاملاً جامد شود، ادامه می یابد.
4 .انجماد:
- اعمال فشار و تماس مستقیم مذاب با جداره قالب، باعث انتقال سریع حرارت و انجماد سریع فلز می شود.
- این امر سبب می شود که قطعه نهایی دارای ساختاری ریزدانه و عاری از تخلخل باشد.
5 .انجماد و انقباض:
- پس از انجماد کامل، فلز دچار انقباض می شود.
- برای جلوگیری از ایجاد ترک در قطعه، از سیستم های خنک کننده مناسب استفاده می شود.
6 . خارج کردن قطعه:
- پس از انجماد کامل و افت دمای قالب، از سنبه ها برای خارج کردن قطعه از قالب استفاده می شود.
- سپس قطعه نهایی مورد بازرسی و عملیات تکمیلی قرار می گیرد.
نکات مهم:
- نوع آلیاژ، درجه حرارت ریخته گری، سرعت اعمال فشار و زمان انجماد از جمله پارامترهای مهمی هستند که باید در ریخته گری کوبشی به دقت کنترل شوند.
- این روش برای تولید قطعات از آلیاژهای مختلف مانند آلومینیوم، منیزیم، مس و آلیاژهای روی قابل استفاده است.
- ریخته گری کوبشی مزایای زیادی از جمله تولید قطعات با کیفیت بالا، کاهش ضایعات و صرفه جویی در انرژی دارد.
نکات روش انجام ریخته گری کوبشی
ملاحظات مربوط به فرآیند:
سرعت اعمال فشار باید به گونه ای باشد که از ایجاد ترک در قطعه جلوگیری شود. سرعت فشار زیاد می تواند منجر به ایجاد ترک در قطعه شود. زمان انجماد باید به دقت کنترل شود. زمان انجماد زیاد می تواند منجر به رشد دانه ها و کاهش خواص مکانیکی قطعه شود. راز سیستم های خنک کننده مناسب برای کنترل دمای قالب ریخته گری و قطعه در حین انجماد استفاده می شود.
کاربرد ریخته گری کوبشی
همانطور که در پاسخ قبلی اشاره شد، ریخته گری کوبشی به دلیل مزایای متعددی که دارد، در صنایع مختلف کاربردهای فراوانی پیدا کرده است. در این بخش قصد داریم به برخی از این کاربردها به تفصیل بیشتری بپردازیم.
صنعت خودرو:
بلوک موتور: بلوک موتور یکی از مهمترین اجزای موتور احتراق داخلی است که وظیفه ی آن تحمل تنش ها و بارهای سنگین ناشی از احتراق را بر عهده دارد. بلوک موتورهای تولید شده با روش ریخته گری کوبشی به دلیل استحکام و چقرمگی بالا، می توانند این تنش ها را به خوبی تحمل کنند. همچنین، به دلیل تراکم بالا و ساختار ریز دانه ای که دارند، از لرزش و ارتعاشات موتور می کاهند.
سرسیلندر: سرسیلندر قطعه ای است که در بالای بلوک موتور قرار می گیرد و محل احتراق مخلوط هوا و سوخت است. سرسیلندرهای تولید شده با روش ریخته گری کوبشی از هدایت حرارتی بالایی برخوردار هستند و می توانند گرمای حاصل از احتراق را به طور موثر به سیستم خنک کننده منتقل کنند. همچنین، به دلیل مقاومت بالایی که در برابر خوردگی و فرسایش دارند، عمر طولانی تری دارند.
میل لنگ: میل لنگ قطعه ای است که حرکت خطی پیستون ها را به حرکت دورانی تبدیل می کند و گشتاور موتور را به گیربکس منتقل می کند. میل لنگ های تولید شده با روش ریخته گری کوبشی از استحکام خستگی بالایی برخوردار هستند و می توانند در برابر تنش ها و بارهای متناوب به خوبی مقاومت کنند. همچنین، به دلیل دقت بالایی که در ابعاد و هندسه ی آنها وجود دارد، لرزش و ارتعاشات موتور را به حداقل می رسانند.
منیفولد: منیفولد قطعه ای است که وظیفه ی آن جمع آوری و هدایت مخلوط هوا و سوخت به داخل سیلندرها و یا هدایت دودهای حاصل از احتراق به خارج از موتور را بر عهده دارد. منیفولدهای تولید شده با روش ریخته گری کوبشی از وزن کم و چقرمگی بالایی برخوردار هستند و می توانند در برابر شوک ها و ضربه های ناگهانی به خوبی مقاومت کنند.
مزایای ریخته گری کوبشی
تولید قطعات با چگالی بالا و تخلخل کم:
در فرآیند ریخته گری کوبشی، مذاب تحت فشار زیاد در قالب قرار می گیرد و به طور کامل در تمام حفره ها و سطوح قالب فشرده می شود. این امر منجر به تولید قطعاتی با چگالی بالا و تخلخل کم می شود. قطعات با چگالی بالا استحکام و چقرمگی بیشتری دارند و در برابر تنش ها و بارهای سنگین مقاوم تر هستند. همچنین، تخلخل کم باعث افزایش عمر مفید قطعه و بهبود خواص مکانیکی آن می شود.
افزایش استحکام و چقرمگی قطعه:
فشار اعمال شده در فرآیند ریخته گری کوبشی، ساختار دانه ای ریز و یکنواخت را در قطعه ایجاد می کند. این ساختار دانه ای ریز به افزایش استحکام و چقرمگی قطعه کمک می کند. قطعات با استحکام بالا می توانند تنش ها و بارهای بیشتری را تحمل کنند بدون اینکه دچار شکستگی یا تغییر شکل شوند. چقرمگی بالا نیز به معنای مقاومت بیشتر قطعه در برابر ترک خوردگی و شکست ناگهانی است.
قابلیت تولید قطعات با هندسه های پیچیده:
ریخته گری کوبشی به دلیل انعطاف پذیری بالایی که دارد، برای تولید قطعات با هندسه های پیچیده و اشکال نامنظم ایده آل است. در این روش، مذاب به طور کامل در تمام حفره ها و سطوح قالب تزریق می شود و شکل قالب را به خود می گیرد. این امر امکان تولید قطعاتی را فراهم می کند که با روش های دیگر مانند ماشینکاری به سختی یا به هیچ وجه قابل تولید نیستند.
کاهش نیاز به ماشینکاری نهایی:
قطعات تولید شده با روش ریخته گری کوبشی به دلیل دقت بالا در ابعاد و هندسه، معمولاً به ماشینکاری نهایی کمی نیاز دارند. این امر باعث کاهش هزینه های تولید و زمان ساخت قطعه می شود.
بهبود خواص خستگی قطعه:
فشار اعمال شده در فرآیند ریخته گری کوبشی، تنش های داخلی موجود در قطعه را تا حد زیادی کاهش می دهد. این امر به بهبود خواص خستگی قطعه و افزایش عمر مفید آن در برابر بارهای متناوب و شوک ها کمک می کند.
کاهش ضایعات:
در فرآیند ریخته گری کوبشی، ضایعات مواد اولیه به حداقل می رسد. زیرا مذاب به طور کامل در قالب تزریق می شود و از ایجاد پلیسه و ضایعات اضافی جلوگیری می شود.
معایب ریخته گری کوبشی
در کنار مزایای ذکر شده، ریخته گری کوبشی معایبی نیز دارد که از جمله ی آنها می توان به موارد زیر اشاره کرد:
- هزینه بالای تجهیزات و قالب ها
- پیچیدگی فرآیند و نیاز به مهارت بالا
- محدودیت در اندازه قطعات قابل تولید
- ایجاد سروصدای زیاد در حین فرآیند
جمع بندی
ریخته گری کوبشی، فرآیندی نوین است که مزایای ریخته گری و آهنگری را به طور همزمان ارائه می دهد. در این روش، فلز مذاب تحت فشار زیاد در قالب بسته تزریق شده و سپس منجمد می شود. این امر منجر به تولید قطعاتی با چگالی بالا، تخلخل کم، استحکام و چقرمگی بالا و هندسه های پیچیده می شود.
سوالات متداول
1. ریخته گری کوبشی چیست؟
ریخته گری کوبشی نوعی از ریخته گری تحت فشار است که به شما امکان میدهد حجم بالایی از ریخته گری را برای تولید انبوه ایجاد کنید. از نظر مواد، ریخته گری فشاری میتواند شامل آلیاژها، آلومینیوم، منیزیم و غیره باشد.
2. مراحل ریخته گری کوبشی چیست؟
ریخته گری کوبشی با 3 روش انجام میشود: ریخته گری مستقیم، غیر مستقیم، تخصصی، که در مقاله به صورت کامل به آن پرداختیم.
3. معایب ریخته گری کوبشی چیست؟
هزینه بالای تجهیزات و قالب ها، پیچیدگی فرآیند و نیاز به مهارت بالا، محدودیت در اندازه قطعات قابل تولید، ایجاد سروصدای زیاد در حین فرآیند.
آخرین مقالات
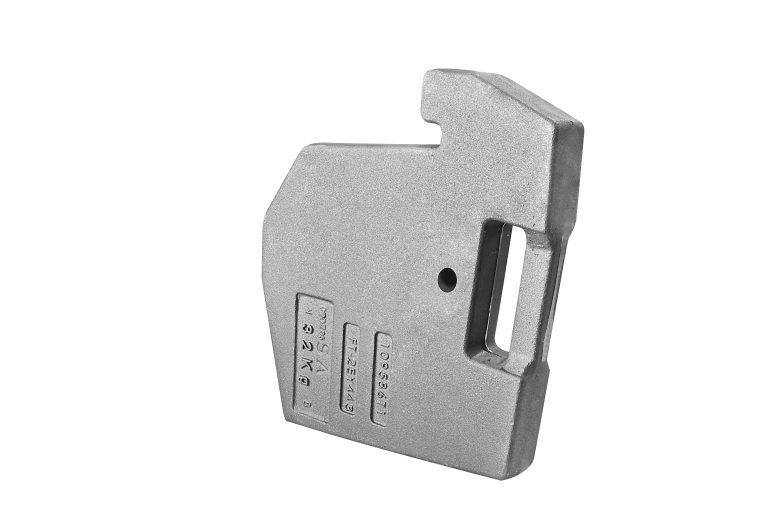
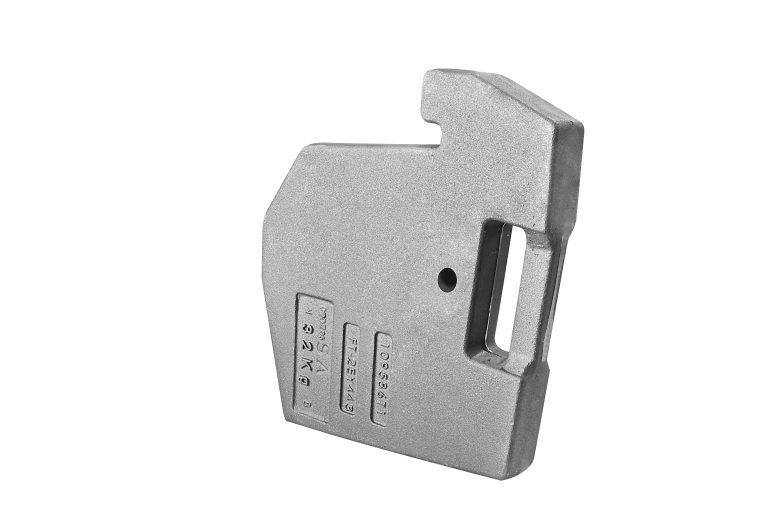
راهنمای جامع انواع، کاربردها و ویژگیهای فنی وزنه تراکتور
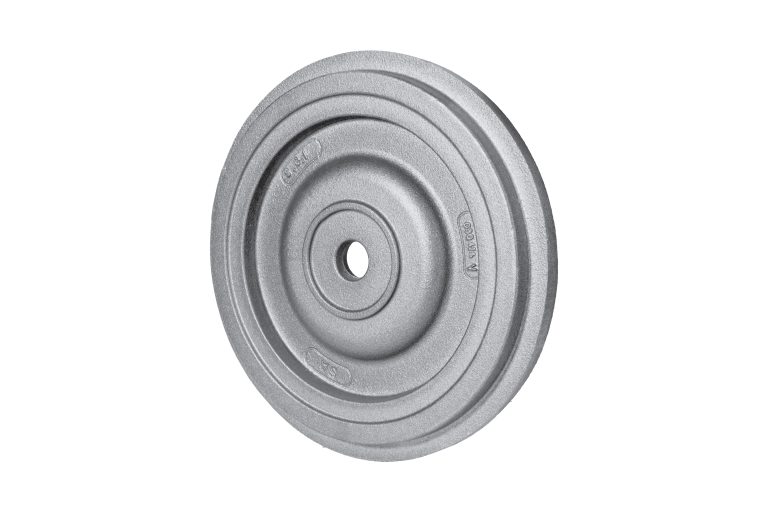
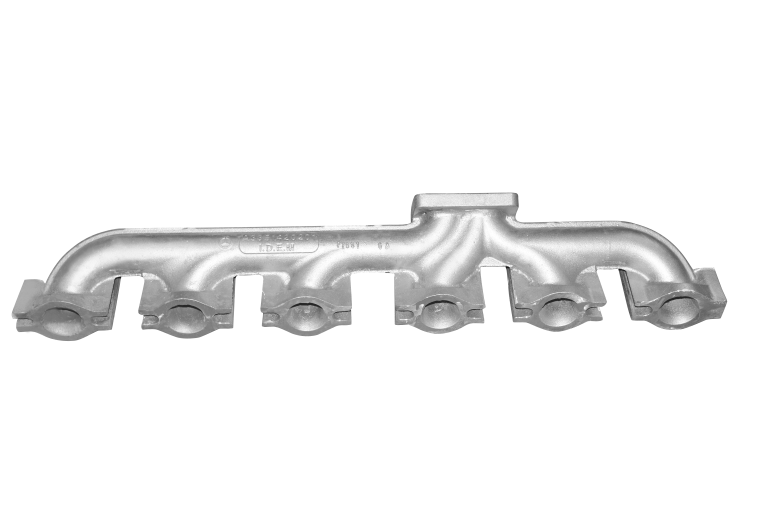
منیفولد خودرو، انواع، جنس، کاربرد و فناوریهای سهند آذرین
محصولات
مقالات و اخبار
یک نظر در “ریخته گری کوبشی چیست؟ + انواع روش های آن”
ریختهگری کوبشی چه فرقی با روشهای معمولی داره؟ واقعا کیفیت قطعه رو خیلی بهتر میکنه؟